Injection molding is a process where melted plastic is poured into a mold to make different products. The plastic cools and hardens into various items. This method is used to produce things like commercial goods, medical parts, car parts, toys, home items, decorations, and sports equipment. Sprues, runners, and gates help direct the melted plastic into the mold sections for accuracy and variety.
What is Injection Molding Sprue?
All types of molds, whether for car parts, plastic bottles, or toys, have a sprue. The sprue is the part that connects the mold to the machine. It lets the liquid plastic (like polystyrene or polyvinyl chloride) flow into the mold, where it cools and hardens into the final shape.
The sprue has a rounded, concave shape, and it’s important that the sprue seat and the nozzle tip have the same size. If they don’t match, the material can leak, leading to uneven parts. The melted plastic goes through the sprue and into the runner system. In some cases, like with large parts, the sprue can also act as both the gate and the runner. This is called direct sprue gating.
In single-cavity molds, the sprue goes directly into the molded part. The time it takes for the sprue to cool affects how the single-cavity mold is made.
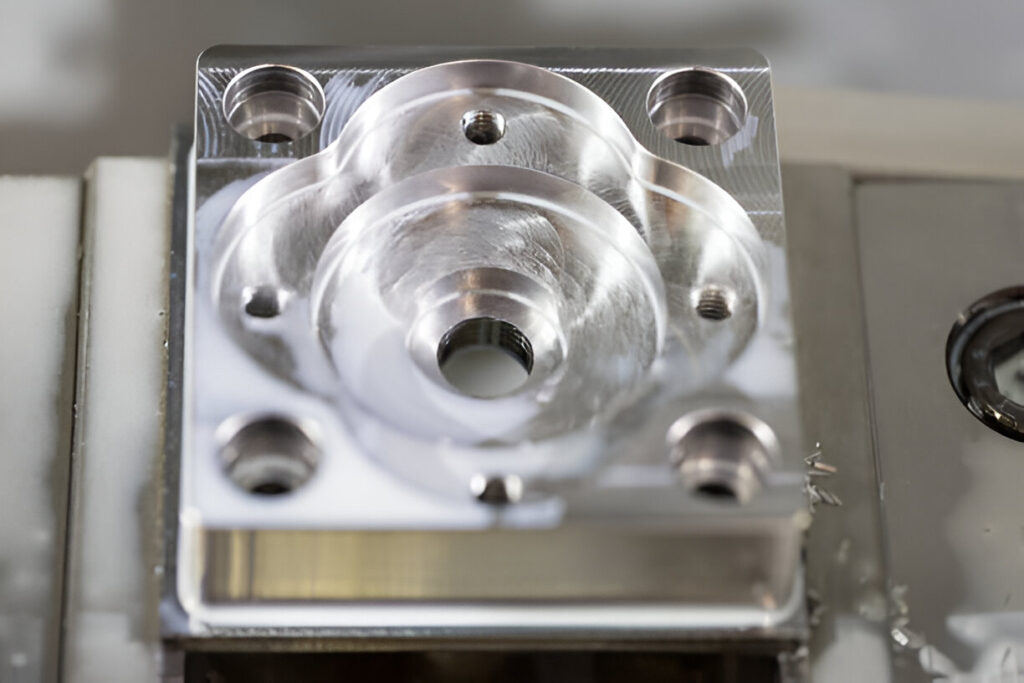
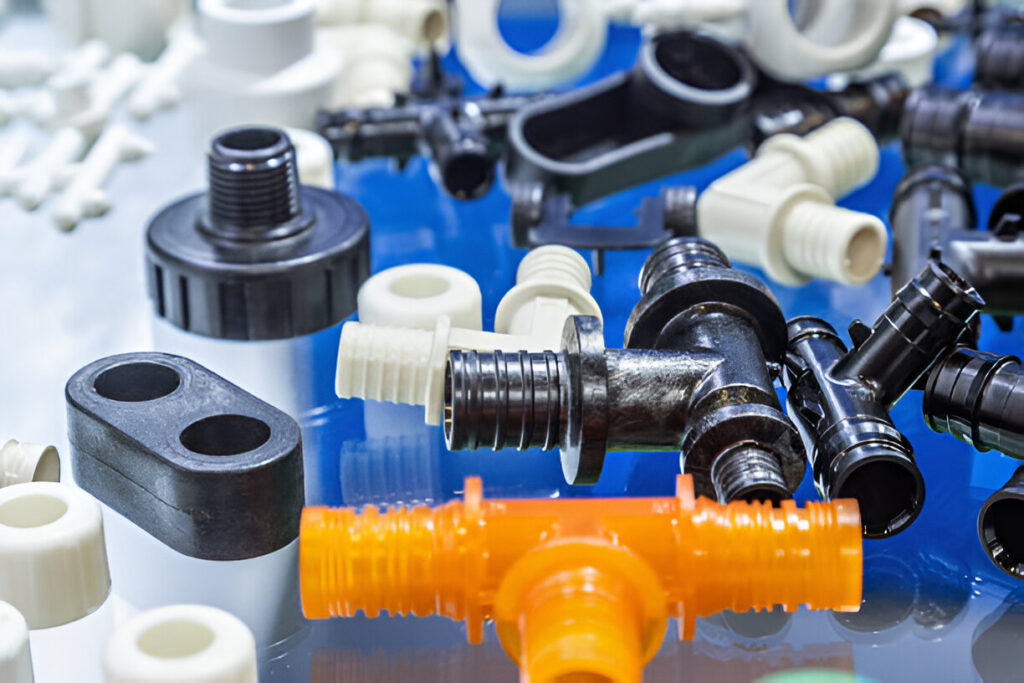
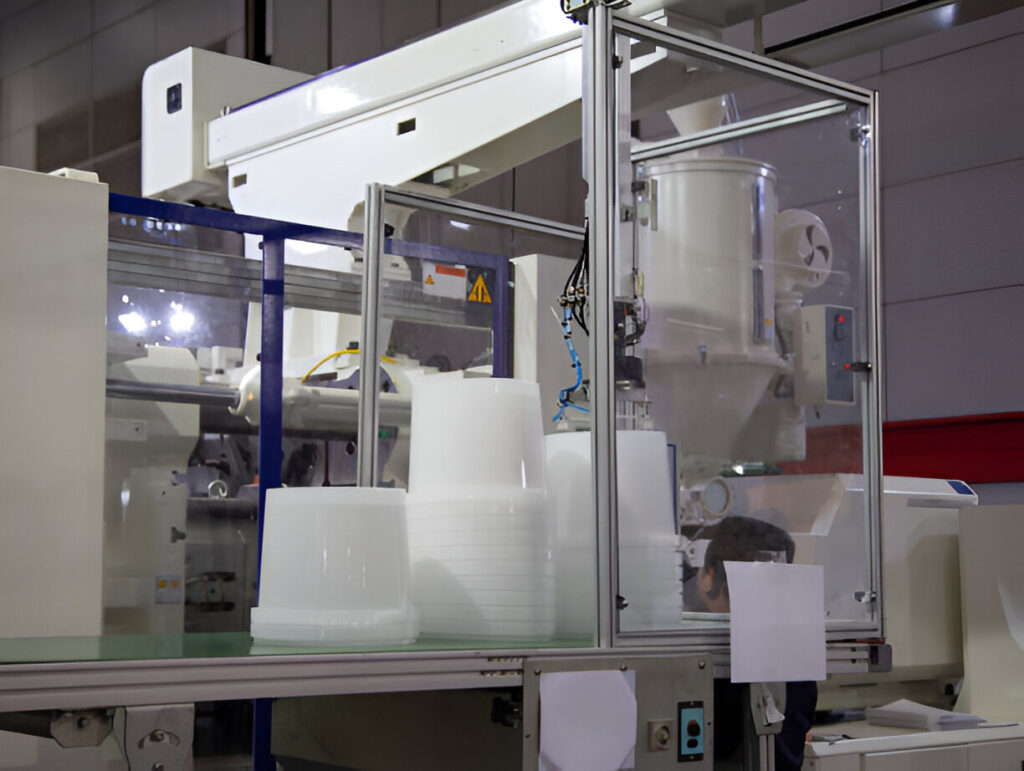
Functions of a Sprue
- Transporting Molten Plastic: The sprue is a passage that transports molten plastic to the runner system in the injection molding machine. This insures that all the plastic particles will flow smoothly into the mold.
- Handling High Pressure: During the injection, the plastic can be forced into the mold at high pressure. It is very important that it is strong enough to handle the pressure without bending and locking.
- Starting Point of Distribution: sprue is the starting point for plastic from where it begins its journey and is felt in the mold cavities. This helps in distributing the plastic into different parts inside the mold.
Types of Sprues
There are mainly two types of sprues:
- Hot Sprue: In this system, the screw is kept in hot form in order to ensure that the plastic can remain in molten form. Consequently, this technology is used in the hot runner system. Furthermore, the plastic of the body is kept in the process in such a way that the waste can be reduced. In this system, the screw is kept in hot form in order to ensure that the plastic can remain in molten form. Consequently, this technology is used in the hot runner system. Furthermore, the plastic of the body is kept in the process in such a way that the waste can be reduced. Additionally, this method allows for better flow control, therefore improving efficiency. Moreover, by reducing waste, it helps in cutting down material costs. As a result, the production process becomes more sustainable. Thus, hot runner systems are often preferred because of their ability to enhance overall efficiency and minimize waste., this method allows for better flow control, therefore improving efficiency. Moreover, by reducing waste, it helps in cutting down material costs. As a result, the production process becomes more sustainable. Thus, hot runner systems are often preferred because of their ability to enhance overall efficiency and minimize waste.
- Cold Sprue: In cold sprue system, the sprue solidifies along with the product. It is most common in cold runner systems and involves few extra task to remove the sprue.
What is a Runner?
Runners are the next step for the molten metal. They are horizontal channels that come from the sprue base and guide the metal to the molds. Runners can also be made to supply metal to several molds. Like sprues, the design of runners is important for the cast’s quality. They help keep the metal flowing smoothly and prevent it from cooling too quickly. We need to make sure the metal doesn’t harden before it fills the mould completely.
Functions of a Runner
- Distributing Plastic: The runner system distributes the plastic from the sprue to each part of the mold. In molds with multiple cavities, the runner ensures that all cavities are filled at the same time.
- Controlling Flow: The runner system helps to control how fast and smoothly the plastic flows into the mold. A well-designed runner system ensures that the mold is filled without issues like short shots (incomplete filling) or overpacking (too much plastic).
- Maintaining Pressure: The runner system also helps maintain the pressure needed to fill the mold properly. Consistent pressure is important to ensure high-quality parts.
Types of Runners
There are several types of runners, including:
- Cold Runners: In cold runner systems, the runner solidifies along with the part and needs to be removed after the molding process. These systems are simpler and cheaper but result in more waste.
- Hot Runners: In hot runner systems, the runners are kept hot, allowing the plastic to remain molten. As a result, this reduces waste. Furthermore, it can improve production speed. However, hot runners are more expensive. Additionally, they are more complex to implement. Nevertheless, many manufacturers prefer hot runner systems because, in the long run, they can boost efficiency. Moreover, despite the higher cost, the benefits often outweigh the drawbacks. Ultimately, the decision depends on the specific needs of the production process.
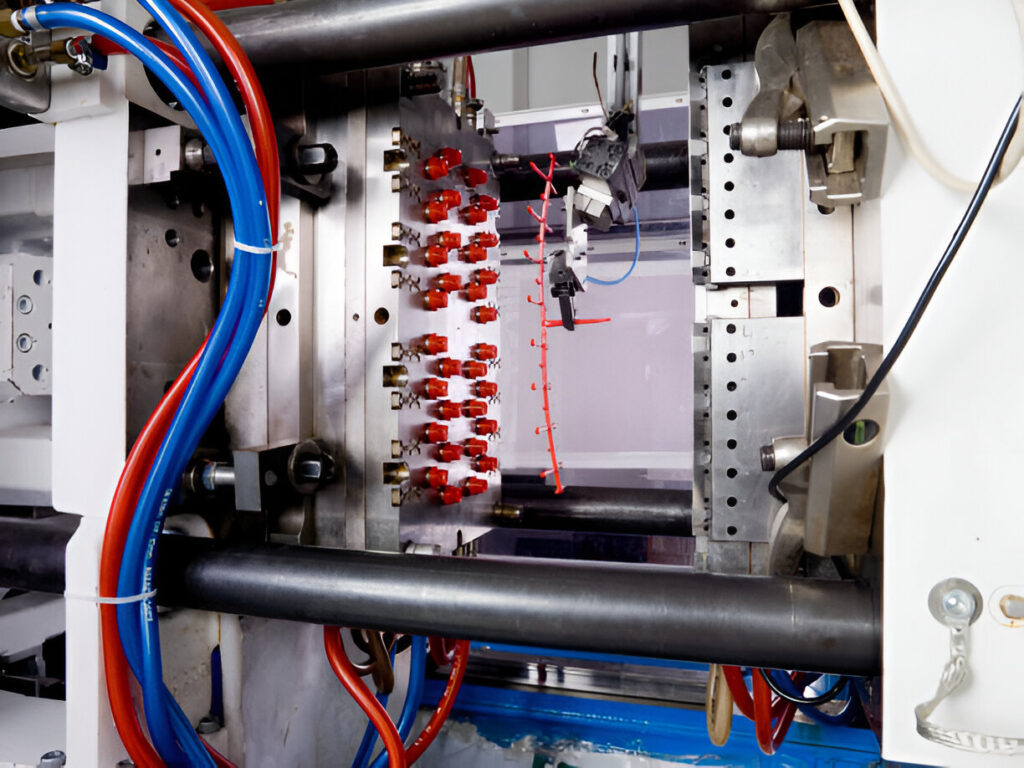
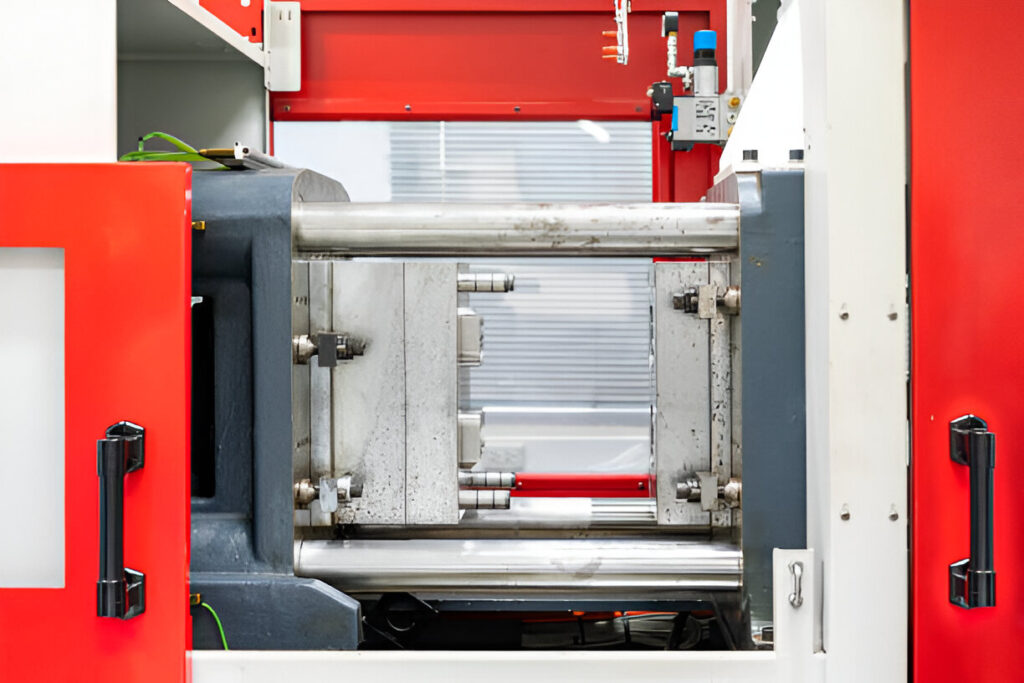

What is a Gate?
A gate is a small part that helps separate the runner from the molded item. Its size, shape, and position can affect how well the item is made. The gate should allow the part to be easily removed from the runner while making sure the part is filled and packed correctly.
The gate should be small enough to be removed easily, but not too small, or it might cause problems like poor packing, material damage, or defects like jetting. Gates should be placed at the thickest part of the mold to avoid issues like hesitation.
Functions of a Gate
- Controlling Flow Rate: The gate controls how fast or slow the plastic will enter in the mold cavity. After adjusting the Shape and size, we try to control the flows that only good-quality products enter.
- Regulating Pressure: The gate also regulates the pressure on the plastic as it enters in the mold. And that pressure should be high enough to fill the cavity and not cause any kind of defect.
- Part Separation: The gate determines how smoothly all the parts can go inside the turn and no separation or interference is created and the runner system plays a very important part in this. And when the Product cools down, it is rejected.
Types of Gates
There are various types of gates, including:
- Edge gates: Located at the edge of the part
- Submarine gates: Hidden beneath the part’s surface or in other hidden areas
- Pinpoint gates: A small, precise gating technique
- Fan gates: Have a triangular or fan-shaped opening
- Cashew gates: Arc around the part to minimize contact with it, which can help achieve a smooth finish. However, the curved design can make it difficult to maneuver the part during ejection, which can cause the gate to break.
- Pin gates: Ideal for three-plate molds with the runner channel in a different runner plate. The gate point is small enough to be trimmed off by the injection mold opening.
- Tunnel gates: Having a smaller cross-sectional area than subgates, therefore, this can affect how the material enters the cavity under pressure. Furthermore, as a result, it may impact the flow speed. Moreover, consequently, it could influence the overall quality of the molded part.
0 Comments
Trackbacks/Pingbacks