Injection molding is a versatile production process used in the manufacturing of many products in various industries including automotive, consumer goods, electronics, medical devices and more. A major concern when producing injection moldings are part weights since it effects material costs, cycle time of production, product performance as well as sustainability.
Reducing part weight while maintaining functionality and structural integrity represents a real challenge for every manufacturing company. In this blog post we are going to discuss several different approaches on how to reduce part weight for injection moldings.
1. Material Choice
The first – and easiest – thing you can do to reduce the weight of your part is to simply select a lower density material. That’s why high-density materials like tungsten are often used in applications where weight is necessary: inertia, balancing, or collimation. Needless to say, affordability isn’t one of these selection criteria.
a) Low-Density Materials
Use materials of low density, such as polypropylene (PP) or high-density polyethylene (HDPE), which are light in weight compared to other plastics like polycarbonate (PC) or acrylonitrile butadiene styrene (ABS), but still have sufficient strength.
b) Reinforced Injection Molding Plastics
Use composites incorporating fillers like glass fibers, carbon fibers or talc. Such material can provide high strength and rigidity so thinner walls and reduced weight are possible without any performance sacrifice.
c) Foamed Plastics
Addition of foaming agent during molding to introduce microcellular structures in plastics, thereby reducing material density and weight while maintaining part stiffness.
d) Bio-Based Polymers
Consider bio-based or biodegradable polymers that are not only lighter but also help meet sustainability targets.
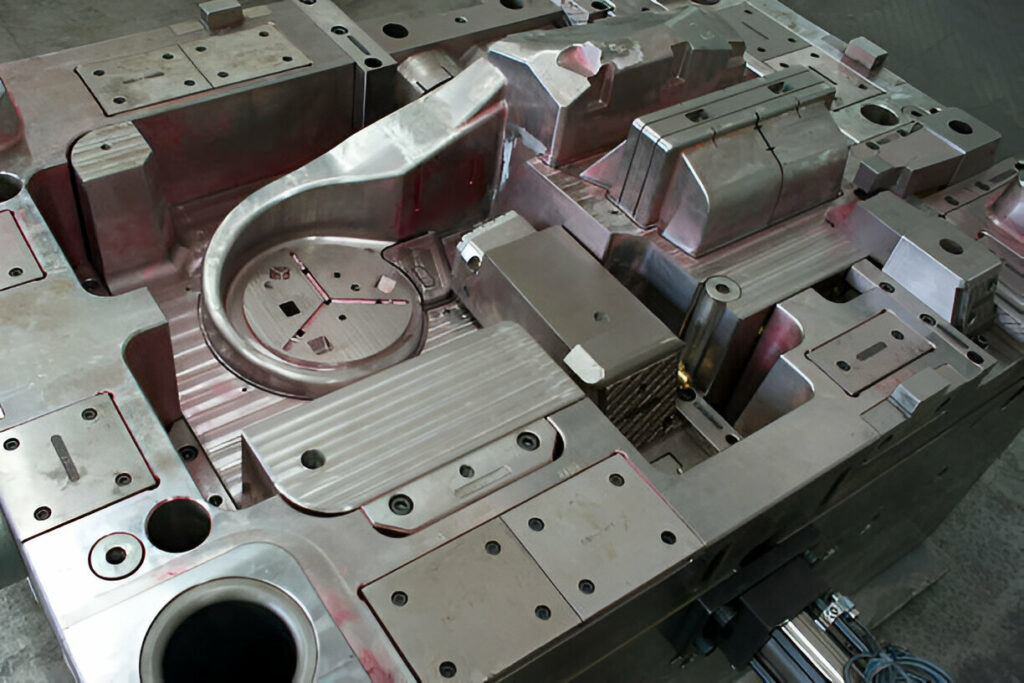
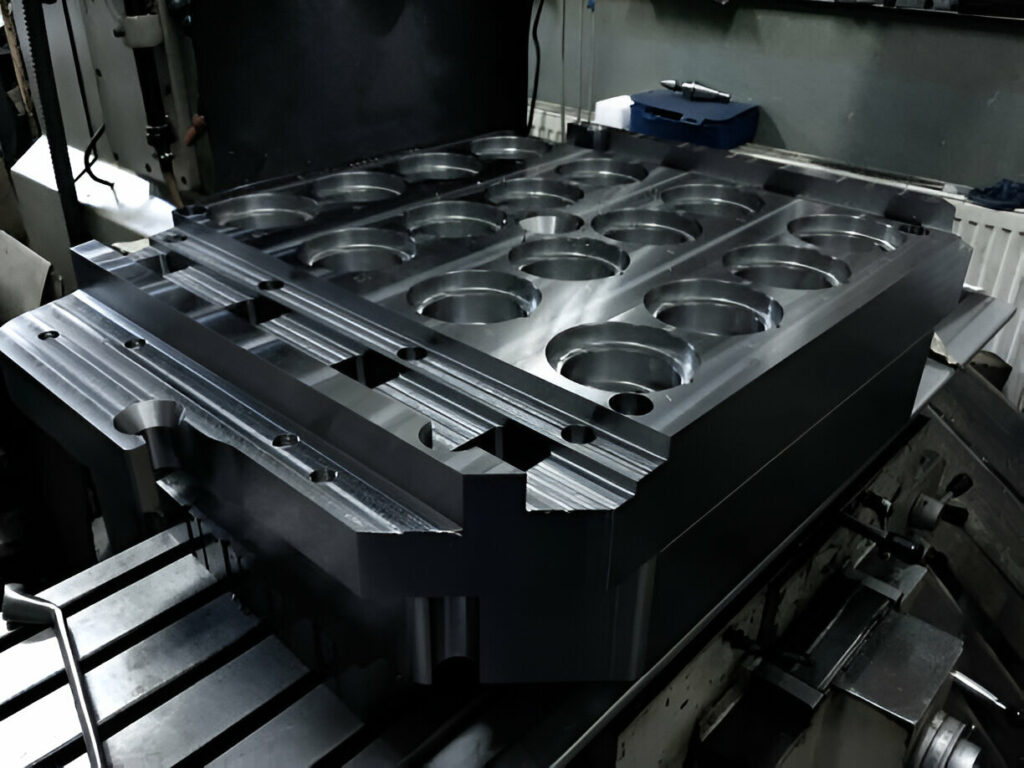
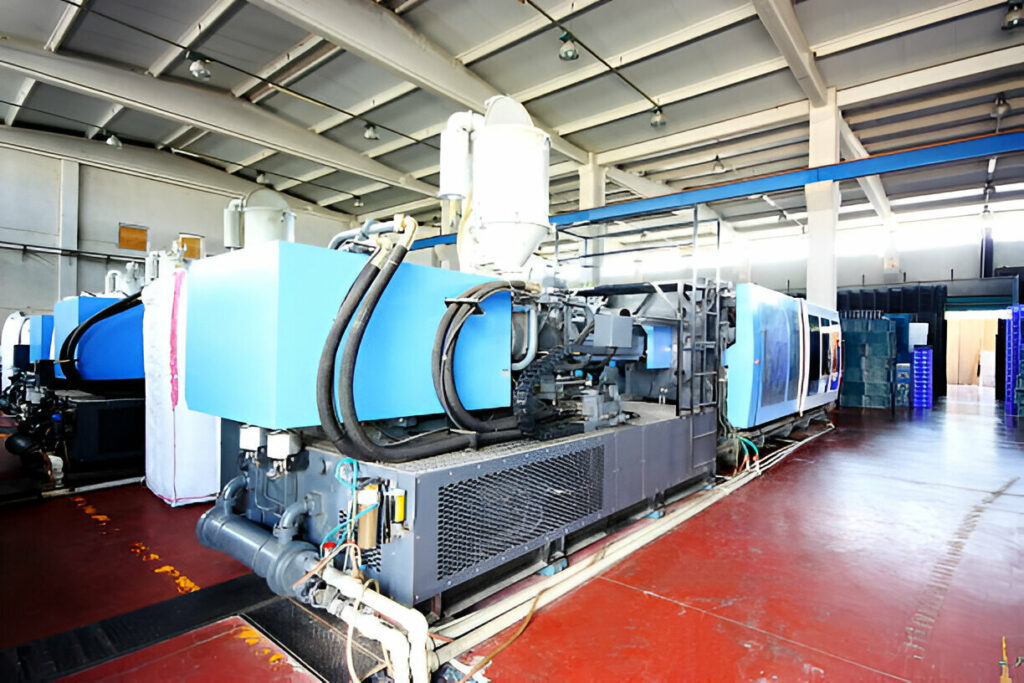
2. Part Design Optimization
Design has a major effect on the weight of a part. Modern design technologies can be used to minimize the weight of a part and ensure that it still performs as needed and fits into the product assembly.
a) Thin Wall Design
Reducing wall thickness is one of the most effective methods to decrease part weight. With modern injection molding machines and materials, wall thicknesses can be as low as 0.5mm. Keep the wall thickness uniform to prevent warping and facilitate proper flow.
b) Ribs and Gussets
Use ribs and gussets instead of thick walls to increase strength and rigidity. By doing this, you use less material but the structure will still be intact.
c) Hollow Structures
Incorporate hollow sections into the design. Techniques like gas-assisted injection molding can allow structures to be produced within parts, thus reducing material usage and weight.
d) Remove Unnecessary Features
Carry out a design review to spot and remove any non-essential features which add nothing to the overall function or look of a product.
e) Topology Optimization
Use computer-aided design (CAD) tools having topology optimization capabilities to create designs using minimum material when subjected to some performance criteria.
3. Advanced Injection Molding Techniques
Advanced molding processes can significantly reduce part weight without compromising quality.
a) Gas Assisted Injection Molding
This is a technique where gas is injected into the molten plastic during molding; as the part cools, the gas creates hollow sections in it. This helps not only in reduction of material consumption but also the weight of the part itself.
b) Foam Injection Molding
Foam injection molding uses a blowing agent that creates a cellular structure in the plastic, which reduces density and weight while increasing strength.
c) Microcellular Injection Molding
Microcellular foaming is the process of introducing nitrogen or carbon dioxide into the polymer melt, which results in uniform microcells in the polymer melt. It reduces weight and improves dimensional stability.
d) Over molding
Over molding is a process of molding a lightweight material over a substrate. This process helps to reduce overall weight of complex assemblies.
4. Tooling Considerations Of Injection Molding
Design and maintenance of molds have very significant role play for achieving weight reduction.
a) Precision Tooling
High precision molds enable to make thinner walls and complex design, proper venting, gating ensures uniform material flow, minimizes defects risk.
b) Multi-Cavity injection molding
The use of multi-cavity molds can help to improve efficiency and minimize material waste, particularly for light weight parts produced in high volumes.
5. Process Optimization
Injection molding process parameter optimization can reduce part weight significantly with quality maintained.
a) Injection Molding Pressure and Speed
Lower injection pressure and speed can help save on material by not over-packing the mold.
b) Packing and Holding Time
Minimize packing and holding time in order to limit the amount of material packed into mold during solidification.
c) Melt Temperature
Optimum melt temperature used assures good flow and minimal chances for defects that may require additional material.
d) Material Drying
Dry material permits better flow, thinner walls, and overall better part quality.
6. Simulation and Analysis
Simulation tools can be used to predict material and design behavior before manufacturing, eliminating costs associated with physical prototyping and testing of materials or components.
a) Mold Flow Analysis
Perform mold flow analysis for optimum gate location, minimum material usage and uniform flow.
b) Finite Element Analysis (FEA)
Simulation of real-world conditions and part validation with minimal material usage.
c) Prototyping
Creating prototypes to test and validate designs before hitting mass production.
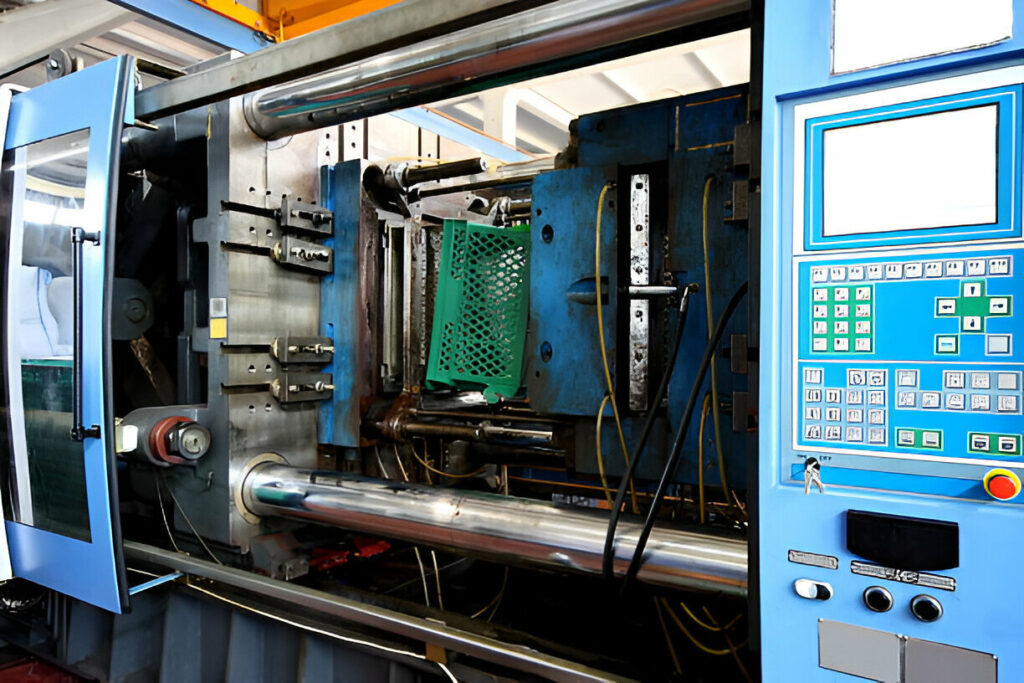
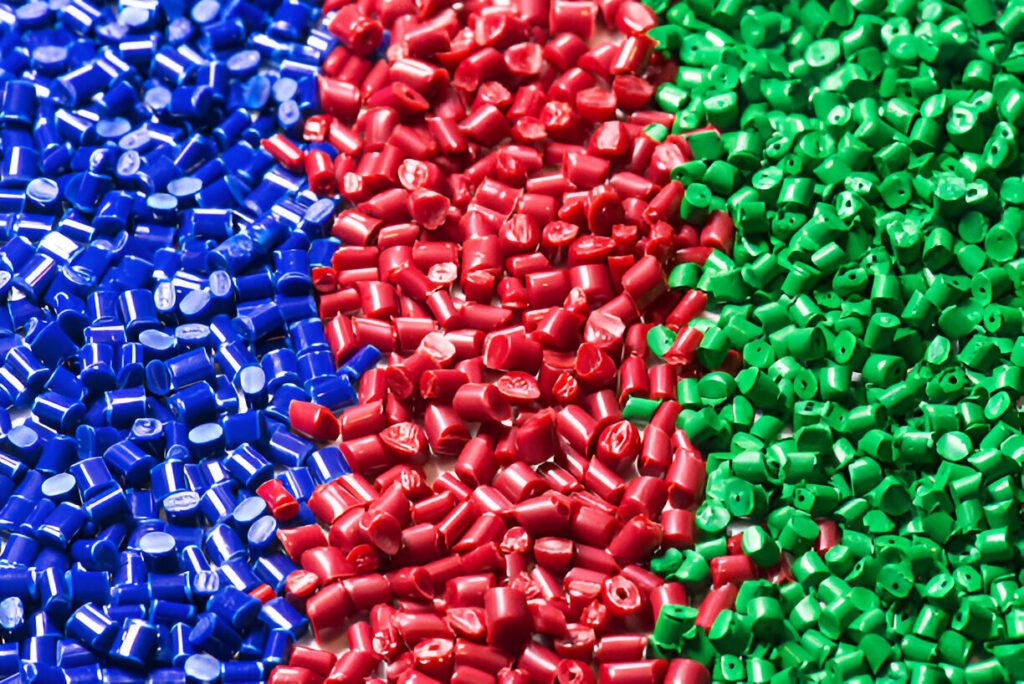
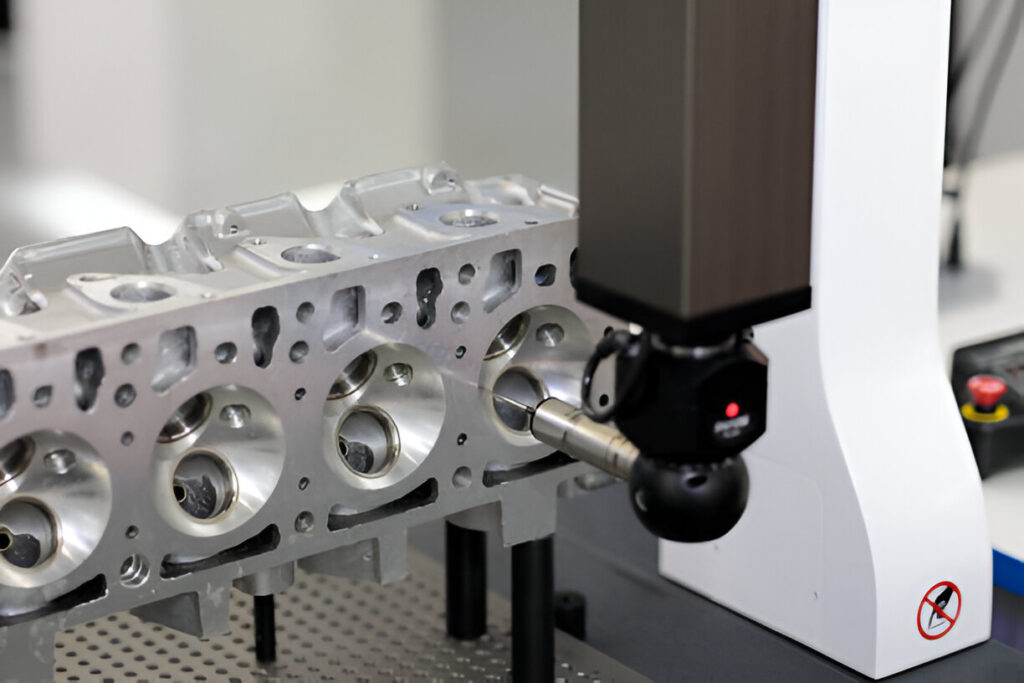
7. Material Recycling and Sustainability
The use of recycled materials and sustainable practices can help achieve weight savings and environmental advantages.
a) Recycled Injection Molding Plastic
Use post-consumer or postindustrial recycled plastics, which often have lower densities than virgin materials.
b) Closed-Loop Systems
Introduce closed-loop systems that will allow to recycle scrap back into production, which will reduce waste and overall quantity of material.
c) Light weight Additives
Incorporation of light weight additives or fillers to reduce the density without affecting performance.
8. Working with Experts Injection Molding
Work with suppliers of materials, mold makers and engineers who are anxious to help you find the most innovative ways to take weight out of your part. Many material suppliers have people on staff who are experts in both material selection and design optimization.
Conclusion
Weight reduction in injection molding is a complex process. It requires material optimization, design optimization, advanced molding and processing technologies. But when recycling and production costs are considered, it also represents a much sought after “green” or environmentally friendly solution.
Although some weight reductions in certain applications may actually increase the part cost – based on the considerations given above – for the vast majority of high-volume production parts’ weighting reduction leads to significant cost savings; improved product performance; achieving sustainability goals, being enabled to use less expensive materials or to further tailor materials properties as well as reaching important new market segments.
The best results come from using expert collaboration combined with simulation tools since only they can predict effects including those from specific designs, materials used and dedicated post-injection molding processes simulations.
Lightweight parts need not mean low strength or poor aesthetics as illustrated by paying attention to detail present case studies demonstrate- compression molded thermoplastic composite (CF/PP) automotive brackets.
0 Comments