Life cycle of a mold is a critical tool in the manufacturing industry for the production of particular plastics that precise and form complex plastic components, which may range from automotive and electronics to medical devices or consumer products. However, it is important to understand that the life cycle of an injection mold is essential in manufacturing as it helps to optimize performance and ensure cost effectiveness and maintain product quality.
In this article, you will read and explore the life cycle of an injection molding, which will be described in all the details and points and all the factors will be explained in a way that you can understand every point.
The Concept of the Injection Mold Life Cycle
The life cycle of an injection mold refers to the various stages that go through a mold, from design to manufacturing to retirement and replacement. This life cycle is influenced by various factors, including the quality of materials used, maintenance practices, and the operational environment, which are monitored and managed. Each stage is manufactured to maximize its utility.
Stages of the Life cycle of a mold
1. Design Phase
This journey starts with the injection model. The design is deeply rooted in physics to understand how the molds work efficiently, have durability and long term performance. Designers use the CAD (Computer-Aided Design) software to create all the details that go into the blueprint. The models consider several factors such as:-
- Product specifications
- Material type (e.g., thermoplastics, thermosetting plastics)
- Shrinkage rates
- Ejection mechanisms
- Cooling channels
The mold wall design minimizes the risk of defects and assures long term operational life.
2. Manufacturing Phase
Once you finalize the design, the manufacturing process begins. Manufacturers typically use high-quality tools such as steel and aluminum. They produce these products using advanced machine techniques like CNC (Computer Numerical Control) milling and EDM (Electrical Discharge Machining). Employed achieve precise tolerances in surface finishes.
This quality material allows craftsmanship to face significant impacts. Improves the durability and performance of molds. Better materials are used to expand with skilled craftsmanship and extend the life cycle of the mold.
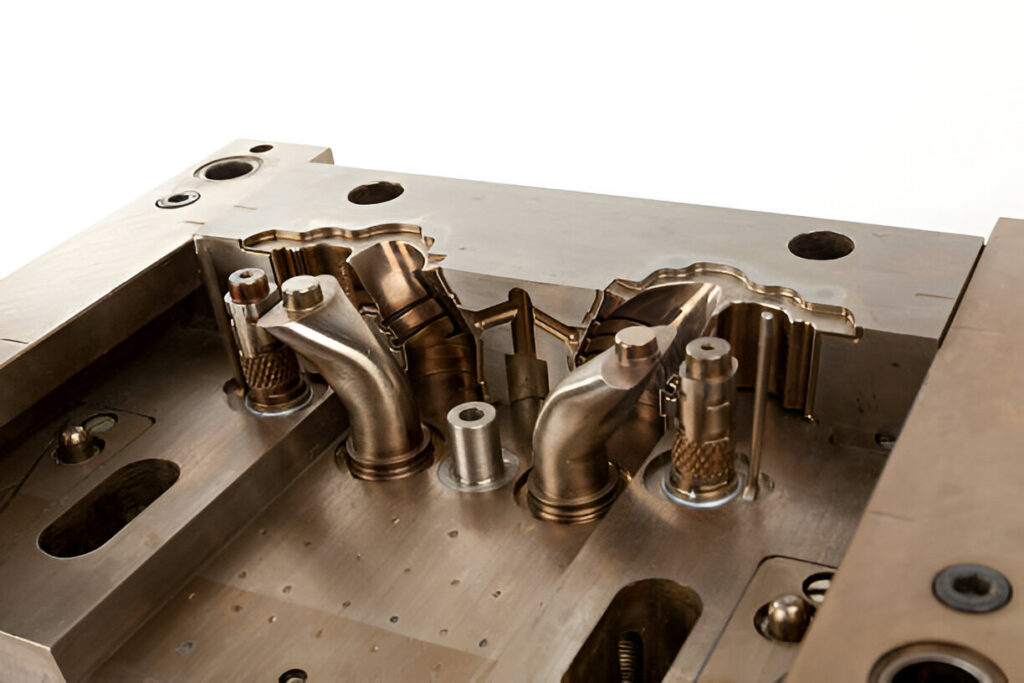
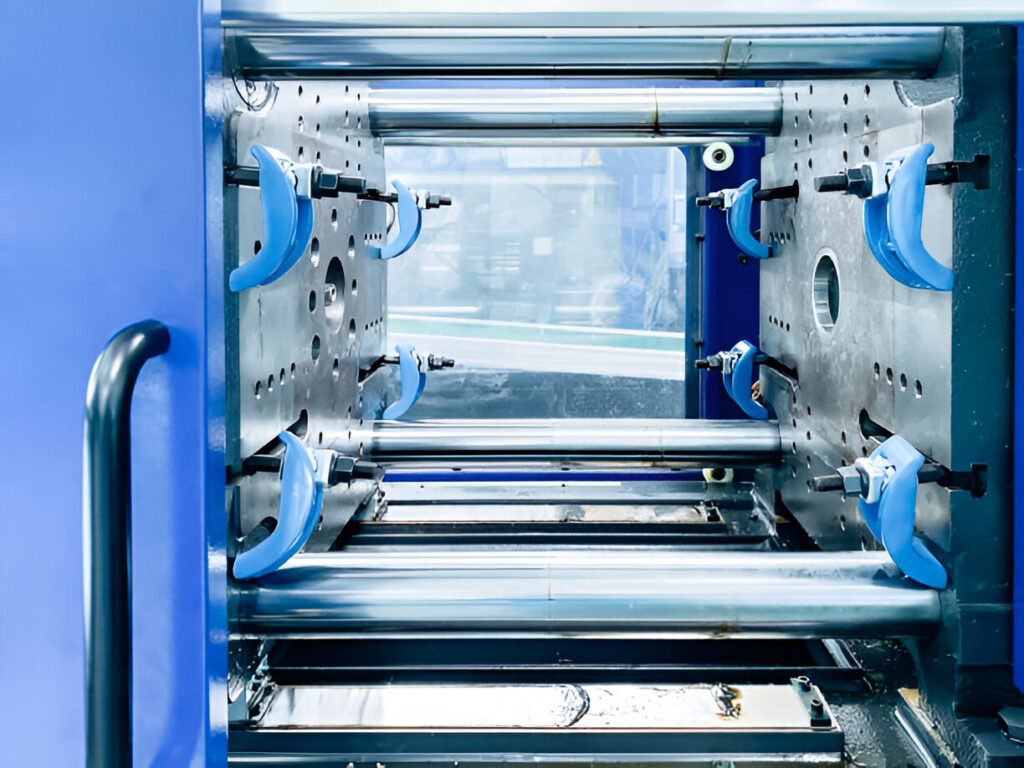

3. Testing and Validation
The model is sent to full production first. It undergoes rigorous testing and validation. This phase assures that the manufacturers producing the parts will comply with design specifications and that the tests include certain features such as:–
- Dimensional accuracy testing
- Cycle time optimization
- Material flow analysis
If you identify any defect during testing, correct it and ensure you reduce the material properly after completing production. This stage is very clear and costly. Costly issues occur during the production phase.
4. Production Phase
This production phase is the longest and most critical stage. During this phase the mold is used for the entire life cycle of the mold. This mold is used to manufacture large quantities of plastic products. Many processes are required to ensure the safety of many operations such as:–
- Operating conditions (e.g., temperature, pressure)
- Material properties
- Injection molding machine settings
You must regularly monitor all these parts to ensure they work properly, correctly, and consistently to prevent any kind of damage.
5. Maintenance and Repairs(Life cycle of a mold)
Routing maintenance is quite tedious and is extended. The life cycle of the injection mold includes maintenance activities. Some points such as:–
- Cleaning the mold to remove residue and debris
- Inspecting for signs of wear, corrosion, or damage
- Lubricating moving parts
- Replacing worn components (e.g., ejector pins, seals)
Through implementing proactive maintenance, minor repairs are also necessary for manufacturers to prevent unexpected breakdowns and reduce down time. Issues to address include surface scratches and damaged components.
6. Retirement or Replacement
All injection molds eventually reach the end of their useful life. Some molds, which may tell you when they may be due for retirement or replacement, which includes such as:–
- Frequent defects in produced parts
- Excessive maintenance costs
- Significant wear or damage that affects performance
When the device reaches these statuses, the manufacturer must consider whether to repair or replace it because of the significant cost-benefit analysis.
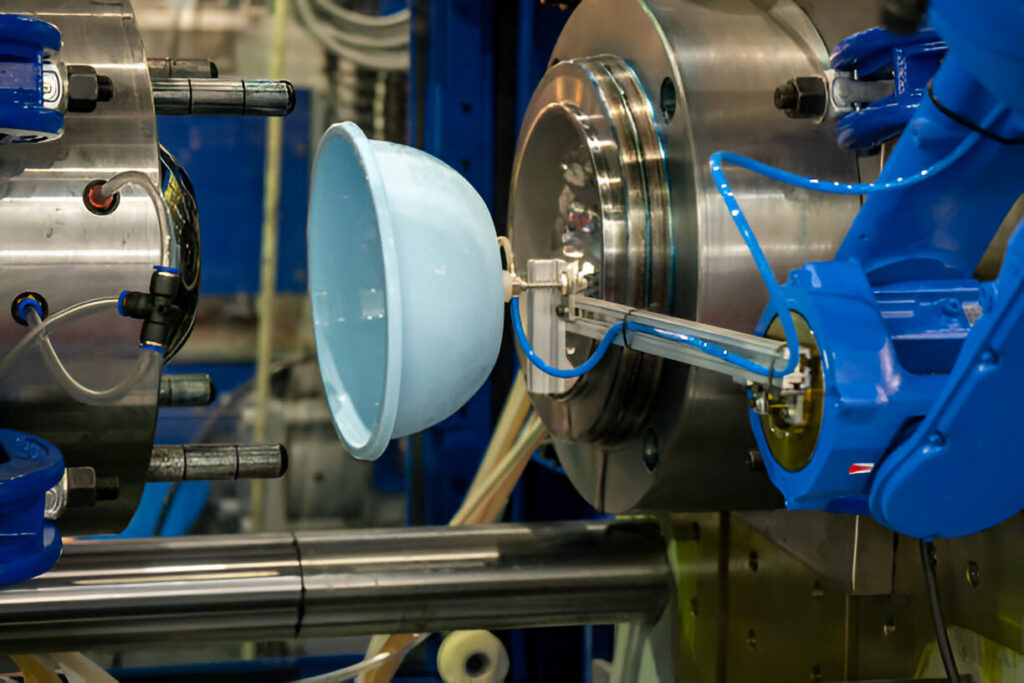
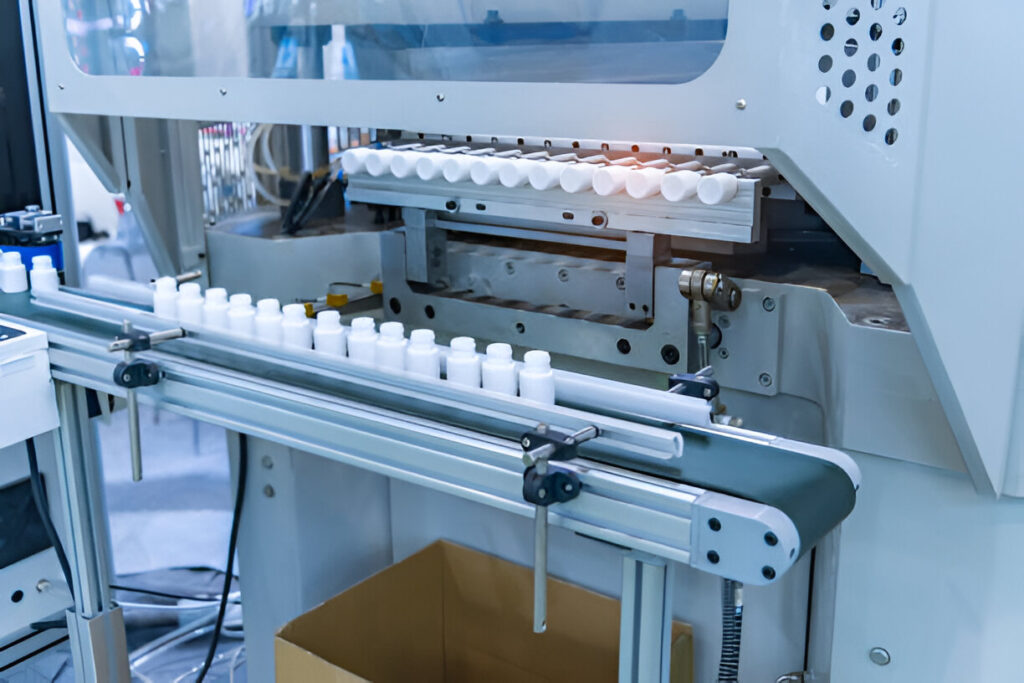
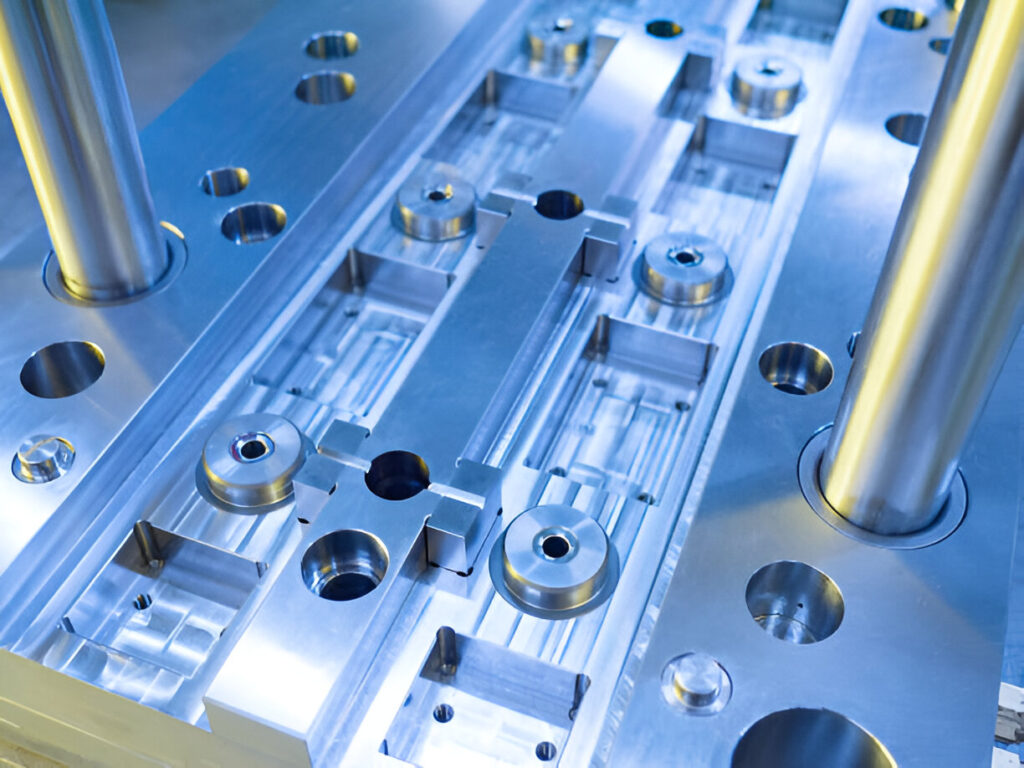
Factors Influencing the Life Cycle of an Injection Mold
There are several factors whose determination can determine the life cycle of an injection mold. By understanding and controlling these factors, we can understand that manufacturing can be maximized. More efficiency for long cavities!
1. Material Quality
This is the quality of a material that is being processed and plays a role in mold construction. A lot of pressure rules in their durability. The high grade tool steels includes such as P20, H13, stainless steel and offers an excellent resistance to corrosion and high temperatures and extends the modern lifestyle.
2. Production Volume
This number of cycles the mold completes directly impacts the life span of high volume production runs. According to the subject, greater stresses and wear are kept and reduced. This extends the operational life. Essential things are involved in manufacturing, such as:-
- Use molds designed for high durability
- Implement rest periods for the mold
3. Maintenance Practices (Life cycle of a mold)
Proper maintenance is a key determinant. Regular cleaning, inspection and lubrication prevent the long term operation of the mold. Many problems may occur in the future, so it is better to keep all these things in mind now and keep doing the maintenance from time to time.
4. Operating Conditions
Extreme operating conditions such as high temperature, pressure and compressive materials can derail all of these. This mode optimizes injection molding machine settings, combines with appropriate materials, and we will discuss its effects later.
Conclusion
Understanding and managing the Life cycle of an injection mold is a vital manufacturing process to achieve cost efficiency, consistent product quality, and high productivity of the mold. At every stage of manufacturing, from initial design to mold execution, the team performs maintenance and eventually retires molds to replace parts.
These parts play a critical role in their performance and it is best to invest in quality materials, optimized design and implementing proper activities that will maximize the value of the injection molds and provide competitive advantages in this industry.
0 Comments