Plastic injection molding materials is a widely used manufacturing process that creates custom-made plastic parts and components. A process involves injecting molten plastic material into a mold and allowing it to cool and give us the final product.
It is very important that we can understand the plastic injection molding material which plays crucial role in the functionalities, durability and appearance of the product. This article will help you explore and determine which plastic materials will best suit your product.
We will go through all these points one by one and will try our best to explain to you what are the specifications according to the requirement of materials.
1. Understanding Plastic Injection Molding Materials
Plastic injection molding materials are typically categorized into two board classes are as followed:
1.1 Thermoplastics
Plastic becomes soft and pliable when we provide heat and also upon cooling. It can be melted and reshaped multiple times and is ideal for recycling. Mostly plastic injection molding materials are found in all these categories.
1.2 Thermosetting Plastics
The material is such that once it has been molded and hardened then after cooling it does not remelted. It undergoes a chemical change during molding, which makes them set permanently. We use less commonly in plastic injection molding.
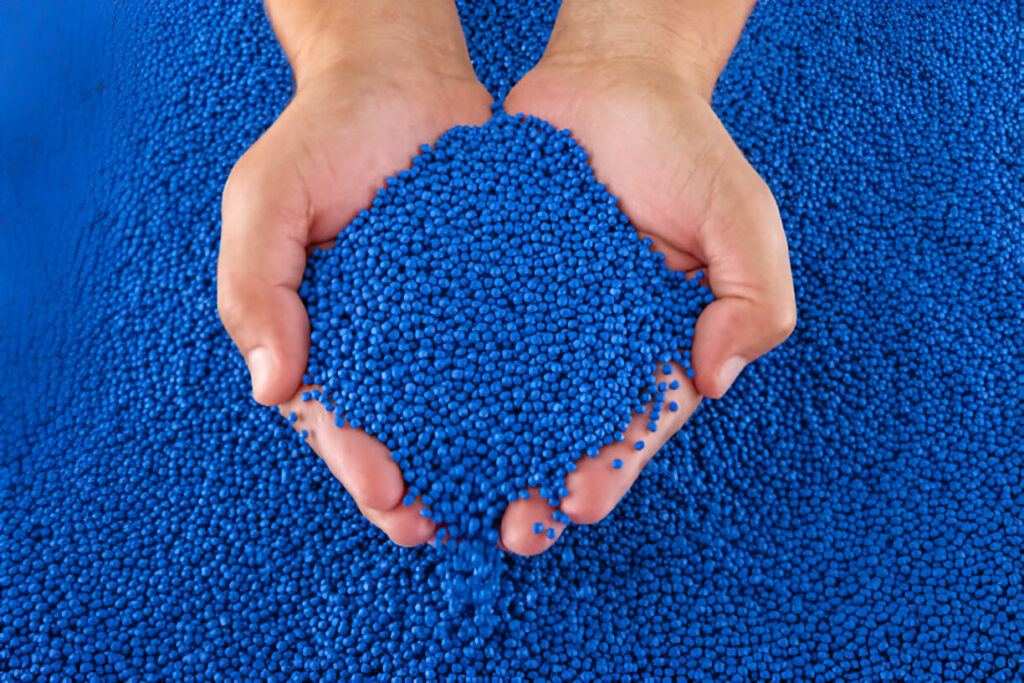
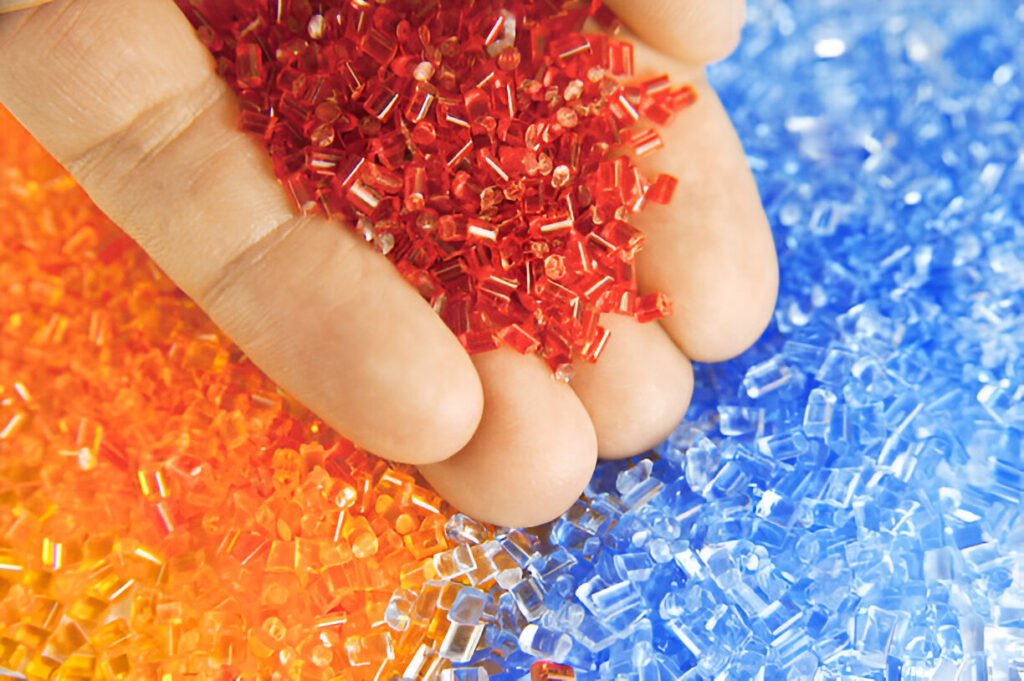
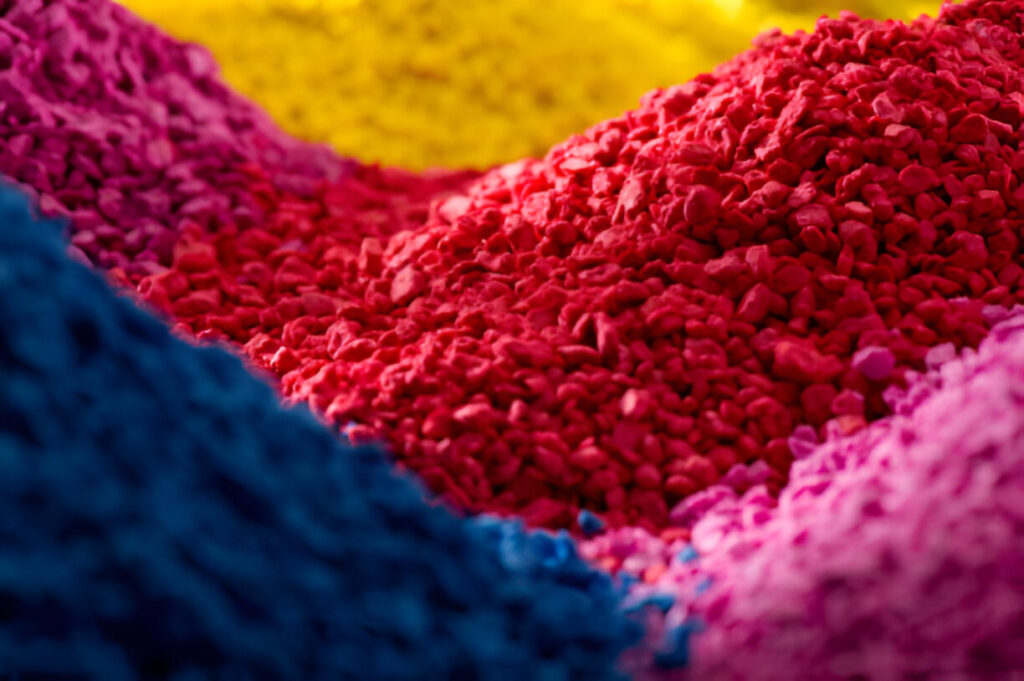
2. Common Plastic Injection Molding Materials
Searching the right material is difficult task as it affects the device’s performance, safety with Regulation. ABS stands for Acrylonitrile butadiene styrene. It is a typical thermoplastic type of plastic injection molding materials that’s in pipes, automotive body parts. Here are few name of materials are:
2.1 Polyethylene(PE)
Polyethylene was first synthesized by the German chemist Hans von Pechmann, who prepared it by accident in 1898 while investigating diazomethane.
Properties:
- It has the ability to various densities such as Low-Density Polyethylene – LDPE, High-Density Polyethylene – HDPE.
- It has excellent moisture resistance protection.
- It is flexible and has good impact resistance at low temperatures.
Applications:
- We mostly use them in packaging materials like bottles, containers, plastic bags etc.
- If we talk about domestic appliances, they are used like bin, bucket, storage containers etc.
- If we talk about industrial sector, we use it like on pipes, tubing and other appliances.
Advantages:
- When we look at it economically, it does much better, that is why it is now being sold in a wide range.
- It has some good properties like it has high ductility, and has very good impact resistance.
- And most important is its good chemical resistance.
Disadvantages:
- When we are talking about disadvantages, let us talk about the most important things. The first thing that we see is low tensile strength and stiffness.
- Susceptible to environmental stress cracking.
2.2 Polypropylene (PP)
Polypropylene is used in a range of industries including packaging, and consumer goods. Polypropylene’s advantages are its strength and low cost. It is Great electrical insulator.
Properties:
- Polypropylene is highly resistant to chemical, moisture and fatigue.
- Lightweight with excellent flexibility and toughness.
- Good heat resistance, typically used in applications with temperatures up to 100°C (212°F).
Applications:
- Polypropylene makes packaging products such as container, caps and plastic bags.
- It is used in automotive components such as battery cases, bumpers and interior parts.
- Also are made and implemented on small consumer products such as toys, furniture and household appliances.
Advantages:
- It is also much better economically and is easy to mold.
- This is a very good resistance which we should take and its effects are also very good.
- Electrical insulation properties are much better in this.
Disadvantages:
- Poor UV resistance.
- Limited ability to bond with adhesives or paints.
2.3 Polycarbonate (PC)
It is a group of thermoplastic polymers containing carbonate groups in their chemical structures. Polycarbonate is a durable material. Although it has high impact-resistance, it has low scratch-resistance.
Properties:
- This material has very high impact resistance and is optically clear.
- This is a very good resistance because it is very heat resistant and dimensional stability is also very good in it.
- And the most beautiful and best thing is that it also has transparency due to which it is much more excellent as an alternative to glass.
Applications:
- We use it to make maximum optical lenses including eyeglasses and also make camera lenses.
- This also happens in the medical sector in which we make syringes and containers.
- Automotive components are very easy to make because they are very lightweight. That’s why we use it in the automotive sector too.
Advantages:
- It has better impact resistance and strength.
- It has very high clarity and is ideal for transparent applications.
- And the most important and Advantages part is that we can easily mold it into complex shapes in comparison to others components.
Disadvantages:
- It is much more expensive in comparison to other thermoplastics.
- Susceptible to scratches and chemical attack.
2.4 Thermoplastic Elastomers (TPE)
It is few times referred as thermoplastic rubbers (TPR), are a class of copolymers or a physical mix of polymers that consist of materials with both thermoplastic and elastomeric properties. Flexible and durable, used in IV bags and catheter tubes.
Properties of Thermoplastic Elastomers:
- Elasticity and Flexibility
- Thermoplastic Behavior
- Chemical Resistance
- Excellent Compression Set
Advantages of Thermoplastic Elastomers (TPE):
- Recyclability and Reusability
- Ease of Processing
- Cost Efficiency
- Design Flexibility
Disadvantages of Thermoplastic Elastomers (TPE):
- Heat Sensitivity
- Lower Tensile Strength
- Chemical Vulnerability
Applications of Thermoplastic Elastomers (TPE):
- Automotive Industry :- Seals and Gaskets, Interior Components and Cable Insulation.
- Consumer Goods :- Sports Equipment, Household Products, Footwear etc.
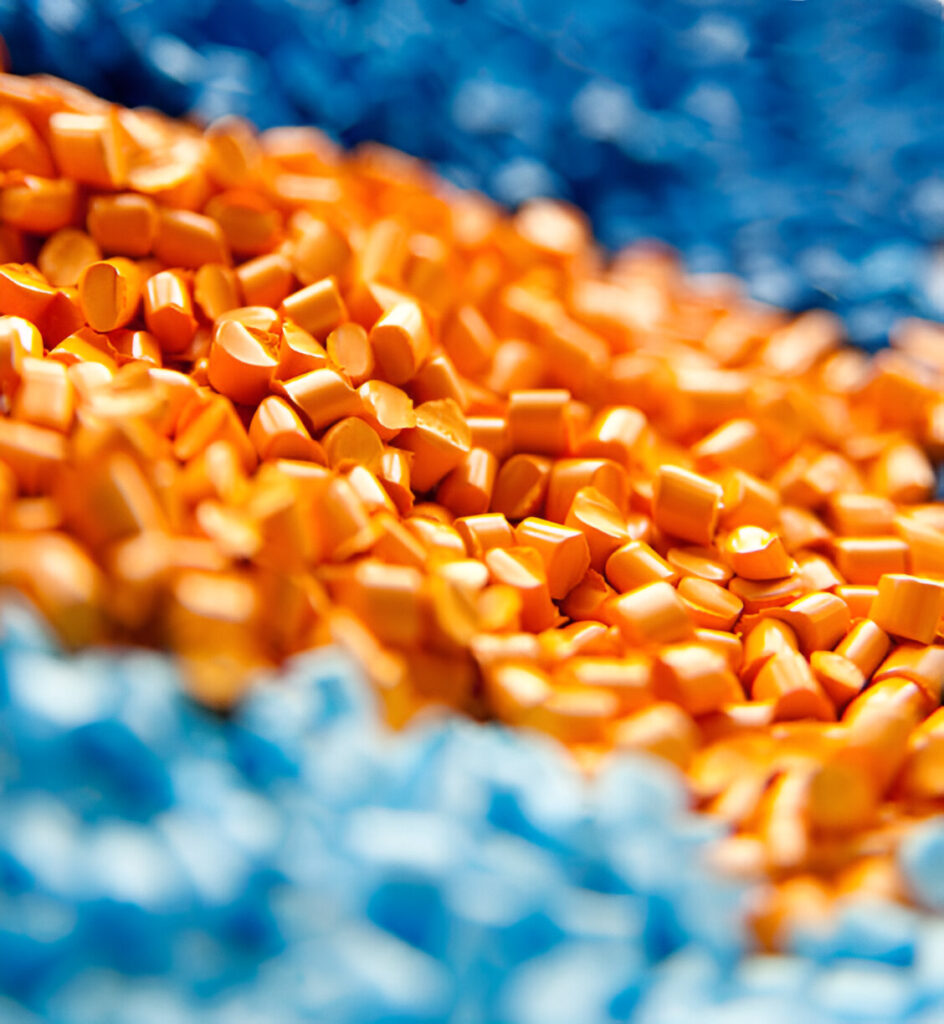
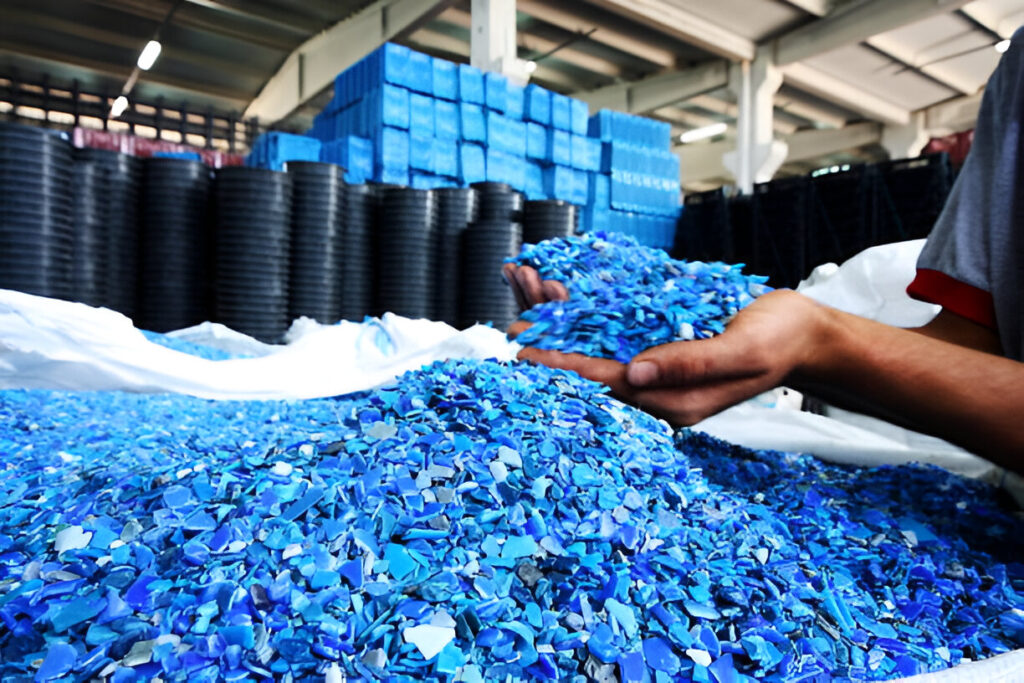
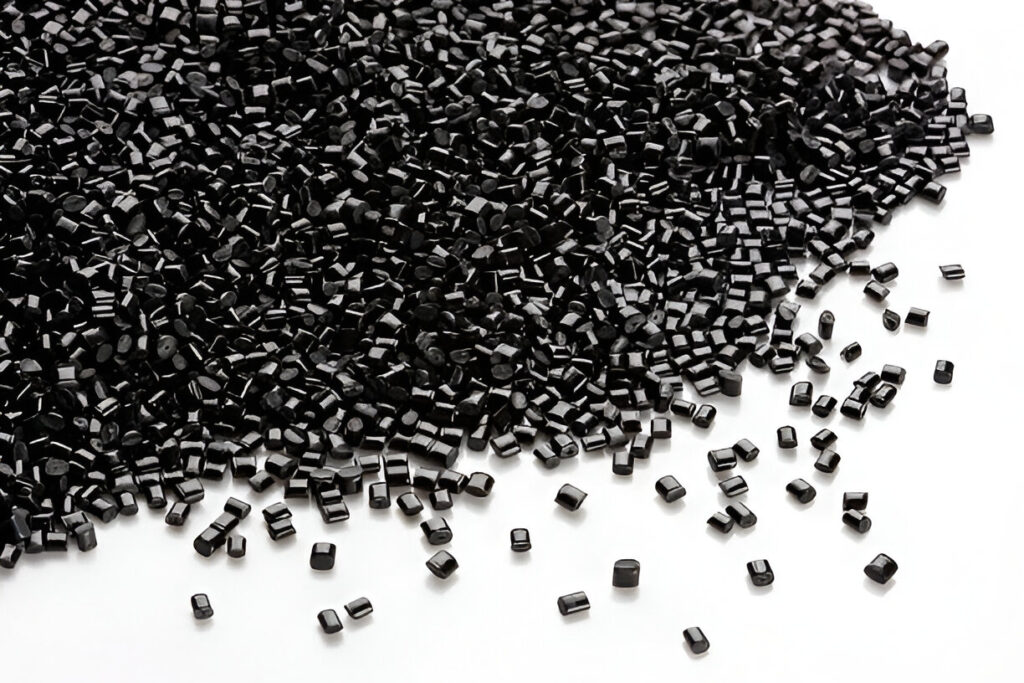
Conclusion
It becomes very important that we can select the material better because we know that plastic injection molding is an important process, which has a lot of requirements. Hence, because the quality and composition of the product and a final touch of the product, depends on its material.
In which we have given you complete details regarding some materials like polypropylene, polycarbonate and many more materials. And in this Article, i have told you in a much better way that which has high performance rate, what properties, disadvantages, advantages and applications it has, so with its help you can understand and you can select the material according to your needs.
So our hope is that you will make a better product and optimize the product, your work will be done in efficient manner and if there is any kind of issue then you can contact us, our company will give you all the information.
0 Comments
Trackbacks/Pingbacks