Injection molding is one of the most popular manufacturing processes for producing large volumes of plastic parts with high efficiency and precision. However, product warpage is a common issue in injection molding process.
Warpage refers to the distortion or deformation that occurs when a plastic molded part after it has been ejected from the mold. The warpage can reduce product quality significantly including functionality and aesthetics, increase production costs and material waste.
Understanding warp issues helps improve plastic injection molding part quality and helps optimize your part design on injection molding process. This article will introduce some main factors cause your product to warp over on injection molding process, as well as some effective solutions for each.
1. Uneven Cooling
Cooling is an important part of the injection molding process, and if it’s not done right, that will cause your parts to warp. Plastic shrinks as it cools. Therefore, if different areas of a part cool at different rates (which is often the case) those areas will shrink at different rates causing internal stress leading to warpage.
Causes of Uneven Cooling:
- Poor mold design which means there are not enough cooling channels.
- Variations in wall thickness of the molded part.
- Insufficient cooling time before ejection.
- Cooling lines in the mold are not placed properly.
Solutions:
- Optimize the cooling pass selection and locate them in high temperature gradient areas.
- If needed, use a mold temperature controller and increase the cooling time.
2. Residual Stresses in the Material
Residual stress is the stress that remains in a material after the cause of such stress has been removed. In other words, it is the stress that is locked into a part or component and will distort it over time. Residual stress is not often considered in product design but can be a major factor leading to warpage of injection molded parts.
Causes of Residual Stress:
- High injection pressure leading to stress in the part.
- Rapid cooling—so rapid that residual stress is frozen into the material.
- Non-uniform mold filling, which leads to differential shrinkage.
Solution:
- Optimize injection pressure to achieve the minimum internal stress.
- Gradually cool the part so that it will shrink uniformly.
- Have the gate in such a place that the material will move uniformly and don’t be under strain.
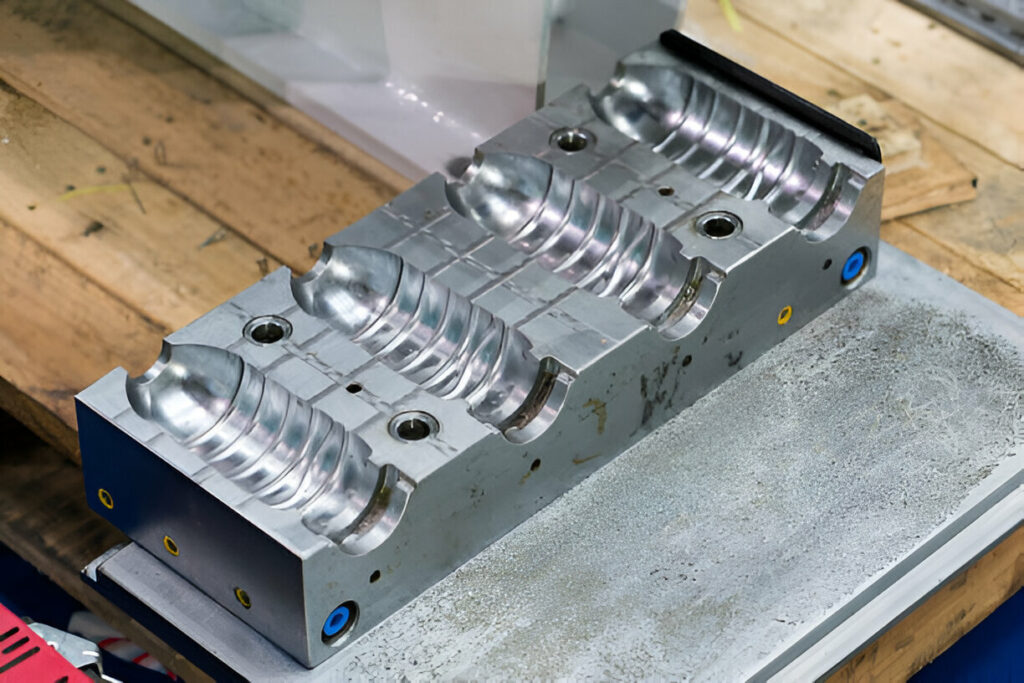
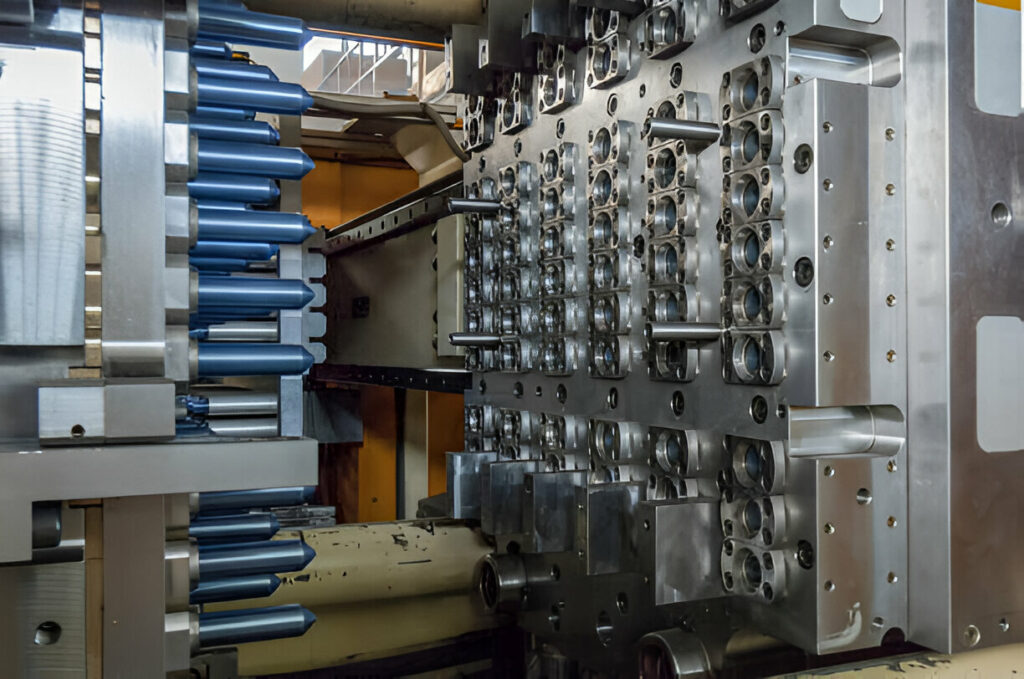
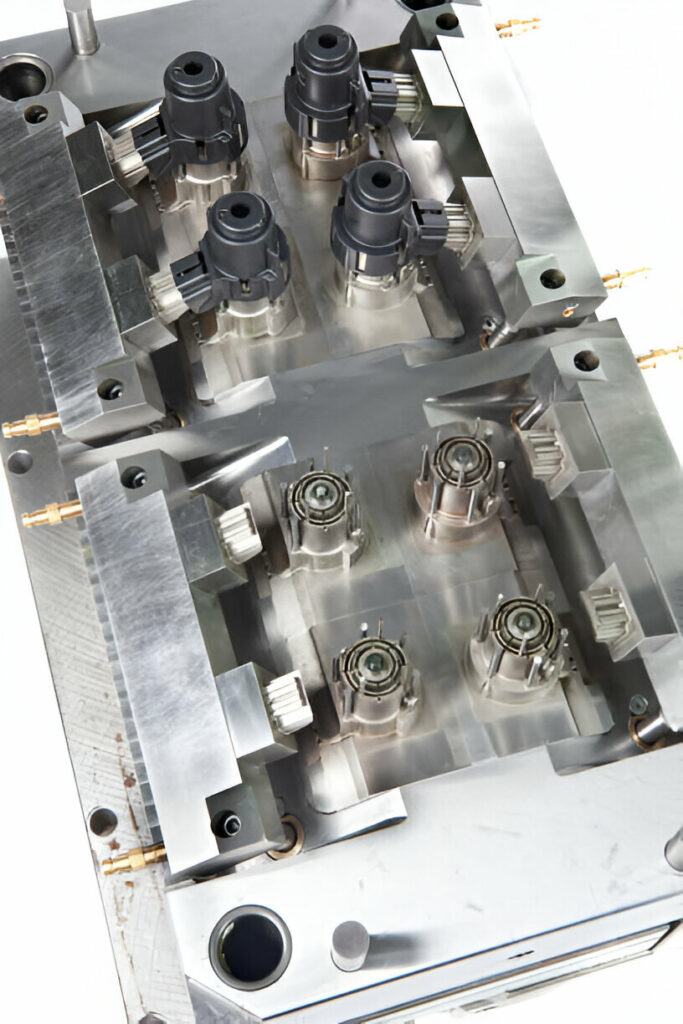
3. Poor Mold Design
Mold design is also an important factor in producing the perfect plastic injection molded part. A poorly designed mold will certainly lead to warpage due to uneven cooling, improper location or size of gate(s), or lack of support for a part while it cools.
Common issues with injection molding warpage:
- Uneven stress distribution due to asymmetric mold cavities.
- Poor gate location which results in uneven flow of material into the cavity.
- Insufficient venting, trapped air and differential shrinkage.
Solutions:
- Design symmetrical molds to ensure uniform shrinkage.
- Strategically place gates to ensure a uniform flow of the material.
- Provide adequate venting to avoid trapping air in the mold.
4. Inconsistent Material Properties
If different plastic resins are used together in a part, they can have different shrinkage rates and this may change the dimensions of the final product. Obviously, if material properties are not uniform throughout, then warpage is more likely to occur.
Causes of Inconsistent Material Properties:
- Use of low-quality plastic resins having variable shrinkage rate.
- Improper drying of the plastic material before molding.
- Contaminants in the resin that affect flow.
Solutions:
- Use high quality resins having consistent shrinkage.
- Ensure proper material drying to avoid moisture-related defects.
- Maintain strict quality control in material selection.
5. Insufficient Processing Parameters
The parameters of plastic injection molding machine have great effect on product quality. Inappropriate processing parameters, such as injection speed, temperature and pressure will cause the warpage problem.
Common Processing Errors:
- Too high an injection speed leading to turbulence of the material.
- Incorrect melt temperature, made the poor flow of material.
- Insufficient holding pressure caused the unequal shrinkage.
Solutions:
- Optimize the injection speed so that material flow is smooth.
- Maintain proper melt temperature as per resin provided specification.
- Adjust holding Pressure & Time to prevent shrinkage variation.
6. Non-Uniform Wall Thickness
With non-uniform wall thicknesses, parts will cool down and ultimately shrink at different rates. Thin regions and features will cool much faster than thicker sections of the part, causing stress and distortion in the thinner sections.
Causes of Non-Uniform Wall Thickness:
- Poor part design without considering the uniform shrinkage.
- Inconsistent material flow causing weak areas.
Solutions:
- Design parts with uniform wall thickness.
- Use ribbing or reinforcing to support weak or inadequate sections.
7. Improper Mold Release
If a part is ejected from the mold improperly, it can become deformed due to residual stresses or because it sticks.
Causes of Improper Mold Release:
- Insufficient draft angles making ejection difficult.
- Mold surface finish poor causing sticking.
- Ejection force too high deforming.
Solutions:
- Provide adequate draft angles for ease of releasing parts.
- Improve mold surface finish in order to reduce friction.
- Minimize the Ejection force, by optimizing the ejection system settings.
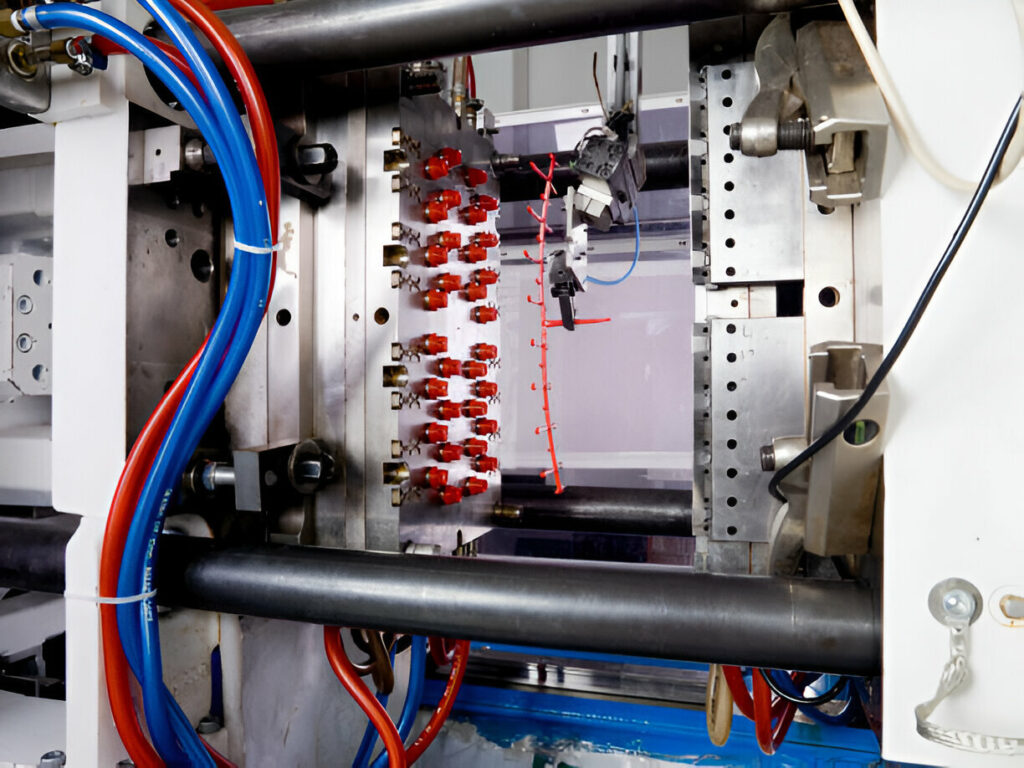
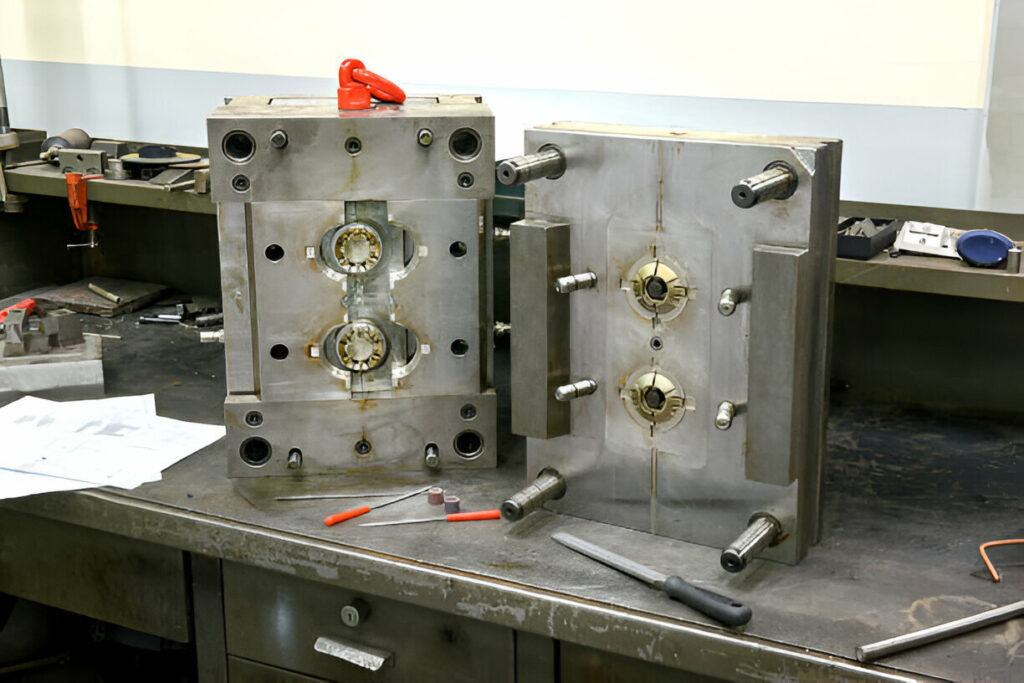
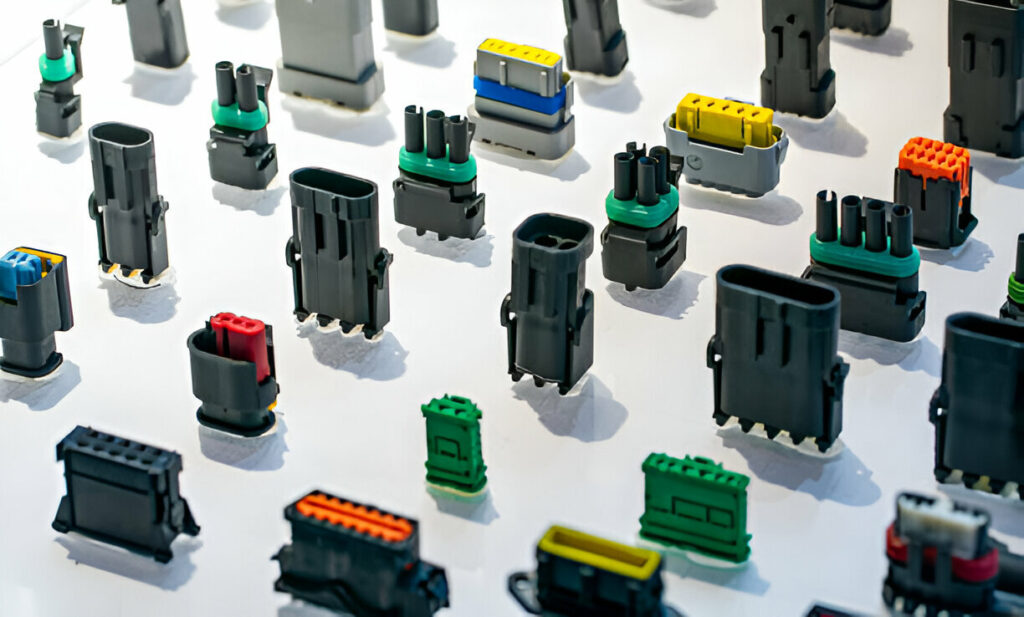
8. Environmental Factors
The final shape of plastic injection molding products after molding can be affected by external factors such as humidity and temperature variations.
Environmental Causes of injection molding warpage:
- Rapid cooling from exposure to a cold environment.
- Storage conditions after molding.
- Presence of moisture leading to expansion.
Solutions:
- Store molded parts in environment.
- Allow sufficient post molding cooling time before packaging.
- Use protective coatings to minimize moisture pickup.
Conclusion
Warpage is a common defect in plastic injection molding that directly affects the appearance and performance of injection molded products. Knowledge about plastic warpage, including its causes (such as uneven cooling, residual stresses, design flaws, material property variations, and inappropriate process parameters) and remedies, is important for manufacturers to reduce warpage defects.
Plastic warpage can be minimized by optimizing the settings of the plastic injection molding machine, using high-quality raw materials, making reasonable designs for the mold and cooling system layout, as well as adhering to appropriate process operation rules. Reliable products can be obtained with little waste if these factors are considered in the plastic injection molding process.
0 Comments