Steps to optimize Plastic injection molding for mass production is one of the most important and most efficient and versatile methods to produce high quality plastic products. Optimization for mass production is an essential role in this process which includes some things like consistency, cost effectiveness and quality.
In this article you will get a complete brief guide, with its help you will be able to take critical steps and achieve all the important points regarding your injection molding process will become clear. In this process, you will be told many points like design, automation and quality control.
1. Choosing the Right Material
The first step that we can take to optimize Plastic injection molding for mass production is to approach like good materials. This substance has properties such as it impacts significantly. It also has some properties such as quality, durability, functionality and finished product. Let us brief you with the help of some points :
- Evaluate Material Properties: Some materials are considered inside it such as thermal, mechanical and chemical properties. This material will have some properties like strength, flexibility, temperature resistance and requirement which will fulfill all the applications according to.
- Consider Cost and Availability: High volume production demands a study supply of materials. Evaluate the material cost, supplier reliability, and availability to ensure it aligns with your budget.
- Test Material Compatibility: Some materials become more challenging for molds or may cause premature wear on machine parts. We are testing the compatibility of materials which we will use in machines because they play an important role in its maintenance and repair.
2. Perfecting Mold Design
Its basic design is that it will play a critical role in its efficiency and quality which comes under the optimize Plastic injection molding for mass production. Inside this, well design molds are created which reduce cycle times, minimize waste and improve parts quality. Let us brief you everything with the help of some points:
- Optimize Gate Placement and Size: Proper gate design ensures consistent material flow and reduces defects like short shots and warping. Using simulation tools helps find the best gate size and location.
- Incorporate Cooling Channels: Efficient cooling is a crucial step in the injection molding process. A well-designed cooling channel ensures uniform heat distribution and faster cooling, which significantly boosts production speed and overall efficiency.
- Use High-Quality Mold Materials: High quality molds of plastic become essential for mass production. Consider hard and steels and durable materials that can withstand repeated cycles.
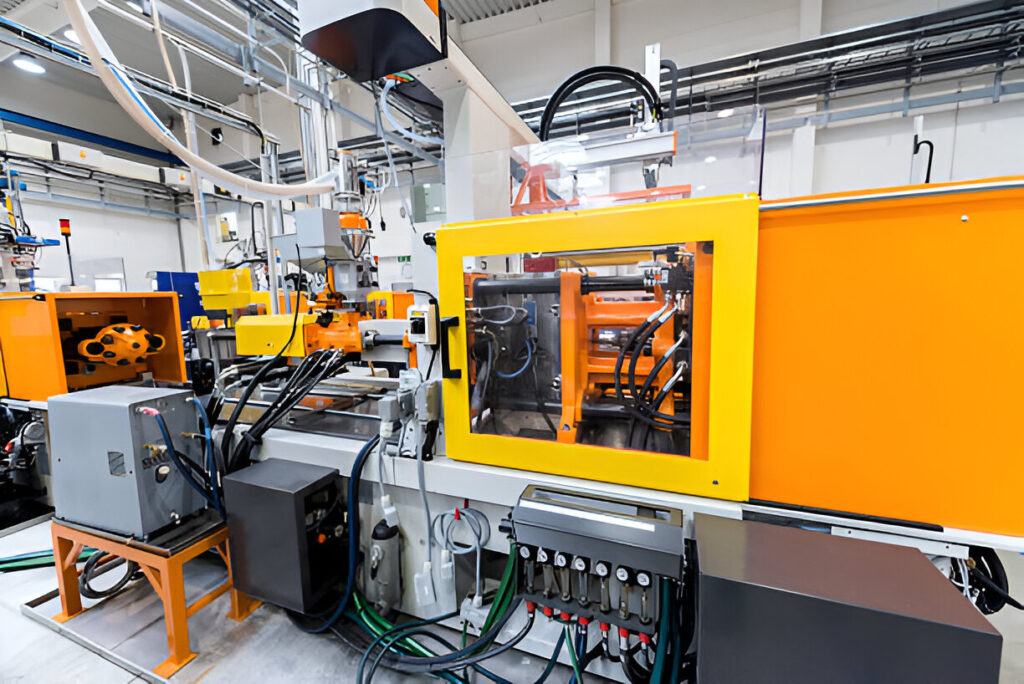
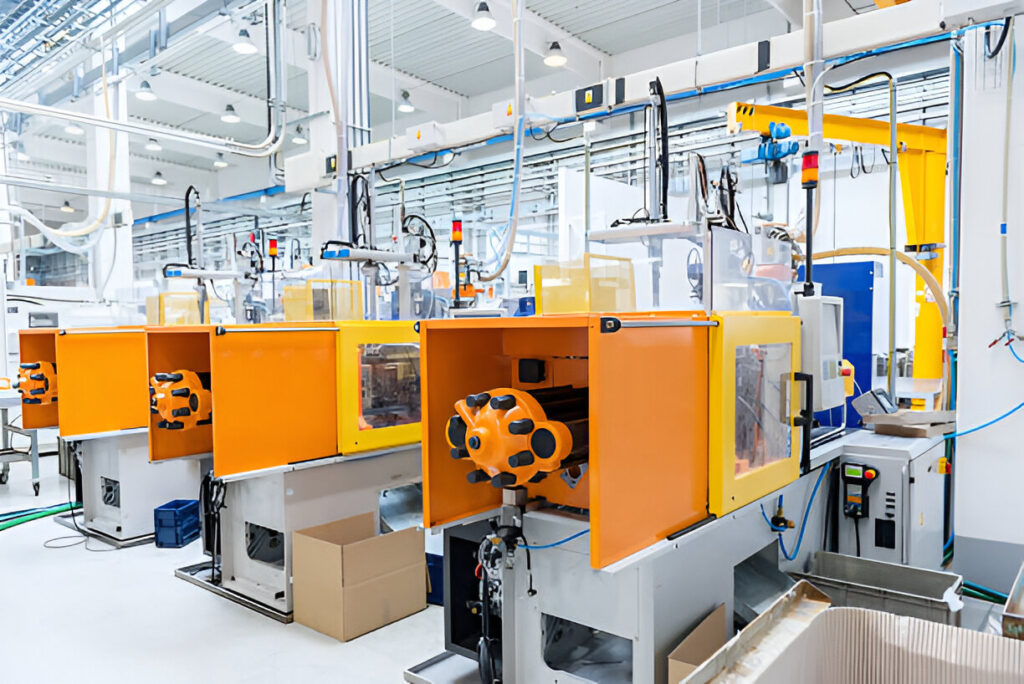
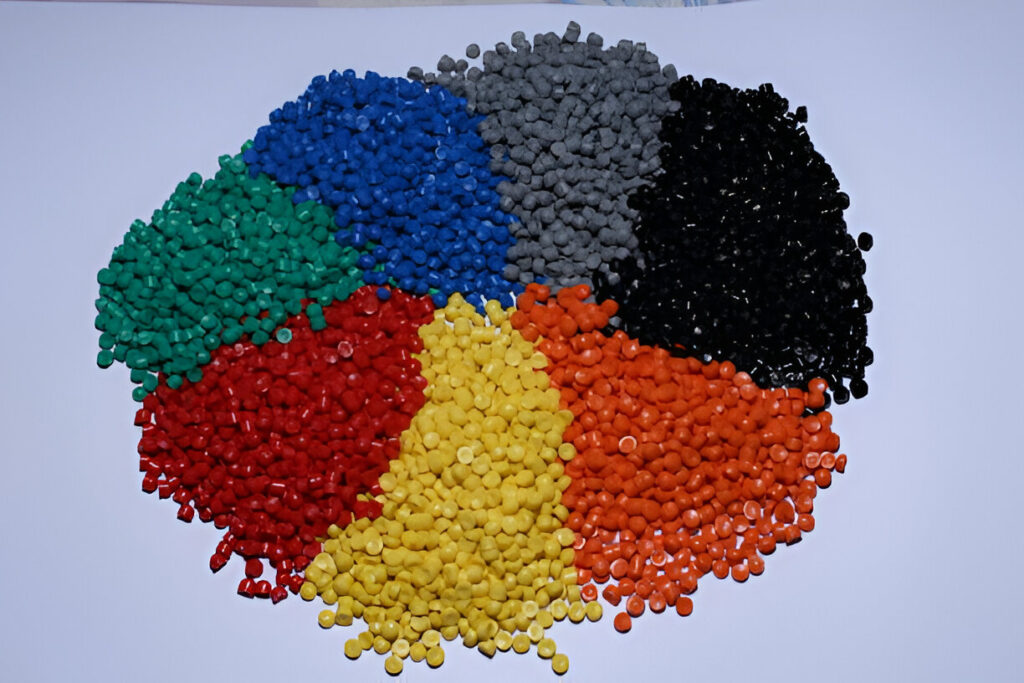
3. Implementing Process Control
Process control becomes a essential to ensure that all parts are of standard quality. You can maintain consistency by passing parameters within the process, reduce defects and optimize efficiency.
To brief everyone, we have explained them in 3 points:
- Set and Monitor Key Parameters: Key parameters include such as injection speed, pressure, temperature and cycle time. We will have to monitor these variables with the help of which we can maintain the consistency of qualities.
- Use Real-Time Monitoring Systems: Real-time monitoring tools collect data on a weekly basis and quickly adjust parameters drift out of range. This technology reduces the change in defects caused by parts in production.
- Automate Process Adjustments: Automated systems adjust parameters in real time to maintain optimal conditions. For example, if the sensor detects a temperature change, the system automatically adjusts the heater.
4. Optimizing Cycle Time
Minimizes cycle times without any comparison of quality which is a crucial role for optimize Plastic injection molding for mass production. Optimizing cycle times involves a number of tuning stages within injection molding processes. Let us brief you on these three stages:
- Reduce Cooling Time: Cooling time account can be up to 80% as long as this time slot is running. Efficient cooling like conformal channels and high-conductivity materials will greatly cut cooling time.
- Balance Injection and Packing Time: Set the appropriate injection and packing times to avoid part defects like sink marks or flash. Simulation software can help in finding the optimal balance.
- Use Fast-Acting Mold Opening and Ejection Mechanisms: Automated injection systems open molds quickly, reduce idle time, and increase production output.
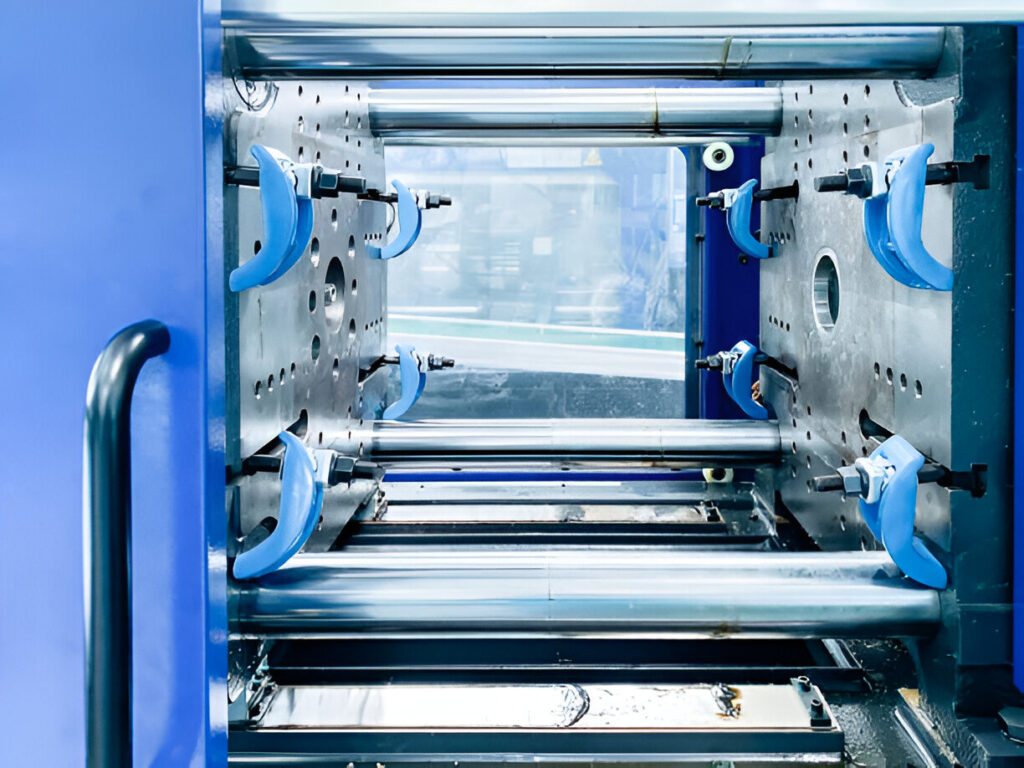
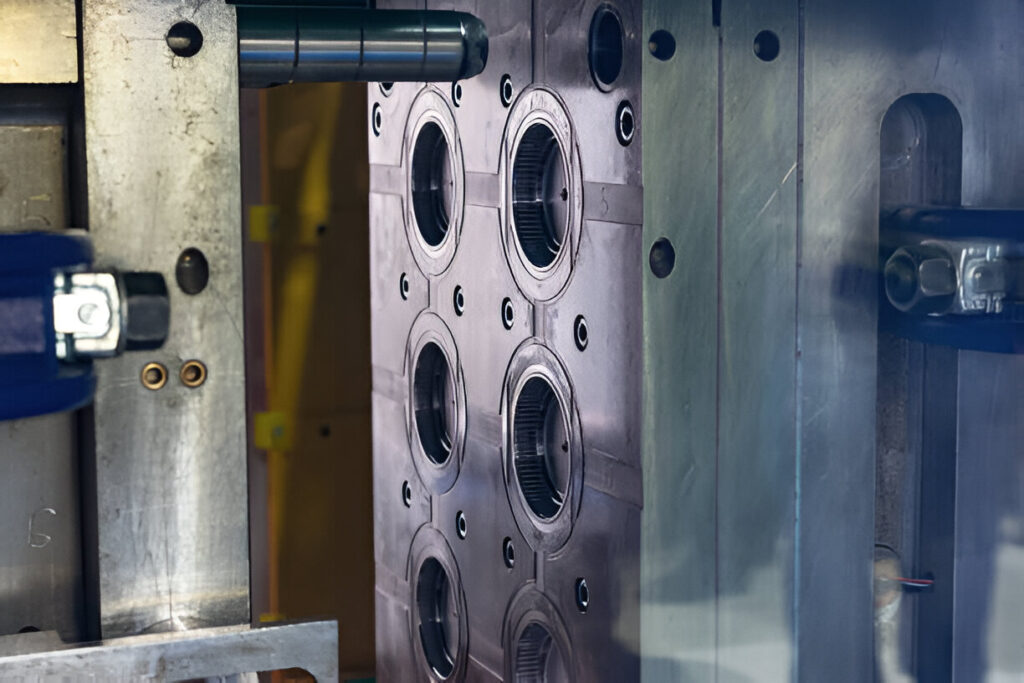
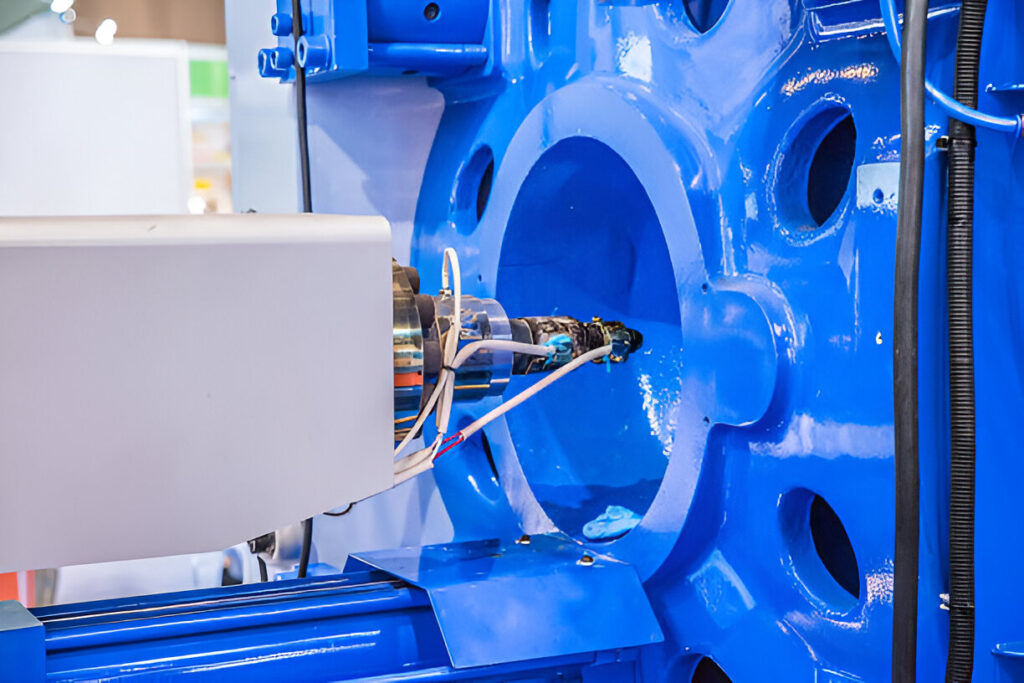
Conclusion
Optimizing plastic injection molding for mass production involves a multifaceted approach that includes careful material selection, mold design, process control, and quality management. Follow these steps to boost manufacturing, cut costs, ensure quality, and scale with automation and trained workforce support.
As you all know that this industry is evolving day by day, new technology and data driven practice is increasing, so we maintain their efficiency and sustainability in which plastic injection molding. To stay ahead of competitors, the company adopts these strategies to ensure consistent, high-quality output.
0 Comments