Inexpensive Plastic injection molding is a way in which we produce large amount of product in low cost. It is an important manufacturing process that allows for the mass production of plastic at a low cost. It is used in various industries such as automotive, consumer goods, electronics, and medical devices.
The advantage of inexpensive plastic injection molding provides high efficiency and fast production. In this article we have explained the details of inexpensive plastic injection molding, including its process, materials used, cost factors, and tips to reduce expenses.
What is Plastic Injection Molding?
It is the manufacturing method where molten plastic is injected into a mold, then the plastic cool and hardens and take the shape of the mold. It is the best way to making large amount of product at low cost. This process is ideal for producing a large number of identical parts, making it perfect for high-volume production.
The process has several important steps:
1. Clamping
When the mold is closed tightly and the two halves of the mold are secured together by a clamping unit.
2. Injection
The molten plastic is injected through a nozzle at a high pressure into the mold cavity. This pressure helps the plastic fill the whole mold cavity with the molten plastic evenly.
3. Cooling
When the plastic cool down, the molten plastic turned into solid and form the desired shape.
4. Ejection
After the completion of task, the product is removed from the mold and ready for next processed if needed.
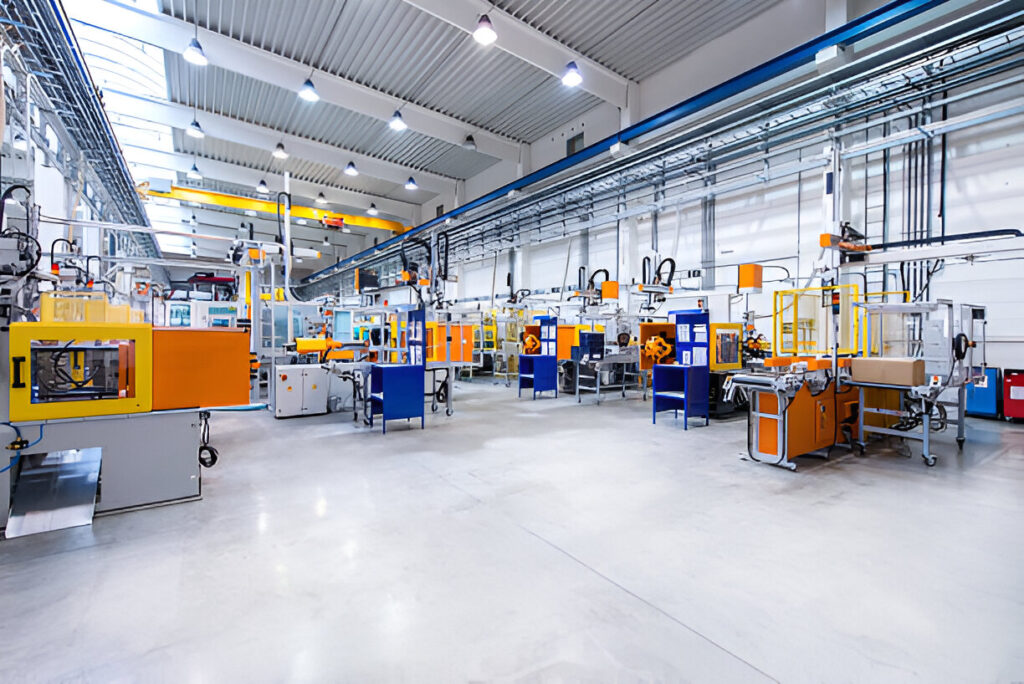
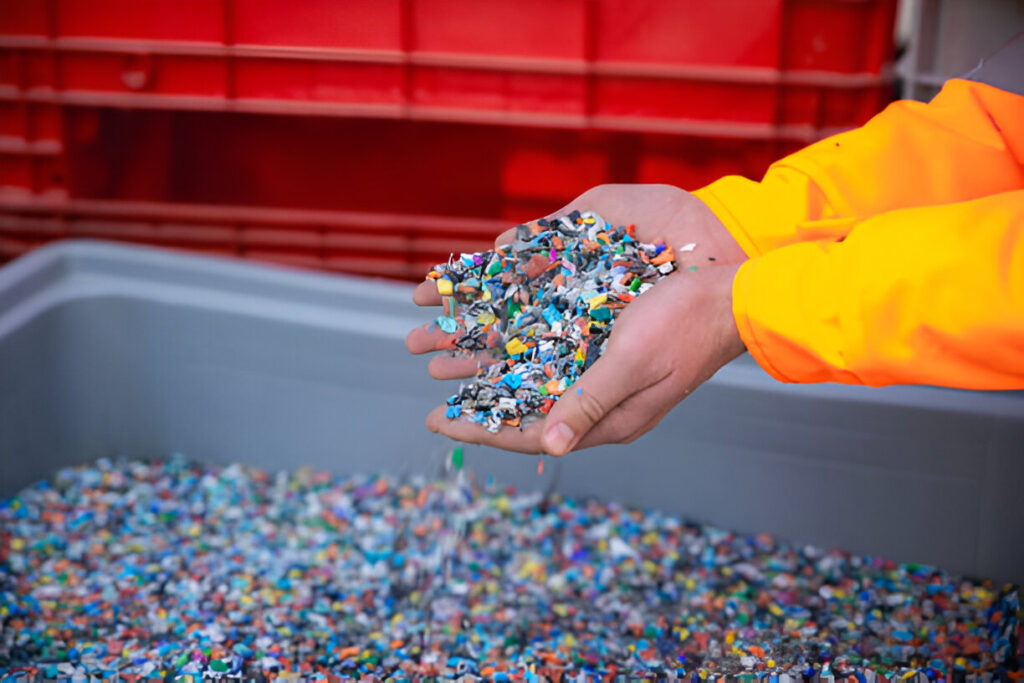
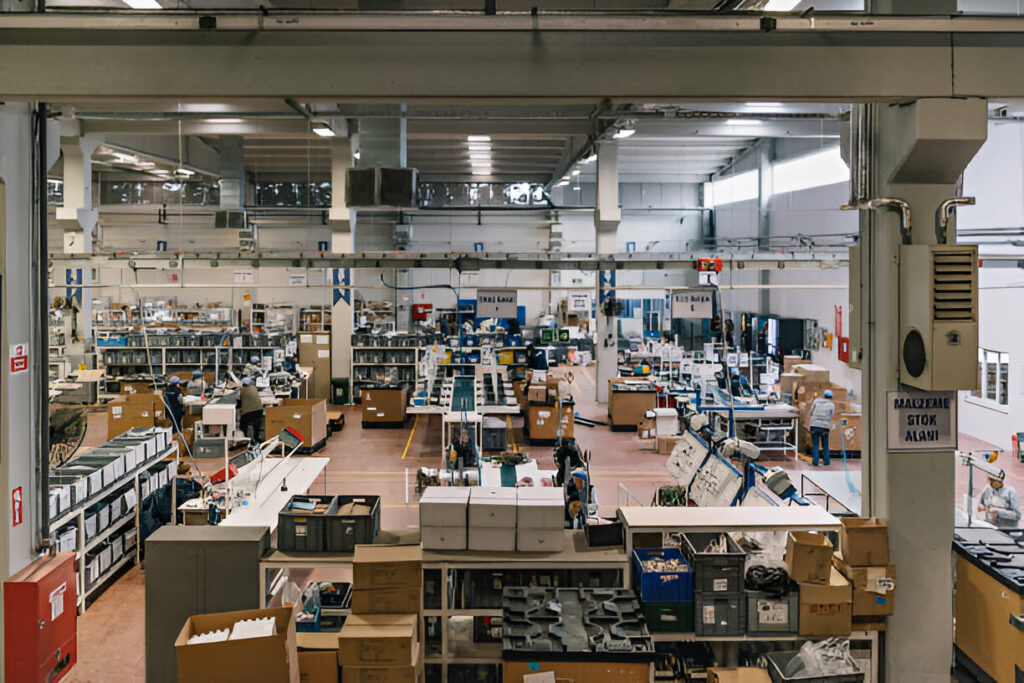
Materials Used in Injection Molding
It is very important to choosing a best quality of material for injection molding otherwise it affects the cost, strength, and quality of the final product. Commonly material used are:
- Polyethylene (PE): Polyethylene is the most commonly used plastics. It is cheap and available in different types. Products like plastic bags, bottles, and containers.
- Polypropylene (PP); It is used in packaging, automotive parts and everyday consumer products. It is known for its flexibility and strength.
- Polystyrene (PS): This plastic has lightweight material that is water resistant, environmentally friendly, economically viable and fully recyclable.
- Acrylonitrile Butadiene Styrene (ABS): ABS is a common thermoplastic used to make light, rigid, molded product such as pipe, automotive body parts, wheel covers, enclosures, and protective head gear.
- Polyvinyl Chloride (PVC): Due to its good chemical resistance and low cost it is used in products like pipes and fittings.
Cost Factors in Injection Molding
The cost of plastic injection molding depends on many things. Few of them are:
- Material Costs: The material cost is depended on what type of material we used. If we used cheaper material, it might be saving our money but may not provide the desired durability or appearance.
- Tooling Costs: These costs include the expenses for the designing, producing, and maintaining the tools, dies, molds, and other equipment used in manufacturing processes.
- Cycle Time: The cycle time is considered is the time takes to complete one injection molding cycle, affect the cost.
- Labor Costs: Labor cost will be depended upon places and complexity of the process. May be automation can reduce labor costs but requires an initial investment in machines.
- Production Volume: The fixed value is spread in large amount so the higher production volumes generally lead lower costs per part.
Strategies to Reduce Costs in Injection Molding?
It requires careful planning and consideration for reducing costs in plastic injection molding. Here are some strategies to minimize expenses:
- Material selection: We have to choose the right material it saves costs because the right material that meets the product’s requirements without over-specifying.
- Optimizing Cycle Time: When you reduce cycle time while keeping the quality the same, the cost per part goes down. You can do this by optimizing cooling times, using better mold designs, and adjusting injection settings.
- Volume Production: The cost will we be reduced when we producing the product in large amount. If the demand of the product is high so, the cost of per unit will be low.
- Outsourcing: Moving production to areas where labor is less expensive can cut costs, but you must balance this with quality control, shipping, and time to deliver
- Using Standardized Components: Whenever it’s possible we have to using standardized components, it’s reduced costs. If we used custom component, it requires additional tooling and it can lead higher expenses.
- Recycling and Reusing Materials: We have to use recycle material so we can reuse the material and it’s not affected on environment.
Low-Cost Tooling Solutions
Injection molding is the one of the most expensive parts of injection molding, but there are several ways to reduce their costs:
1. Aluminum molds: Aluminum molds are cheaper and faster to make than steel molds. They may not last as long, but they are suitable for low to medium production runs.
2. Family molds: A family mold is type of mold in which we construct different type of shape together. But it is complicated when we have to used different material or cycle times.
3. Soft Tooling: We are using aluminums material for soft tooling because it is cheaper than other material and it is suitable for shorter production.
Injection Molding for Prototyping and Low-Volume Production
Injection molding is not only meant for mass production. Thanks to advances in technology, it can also be used for making prototypes and small quantities.
1. Rapid Tooling: It is used for creating mold quickly and at a low cost for this it is using a method 3D printing and CNC. It is not durable as traditional molds.
2. Low-Cost Molding Machines: It useful for small business or startup. It is available for low-volume production. These machines are less expensive and can be a cost-effective solution.
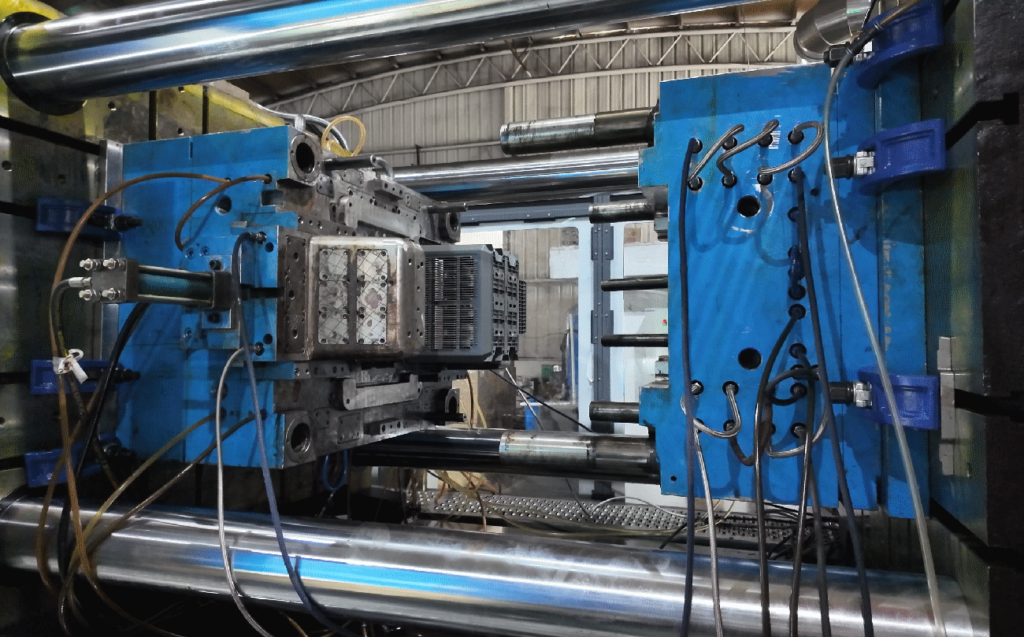
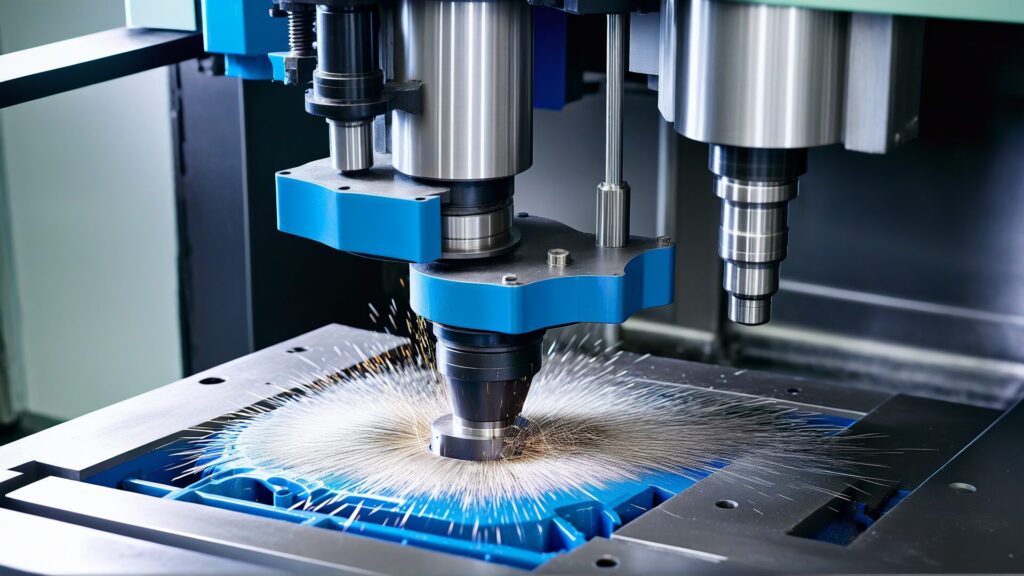
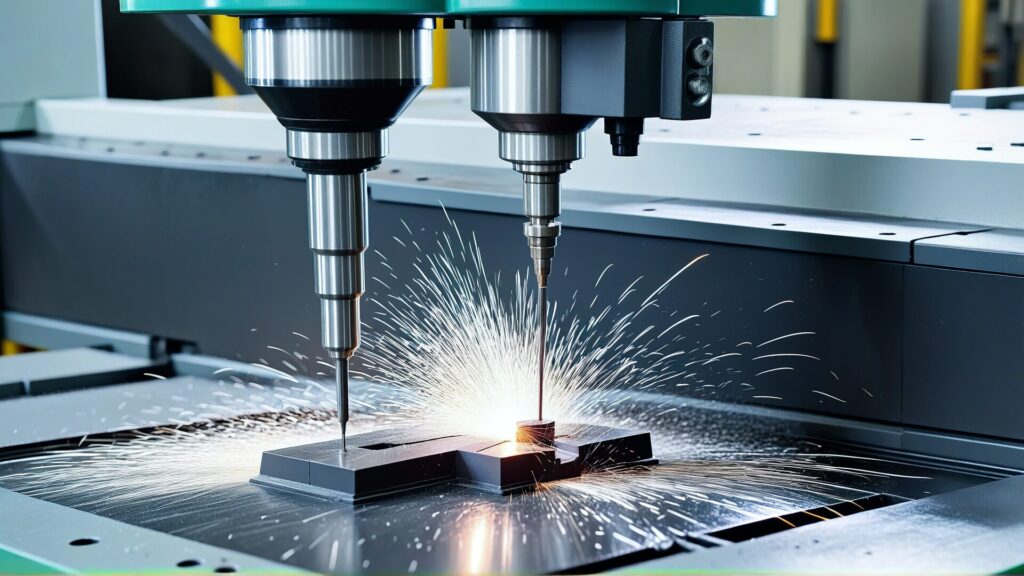
Quality Control in Low-Cost Injection Molding
It is challenging to maintain the quality of product and their cost in any manufacturing process.
Process Control
By following strict process controls, you can maintain consistent quality. This includes keeping an eye on injection settings, mold temperature, and material properties during production.
Conclusion
Inexpensive plastic injection molding is a way in which we produce large amount of product in low cost. It is a best manufacturing process it produces plastic parts. It is mostly used in industries like automotive, consumer goods, electronics, and medical device. Plastic injection molding is method where molten plastic is injected in the mold and then the plastic cool down and get hardens and take its shape.
The material used are: – polyethylene, polypropylene, polystyrene, Acrylonitrile Butadiene Styrene and polyvinyl chloride. It is environment friendly, reusable and recyclable.
0 Comments
Trackbacks/Pingbacks