Injection molding is the most efficient and cost-effective method of plastic mass production in required quality. Injection molding tooling construction is crucial for the product development process, as tooling has major influence on the shape, surface quality, dimensional accuracy and number of possible details in product construction or assembly.
In this article we will introduce what injection molding tooling is, why it’s needed, its design process, main components and properties based on technical project requirements, as well as how it works in plastic product manufacturing industry.
1. Introduction to Injection Molding Tooling
Injection molding tooling, otherwise referred to as mold tooling, is the heart of injection molding. It is the physical equipment that transforms melted plastic into a molded part. Such molds are precision engineered to produce consistently high volumes of identical parts with extremely tight tolerances.
From automotive parts to medical devices, consumer goods and electronics, almost everything made from plastic by injection molding process owes its shape and properties to the tooling.
2. The Importance of Mold Tooling in Manufacturing
The mold tooling in injection molding plays a vital part for varied reasons. Some of them are:
- Precision and Accuracy: The tool defines the shape and size of the final product.
- Efficiency: Well-designed molds help to reduce cycle times and increase productivity.
- Product Quality: A mold of high quality ensures the part with minimum of defects and with a superior surface finish.
Though tooling is typically the most expensive item on an injection mold project, the investment often proves to be the best option for reducing overall part cost at high volumes.
For this reason, knowing something about molds and how they are built is a good idea for any designer or engineer wanting to take advantage of the full potential of additive manufacturing.
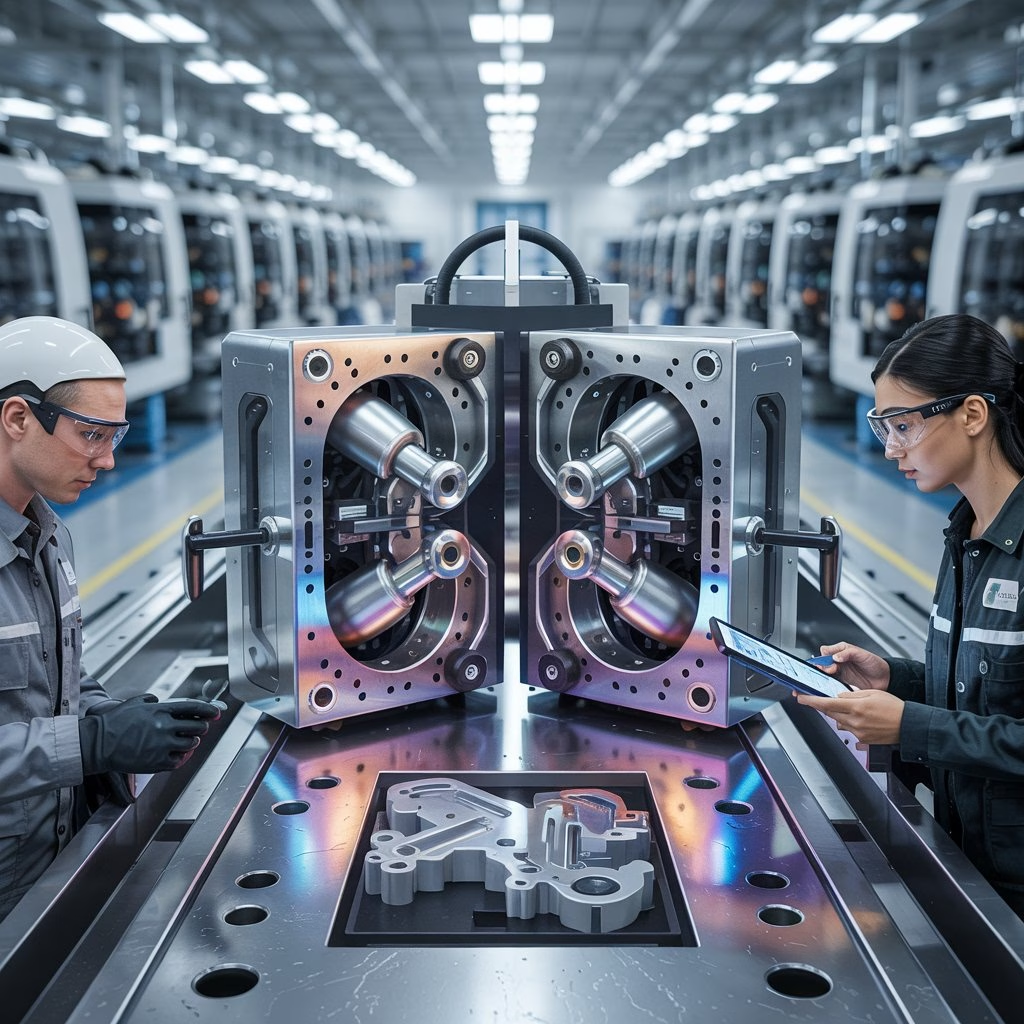
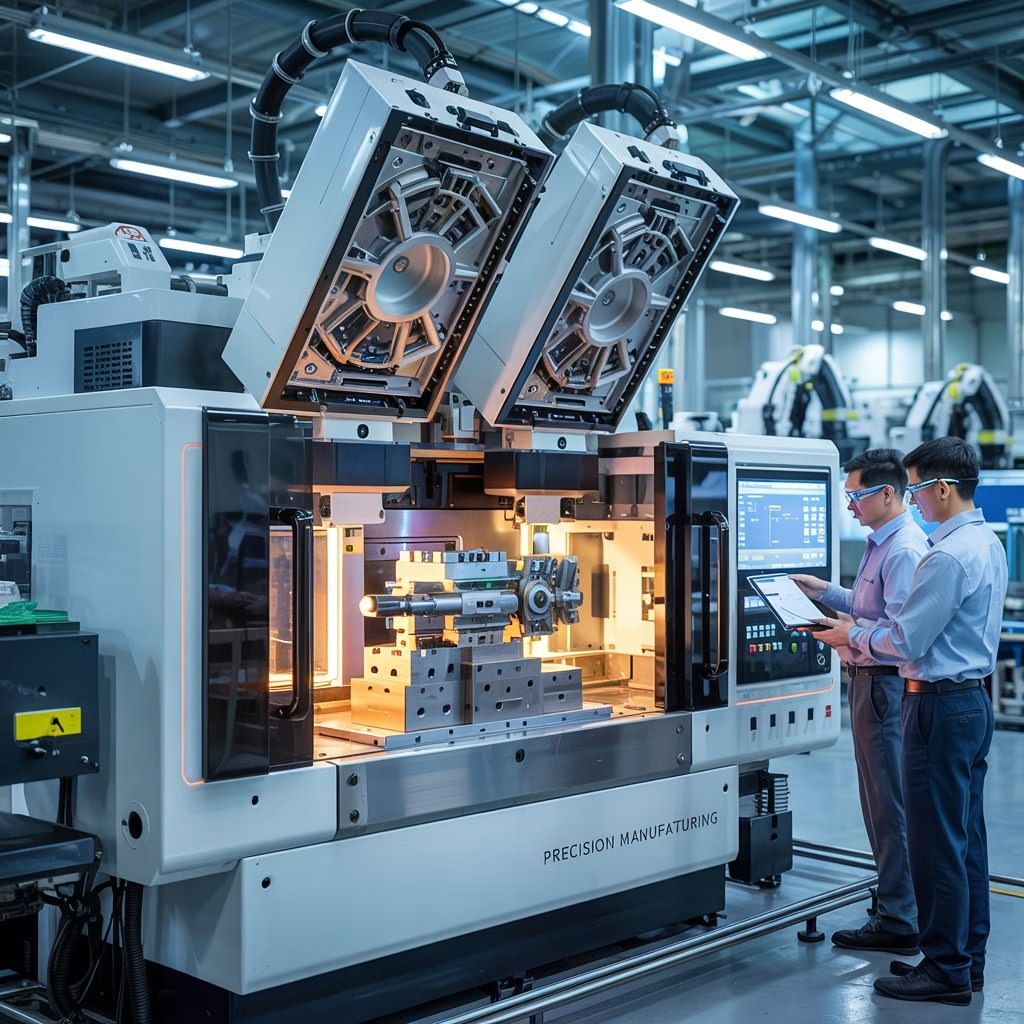
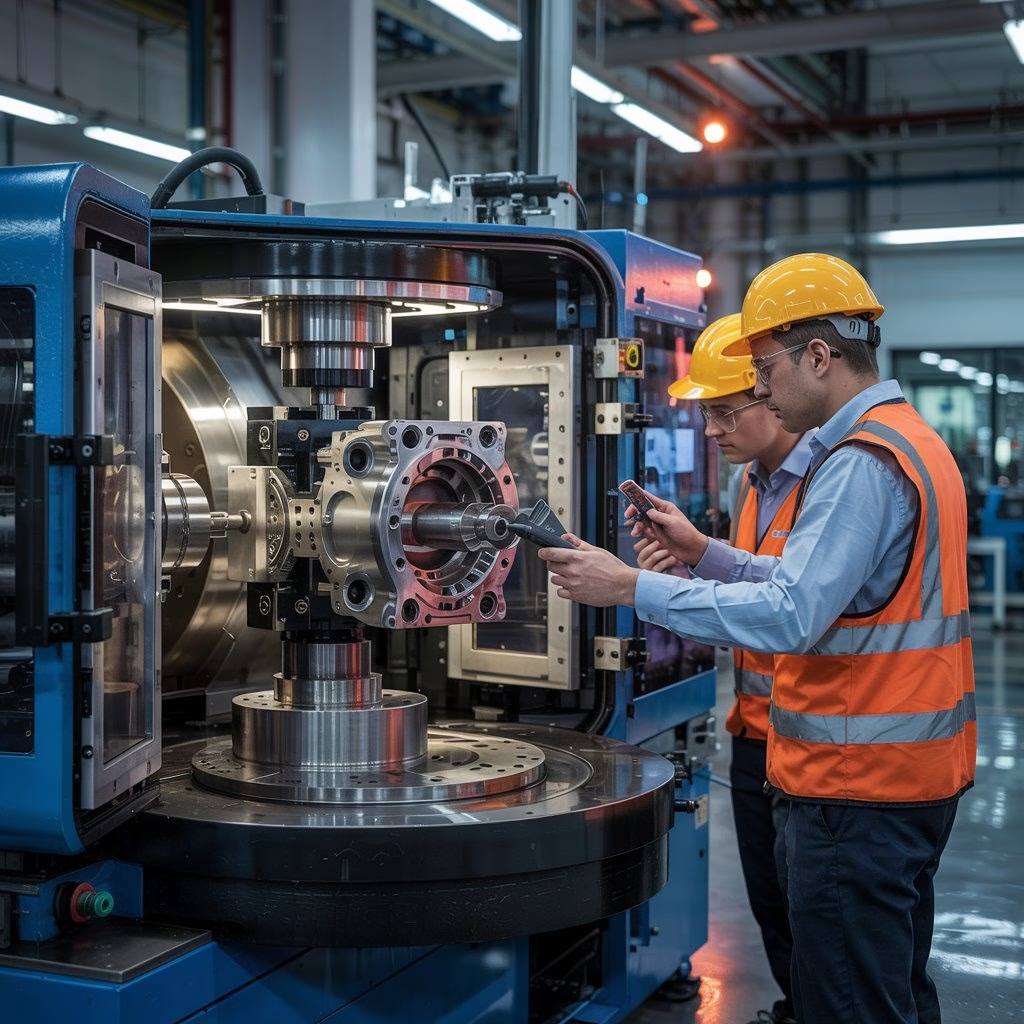
3. Key Components of Injection Molding Tooling
a. Core and Cavity
The core and cavity are the two main parts of the mold that directly shape the plastic part. The part is formed by injecting plastic into the cavity, which is then solidified and ejected from the mold.
b. Runner System
The runner system consists of channels that direct the molten plastic from the injection molding machine nozzle to the mold cavity. These channels must be designed accurately to achieve balanced flow and minimal wastage of material. Hot or cold runner systems can be used, depending on whether heated components are present in directing the temperature of the material. The design of runners indirectly affects the time required for a cycle, part quality and how much material is wasted.
c. Gates
Gates are the small restricted openings through which the molten plastic enters into the cavity from the runner system. Gate design, size, shape and its location influence the filling pattern of molten plastic in the cavity. Some common types of gates are edge gate, pin gate and sub-gate etc. The gate design should help in uniform filling so as to avoid any chance of air traps, and less defects like weld lines or burns marks etc.
d. Ejection System
After the molded part has sufficiently cooled down and solidified inside the mold cavity, it must be removed. The ejection system consists of ejector pins, sleeves, stripper plates and other mechanical components that will push the part out of the tooling. It is important to design this system in such a way so as not to damage the product while ejecting it from a tool mold, especially when dealing with complex geometries or fragile features. The ability for parts to eject smoothly and consistently also minimizes cycle time disruptions and prevents unnecessary wear on both parts and equipment.
e. Cooling System
A highly effective cooling system is essential to consistently maintain mold temperatures and reduce cycle time. Cooling systems consists of a network of water channels, baffles and often advanced techniques such as conformal cooling, – which involves using geometrically complex cooling lines that are positioned close to the mold cavity surface to optimally control temperature distribution. By ensuring uniform cooling, dimensional accuracy can be achieved along with reduced internal stresses within the part. Poorly designed or positioned cooling lines can lead to warping of the part or sink marks especially on thick sections of parts that require longer cool times.
f. Venting System
Vents are provided in the mold to allow the air trapped inside the mould and gases evolved by the molten plastics during injection process, to escape out of the mould. If these vents are not provided, then pressure built by this trapped air or gas may lead to incomplete filling or burn marks on container’s surface.
g. Mold Base
The mold base is the foundation of the entire tooling system. It holds all of the components together such as the core, cavity, runner systems and ejection mechanism. Mold bases are typically made from a hardened steel material able to withstand high clamping forces and production runs over an extended period of time. A well-machined mold base will provide precise alignment of all components, smooth performance and allows for interchangeability on various injection molding machines.
4. The Tooling Design Process
Injection mold tooling design is an art and science. It’s a specialist engineering discipline that integrates cutting-edge technology, decades of experience, and high-precision manufacturing. A modern systematic overview of your traditional, high-quality injection mold tooling design process typically consists of the various stages below:
a. Part Design Review
The first step involves a design for manufacturability review of the plastic part. Engineers analyze draft angles, wall thickness, undercuts, ribs, bosses and overall geometry to verify that the part can be adequately molded. This analysis highlights any design changes that could promote better mold performance, cycle time reduction and longer tool life.
b. Tool Design
Following finalization of the part design, the mold is designed 3D with advanced CAD software. The design includes core and cavity splits, gate locations, runner layouts, ejector systems, cooling channels, and venting. Digital collaboration between design and manufacturing eliminates manufacturability concerns while ensuring all attribute targets are met with no degradation of part performance/functionality.
c. Material Selection
Material selection is based on production volume, plastic resin type and performance expectations. For instance, P20 steel, H13 or stainless-steel are selected for high production volumes while aluminum is used for prototype or low volume tooling due to its machine-ability and faster turn-around time.
d. Mold Flow Analysis
Before steel is cut, mold flow simulation software is used digitally simulate the flow of molten plastic within the mold. This analysis allows us to identify potential problems such as air traps, weld lines, shrinkage, sink marks and warpage. Engineers can then optimize gate locations, runner systems and cooling layout to insure uniform filling and efficient cooling.
e. Machining and Fabrication
The approved mold design undergoes machining and fabrication using high-precision CNC and EDM (electrical discharge machining) processes. Technicians fabricate every component of the mold with tight tolerances. They assemble the core, cavity, sliders, lifters, and inserts precisely to ensure reliable mold functionality. Based on the final part requirements, they apply surface finishing, polishing, and texturing as needed.
5. Common defects due to the poor Tooling
No matter how advanced is your molding machine, poor mold design will eventually create defect. Let us see few of them:
- Sink marks are caused by inconsistent wall thickness
- Flash is caused by improper clamping or gate design
- Warping from uneven cooling
- Short shots when the mold isn’t filled completely
- Burn marks from trapped gases
- Jetting caused by high-speed injection and poor gate design
Avoiding these problems starts from accurate injection molding tooling design and mold making quality.
6. Advances in Injection Molding Tooling Technology
a. Conformal Cooling
Cooling channels are designed to follow the contour or shape of the part and are often produced using additive manufacturing (3D printing). Instead of straight-line cooling, as with traditionally manufactured tools, conformal cooling mimics the shape of the mold cavity and results in more uniform temperature distribution, reduced cycle times and higher part quality particularly with complex or thick-walled parts.
b. 3D Printed Molds
3D printing is massively transforming prototyping. Manufacturers now use materials like resin, composite, or even metal to quickly create molds at a fraction of the cost, while producing parts in the final intended real material. While it’s not adequate for high volume production, it makes creative part production easy, which significantly shortens development cycles.
c. High-Speed Machine
Technicians use advanced CNC tools in high-speed machining to quickly cut and shape mold components with extreme precision, reducing lead times and improving dimensional accuracy. It also allows for the production of complex geometries and fine surface finishes, which are essential for modern injection molding applications.
d. Automation and Sensors
Today’s smart molds use sensors to gather real-time data on temperature, pressure, humidity, and cycle time. This data enables predictive maintenance, minimizes machine downtime, and ensures consistent product quality. Automation features such as robotic part removal, insert placement and in-mold labeling contribute to increased efficiency and lower labor cost.
e. Modular Tooling
Modular tooling systems are where inserts and components can be easily replaced within a single mold to produce various parts or part families. This takes out the huge investment in high volumes of excessive tooling if you require a family of similar products. This is ideal if you have low to medium volume requirements and also if there is potential for new part introduction during the life cycle of your product.
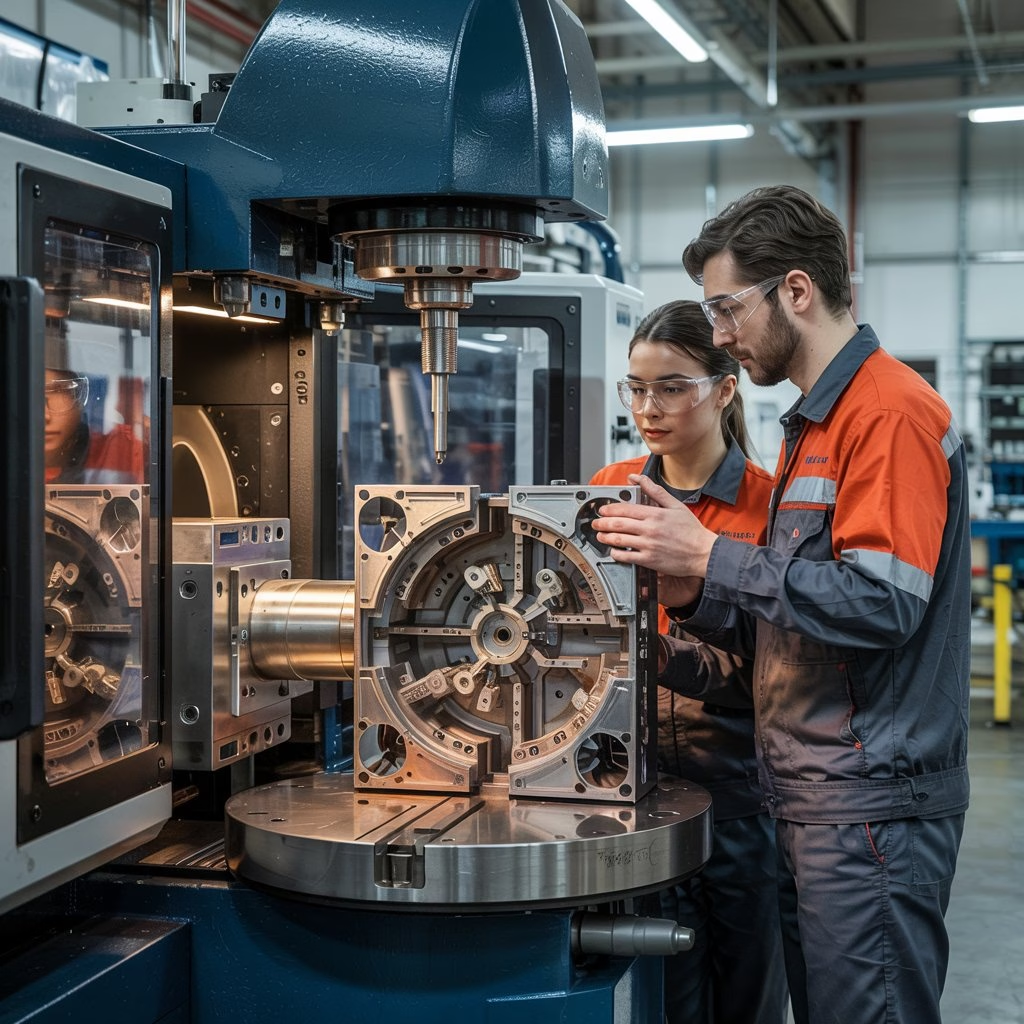
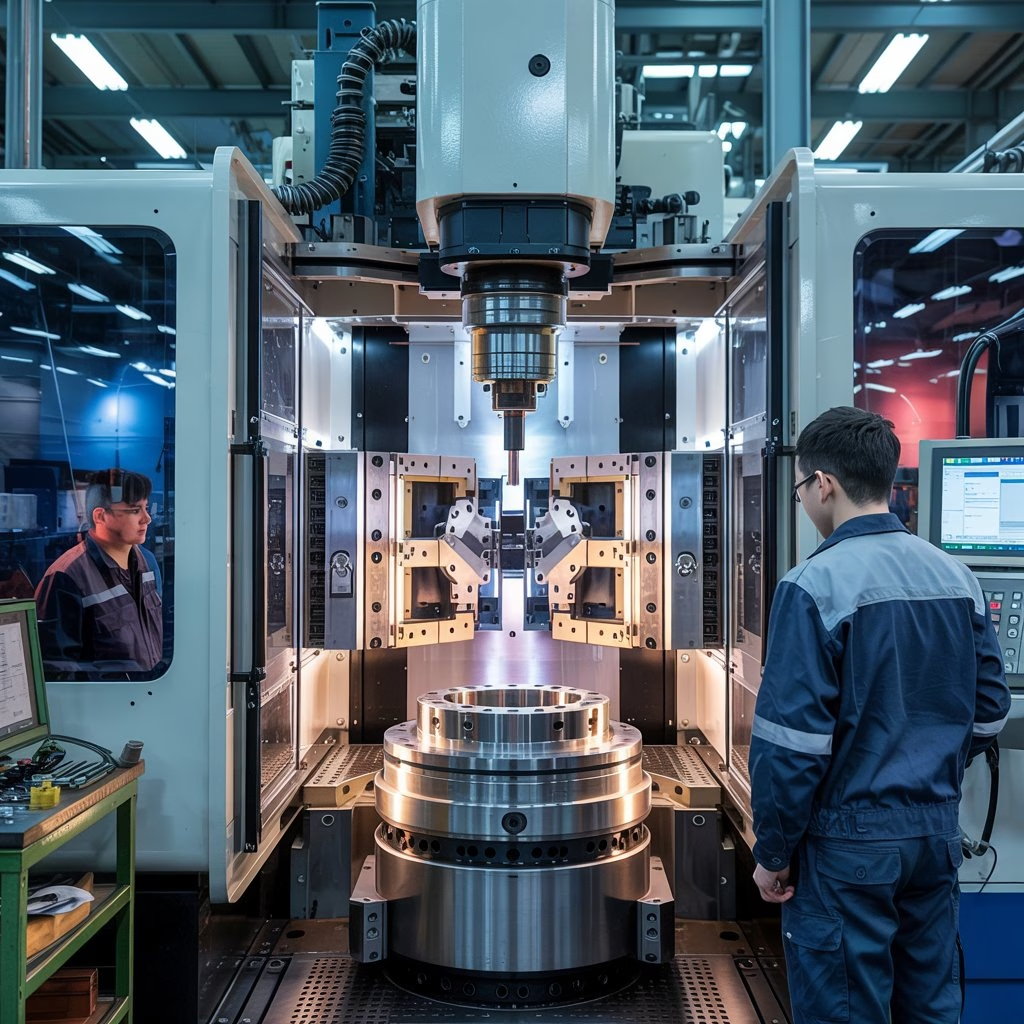
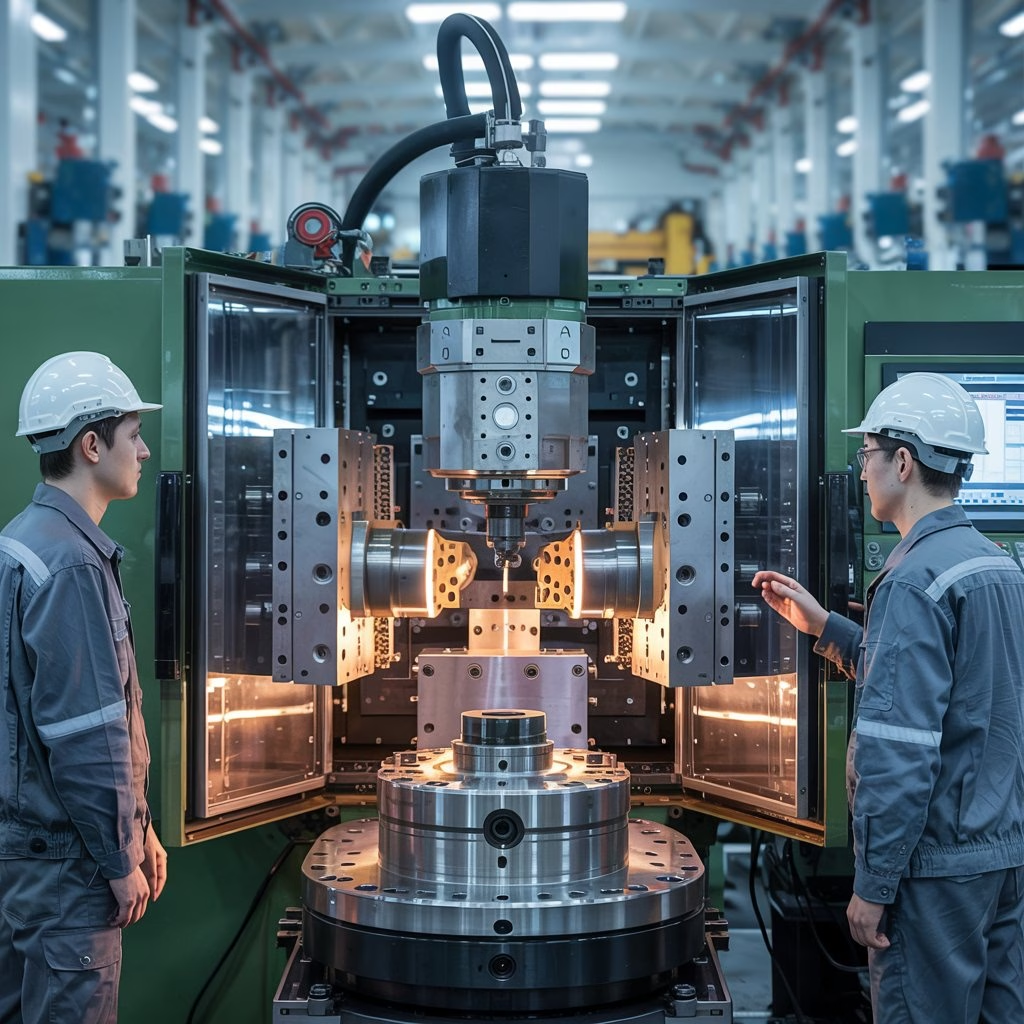
7. Industries Using Injection Molding Tooling
Virtually every industry uses injection molding for its plastic parts including:
- Automotive – dashboards, clips, connectors
- Medical – syringes, enclosures, surgical instruments
- Consumer Goods – toys, kitchenware, electronics
- Packaging – caps, containers, closures
- Aerospace – interior parts that are lightweight and durable
- Telecommunications – housing for connectors and devices
Manufacturers design injection molding tooling to meet the specific production requirements of different industries, ensuring production flexibility, high part repeatability, and cost efficiency.
8. Future Trends in Injection Molding Tooling
- As the industry advances, so does mold tooling. Watch for these future trends:
- AI and machine learning integration for predictive maintenance and process optimization
- Cloud connected molds transmitting live performance data
- Eco-friendly tooling materials with lower carbon footprints
Additive manufacturing (AM) is a promising technology for the direct fabrication of complex shaped metal parts with functional gradients, which cannot be efficiently or even possibly manufactured by traditional methods. It could also become an enabling technology for custom on-demand tooling to further improve productivity in many industries as it offers highly flexible, rapid design and manufacturing capabilities.
Conclusion
Injection molding tooling is the essence of productive and cost-effective injection molding. It lies at the heart of modern plastics manufacturing, which simply wouldn’t be feasible without this long-lasting capital equipment. In order to make astute business decisions regarding mold tooling, companies must first become familiarized with molds and injection molding tooling. Then they will be in a better position to organize, conduct, manage, and supervise projects that meet specified quality, time, and cost-based targets.
Either you are building your own injection mold or choose a high-quality mold maker partnered with us, whether you consider preliminary mold costs or decide for definite pricing before shipping, whether you design one cavity or like to implement family molds as part of automatic production equipment no matter what: in times of single-digit duplication cycles and long product-life cycles when quality matters most speed-to-market means using unsung hero.
0 Comments