Plastic injection molds are the backbone of modern manufacturing, facilitating the mass production of precision plastic components used in industries such as automotive, medical, electronics, and consumer goods. However, these molds are subjected to immense stress, high temperatures, and repetitive use, making them prone to wear and damage over time. Issues such as cracks, corrosion, misalignment, and blocked cooling channels can disrupt production, reduce part quality, and lead to costly downtime.
Injection Molding Machine Repairing plays a crucial role in restoring the functionality and efficiency of these essential tools. Whether it involves fixing minor wear or addressing significant damage, timely and effective repairs can extend the lifespan of a mold, maintain consistent part quality, and minimize operational disruptions. In this guide, we explore the repair process, common challenges, and preventive measures to ensure injection molds remain in optimal condition for long-term use.
Understanding Injection Molding Machine Repairing
Injection mold damage can occur due to various reasons, including wear and tear, accidents, and improper maintenance. Some common types of damage include cracks, dents, and scratches. It is essential to identify the type and extent of damage before proceeding with the repair process.
Excessive stress, temperature fluctuations, or poor-quality materials can cause cracks in the mold. Improper handling, collisions, or foreign objects getting stuck in the mold can result in dents and scratches. It is crucial to address the damage as soon as possible to prevent further damage and maintain the quality of the final product.
Injection molds are designed to last a certain number of cycles based on their mold class specification requirements. Once the mold reaches its usable life, signs of wear will appear, and you will need to replace components. When the mold is nearing the end of its functional life, it is essential to start looking at long-term repair costs, proactively sourcing back-up parts, and potentially complete mold replacement.
Let us discuss the key factors in determining whether to repair a mold:
Common Injection Molding Machine Repairing Techniques
There are several techniques used for Injection Molding Machine Repairing, including welding, grinding, and machining. Welding is often used for repairing cracks and other types of damage. The damaged area is first cleaned and then welded using a specialized welding machine. After welding, the area is ground and polished to restore the original shape of the mold.
Grinding is used for removing dents and scratches from the mold surface. The damaged area is first identified and then ground using a specialized grinding machine. The area is then polished to restore the original finish of the mold.
Machinists repair extensive damage like deep scratches or large dents by first identifying the damaged area. They use specialized machines to remove the damaged material and apply new material with a welding technique. Finally, they grind and polish the area to restore the mold’s original shape and finish.
Tooling Repair Prioritization
When prioritizing tooling repairs, it is important to consider the impact of the damage on production and the cost of repair. Repairs that will significantly impact production should be given higher priority, as delays can result in lost revenue. It is also important to consider the expected lifespan of the tooling when prioritizing repairs. If the tooling is near the end of its lifespan, it may be more cost-effective to replace it rather than repair it. On the other hand, if the tooling is relatively new and has a long-expected lifespan, repairs may be a more viable option.
Mold Repair – Parting lines
The parting line is nothing but where the two halves of the mold intersect along with the part parameter. All parting lines need to be adequately sealed while the mold is clamped in a molding machine.
Mold Repair – Gates
Each part of the injection molding service has one or more gate locations. The gate is where the melted plastic comes into the portion of the runner device. Mold builders can take special steps to measure and build the gate’s portion accurately. A significant concern, especially for high-volume molding applications, is preserving the gate over time. Now, let’s discuss why the gates wear and how to solve this problem.
Ejector Pin & Hole Wear
Ejector pins (knockout pins) sit around the surface of the element. During the injection molding process, the ejection assembly retracts, making the ejector pins flush with the tooling surface. Then, the ejection system and pins advance, ejecting the component from the molding board.
Since the ejection systems cycle back and forth during each molding cycle, the guide hole in the tooling surface or the pin itself may wear over time. That wear will display like flashing around a pin (since plastic can flow into the wear area).
Repair Processes
When it comes to repairing injection mold tooling, there are several processes that can be used. Each process has its own advantages and disadvantages, and the best one to use will depend on the specific situation.
In this section, we will discuss three of the most common repair processes: welding and resurfacing, component replacement, and precision machining.
Welding and Resurfacing
Welding and resurfacing is a common repair process for Injection Molding Machine Repairing. This process involves welding new material onto the mold to fill in any gaps or cracks that may have formed. Once the welding completes, workers resurface the mold’s surface to ensure it remains smooth and even. This process often addresses small cracks or other imperfections that need repair.
Component Replacement
Component replacement is another common repair process for injection mold tooling. This process involves replacing any may include replacing things like ejector pins, bushings, or guide pins damaged or worn components in the mold with new ones. This Component replacement is often used when there are specific parts of the mold that are damaged or worn out and need to be replaced.
Precision Injection Molding Machine Repairing
Precision machining is a more complex repair process that involves using specialized machinery to repair the mold. This process is often used when there are more serious issues with the mold, such as large cracks or other damage. Precision machining involves using a CNC machine to remove any damaged material from the mold and then replacing it with new material. This process is very precise and can take a significant amount of time, but it is often the best option when there are serious issues with the mold.
Finishing and Polishing
When it comes to injection mold tooling repair, finishing and polishing are essential steps to ensure the mold is in optimal condition for production. The finishing process involves removing any burrs, sharp edges, or other imperfections that may have occurred during the repair process. Polishing, on the other hand, is the process of smoothing out the mold’s surface to achieve a desired finish.
Surface Finishing Techniques
There are several surface finishing techniques that can be used to achieve a smooth finish on an injection mold. These techniques include:
- Sanding: This technique involves using sandpaper to smooth out rough surfaces on the mold. Sandpaper comes in different grits, and the coarseness of the grit used depends on the level of roughness on the mold’s surface.
- Bead Blasting: Bead blasting involves using small glass beads to blast the mold’s surface, removing any roughness or imperfections. This technique is particularly useful for removing rust or other types of corrosion.
- Chemical Etching: Chemical etching involves using chemicals to dissolve the mold’s surface, creating a smooth finish. This technique is particularly useful for removing stubborn stains or other types of discoloration.
Polishing Standards and Quality Control
Polishing plays a critical role in the injection mold tooling repair process. It is essential to polish the mold’s surface to the appropriate standard. The Society of Plastics Industry (SPI) has established a set of standards for polishing injection molds. These standards range from A-1 (the highest level of polish) to A-3 (the lowest level of polish).
To ensure the mold’s surface is polished to the appropriate standard, we must implement quality control measures. These measures may include using specialized equipment to measure the mold’s surface roughness or using visual inspection techniques to identify any imperfections. Finishing and polishing are critical steps in the injection mold tooling repair process. By using the appropriate surface finishing techniques and adhering to established polishing standards, you can ensure that the mold is in optimal condition for production.
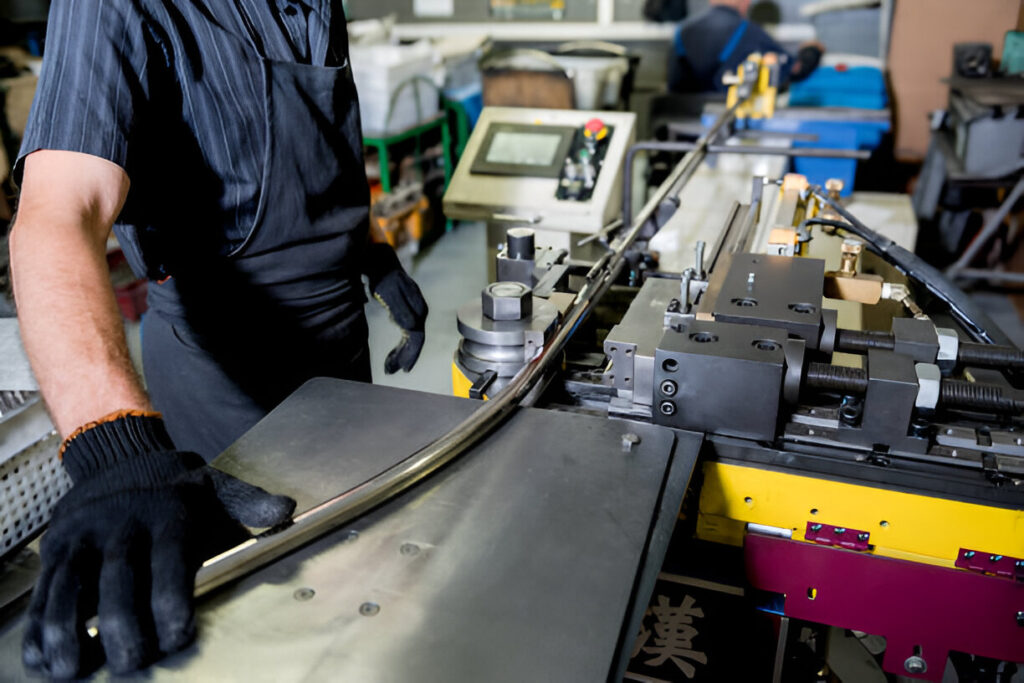
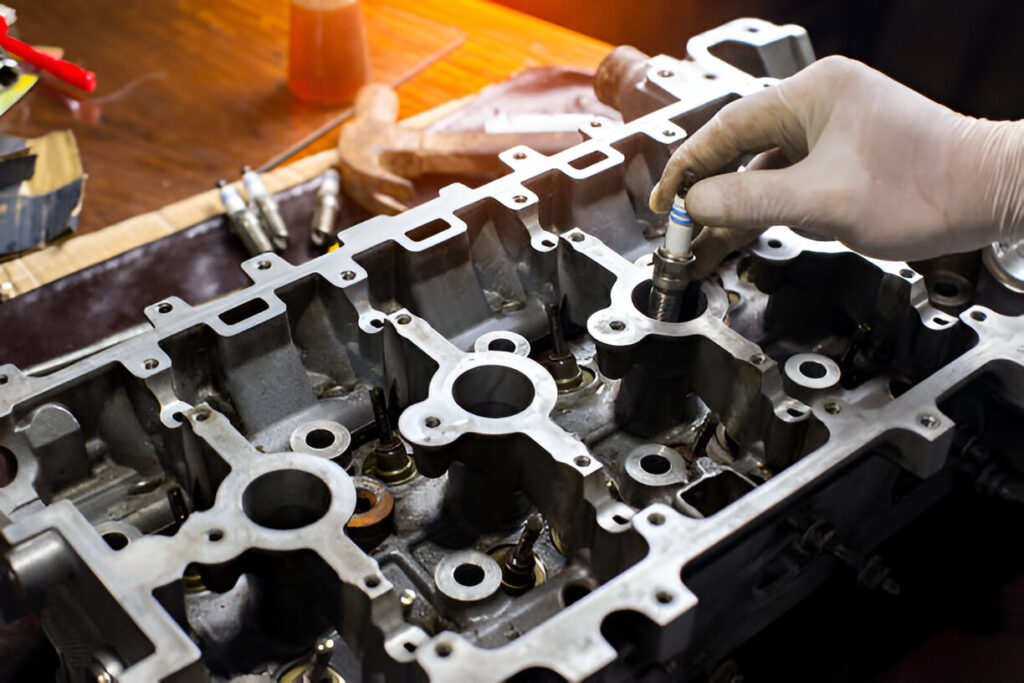
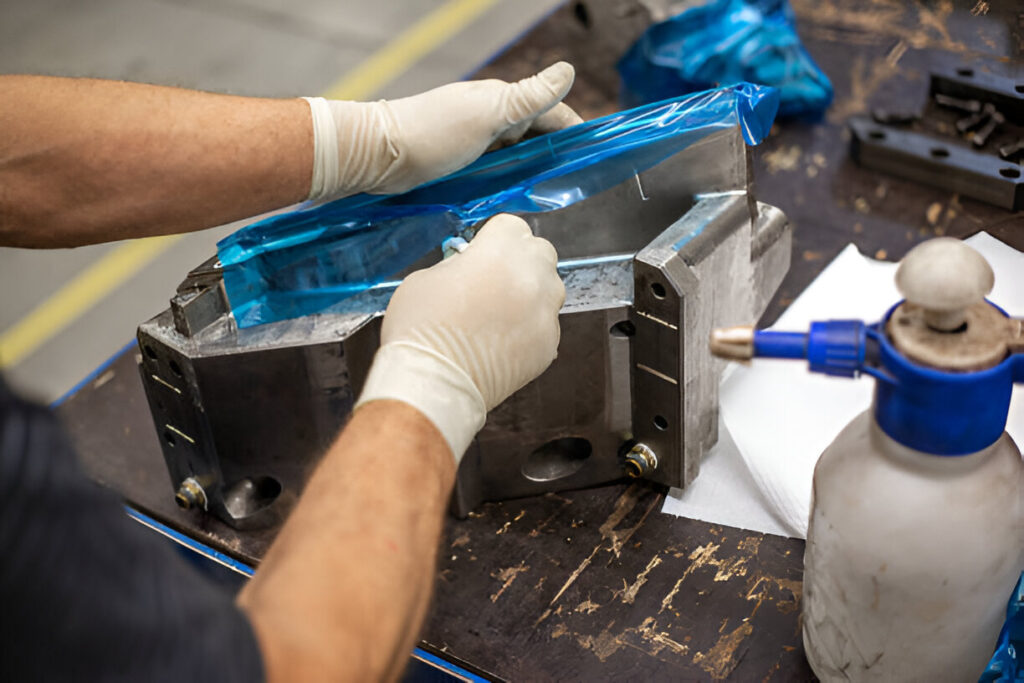
Conclusion
Injection Molding Machine Repairing is a vital aspect of maintaining production efficiency and part quality. By understanding the common issues, following a systematic repair process, and implementing preventive measures, manufacturers can extend the lifespan of their molds and reduce operational costs.
Investing in regular maintenance, skilled technicians, and high-quality materials ensures that molds remain reliable and productive, even under demanding manufacturing conditions. A well-maintained mold is not just a cost-saving asset but also a cornerstone of consistent and high-quality production.
0 Comments