In this world, manufacturing, efficiency, precision and cost effectiveness are the factors for success. How Injection Molding Reduces Manufacturing Costs, the companies always keeps looking out on all those methods where, when it makes the product, it should be a reduced and expensive one and there should not be any difference in its quality and efficiency of any method. Injection molding has always been proven to be an effective technique to achieve your goals. It is used in various industries such as automotive, consumer goods, electronics, and medical devices.
This article will be delivered to you for various ways in which injection molding helps in reducing manufacturing costs and becomes attractive and an option for the company in wide range.
1. Introduction to Injection Molding
Injection molding is a manufacturing process where we produce large quantities of products, including small parts. We heat plastic until it becomes liquid, then inject it into a mold cavity. As the plastic cools and solidifies, it takes the shape of the mold, and we remove the final product. We use this method in many industries such as automotive, electronics, healthcare, consumer goods and packaging. It is the best way to making large amount of product at low cost. This process is ideal for producing a large number of identical parts, making it perfect for high-volume production.
The process has several important steps for How Injection Molding Reduces Manufacturing Costs:
- Clamping: When the mold is closed tightly and the two halves of the mold are secured together by a clamping unit.
- Injection: The molten plastic is injected through a nozzle at a high pressure into the mold cavity. This pressure helps the plastic fill the whole mold cavity with the molten plastic evenly.
- Cooling: When the plastic cool down, the molten plastic turned into solid and form the desired shape.
- Ejection: After the completion of task, the product is removed from the mold and ready for next processed if needed.
2. High Efficiency in Mass Production
One of the primary reasons injection molding is so popular is because of its ability to produce large quantities of parts. After creating the mold, we quickly scale up production and reduce cycle time for millions of units. We produce a large number of products in a short time. The high efficiency in mass production lowers unit costs, benefiting industries during large-scale manufacturing.
When we use traditional manufacturing methods, creating complex shapes takes a long time, which increases production time and raises the overall cost of the product. Injection molding simplifies the process so that the mold will be reusable for a long time and due to this there will be no impact or effects on the quality of the product.
This speed and efficiency will be very high in the injection molding process because it reduces the cost of labors and production time so that we can manufacture products in very high volumes as quickly as possible.
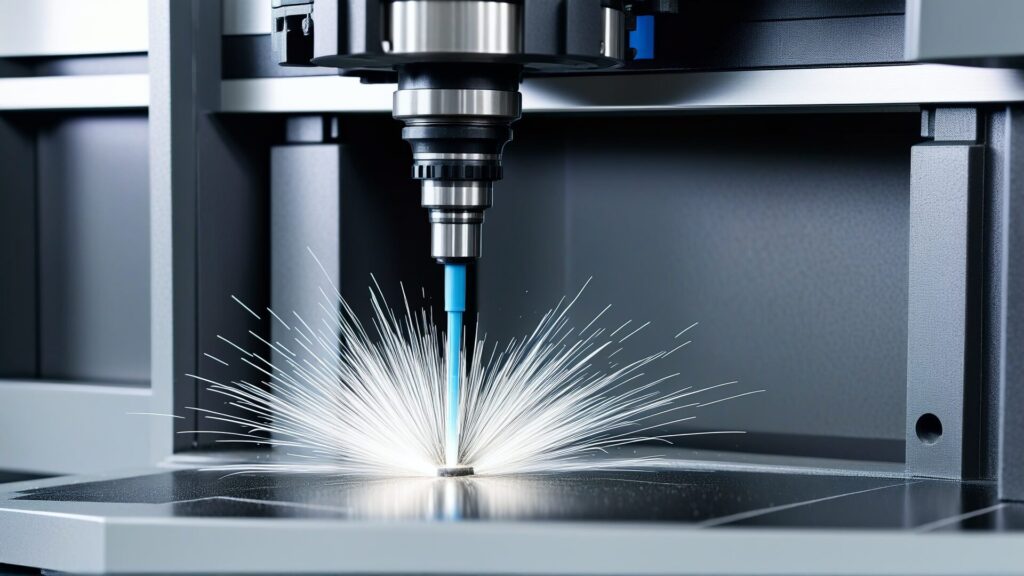
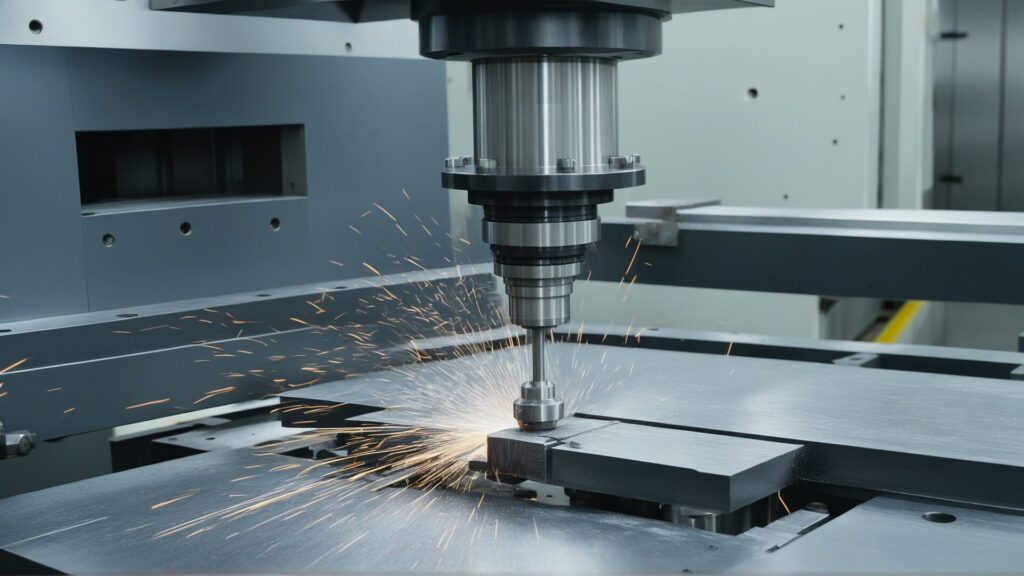
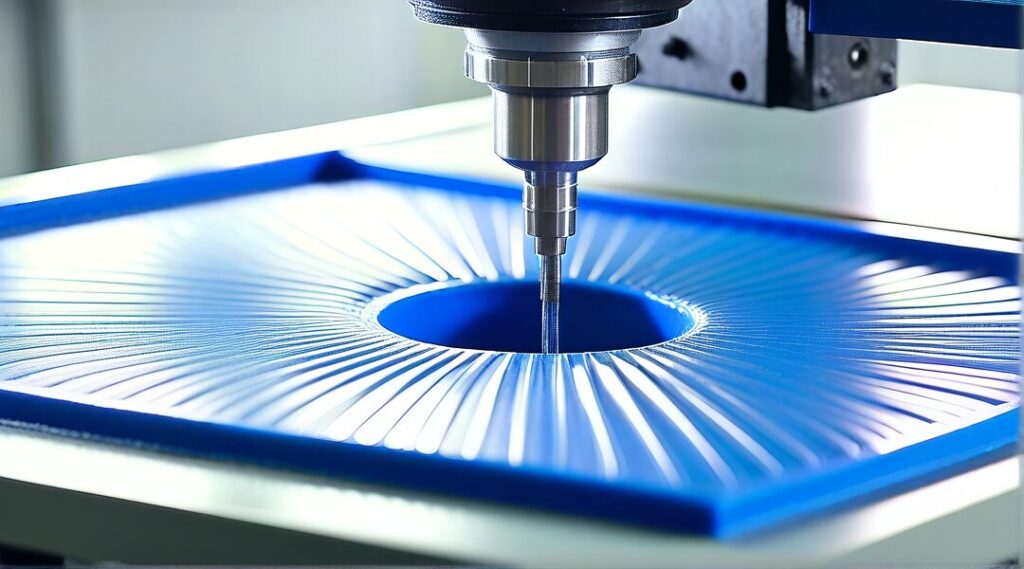
3. Materials Used in Injection Molding
Injection molding is another material efficiency factor that will reduce manufacturing costs. A process allows it to be precise and controlled and to minimize the amount of waste materials being processed. It is very important to choosing a best quality of material for injection molding otherwise it affects the cost, strength, and quality of the final product.
Commonly material used are:
- Polyethylene (PE): Polyethylene is the most commonly used plastics. It is cheap and available in different types. Products like plastic bags, bottles, and containers.
- Polypropylene (PP): It is used in packaging, automotive parts and everyday consumer products. It is known for its flexibility and strength.
- Polystyrene (PS): This plastic has lightweight material that is water resistant, environmentally friendly, economically viable and fully recyclable.
- Acrylonitrile Butadiene Styrene (ABS): ABS is a common thermoplastic used to make light, rigid, molded product such as pipe, automotive body parts, wheel covers, enclosures, and protective head gear.
- Polyvinyl Chloride (PVC): Due to its good chemical resistance and low cost it is used in products like pipes and fittings.
4. Automation Reduces Labor Costs
Automation in manufacturing can help lower costs, improve worker safety, reduce factory lead times, provide faster ROI, allow your operation to become more competitive, increase production output, and so much more. Explore the benefits of automation in detail.
Lowered operating costs
automation perform the work of three to five people, depending on the task. In addition to savings on the cost of labor, energy savings can also be significant due to lower heating requirements in automated operations. Automation integration streamlines processes and increases part accuracy, which means minimal material waste for your operation.
Reduced factory lead times
Automation can keep your process in-house, improve process control and significantly reduce lead times compared to outsourcing or going overseas.
Faster ROI
Automation solutions are based on your unique needs and goals and pay for themselves quickly due to lower operating costs, reduced lead times, increased output and more.
Ability to be more competitive
Automation allow you to decrease cycle times and cost-per-piece while improving quality. Additionally, the flexibility of automation integration enables you to retool a cell to exceed the capabilities of your competition.
Increased production output
Automation has the ability to work at a constant speed, unattended, 24/7. Automation in manufacturing means you’ve got the potential to produce more. New products can be quickly introduced into the production process and new product programming can be done offline with no disruption to existing processes.
Consistent and improved part production and quality
Automation perform the manufacturing process with better consistency than human machinists. This results in greater control and consistency of product quality.
Smaller environmental footprint
By streamlining equipment and processes, reducing scrap and using less space, automation uses less energy. A key benefit of automation is that it reduces your environmental footprint which can save you real money.
Reduced need for outsourcing
Automation have large amounts of potential capacity concentrated in one compact system. This allows shops to produce parts in-house that have previously been outsourced.
Conclusion
How Injection Molding Reduces Manufacturing Costs, Injection molding is a cost-effective manufacturing technique, especially when high volume production is required. Its main objective and ability is to provide a high quality production with identical parts with high precision and minimizes minerals material waste significantly and reduces manufacturing costs. Your process simplifies production, makes molds quickly, accelerates production cycles, and removes the complexity of traditional manufacturing methods.
By utilizing a variety of plastic materials, including polyethylene, polypropylene, and ABS, manufacturers can select the most suitable option for their specific needs while optimizing costs.
In summary, it is a combination of high efficiency which helps in high production through its precise material usage and automation which increases the valuation of injection molding and can reduce the manufacturing cost which can never compromising the quality.
Automation allows machines to perform comparisons faster and more efficiently than humans. When we have to produce more in less time, it is easier to reduce the large workforce.
I’m really enjoying the design and layout of your site. It’s a very easy on the eyes which makes it much more pleasant for me to come here and visit more often. Did you hire out a developer to create your theme? Great work!