The Plastic injection molding machine works in the following way.
How to operate a plastic injection molding machine? Start by loading plastic pellets into a hopper, which feeds them into a barrel. Inside the barrel, an internal auger, a screw-like device, rotates to move the material forward and prepare it for the molding process. The barrel and screw are heated by heat bands on the outside, melting the plastic into a molten state.
When the machine’s cycle begins, the mold closes and the auger, like a large plunger in a syringe, plunges forward under high pressure. The internal auger injects molten plastic into the cavity, which is an empty section of the mold, in less than a few seconds. The plastic forms into the shape of the cavity in less than 60 seconds on average.
The mold will then open when the plastic part has solidified, and the part is ejected. The procedure might resume once the plastic injection molding machine ejects the solidified plastic item.
Components of injection molding machine.
The injection molding machine has several components which include:
1. The Injection Unit
This component of the injection molding machine is responsible for heating and injecting resins into the plastic injection mold. A hopper, barrel, injector, reciprocating crew, screws, and nozzle are among the components of the device. The material is fed to a barrel through a hopper, which is a huge container with an open bottom.
The injection molding material is forced forward via a heated area by the barrel, which is equipped with a ram injector. Injection molding materials are propelled forward using reciprocating screws. The resins are then forced to travel towards the plastic injection mold through the slots in the screw. The resins and molten metal are melted in the heating channel.
2. The Clamping Unit
Molds are normally made in two sections, which are clamped together. The injection molds are fastened together just before the injection procedure. Each half must be secured to the platen, which resembles a huge plate.
The molds are opened with a clamping motor after the injected molten resins have cooled to the desired temperature. The solid plastic object was forced out of the open chamber by an ejection system with an ejection bar in the back half of the mold.
3. The Mold Base
The mold core and the mold cavity are the two major components of a mold. These two components are attached to the platens of a mold base to form a pair. The support plate, sprue bushing, and locating ring on the front part of the molded baseline the mold base with the nozzle.
An ejection system and a support plate are located on the back part of the mold base. As previously stated, the ejection system includes an ejection bar. It aids in the removal of solidified plastic injection molds from the mold cavity, as the name implies.
4. The Mold Channels
Mold channels are the channels via which plastic resins flow into mold cavities. To make a single component, these channels are incorporated into the mold design. The molten plastic enters through the sprue and then continues into the runners.
The runners guide the plastic resin through a gate, allowing the molten resin to fall into the hollow. Cooling channels are occasionally made to let water travel along the mold walls and speed up the cooling process of molten plastic.
5. Mold Design
In addition to the mold base and mold channels that are discussed above, there are a number of other designs that should be considered while building a mold. Complex geometries and features must be included in the plastic injection mold design for instance the undercuts.
Some devices can also be introduced along the parting direction into the injection mold. The injection molding design includes the draft angle that is applied to the mold walls.
6. Mold Tooling
Molds manufactured of steel or aluminum are used in custom tooling. Each metal has its own set of benefits and is employed in different ways, of course, based on the sort of plastic part needed. The two primary components of the part cavity are the mold core and mold cavity. When the mold is closed, the area between these two forms the part cavity, which is then injected with molten plastic resin.
7. Specifications of Machines
A plastic injection molding machine has different specifications. Injection molders are typically characterized by the clamp force tonnage that they provide. The pressure used to inject the molten resins also plays a big role. High tonnage is required for materials that require a high injection pressure. The shot capacity, clamp stroke, mold thickness, and platen size are all critical variables that must be considered when purchasing a plastic injection molding machine.
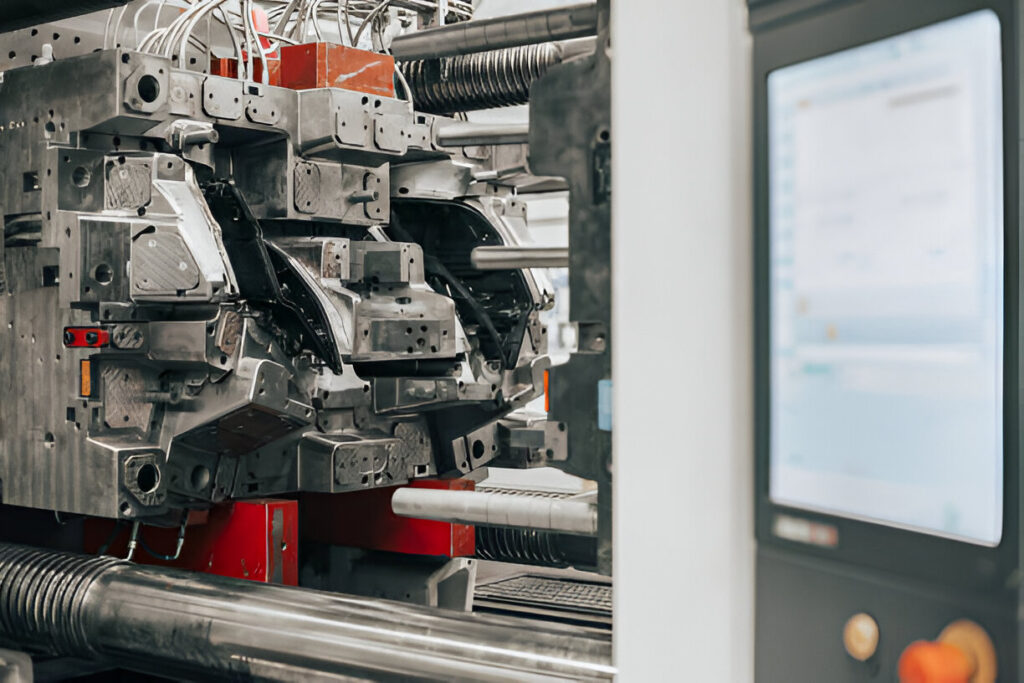
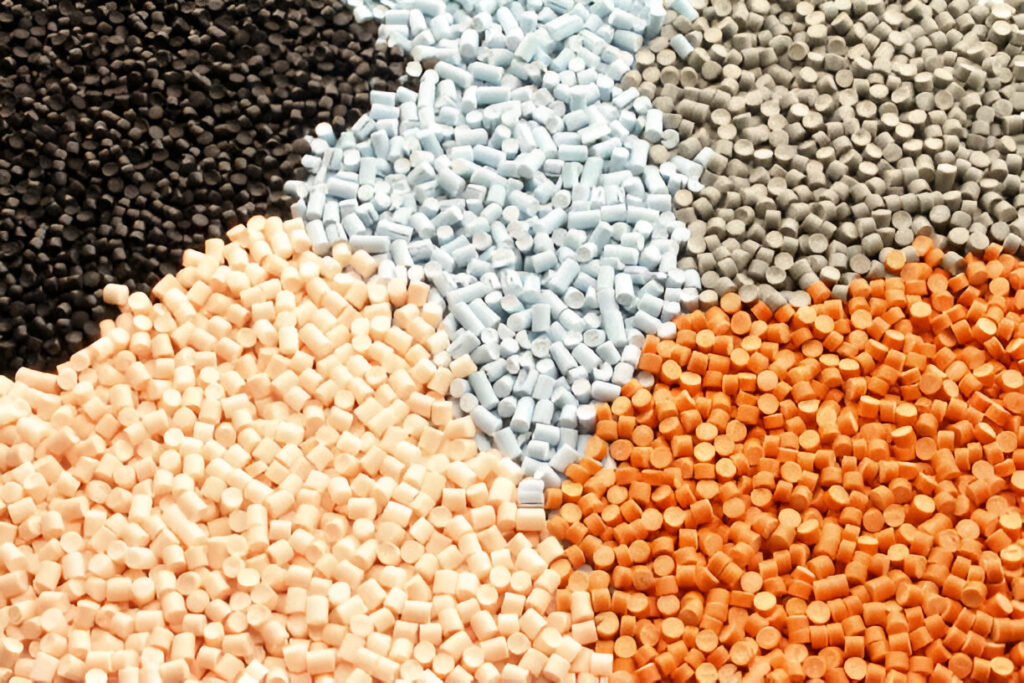
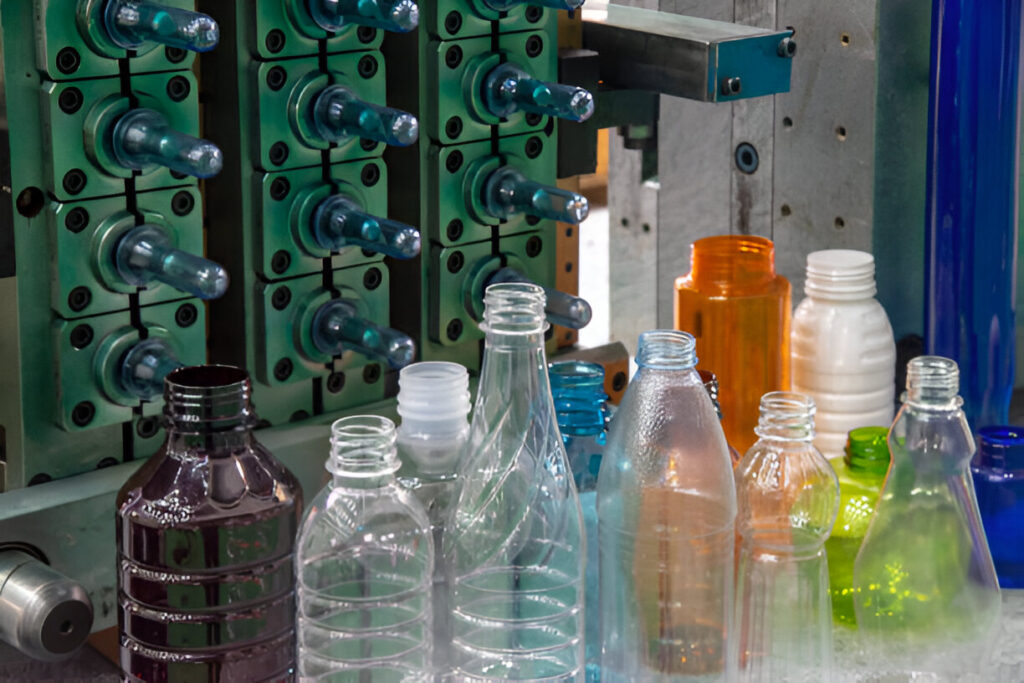
Types of plastic injection molding machines.
Basically, molding machines are classified according to the kind of drive systems they employ. They include hydraulic, electrical, and electrical injection molding machines.
Hydraulic Injection Molding Machine:
when the first all-electric injection molding machine was introduced, the hydraulic technique was the only alternative accessible to molders. During the injection molding process, pressure-creating substances known as hydraulic oils are used to create pressure. This oil is pumped through a hydraulic motor, which rotates the screw.
The creation of leak-free systems for the molding process is one of the most important aspects of hydraulic injection. Hydraulic oil may frequently spill into the plastic, causing imperfections. To protect the engine, it was necessary to carefully study seal design. Hydraulic injection molding machines have been popular due to their inexpensive cost and ease of maintenance.
Electrical Injection Molding Machine:
The first electronic hydraulic machine was introduced in Japan in the 1980s. It has been utilized as a replacement for the larger hydraulic machine ever since. High-speed service motors are used in electrical injection molding. It is simple to operate and more modern than the traditional hydraulic ones.
Based on the injection molding cost, a lot of factories prefer this type of machine. This is because of the comfort and speed of production provided by this equipment; it is extremely cost-effective. At the same time, an electric hydraulic machine requires less maintenance and has a digital control option. This allows you to customize the amount of energy and pressure required.
Hybrid Injection Molding Machine:
Hydraulic injection molding and electrical injection molding are combined in this molding technology. It was created with both molding advantages and has proven to be superior to the previous two varieties. This molding method is very flexible and has the same selling quality as the previous two types of molding machines.
A hybrid injection molding machine is preferred by many injection molding companies because it can save energy like an electrical system while maintaining the hydraulic unit’s accuracy. It may switch between the DC pump motors and the hydraulic pump, allowing each to function just when it is required. There are no quality compromises as a result of this.
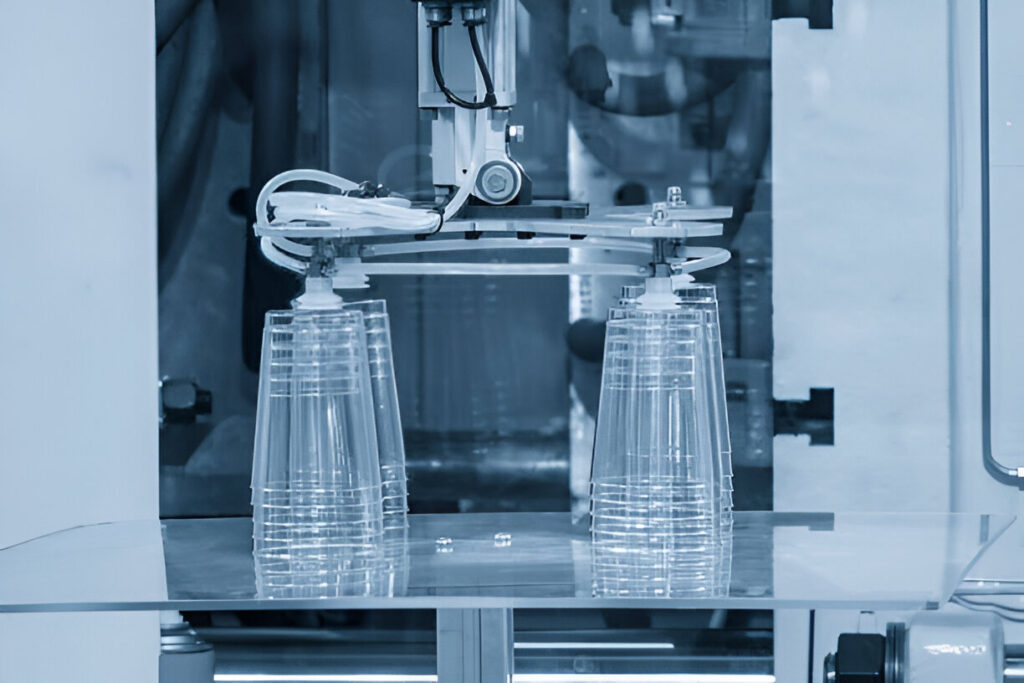
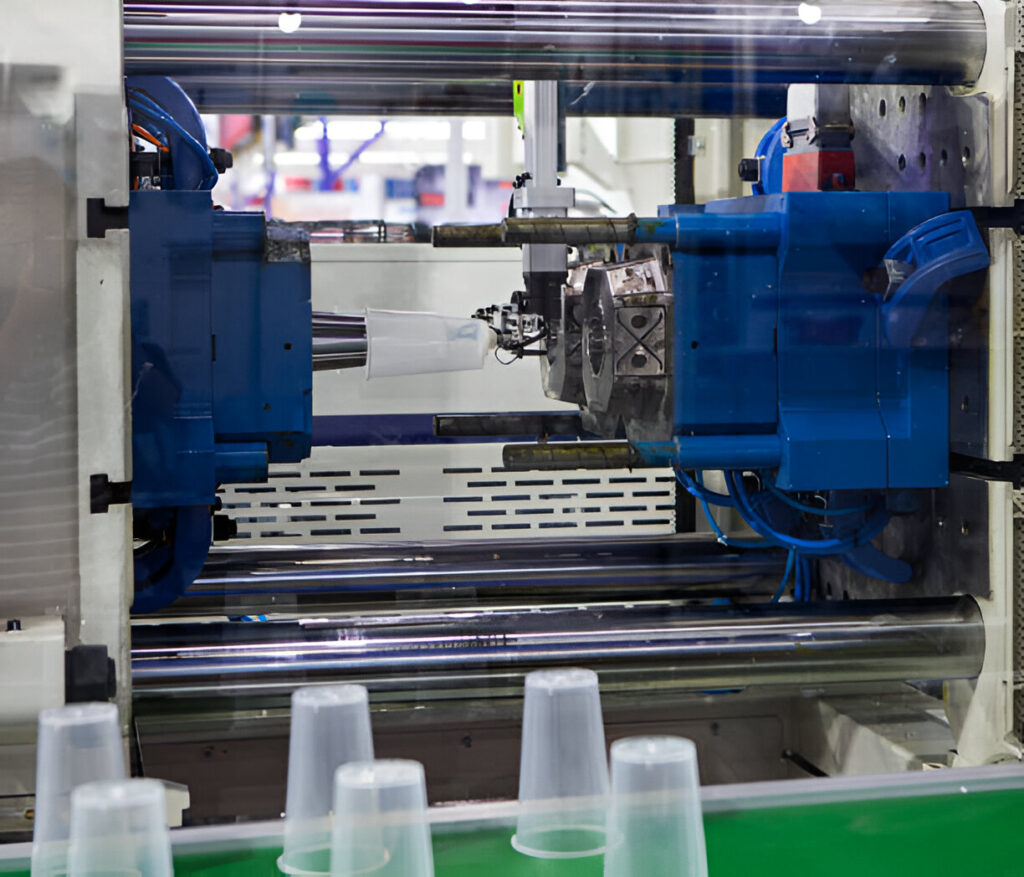
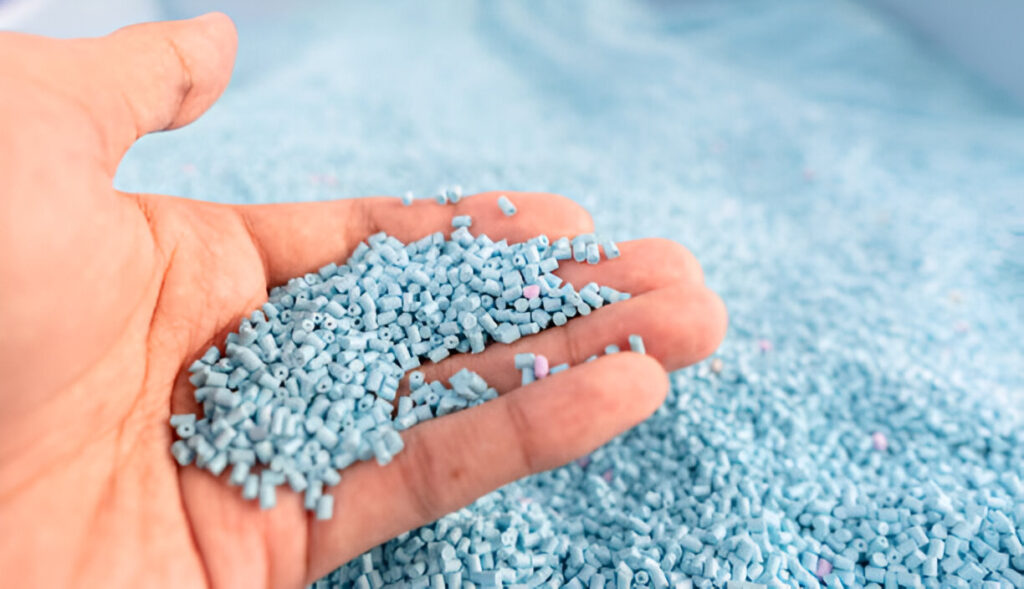
Conclusion
Injection molding is an excellent method for large-scale production. But how to operate a plastic injection molding machine? It is both an art and a science, requiring a deep understanding of the machine, material properties, and production parameters. By following the steps outlined in this guide, you can ensure efficient, safe, and high-quality operation. Whether producing small consumer goods or industrial components, injection molding remains a reliable and cost-effective manufacturing method.
0 Comments
Trackbacks/Pingbacks