Injection molding machine diagram, also known as injection machines, are special machines used to make every plastic products. These machines will come in different types, which can be grouped based on their power source, the raw materials use by machine and prepare product, the mold clamping system, and the design of the injection systems.
There are many different types of injection molding machines, like motorized machines that use servo motors, hydraulic machines that use hydraulic motors, and hybrid machines that use both servo and hydraulic motors. The basic structure of an Injection molding machine diagram includes an injection unit that pushes the melted plastic into the mold and a clamping unit that holds and operates the mold.
CNC (Computer Numerical Control) technology has become more popular in injection molding machines, allowing for high-speed injection with precise control. There are also special machines made for specific tasks. We will explain various types of machine that will help you to get the right Injection molding machine.
Mold
The mold is where the plastic part takes shape. It is made up of two halves (core and cavity) that come together to create the final part.
- Core: The core is the inside part of the mold, forming the inner features of the part.
- Cavity: The cavity is the outer part of the mold, forming the outside of the part.
- Runner System: This system channels the melted plastic from the nozzle to the mold cavities.
- Gate: The gate controls the flow of plastic into the mold cavity.
- Ejector Pins: After the part cools and hardens, ejector pins push the part out of the mold.
Types of Injection Molding Machines?
There are many types of injection molding machines, generally categorized by the following methods:
1. Hydraulic Injection Molding Machines
Hydraulic injection molding machine is a large injection molding machine. The action of the hydraulic injection molding machine is to control every action of the injection molding machine by controlling the flow, pressure and direction of the hydraulic power source. Hydraulic injection molding machines first appeared in the late 1930s and once occupied a dominant market position, but since the introduction of all-electric injection molding machines in the 1980s, their dominance has been affected.
2. Electric Injection Molding Machines
Electric Plastic injection molding machine are a major advancement in injection molding technology. They use electric servo motors to control all movements, unlike traditional machines that rely on hydraulic systems for tasks like opening and closing molds, injecting plastic, and ejecting products.
In these electric machines, servo motors replace the hydraulic systems, resulting in greater precision and faster operations. The addition of pressure and temperature sensors allows for better control, leading to more accurate manufacturing.
3. Hybrid Injection molding machine diagram
Hybrid plastic injection molding is an energy efficient and long-lasting process without as much demand, all of which leads to a faster return on investment. Some of their specific advantages include:
- Continuous adjustments allowed by the servo pump
- Diversity of product design
- Tends to use a two clamp system over toggle
- Median upfront cost of all three options (hydraulic, electric, hybrid), but could provide the most long-term savings
- Closed loop process with faster response time
- Lower temperature requires less cooling and enables longer oil and machine life
- Faster time to ROI because of these efficiencies
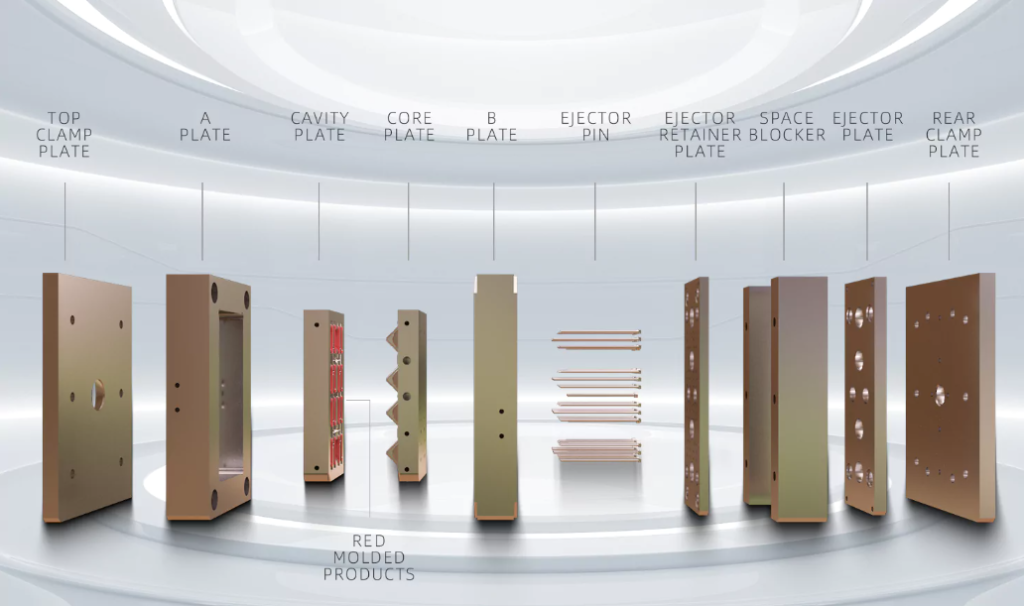
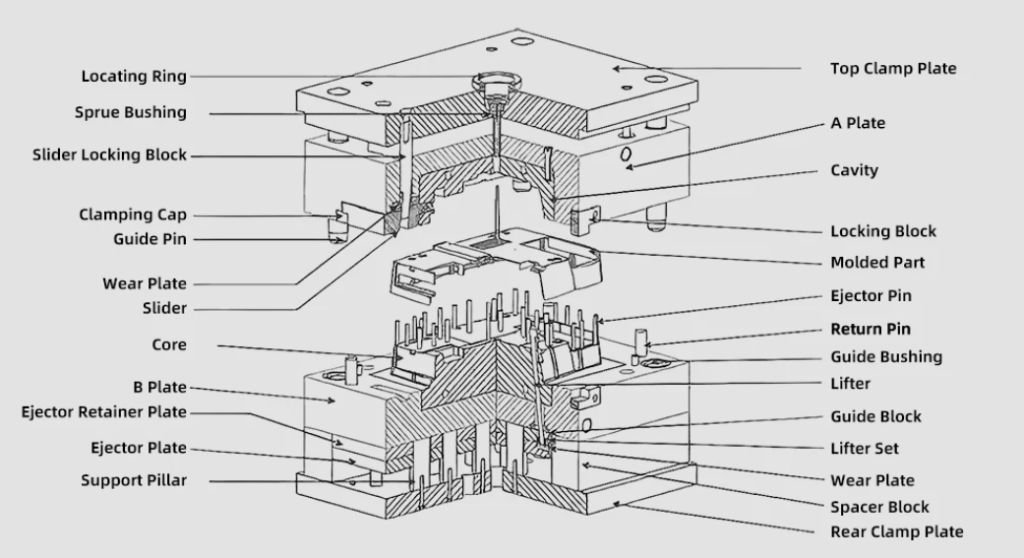
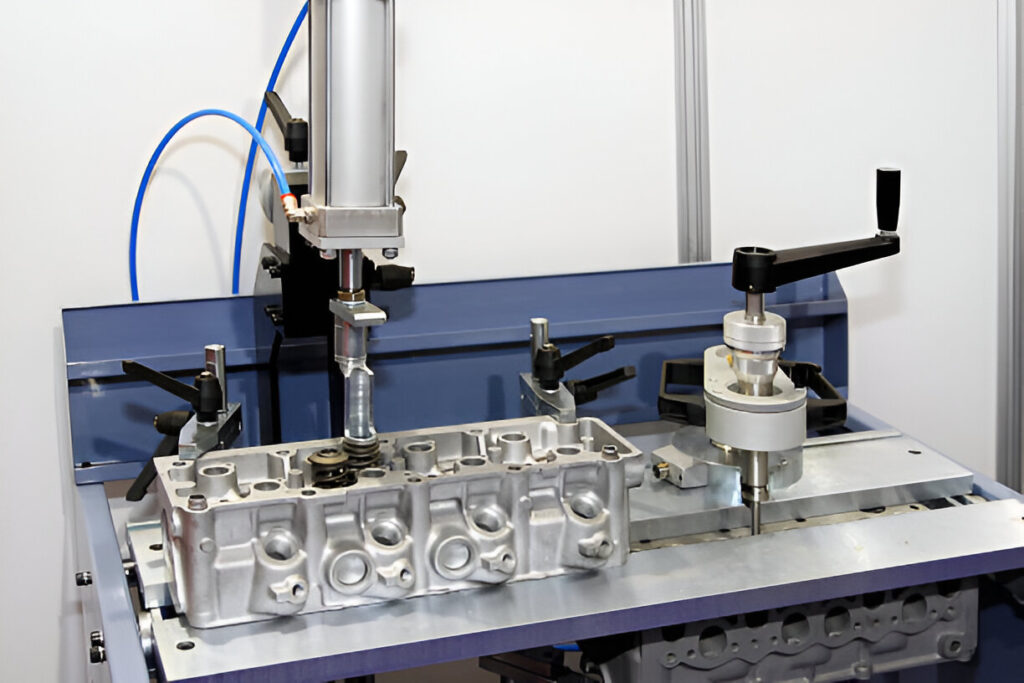
What are the Basic Structure of a Plastic Mold?
Let’s take a look at the different parts of a mold and their functions. I will explain the names and roles of these mold parts. For some important parts, I will write detailed articles separately in the future.
The main components of an injection mold system include the mold base structure, the molding system, the feed system, the ejection system, the cooling system, the venting system, and the guiding structure.
Mold Base Structure of Injection molding machine diagram
The mold base is the semi-finished framework of a mold, made up of various steel plates and parts. It forms the skeleton of the entire mold setup. Since the processing needs of mold bases and molds are quite different, mold manufacturers usually order mold bases from specialized manufacturers. This allows both parties to focus on their strengths, improving production quality and efficiency.
Over the years, the mold base manufacturing industry has become very advanced. Mold manufacturers can either order custom-made mold bases to fit specific mold needs or choose from standard mold base products. The variety of standard mold base designs, shorter delivery times, and even ready-made options give mold manufacturers more flexibility. As a result, standard mold bases have become increasingly popular.
Where we use Injection Molding Machines diagram
Injection molding machines are used in various sectors to create plastic products. Few common applications include are as follow:
1. Automotive Industry
In this industry, used to make parts like dashboards, bumpers, and interior components for cars. These parts needs to be precise and durable, and injection molding can deliver both.
2. Medical Industry
In this the process of making any product is approved by FDA that are both durable and reliable. Plastic is a good option because of its tensile strength.
3. Consumer Goods
Injection molding is used to create many household items, including toys, packaging, and kitchen appliances. The process allows for the mass production of complex shapes at a low cost.
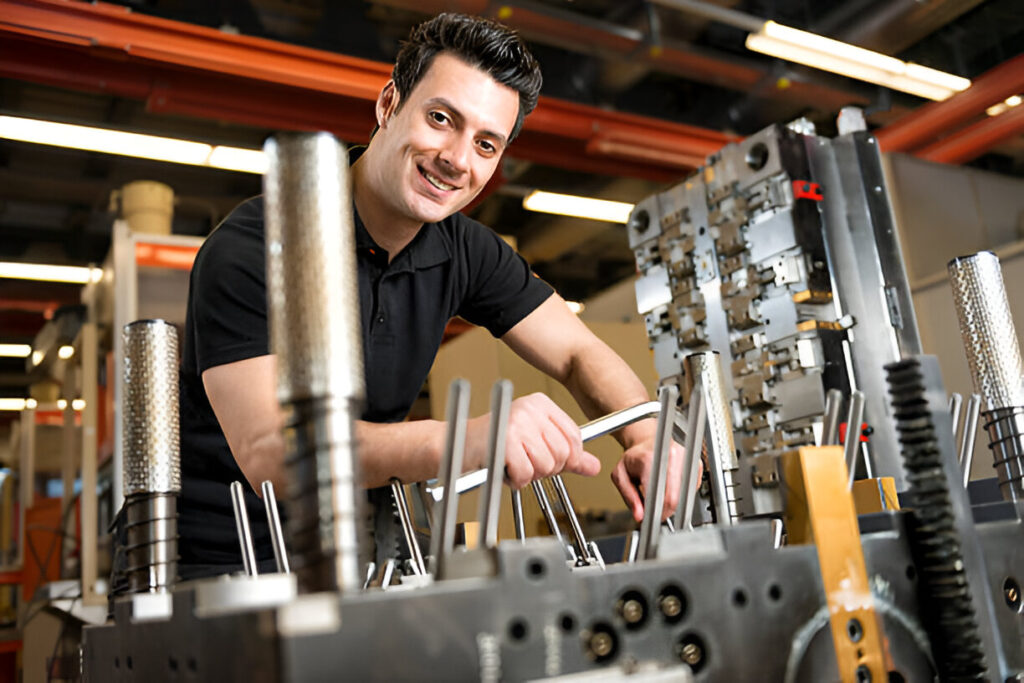
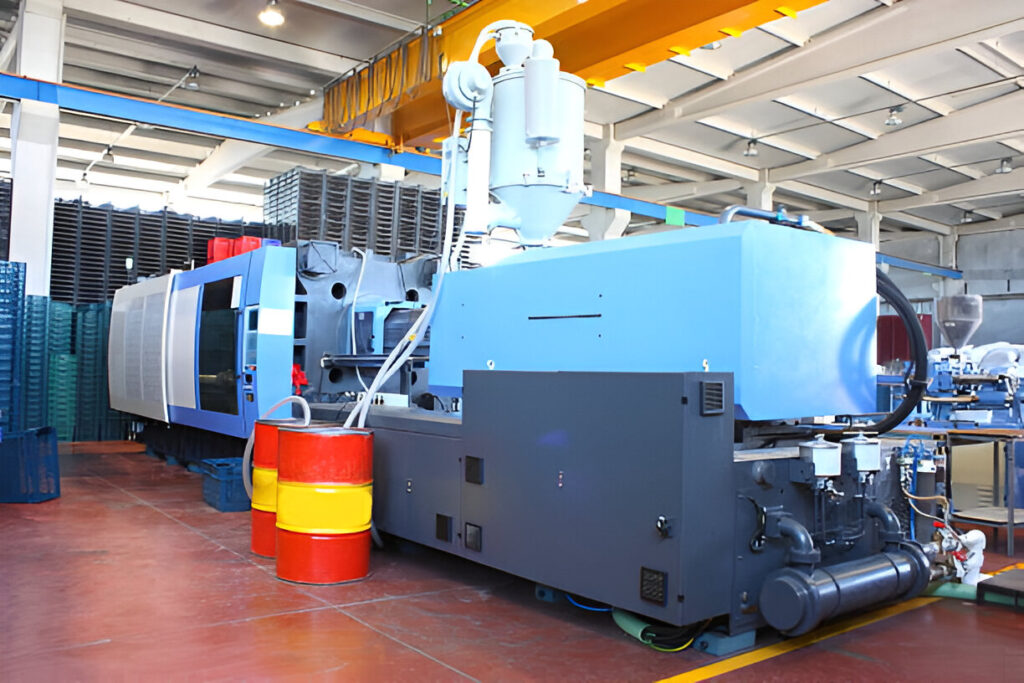
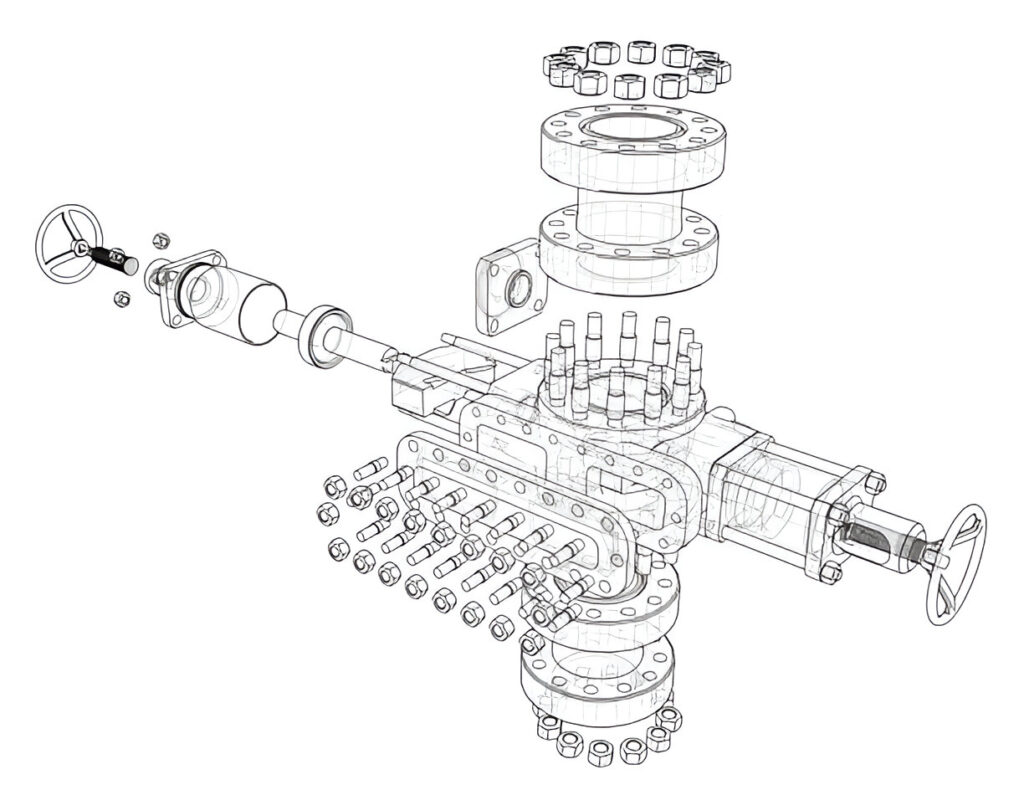
Conclusion
Injection Molding Machine Plays Vital Role for Making Plastic Products Such as Car Parts and Household Items. “There are many different types of machines such as hydraulic, electric and hybrid models“. And the particular advantage of all these machines depends on the way we use it. The main important part in plastic injection molding is the injection unit, through this we inject plastic in liquid format inside the mold. After all the process is over we let the product cool inside the mold. The use of CNC technology has made these machines more precise and faster, improving their efficiency and reliability.
We understand that there are different types of injection molding machines and their functions are different but we will help you in finding and selecting the right injection mold. With this process you can build large amount of products like car parts, medical devices and home appliances etc. And this product will be quite efficient, durable, sustainable and cost-effective so that, it is a much better product for the consumer and he can buy it easily.
0 Comments