Medical injection molding is a manufacturing process that creates plastic medical devices and components. It involves melting plastic then injecting it into the mold and get a hard material elements from the mold. It includes the complete process in which the size, shape, quality and strength of the product.
In this the process of making any product is approved by FDA that are both durable and reliable. Some prototypes are sent to FDS for approval. Plastic is a good option because of its tensile strength. It’s also not likely to develop bacteria.
We are making medical equipment because health is important to us. That’s why efforts are made to create components with a single strength.
What is the Role of Plastic Injection Molding in Medical Devices?
It is a process that is ideal for making medical devices and their creation with high sustainability and consistency. Few Points are:
- Design :- It enable the creation of complex designs and accommodate the flexibility required to meet unique specifications during manufacturing.
- Scalability :- In this you can increase your production quantities, important for meeting the high demand product.
- Material versatility :- The plastic injection molding process supports a broad material selection, including materials with considerable heat resistance and durability.
- Cost-Effectiveness :- Medical plastic injection molding offers cost advantages due to its high production volumes, material efficiency etc. Creating mold can be expensive but the cost per unit is low.
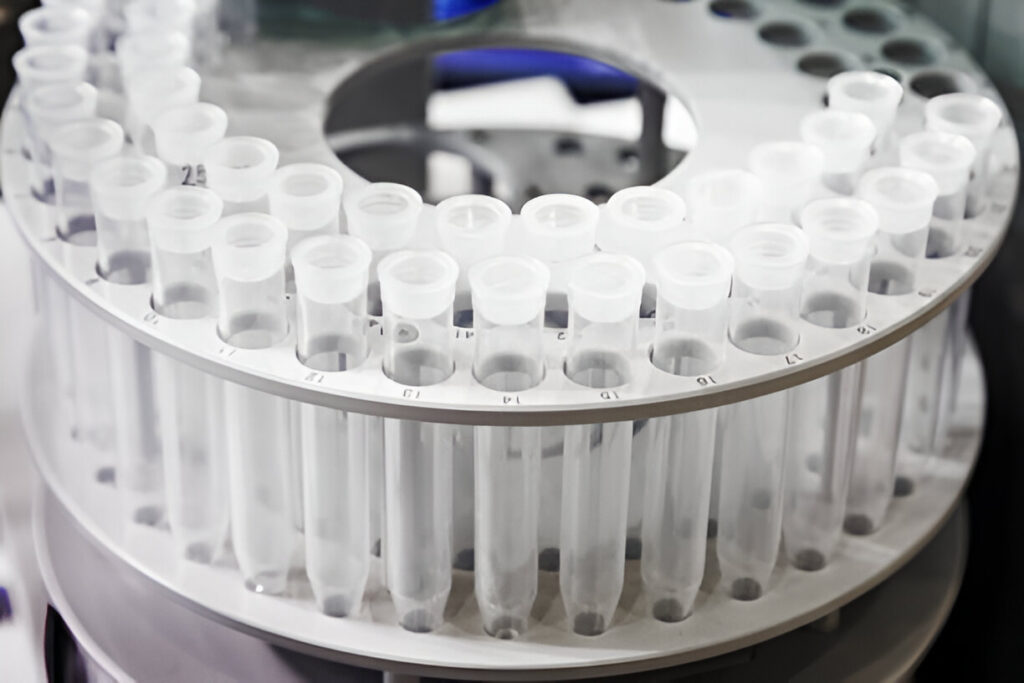

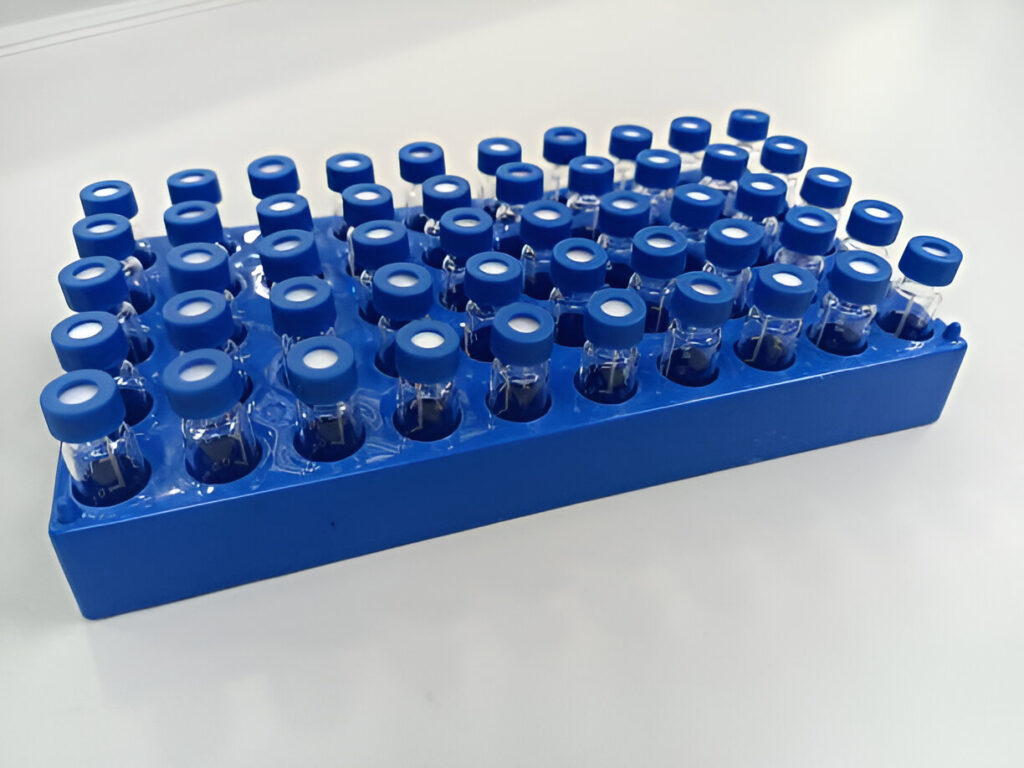
Materials Used
Searching the right material is difficult task as it affects the device’s performance, safety with Regulation. “ABS stands for Acrylonitrile butadiene styrene”. It is a typical thermoplastic type of injection molding materials that’s in pipes, automotive body parts. Here are few name of materials are:
1. Polyethylene(PE) used in Plastic injection molding for medical devices
Polyethylene was first synthesized by the German chemist Hans von Pechmann, who prepared it by accident in 1898 while investigating diazomethane.
2. Polypropylene (PP)
Polypropylene is used in a range of industries including packaging, and consumer goods. Polypropylene’s advantages are its strength and low cost. It is Great electrical insulator.
3. Polycarbonate (PC)
It is a group of thermoplastic polymers containing carbonate groups in their chemical structures. Polycarbonate is a durable material. Although it has high impact-resistance, it has low scratch-resistance.
4. Thermoplastic Elastomers (TPE)
It is few times referred as thermoplastic rubbers (TPR), are a class of copolymers or a physical mix of polymers that consist of materials with both thermoplastic and elastomeric properties. Flexible and durable, used in bags and catheter tubes.
Process of Plastic Injection Molding for Medical Devices
As I have already said about the process in above but I would like to Explain it in brief: plastic is melted in the molding machine and then injected into a mold under high pressure. Then, the material is cooled, solidified and afterwards released by opening the two halves of the mold.
Here are 4 points to express about Process of Plastic Injection Molding :
- Material Selection :- Correct plastic is selected as per the device needs. There are several important properties to consider for selecting injection molding materials for any plastic product. These include the desired tensile strength, flexural modulus (bending stiffness), Izod impact (toughness), electrical insulation, temperature resistance, chemical resistance, FDA compliance, and cost of the final product.
- Mold Design and Manufacturing :- Mold is created usually from steel or aluminum. We ensure that you will receive the final product as per your specifications.
- Injection Molding Process :- Whichever plastic is chosen, we will first melt it, then inject it, cool it inside the mold and extract the solid part.
- Packaging and Distribution :- The devices will be packaged according to regulatory guidelines and distributed to health care facilities.
What are the Challenges in Plastic Injection Molding ?
There are several challenges in plastic injection molding that affect efficiency and quality. Deciding what will be the right material according to the device is important. So we have to be very careful for deciding the material.
There should be some component inside the plastic like durable, safe for medical use and sustainability. Designing the original is a different precision challenge because defeat causes problems like the final pro product. Here are few points that are the challenges in plastic injection molding are :
- Foreign body contamination
- Rising raw material prices
- Air currents/draughts
- Electrostatic forces
- Temperature changes
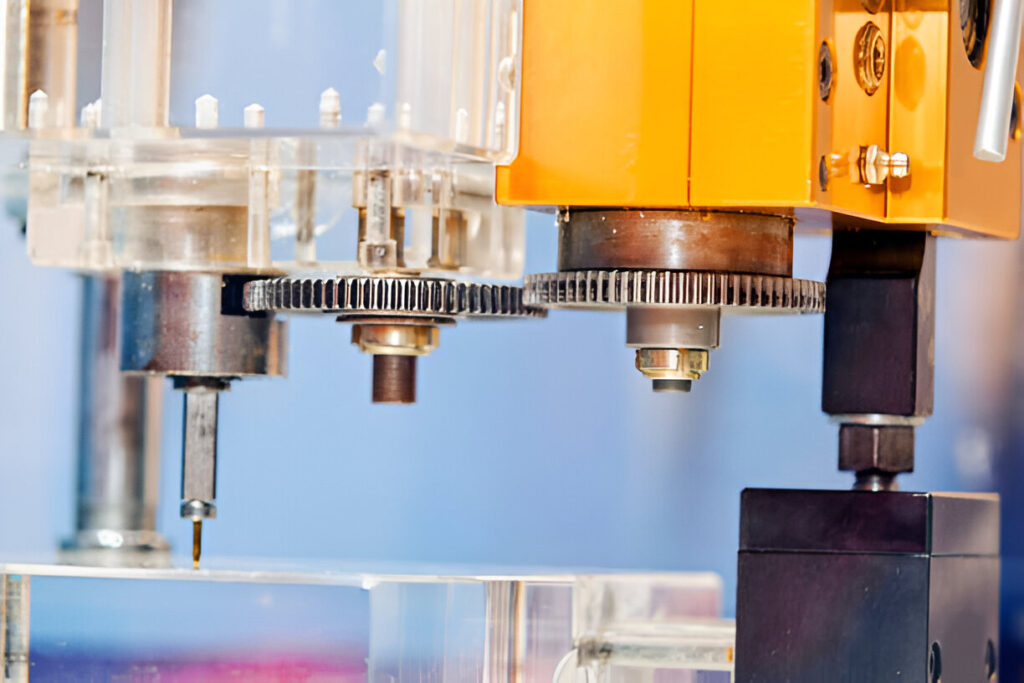
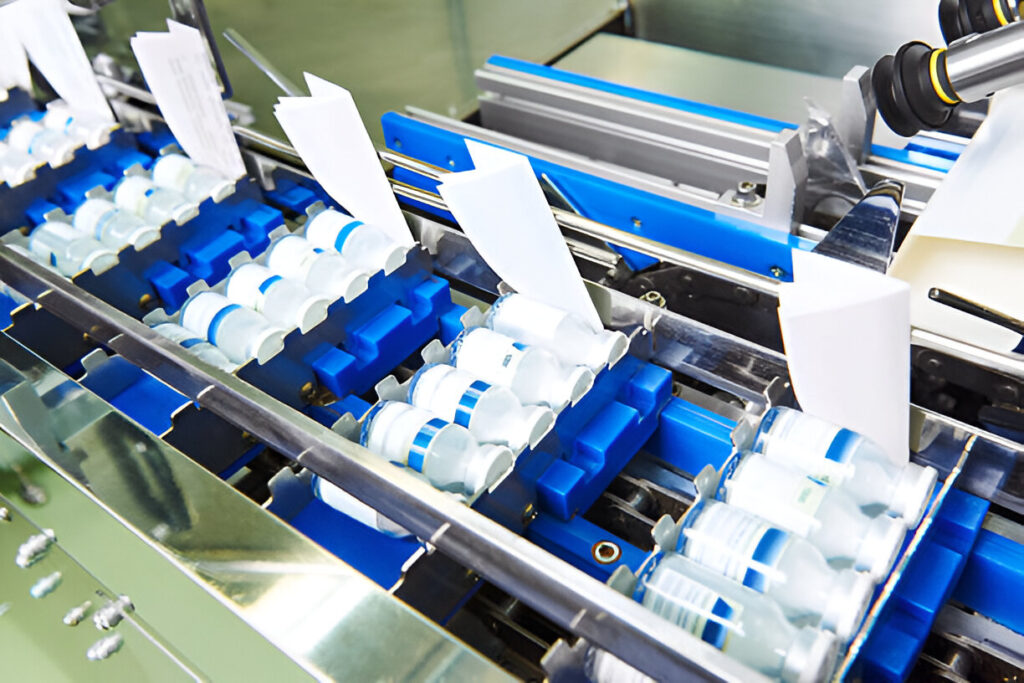
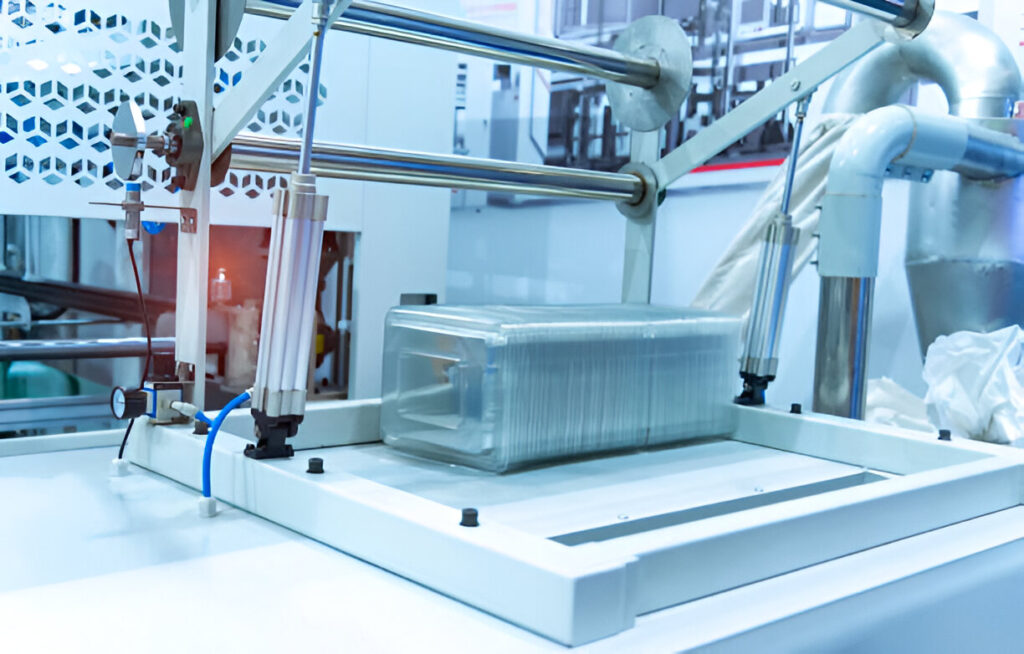
Scope of Injection Molding for Medical Devices
Country has a vast scope of growth within the injection molding industry, primarily due to the current market size and future projections. The market size has grown considerably in recent years and is projected to reach $13.3 Billion by 2025 at a CAGR of 5.7%.
The injection molding market in India has significant potential for growth in key sectors such as automotive, packaging, healthcare, and construction. With India’s population of over 1.3 billion, domestic consumption is on the rise, and manufacturing sectors must ramp up production to meet demand. Here are two points for this:
Industrial Applications
Injection molding technology is widely used in various industries such as automotive, packaging, health care, and construction. Injection molding products have some qualities like consistency, reliability, durability, efficiency.
When talking about the automotive sector, injection molding technology is used to manufacture critical parts of engine components. In this way, many equipment in construction are also made with the help of injection molding. We all know that plastic is very reliable, durable and it can easily maintain. Also, plastic is a very cost effective material when it compare to the other elements.
Export Opportunities
I have said it about the plastic being a cost effective material, So many industries prefer to make their products using plastic materials only. That is why the use of plastic is increasing day by day. So a lot of industries have been set up in different places globally.
Because everyone’s needs can be fulfilled. The industry is booming and manufacturing is also happening with the support of one country and other countries and increment is happening day by day and experts are doing well.
Conclusion
Plastic injection molding is a great way to create high quality products for medical equipment. Which will include many things like pacemaker in heart surgery and many more. But challenges are coming but work and innovation is happening very well, materials are being used and such substances are being used which are sustainable, efficient and cost effective.
We will try our best to provide you with a mode in the cheapest way so that your business can grow. And complete brief knowledge will be given about plastic injection molding, in which methods the process is done.
And our motivation is that the way technology is progressing day by day, our contribution in the health care department will always remain the same and we will try to develop new equipment’s.
0 Comments
Trackbacks/Pingbacks