In the Hybrid injection molding machine, technology is evolving at a rapid pace. One of the most advanced solutions in this industry is the Hybrid Injection Molding Machine. This machine combines the benefits of electricity driven and hydraulic injection molding machines, resulting in top-class performance machines that provide faster cycles, more precise parts due to high control quality & repeatability, reduced energy consumption as well as production flexibility.
Due to these benefits hybrid machines are gaining popularity especially in industries such automotive, medical, Packaging and consumer goods where highest quality with reduced energy consumption and fastest cycle time are key requirements.
In this article, we’re going to take a deep dive into hybrid injection molding machines, their benefits, applications, and the future of hybrids. We’ll also help you determine whether this technology is right for your application.
1. What is a Hybrid Injection Molding Machine?
A Hybrid Injection Molding Machine is an injection molding machine that combines the power of hydraulic systems and the accuracy of electric drives in order to obtain the best performance from both types of machines powering the presses.
Hydraulic System: It is used to provide high pressure power for clamping.
Electric Drive System: The electric drive system provides ultra high-speed response and precision injection control performance.
Servo Motors: These are used for reducing power consumption and improving the accuracy of injection operation.
The result is an efficient and cost-effective solution for multifaceted manufacturing applications.
2. How Hybrid Injection Molding Machines Work
Hybrid machines are similar to hydraulic machines, except they use electric motors for actuation functions such as injection and screw rotation. Electric power is supplied to these motors by an on-board battery or capacitor bank, which can be recharged during machine operation. Like all-electric machines, hybrid machines are generally designed for high-speed, precision operation.
Clamping: The mold is, via the hydraulic power, clamped tightly.
Injection: The melted plastic is injected in the mold into the part, using electrical motors.
Cooling: Cooling of the part till it hardens.
Ejection: The finished part is ejected from the mold.
This process, controlled by state of art control systems guarantees the highest possible accuracy and repeatability.
3. Advantages of Hybrid Injection Molding Machines
Hybrid injection molding machines are the current state-of-the-art in the injection molding industry. These machines use a combination of hydraulic power and electric power. However, some hybrid machines are designed with more emphasis on hydraulic drive system and some with more emphasis on an electric drive system. As all-electric injection molding machines have higher precision and faster response (or reaction), they can be used for a majority of plastics-processing technologies.
3.1 Energy Efficiency
The most obvious advantage of a Hybrid Injection Molding Machine is its inbuilt energy efficiency. Where conventional hydraulic machines consume power constantly – whether the machine is idle or not – hybrids utilize servo motors that only operate when needed, and therefore consume power essentially on-demand. Clearly this kind of power consumption can lead to drastically reduced energy consumption, with some claims as low as 40-60% of what you would expect from a regular hydraulic machine.
Key Benefits:
- Lower electricity bills
- Reduced carbon footprint
- Better alignment with the goals of green manufacturing
3.2 Faster Cycle Times
In high-volume manufacturing environments, speed is of the essence. The Hybrid Injection Molding Machine offers faster cycle times thanks to its electric elements that facilitate fast and precise movements during the injection, clamping, and ejection phases. This translates into increased production output without impacting on part quality.
Key Benefits:
- Increased part output per hour
- Manufacturers will be able to deliver items in less time.
- Manufacturers can gain increased productivity.
3.3 High Precision and Repeatability
The precision levels offered by electric drives result in exceptional repeatability and tolerance control, particularly important for applications (e.g. medical, electronics and automotive) where maintaining close dimensional tolerances is critical.
Key Benefits:
- Same part dimensions on every batch
- Reduced defect rate
- Better material usage and waste control
3.4 Lower Operating Costs
While the upfront investment for a Hybrid Injection Molding Machine might be higher, the savings you see in operational costs are well worth it. With reduced maintenance requirements, lower energy consumption, and less downtime, you will have a lower total cost of ownership (TCO) over time.
Key Benefits:
- Lower maintenance costs
- Less hydraulic oil required
- Decreased downtime as you won’t have to wait for parts.
3.5 Reduced Environmental Impact
With sustainability increasingly a factor in manufacturing, the Hybrid Injection Molding Machine caters to this trend. Less energy consumed, lower emissions, and quieter operations – greener environment and eco-friendly production is finally here.
Key Benefits:
Lower greenhouse gas emissions with global warming becoming a real threat, consumers are continuously demanding eco-friendly products. Noise pollution control systems manufacturers have to ensure that they manufacture their product in such a way that they cause no harm to the environment and also do not become a cause for creating any sort of pollution.
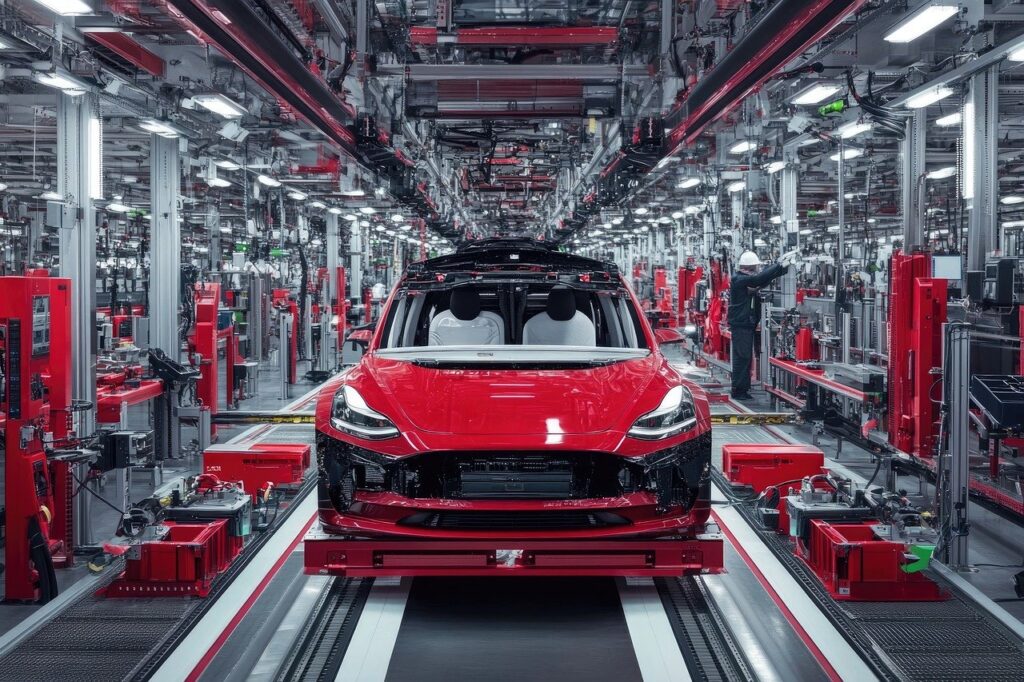
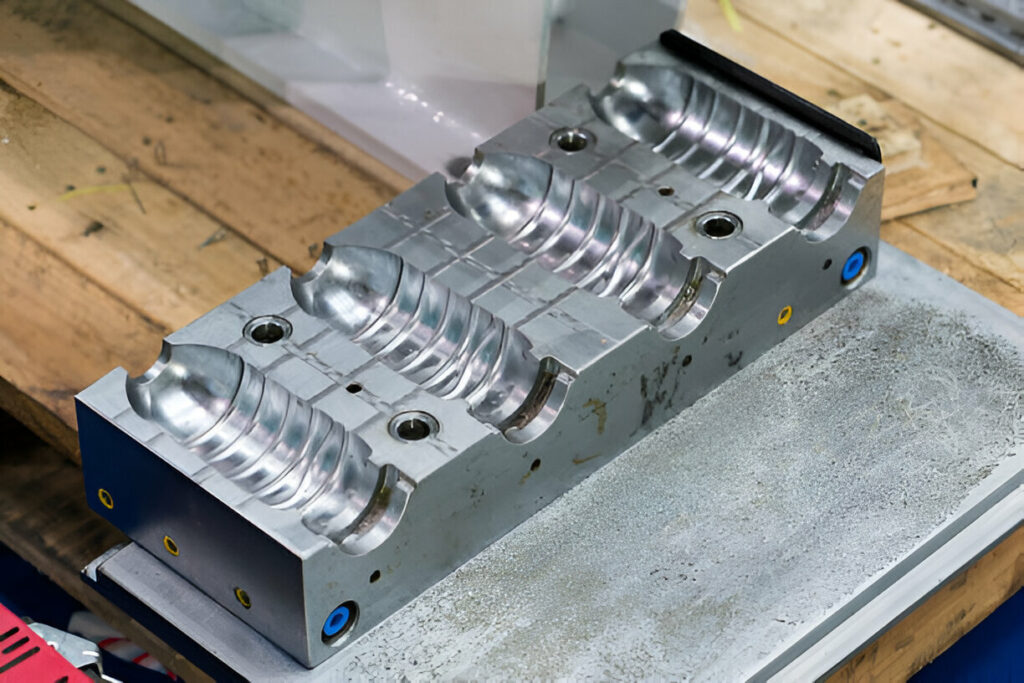
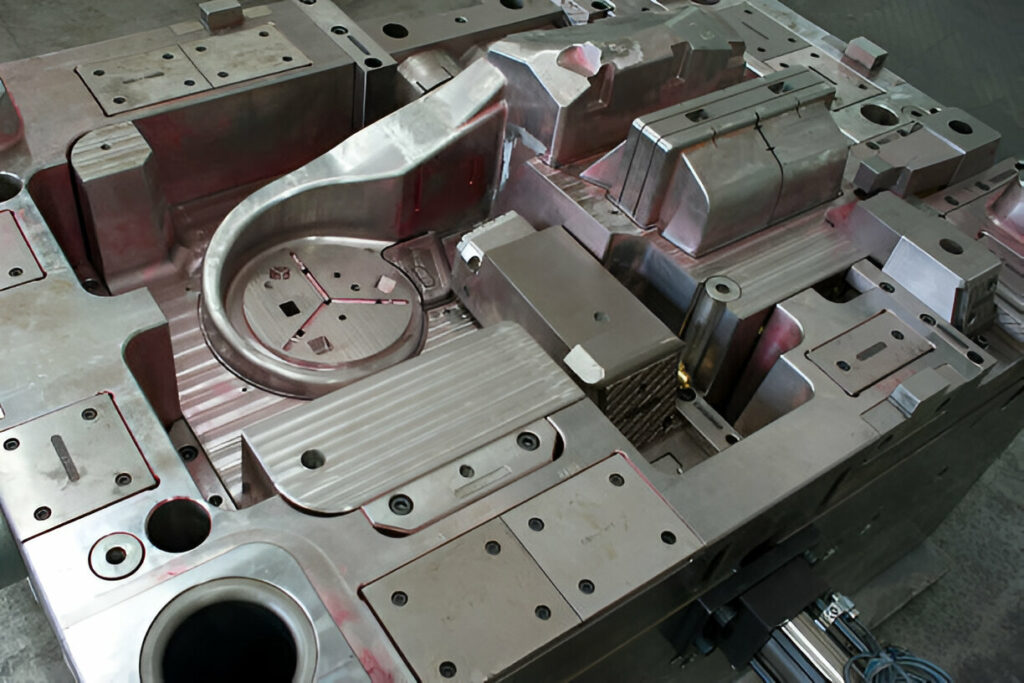
4. Key Industries Using Hybrid Injection Molding Machines
Hybrid Injection Molding Machines are transforming many industries as they can provide high speed, precision and energy efficiency all together. Moreover, the versatility allows hybrid machines to be used in applications where excessive mechanical strength with delicate detailing is required. Below listed are some of the major industries which utilize this advance technology:
4.1 Automotive Industry
Automotive is one of the largest application segments for Hybrid Injection Molding Machine market. In automotive industry, part requirement is extremely stringent as it directly correlated with the safety and efficiency of a vehicle. Hence the parts required in an automobile should be light weight, Strong and precisely manufactured.
Applications in Automotive:
- Dashboard panels
- Bumpers
- Airflow vents
- Interior trims and door panels
- Light housings
- Under-the-hood components
Hybrid injection molding machines offer the benefits of fast cycle times, high clamping force, and repeatable accuracy, which are required for manufacturing under-the-hood automotive parts in large volume with tight tolerance. They also help to reduce vehicle weight by replacing traditional metals with engineered plastics.
4.2 Medical and Healthcare Industry
Precision, hygiene, and compliance to stringent regulations are paramount in the medical industry. Hybrid Injection Molding Machines are instrumental in manufacturing medical grade parts with high precision and cleanroom compatibility.
Applications in Medical Industry:
- Syringes and diagnostic test kits
- Surgical instruments
- Medical device housings
- Implantable devices and connectors (non-reactive plastics)
Hybrid machines guarantee stable production with minimum variance important also for life critical. Their energy efficient operation lowers considerably the carbon footprint of medical device manufacturing.
4.3 Packaging Industry
It is very important to be fast and consistent in the packaging industry as millions of products are being molded every single day. And you get that done with Hybrid Injection Molding Machines, as they provide you high cycle times and reputability.
Applications in Packaging:
- Bottle caps and closures
- Food and beverage containers
- Packaging of cosmetics
- Industrial and household containers
- Pharmaceutical packaging
These machines reduce material waste, use less energy, and enable multi-cavity molds for mass production—making them ideal for modern, sustainable packaging solutions.
4.4 Consumer Electronics and Appliances
Consumer electronics industry requires extremely precise and miniature components. Hybrid Injection Molding Machine allows the necessary control for manufacturing of delicate plastic parts used in such devices.
Applications in Electronics:
- Mobile phone covers
- Laptop components
- Remote control casings
- TV and speaker enclosures
- Connector housings and micro-molding parts
Their ability to repeatedly manufacture thin-walled parts with complex geometries and fine surface finishes, makes hybrid machines invaluable to electronics manufacturers where aesthetics and function is king.
4.5 Household and Consumer Goods
From kitchenware to furniture parts – the consumer goods industry profits from the high productivity and cost efficiency of Hybrid Injection Molding Machines.
Common Products:
- Buckets, basins and boxes for storage
- Plastic chairs and stools
- Toy parts
- Electrical switches and fittings.
Garden equipment components:
This segment is a high-volume business, and therefore hybrid molding machines are the solution to have reduced production costs, without affecting part quality and design.
5. Comparison with Hydraulic and Electric Injection Molding Machines
5.1 Hybrid vs Hydraulic
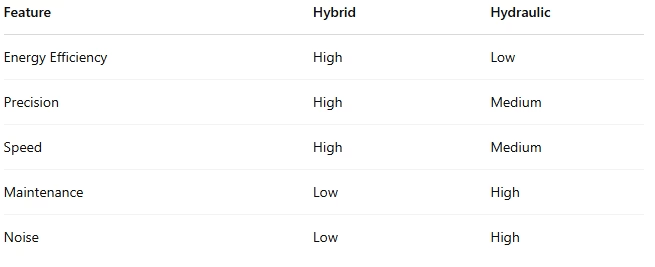
5.2 Hybrid vs Electric
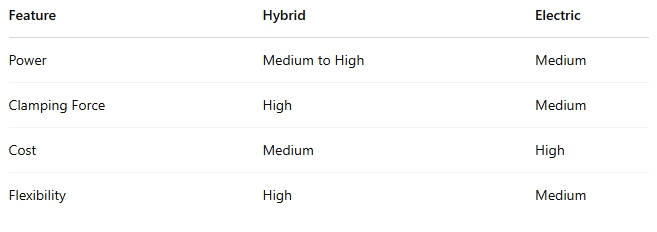
6. Cost Analysis of Hybrid Injection Molding Machines
Before purchase a Hybrid Injection Moulding Machine, it is must to consider the cost parameters in both short term and long-term aspects. Hybrid machines’ initial cost is comparatively higher than Hydraulic machines, but the benefits such as power saving, efficiency and low maintenance shall justify deserve the investment made on it.
6.1 Initial Investment
The initial investment of Hybrid Injection Molding Machine is usually higher as compared to the standard hydraulic model, and this is mainly due to the reason that it incorporates electric servo motors, high-end control systems, and high precision components. Generally, depending on tonnage, brand and specifications a hybrid machine can cost 15% to 30% more than a hydraulic machine.
But, in comparison to all-electric machines, hybrid systems boost performance and energy efficiency for less cost. So, they are a middle-ground option for manufacturers that want similar enhancements but don’t want to pay fully for electric machinery.
Key takeaway
Although hybrid machines require a larger upfront investment, they offer quicker returns through operational savings.
6.2 Operating Costs
One of the single most important benefits to a Hybrid Injection Molding Machine is the lower operating costs it brings along with it, and we’ll break down why here.
6.2.1 Energy Savings
Hybrid machines utilize servo-electric motors that consume power only when required, thus significantly reducing power wastage as compared to hydraulic machines that consume power continuously during use. In many cases savings in energy utilization of up to 40–60% can be achieved.
For high volume manufacturers, this translates to thousands of dollars a year. Over the course of the life of the machine, reduced energy usage means that the small cost difference is more than made up for.
6.2.2 Reduced Cooling
Hydraulic systems produce a lot of heat and require additional energy in cooling systems. Electric driven components on hybrid machines produce less heat, reducing the need for water cooling thus further lowering energy consumption and minimizing water consumption, again particularly valuable where there may be water scarcity or high utility costs.
6.2.3 Less Maintenance and Downtime
Hybrid systems experience reduced wear and tear due to smoother, more efficient operation. Electric servo motors in particular require less maintenance than hydraulic pumps and valves. This reduces machine downtime and increases service intervals resulting in:
- Less maintenance costs
- More machine up-time
Similar improvements have been seen by switching from hydraulic to hybrid machines, with one company reporting a 35% reduction in maintenance costs and a 20% increase in production uptime.
6.2.4 Lower Lubrication and Oil Costs
The most obvious savings from not needing hydraulic fluid for electric components are a reduction in oil purchases, disposal costs, and potential environmental fees associated with oil spills and handling.
6.3 Total Cost of Ownership (TCO)
The TCO of a Hybrid Injection Molding Machine consists of the initial purchase, energy consumption, maintenance, labor, downtime and consumables. Over a 5-to-10-year period Hybrid Machines have consistently lower TCOs than conventional machines.
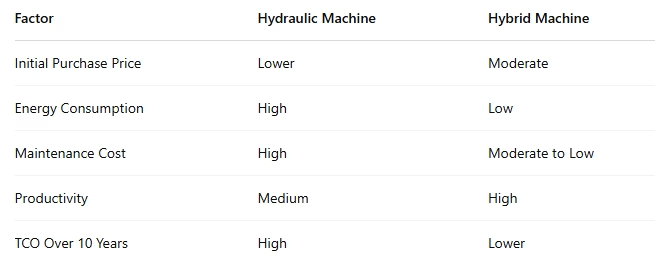
7. Frequently Asked Questions (FAQs)
7.1. What is a hybrid injection molding machine?
A Hybrid Injection Molding Machine is a machine that combines electric and hydraulic technologies for the greater benefit of high speed, high precision and energy efficiency in plastic injection molding. It is really somewhere between an all-electric machine and a hydraulic one – electric machines are designed around linear motor drives whereas hydraulics procures its power from oil which is why they don’t respond as quickly.
7.2. How does a hybrid injection molding machine differ from electric and hydraulic machines?
Electric Machines: They’re precise, clean, and save energy. The knock? They don’t pack the same punch as hydraulics.
Hydraulic Machines: They exert powerful clamping forces and are cheaper up front. The problem? They can be more expensive to maintain and operate because they consume more energy.
Hybrid Machines: Electric efficiency and precision combined with hydraulic power and durability.
7.3 What are the main advantages of using a hybrid injection molding machine?
- Reduced energy consumption
- Faster production cycles
- High precision and repeatability
- Lower operational costs
- Improved environmental performance
7.4 Do all kind of materials fit for hybrid injection molding machines?
Yes, Hybrid Injection Molding Machines are compatible with a wide range of thermoplastics and engineering plastics, such as:
- Polypropylene (PP)
- Polyethylene (PE)
- Polycarbonate (PC)
- Polypropylene (PP)
- Nylon (PA)
- Polystyrene (PS)
- Thermoplastic Elastomers (TPE)
Hybrid injection molding machines are the types of presses that fall into both the electric and hydraulic press categories. They are hydraulic by nature but rely on an electricity-based process for major functions such as injection, clamping, and stripping.
7.5 What industries benefits most with hybrid injection molding machines?
- Automotive – For production of parts such as bumpers and dashboards which are fast and high precision.
- Medical Devices – Sterile, precise and consistent manufacturing.
- Consumer Electronics – Small, detailed parts like buttons and casings
- Packaging – High-speed, high-volume production
- Home Appliances – For structural and aesthetic components
Conclusion
The Hybrid Injection Molding Machine is a real game-changer in the plastic manufacturing industry. It’s the combination of best characteristics of hydraulic and electric systems, resulting in unmatched precision, efficiency and environmental friendliness. As industries are moving towards smart, green and cost-effective manufacturing option, hybrid injection molding would be the obvious choice.
If you belong to automotive, medical, packaging or electronics manufacturing, Hybrid Injection Molding Machines leads to improvements in quality of parts that you produce along with high efficiency in all post process related operations boosting your profitability prospects for longer time durations.
0 Comments