Plastic injection moulding machines are a key element in manufacturing most of the plastic products we use in everyday life. The majority of plastics products are made through injection moulding and many would not be possible without the use of it. In all, a plastic injection moulding machine can be used for engineering or commodity grade plastics production.
What is a Plastic Injection Moulding Machine?
A plastic injection moulding machine is used to produce plastic parts by injecting molten material into a mould. Material can be either thermoplastic or thermosetting.
Parts of an Injection Moulding Machine
- Injection Unit – Heats and injects the plastic into the mould.
- Clamping Unit – This is where the mould is held against the pressures during injection.
- Mould – This is the actual shape or form of the plastic that you’re making.
- Power System – Utilizes hydraulic or electric power for accuracy and precision during operation.
- Cooling System – A system to cool down the plastic to make it solid and rigid after being injected into the mold cavity so as to shape up the desired object.
Types of Injection Moulding Machines
1. Hydraulic Injection Moulding Machines
Hydraulic injection moulding machines are one of the oldest and most widely used types of moulding machines. They operate using high-pressure hydraulic systems, which power the clamping and injection processes. These machines are known for their strong clamping force, durability, and ability to handle large-scale production.
2. Electric Injection Moulding Machines
Injecting molding machines use a processing method in mass production of plastic parts with complex shapes. The advantages of the injection molding machines are fast production speed, high efficiency, automatic operation, variety of colors, shapes from simple to complex, the size can be from large to small, and the size of the injected part is accurate, the product is thick and not thin-walled and it’s easy to insert in various details.
3. Hybrid Injection Moulding Machines
Mixing hydraulic and electric technology, hybrid machines deliver speed, accuracy and up to 40% less energy consumption.
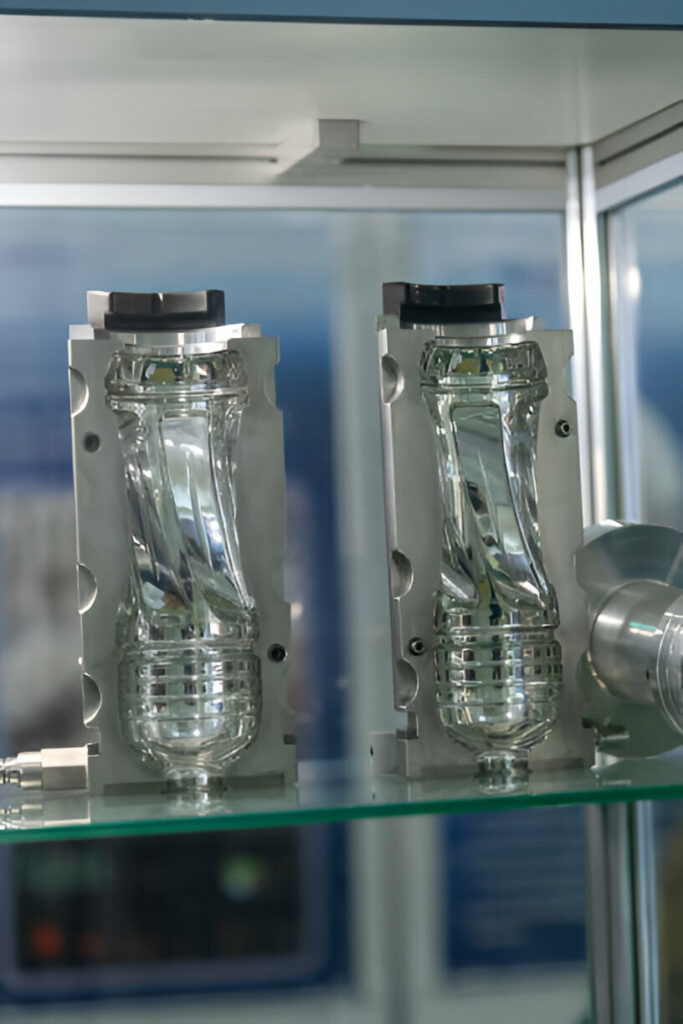
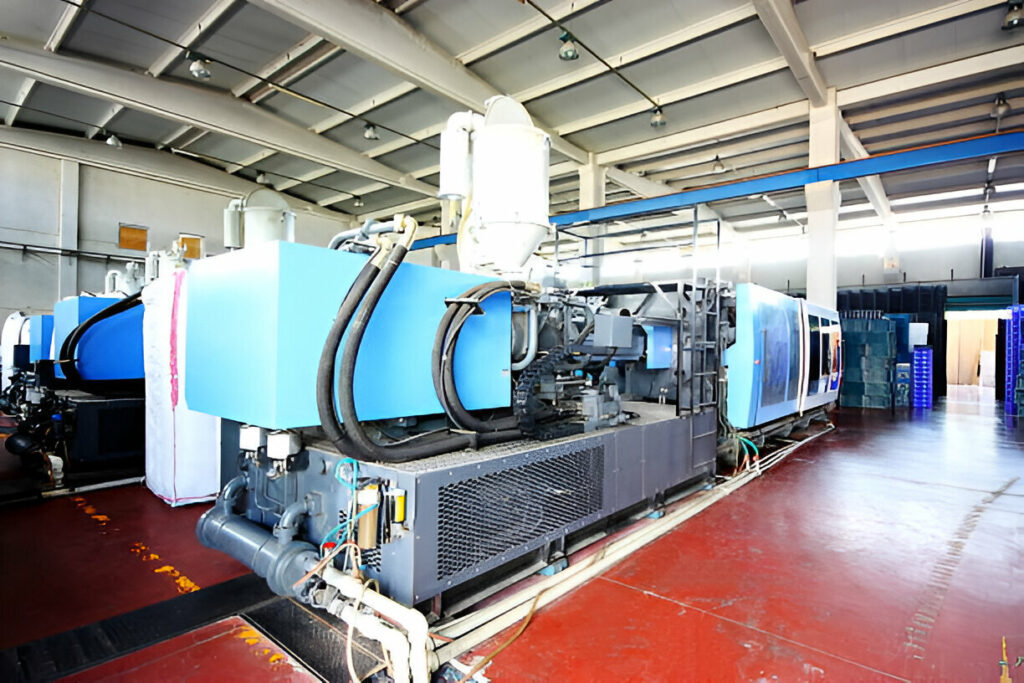
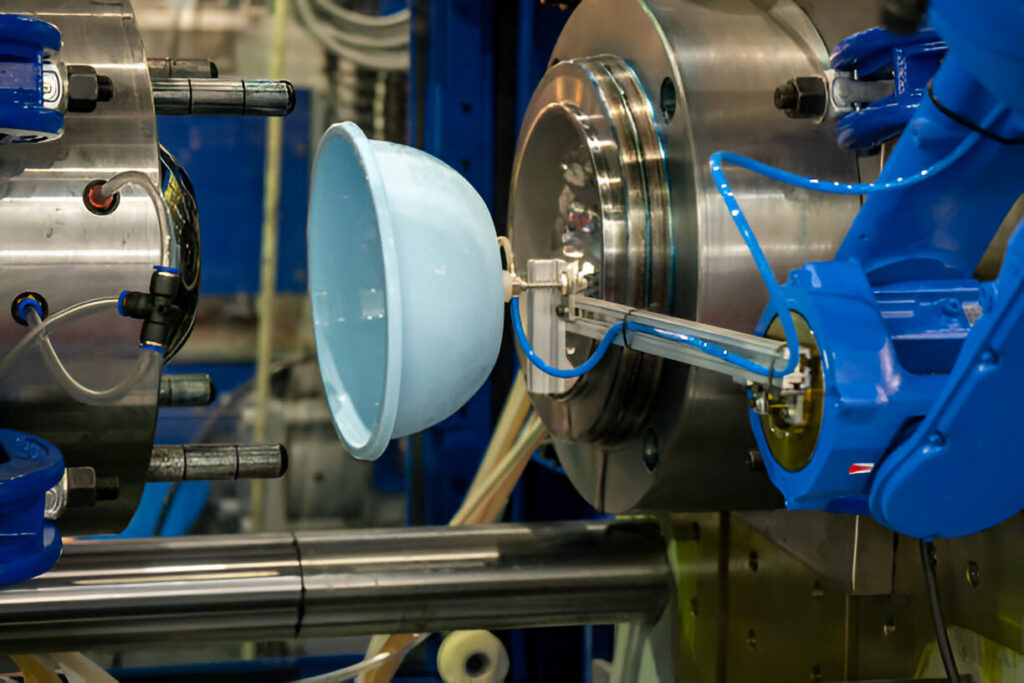
How to choose a right manufacturer?
To achieve the high-quality production required for your business, you must firstly choose an appropriate plastic injection moulding machine manufacturer. The following are details that should be considered when choosing a right manufacturer.
1. Reputation & Experience
A manufacturer’s reputation is built on years of consistent performance, innovation, and customer satisfaction. A company with extensive industry experience understands the challenges of plastic manufacturing and continuously improves its technology to meet modern demands. Look for manufacturers with positive reviews, long-standing industry presence, and a portfolio of successful installations worldwide.
2. Quality & Precision
The best plastic injection moulding machine manufacturers prioritize high-quality materials, advanced engineering, and strict quality control standards. A well-built machine ensures longevity, minimal downtime, and superior output quality. Precision is critical in industries like automotive and medical manufacturing, where even the smallest error can impact the final product.
3. Customization & Support
Every manufacturing setup has unique needs, and a good manufacturer should provide customized solutions tailored to your specific production requirements. This includes modifications in machine size, clamping force, automation levels, and software integration.
4. Energy Efficiency
Energy consumption is a significant factor in manufacturing costs, and energy-efficient injection moulding machines can drastically reduce electricity bills while minimizing environmental impact. Electric and hybrid machines are designed to use power more efficiently, offering savings of up to 50% compared to traditional hydraulic systems.
Benefits of Advanced Injection Moulding Machines
Plastic Injection molding machine is an industrial machine that produces various plastic products by injecting molten material into molds. Injection molding machines have different types of injection machines which vary according to the clamping pressure, weight and size of the product.
Here Is Why You Should Consider Using Advanced Injection Molding Machines:
1. High Efficiency
Modern plastic injection moulding machines can produce a higher output while at the same time saving on costs and increasing overall output.
2. Cost Savings
Automation reduces labor costs as there is no need for manual labor in repetitive work. It also cuts down material cost and wastage.
3. Precision & Consistency
Advanced injection moulding machines offer uniform quality along with complicated designing thus best for complex parts.
4. Versatility
These machines can handle different materials, including thermoplastics, thermosetting plastics, and elastomers.
5. Eco-Friendly Production
Machines which are energy efficient can help reducing environmental impact and to promote sustainable manufacturing.
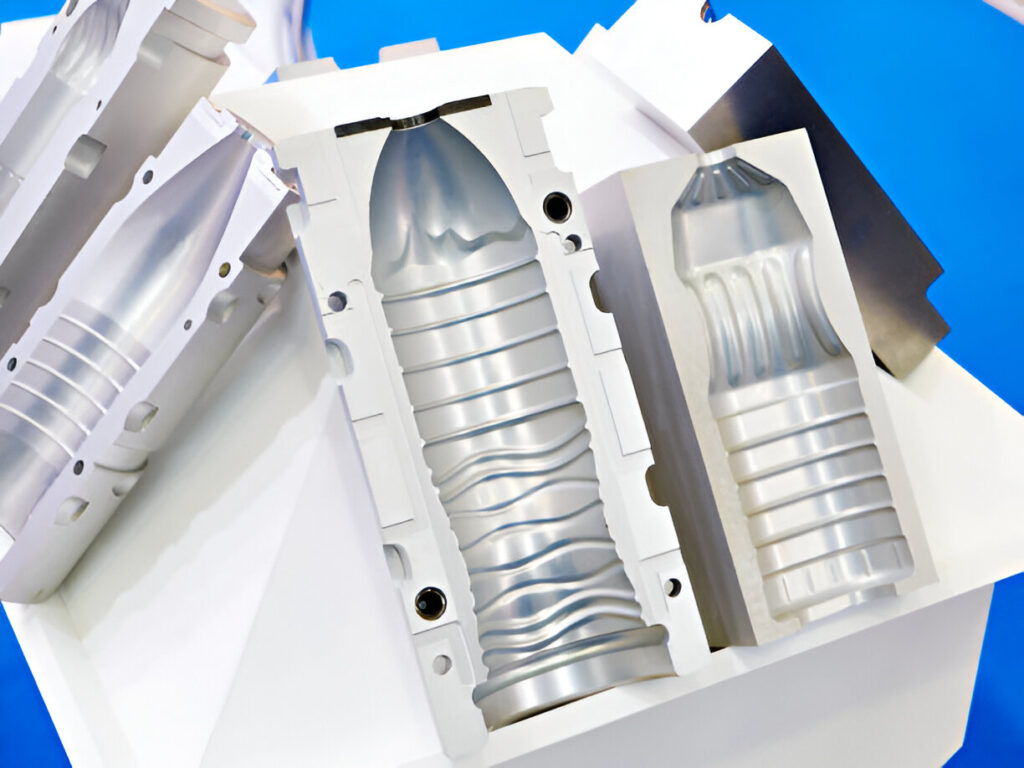
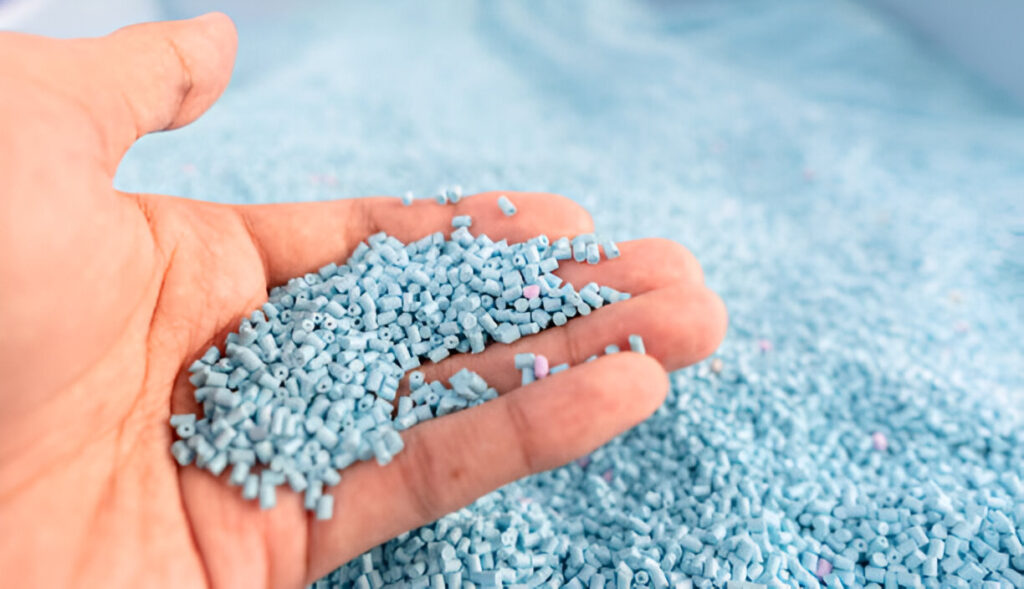
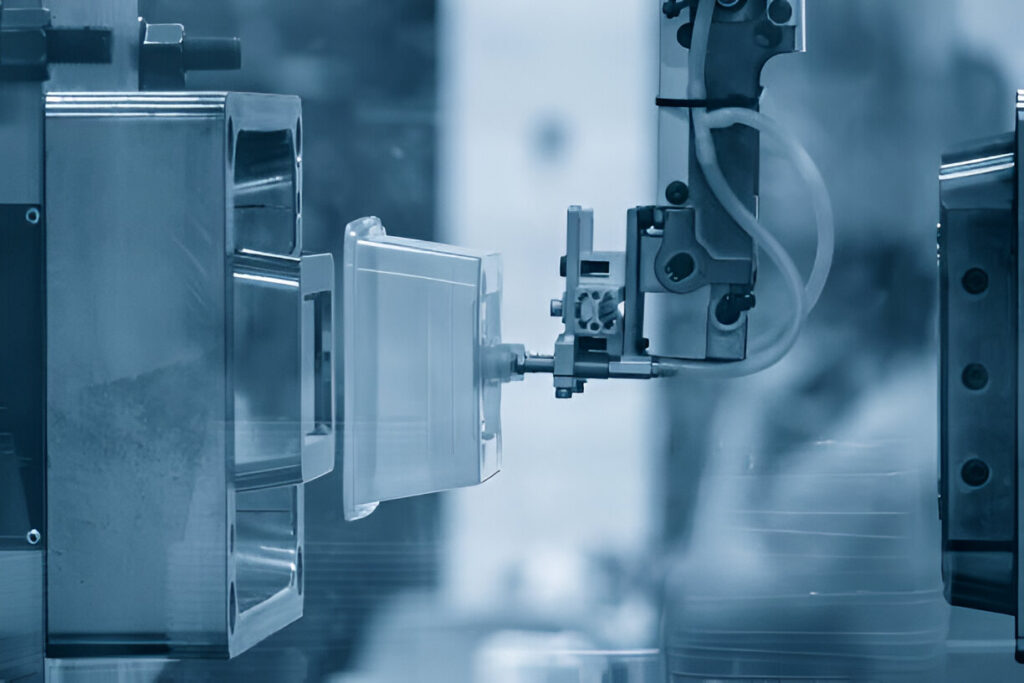
Future Trends in Plastic Injection Moulding Machines
Plastic injection moulding manufacturers is a vital process for manufacturing everything from automotive to medical to packaging to consumer goods. Just as technology is rapidly advancing, the plastic injection moulding industry is also evolving to meet new requirements for efficiency, sustainability and precision.
1. Smart manufacturing and Industry 4.0
Manufacturers are embracing artificial intelligence (AI), internet of things (IoT) and automation for better operational efficiency and real-time monitoring.
2. Sustainable & Recycled Materials
The requirement for biodegradable plastics and recycled materials is increasing resulting in machines being made with environmentally-friendly production in mind.
3. Micro Injection Moulding
In medical and electronics industry, smaller but high-precision plastic injection moulding machines are increasing their market shares.
4. Advanced Cooling & Energy-Saving Technologies
New cooling system innovation and energy-saving motor technology reduce operating costs and improve machine performance.
Conclusion
Choosing the right manufacturer is important for ensuring quality, efficiency and sustainability in production. Moreover, with continuous technological advancements, manufacturers are updating their machines to fulfil industry demands. Be it hydraulic, electric or hybrid machine choosing the right manufacturer will ensure long term success in plastic manufacturing.
Reputation, technology and after-sales service are three major factors to consider if you’re looking for a high-quality plastic injection moulding machine. A correct investment can help elevate production efficiency as well as profitability.
0 Comments