Lifecycle of an injection mold is the most commonly used process for converting raw material plastics to actual plastic parts today. It is a quick and very reliable method that has many advantages over other similar practices. The most common material used for this type of plastic molding is thermoplastic which can be easily melted, shaped and cooled. Plastic injection molding allows for a quick fully automated production of simple or complex high-quality components which can be anything from bottle caps to food packaging and even various automotive products.
The plastic injection molding cycle
Nowadays, plastic injection molding is mostly automated and even though technology has evolved a lot during the years, the process itself has remained relatively simple. This type of plastic molding requires polymeric material in granule or powder form to be inserted in the machine where it is melted and injected into a mold.
The mold itself is usually made of steel, hardened-steel, aluminum or another metal and is held shut under pressure while the molten plastic is being injected. The plastic solidifies very quickly once it enters the mold and is then ejected after a certain period of cooling time which in most cases is very short.
Quality of the mold
This type of plastic molding is preferred by individuals and businesses around the world because of the high level of precision and quality of final parts that it offers. However, incorrect control of the molding process and bad mold design are usually the two main reasons why thermoplastic moldings are sometimes defective. The most common defects include:
1. Shrinkage Lifecycle of an Injection Mold
This happens when the thermoplastic cools in the mold. This usually happens with the use of highly crystalline plastics. Plastic usually shrinks more with the increase of the mold temperature because of its increased molecular energy. This may be compensated by higher packing pressure.
2. Splash marks
These defects usually look like silver streaks on the surface of the mold. It usually happens when there is moisture in the material. In this case moisture is heated and enters the mold cavity. Moisture then volatilizes off and causes the so-called splash effect because of the sudden decompression when the material actually enters the cavity. This defect usually occurs when using thermoplastics which attract moisture better than other materials. Such thermoplastics include polyacetal and nylon.
Plastic molding has been taken to a whole new level with the invention of injection molding. The process allows for hundreds of thousands of parts to be produced with a single mold which also makes it extremely cost effective. Other benefits of plastic injection molding include the wide range of available materials and high level of precision.
Mold Design
Mould design is an important part of the development process when considering the production of a new moulding. Some considerations are given below:
The shape of the moulded part has a direct bearing on the time involved in making the mould, the cycle time of the moulding. For example, undercuts and deep screw threads often require a separate moving part which increases the cycle time of each moulding operation.
Angles on the side walls are necessary to ensure the moulding can be removed from the mould. The surface finish of the moulding needs to be decided before the mould is completed. Embossing, etching and other finishes can be added to the moulding to enhance the aesthetic qualities of the moulding. Any imperfection on the finish of the moulding will transfer to every mould made.
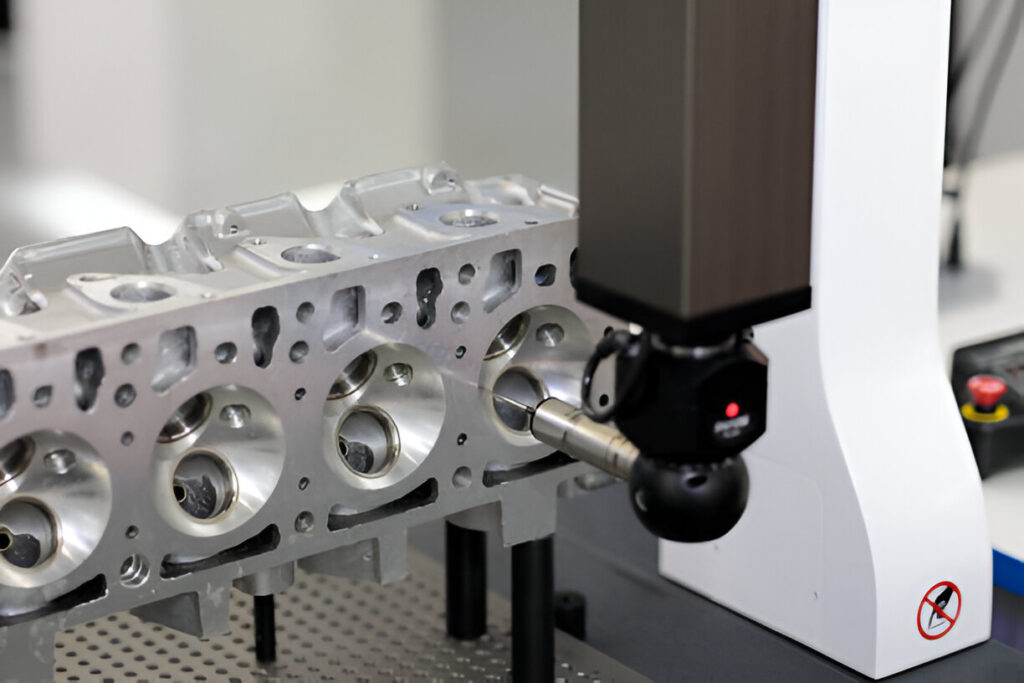
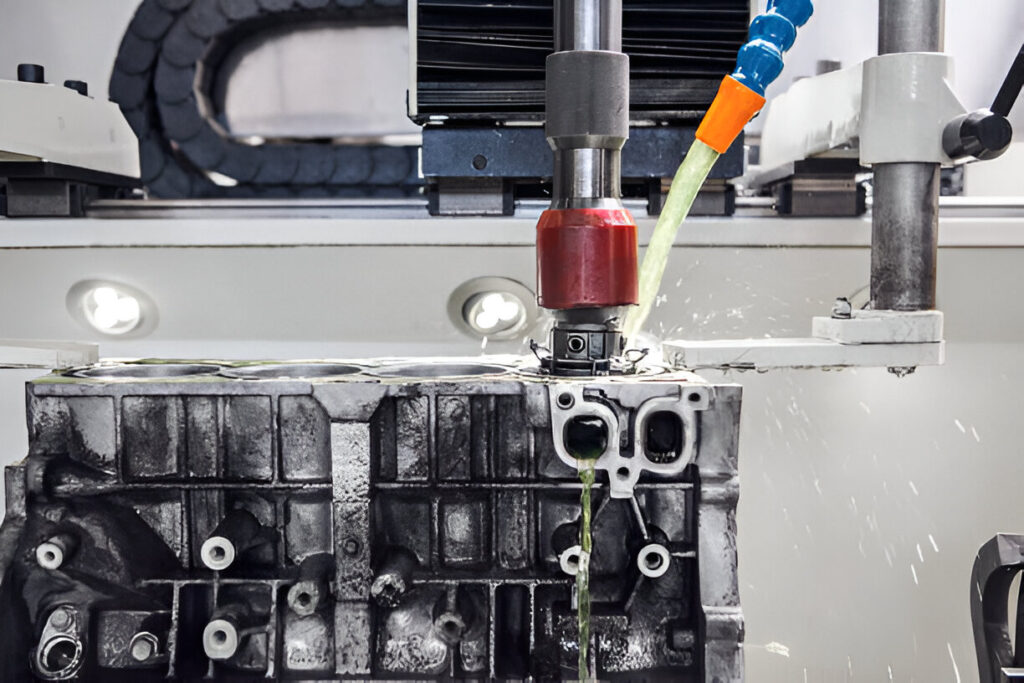
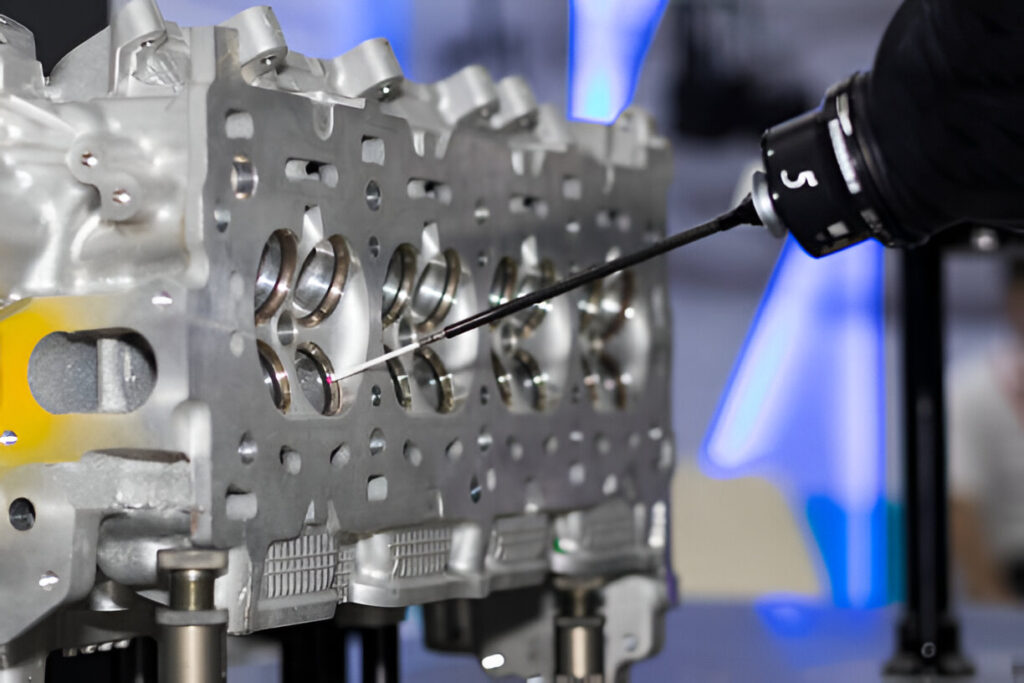
The number of cavities in a mould is governed by the number of units per annum required. The number of cavities directly affects the size of machine required for the multi-cavity mould; this in turn affects the cost of the mould and the unit cost of the moulding. Where there are many cavities, each one must be uniform compared to the others and the cooling profile needs to ensure that the outer and inner cavities cool at an equal rate, otherwise moulds of differing dimension will result.
Hot runner systems are usually used for multi-cavity systems. This reduces the cycle time and amount of waste material formed but increases the overall cost of moulds. The need for an insert or label to be inserted during the moulding sequence has to be considered at the mould design stage.
Maintenance Lifecycle of an Injection Mold
1. Routine Maintenance
With the mold still warm, internal mold surfaces should be gently cleaned with shop safety solvent to remove any residual dirt and grime, the ejector system moved fully forward, then sprayed with approved rust preventive before the ejector system is retracted and the mold closed.
All water lines should be drained and blown free of all residual water to avoid buildup of rust due to standing water. It is imperative that no water be trapped inside mold.
2. Simple Preventive Maintenance
Open the mold. Using properly approved safety shop solvent, remove the mold preservative with a lint free pad. It is bad practice to immediately run parts on the assumption that the first shots will scrape away the protective coating and will therefore be used to clean out the mold preservative.
3. Inspection Maintenance
This maintenance is performed by the lead operator or a tool maker at the end of a production run. Using the check list and visual inspection techniques, the mold is looked over and any minor repairs that are necessary are noted for the convenience of the General Maintenance procedure.
A sample from the blocked cavity should be retained for the mold maker to make repairs. The mold should be washed with safety solvent to remove the varnish and build up-from the molding process.
The vents should be checked for depth in a minimum of four clock-face places around the cavity face. Any work required during the General Maintenance procedure should be recorded on the form for future reference. Additionally, bent, worn, or broken ejector pins must be documented.
4. General Maintenance
Only competently trained tool room technicians should perform this maintenance. All plates are separated and their faces cleaned.
Caution: Highly polished surfaces should not be cleaned with brushes or rags. Use only uncontaminated facial tissues or cotton balls. Loosen dirt by spraying cleaning fluid into cavity and wipe clean with clean cotton balls. Vents should be checked for depth, width and land as compared to the tool drawing specifications.
This data should be recorded on the check list and a determination made to repair if required.
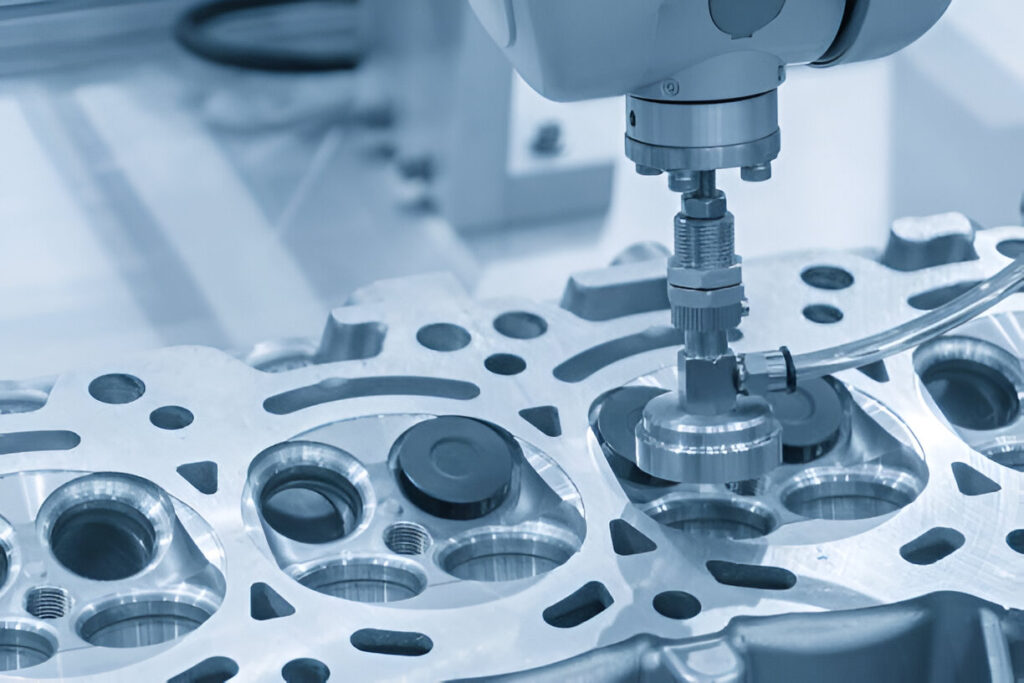
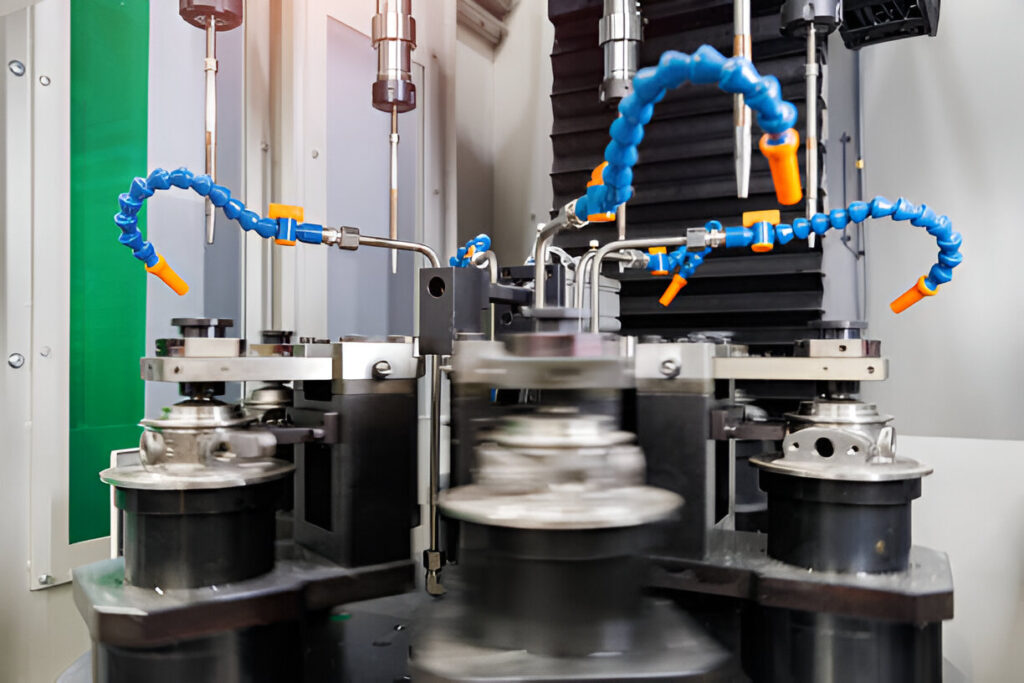
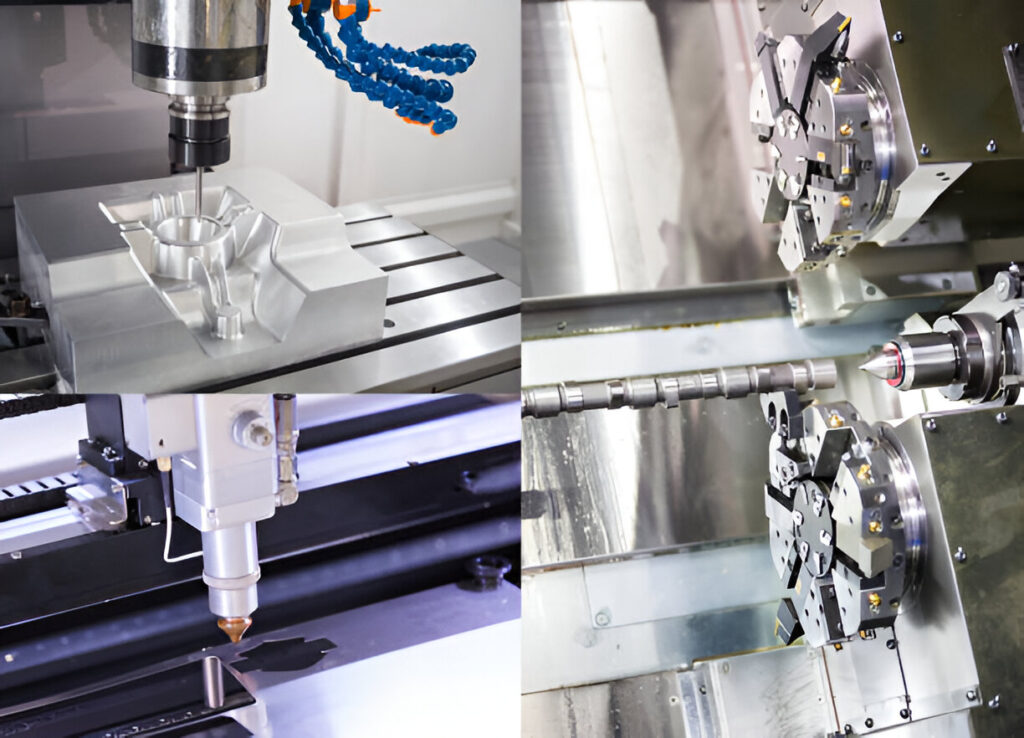
5. Major Maintenance in Lifecycle of an Injection Mold
This maintenance should be performed by skilled tool and die personnel. Maintenance is triggered by reaching cycle limits, excessive wear, or tool damage.
Conclusion
The lifecycle of an injection mold, from its initial design to its ongoing maintenance, is a vital component of modern manufacturing that directly impacts productivity, product quality, and cost efficiency. An efficient mold lifecycle strategy optimizes design to maintenance, meeting production goals while minimizing downtime and costs.
Investing in advanced design, precision manufacturing, and proactive maintenance extends mold life, boosts efficiency, and ensures consistent quality. Embracing IoT, analytics, and sustainable materials drives innovation and adaptability.
Understanding and managing the lifecycle of an injection mold is not merely a technical necessity but a strategic advantage. It helps manufacturers cut costs, stay competitive, and deliver reliable, high-quality products.
0 Comments
Trackbacks/Pingbacks