Hydraulic, Electric Plastic Injection Molding is most popular manufacturer industry where it’s made plastic parts. It works by injecting molten plastic into a Mold, then its cools down and hardest and it takes their desire shape. Mainly it is used in automotive, electronic, and consumer goods because it is easy-to-use and cost efficient. If it is made at once we produce product at large amount.
There are three main types of machines used for plastic injection molding: hydraulic, electric, and hybrid machines. These machines work in a different way and has its own advantage and disadvantage. In this article, we will understand about these three types of machines, how they work, and which is best for use.
Introduction to Hydraulic vs. Electric Plastic Injection Molding
Plastic injection molding is a critical process in manufacturing that shapes products based on daily use and for other purposes. In this it allows the companies to produce large quantities of products and provide details about the plastic parts in an efficient and accurate manner.
From car parts to medical devices, injection molding is playing a big role in today live. It is a development process in which we will explain it like a story, how it progressed and evolved.
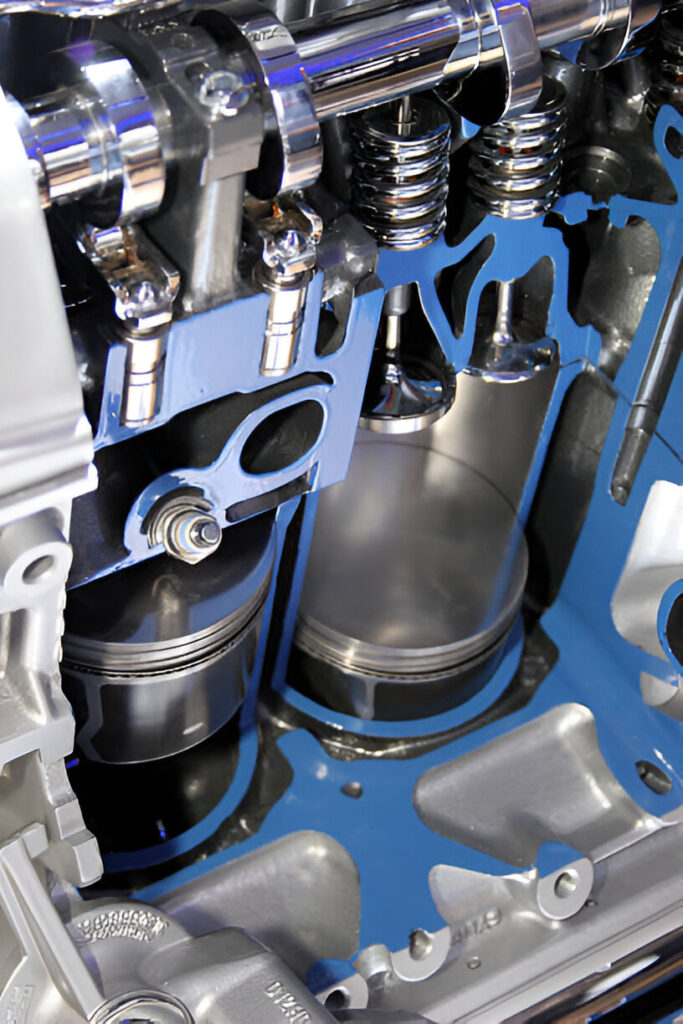
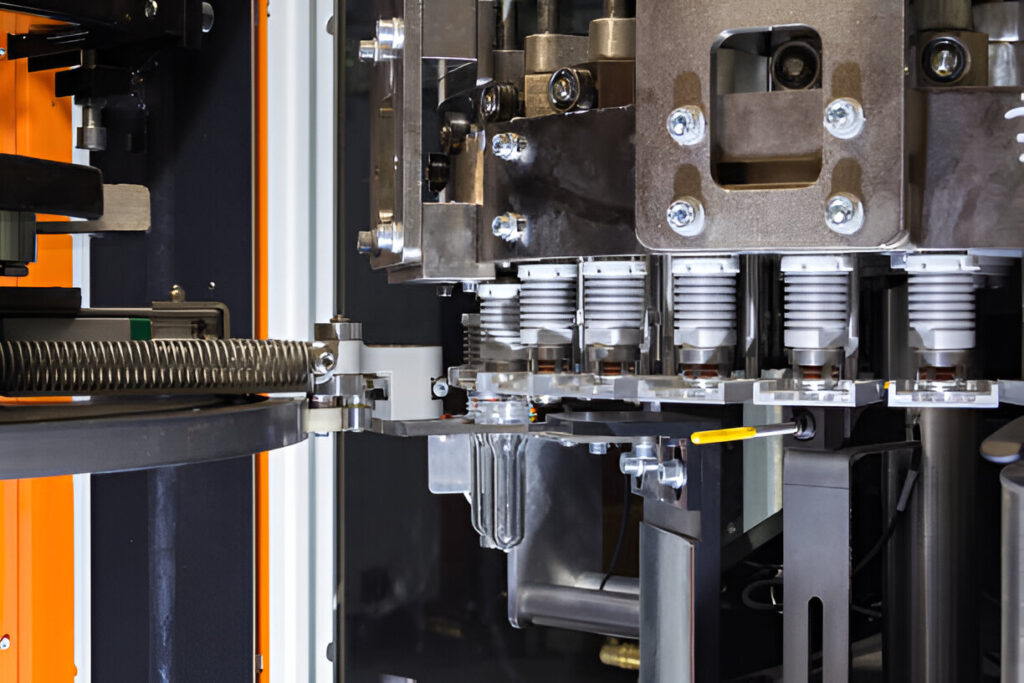
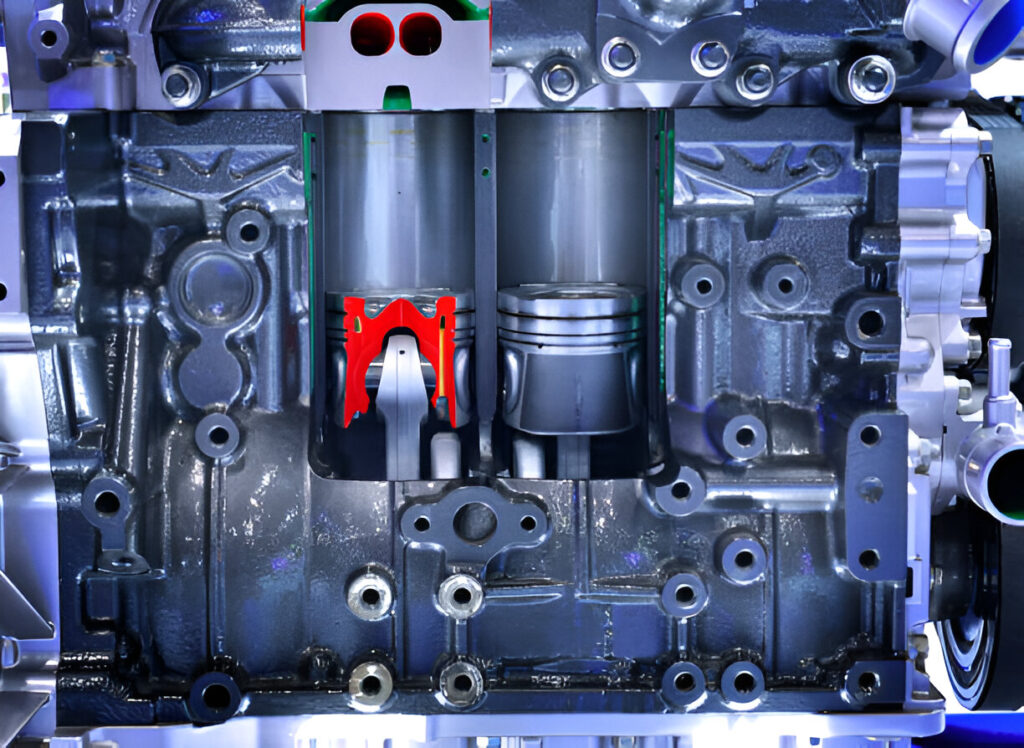
1. What is Hydraulic Plastic Injection Molding Machine ?
Hydraulic injection molding machine is a large injection molding machine. The action of the hydraulic injection molding machine is to control every action of the injection molding machine by controlling the flow, pressure and direction of the hydraulic power source.
Hydraulic injection molding machines first appeared in the late 1930s and once occupied a dominant market position, but since the introduction of electric injection molding machines in the 1980s, their dominance has been affected.
Judging from the current development, hydraulic injection molding machines will still occupy a dominant position for a long time to come.
How It Work ?
The injection molding machine has three main parts: The feed hopper, the screw, and the heated barrel. This machine works by taking plastic powder or granules and shaping them into a part as per the required size and design.
First, the plastic granules are fed into the feed hopper. The screw then creates heat through friction, melting the plastic. Once the plastic is at the right temperature, it is injected into a mold cavity, where it cools down and takes the shape of the mold.
Advanced techniques like repeated injection can be used to make parts from multiple materials if needed. Insert molding can also be used to add plastic parts over existing parts made from other materials.
Though the basic idea of injection molding may seem simple, it is actually a complex process that needs the right equipment and expertise. But when done correctly, injection molding can produce excellent results, even for the most difficult manufacturing projects.
Advantages of Hydraulic vs. Electric Plastic Injection Molding
- Strong Performance: Ideal for molding large or complex parts.
- Versatile: Can process a wide variety of materials.
- Durable: Built to handle heavy use in high-volume production.
- Lower Initial Cost: Generally cheaper to buy than electric or hybrid machines.
Disadvantages of Hydraulic Machines
- High Energy Use: The hydraulic pump runs continuously, even when idle, consuming more power.
- Heat Issues: Generates heat, requiring additional cooling.
- Maintenance Needs: Requires regular maintenance to prevent oil leaks and other issues.
2. What is Electric Plastic Injection Molding Machine?
Electric Plastic injection molding machine are a major advancement in injection molding technology. Use electric servo motors to control all movements, unlike traditional machines that rely on hydraulic systems for tasks like opening and closing molds, injecting plastic, and ejecting products.
In these electric machines, servo motors replace the hydraulic systems, resulting in greater precision and faster operations. The addition of pressure and temperature sensors allows for better control, leading to more accurate manufacturing.
These machines are particularly useful in industries where high precision and consistency are crucial, such as in making medical devices and precision electronics. Overall, electric injection molding machines represent a step forward in technology, offering efficiency, precision, and environmental friendliness.

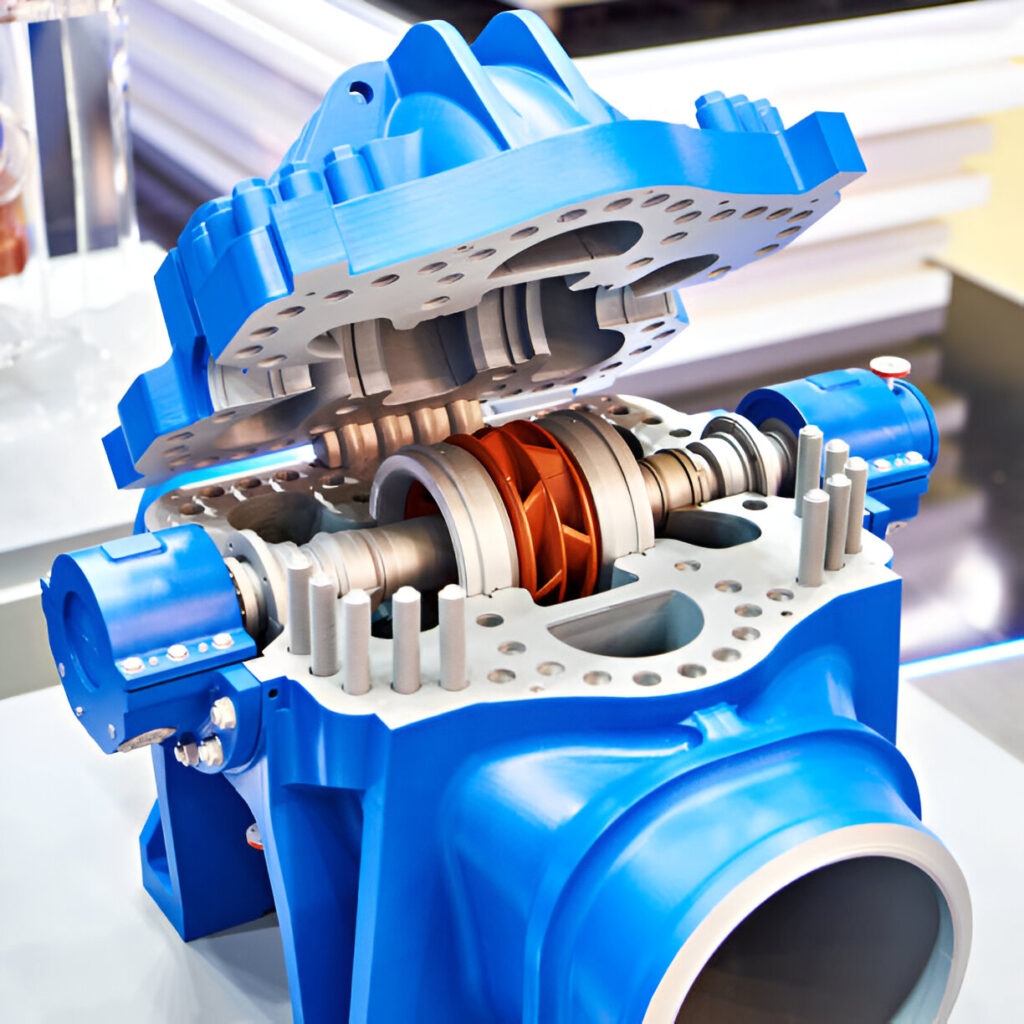
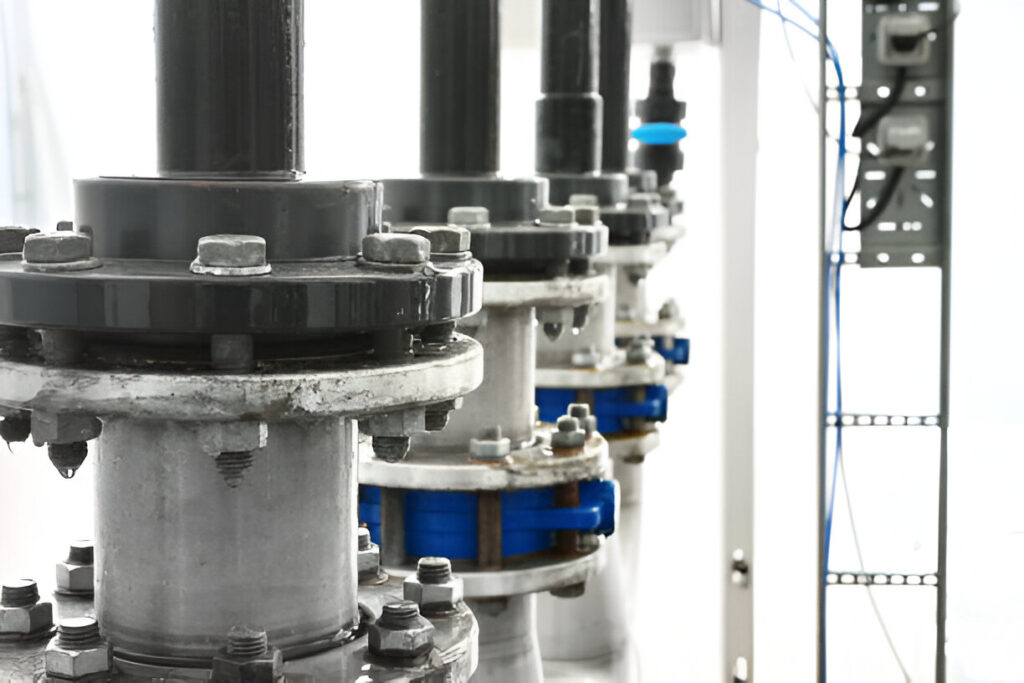
How It Work?
These machines use high-speed servo motors controlled by digital systems instead of hydraulics. This makes them faster, more precise, and more energy-efficient. Because the operation of electric machines is very predictable, once the desired injection process is set, it can be repeated consistently, resulting in better quality parts.
After programming a job into an electric machine, it can run almost automatically without much supervision, reducing labor costs and increasing profits.
Advantages of Hydraulic vs. Electric Plastic Injection Molding
- Energy Efficient: Motors run only when needed, saving energy.
- Precise and Repeatable: Ideal for producing small, intricate parts with high accuracy.
- Faster Cycles: Shorter cycle times lead to increased production efficiency.
- Clean Operation: No hydraulic oil is used, making them suitable for clean environments.
Disadvantages of Electric Machines
- Higher Initial Cost: More expensive to purchase than hydraulic machines.
- Limited Clamping Force: May not be suitable for very large or complex parts.
- Material Limitations: Some high-temperature or abrasive materials may be challenging to process.
Conclusion
Hydraulic vs. Electric Plastic Injection Molding both have own strength and challenges. Hydraulic machines are powerful and electric machines are precise and efficient. Which machine will be right for you depends on several factors such as Part size, product volume, material need, budget and impacts.
As we can see, electric injection molding machines are performing very well. The only drawback seen is mold clamping. The force provided is not sufficient, it is necessary that the full Hydraulic vs. Electric Plastic Injection Molding be produced in large quantities so that the parts can be delivered.
If you are looking for a suitable manufacturer to buy a hydraulic injection molding machine, you can pay attention to our products. It is an enterprise specializing in the production of high-tech injection molding machines.
With its strong independent research and development capabilities and strict quality supervision system, Mouldible injection molding machines supply various types of hydraulic and electric injection molding machines to the market, which have the advantages of high efficiency, energy saving, high pressure and high speed, precision and stability.
0 Comments
Trackbacks/Pingbacks