Cycle time is one of the most important factors in injection molding and it directly affects production performance, product quality and profitability. Reducing cycle time can increase productivity, lower costs and improve competitiveness. In this article we will discuss how to reduce cycle time in injection molding.
Injection Molding Cycle Time
Injection molding cycle time is the total time required for one complete injection molding process, including injection time, mold closing and opening time, mold cooling time and part ejection time.
1. Cooling Time – After the molten plastic has been injected into the mold, it must be cooled down and solidified.
2. Mold Opening & Ejection Time – The time to open the mold and ejecting the product.
3. Clamping & Mold Closing Time – Time required to close the mold for next cycle.
For effective minimization of Cycle time each step shall be optimized by reducing delays / inefficiencies.
Strategies to Minimize Cycle Time in Injection Molding
1. Mold design optimization
The design of the mold has a great influence on the cycle time, so we should make the mold design with the idea of flowing shortest, cooling uniform distribution and ejecting longest.
- Use Thin-Walled Mold Designs: By reducing the thickness of the wall, the mold will fill and cool more quickly, which further reduces your overall cycle time.
- Minimize Runner & Gate Length: Shorter runner systems equate to less wasted material and faster injection speeds.
- Optimize Cooling Channel Layout: Uniform cooling can be achieved by reasonable layout of the cooling channel, which can also significantly reduce the cooling time.
- Use High-Quality Materials: The use of mold materials having a good thermal conductivity, such as beryllium copper and aluminum bronze, can help to accelerate the heat dissipation.
2. Reduce Injection Time
Injection time is decided by injection pressure and injection power. The higher the injection pressure, the shorter the injection time will be.
- Increase Injection Speed: Higher injection speeds can help you reduce the fill time. However, they need to be optimized so as not to create defects such as jetting or flash.
- Optimize Melt Temperature: When using the right melt temperature, your material will flow smoothly, reducing injection resistance and the filling time.
- Use Proper Gate Placement: Position gates to permit flow and minimize flow distance.
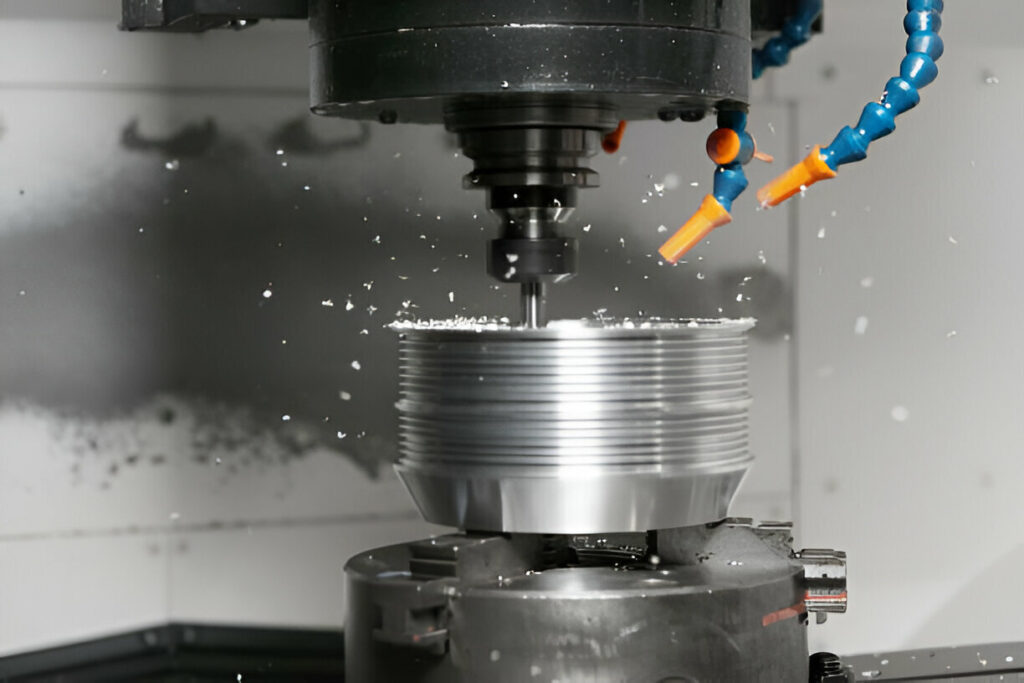
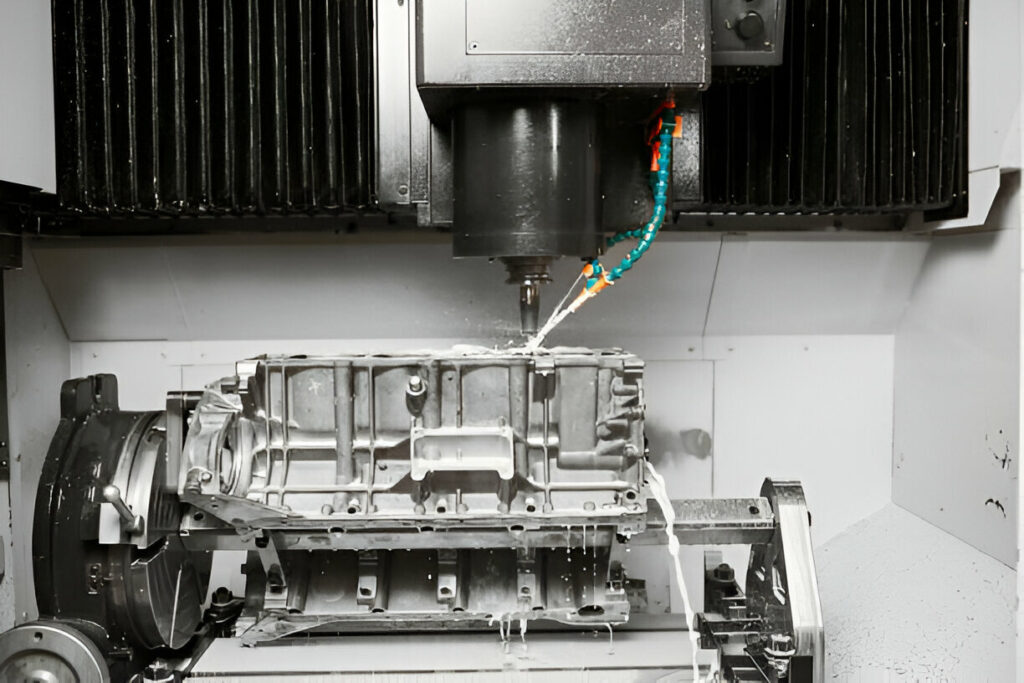
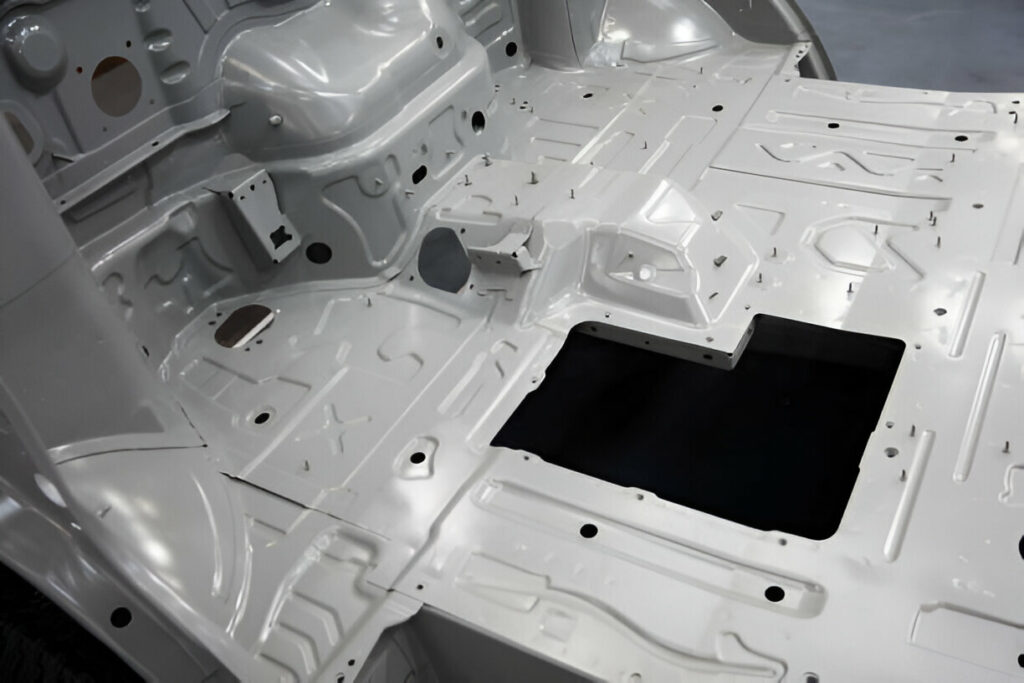
3. Minimize Cooling Time
Cooling time typically comprises the largest portion of the cycle time. Therefore, it is extremely important to adopt effective cooling approaches in order to decrease the total cycle time.
- Use Conformal Cooling Channels: By definition, these channels conform to the shape of the part you are producing. This leads to more uniform cooling and reduced cycle time.
- Use High-Thermal Conductivity Materials: The use of aluminum or copper-based materials in the mold helps with heat dissipation.
- Use chilled water or advanced cooling systems: Cooling systems having capability of controlling the temperature at optimum level helps in better cooling.
- Optimize Part Thickness: Designing parts with uniform thickness helps in minimizing cooling inefficiencies.
4. Improve Ejection Efficiency
Minimize ejection time by a smooth and quick part removal.
- Use Efficient Ejection Mechanisms: Use of air ejectors, ejector pins or robotic systems for rapid removal of the part.
- Apply Mold Release Agents: Using the mold release agents appropriately reduces the friction and helps in quick ejection of the part.
- Maintain Surface Finish: A polished or textured mold surface reduces adhesion thus facilitating faster ejection.
5. Optimize Machine Settings
Fine-tuning the injection molding machine settings will enhance the cycle time.
- Clamping Force – Adjust Clamping Force: Use minimum clamping force required to decrease unnecessary delay for mold opening and closing.
- Screw – Optimize Screw Recovery Time: Faster screw recovery system allows being ready for next cycle.
- Implement Overlapping Processes: For example, start screw recovery while the mold is still cooling to reduce overall time.
6. Utilize advanced automations
Automation in injection molding helps to streamline processes and to make cycle times more consistent as well as efficient.
- Implement Robotics for Part Handling: Automated part removal reduces manual handling time.
- Use Real-Time Monitoring Systems: Sensors and monitoring software’s to gain real time view in order to increase cycle efficiency.
- AI and Machine Learning: Helps identify bottlenecks, process improvement suggestions.
7. Optimize Material Selection and Preparation
Material properties affect flow, cooling, and cycle time. Picking the right material and properly preparing it is critical.
- Use Low-Viscosity Resins: Faster flow means shorter injection time.
- Pre-Dry Materials Properly: Dryness wards off mold moisture-causing defects, and a uniform process.
- Optimize Additives and Fillers: The right combination of additives can help to improve flow characteristics and reduce cycle time.
8. Regular Equipment Maintenance
Performing mold & machine maintenance keeps equipment performing at its best and downtime to a minimum.
- Perform Regular Mold Maintenance: Clean and apply mold release as needed to prevent the part from sticking and slowing down ejection.
- Calibrate Machines Regularly: Make sure that your machines are set up correctly so that you don’t have cycle to cycle inconsistencies.
- Monitor Wear and Tear: Keep an eye on replaceable components e.g. heaters, screws etc. and if they become worn then look at getting them replaced sooner rather than later in order to keep your machine running at peak performance.
9. Apply Scientific Molding Principles
Scientific molding is a systematic, data-driven approach for optimizing injection molding processes — and, by extension, design that focuses on reducing variability and handling time.
- Decoupled Molding: Injection and packing stages are separated for more precise control.
- DOE (Design of Experiments): Are the process parameters best suited for short cycle time?
- Use RJG or Similar Sensors: These sensors monitor real time data which will help in making process adjustments.
10. Downtime and Setup Time Reduction
Faster mold changeovers and less downtimes also help to manage better cycle time.
- Use Quick Mold Change Systems: Hydraulic or magnetic mold clamping systems can be used to reduce the setup time.
- Standardize Molding Parameters: Each mold should have its own predefined setting so you are not guessing what the settings should be.
- Efficient Training of Operators: Good skilled operators are able to troubleshoot and set up a machine much faster.
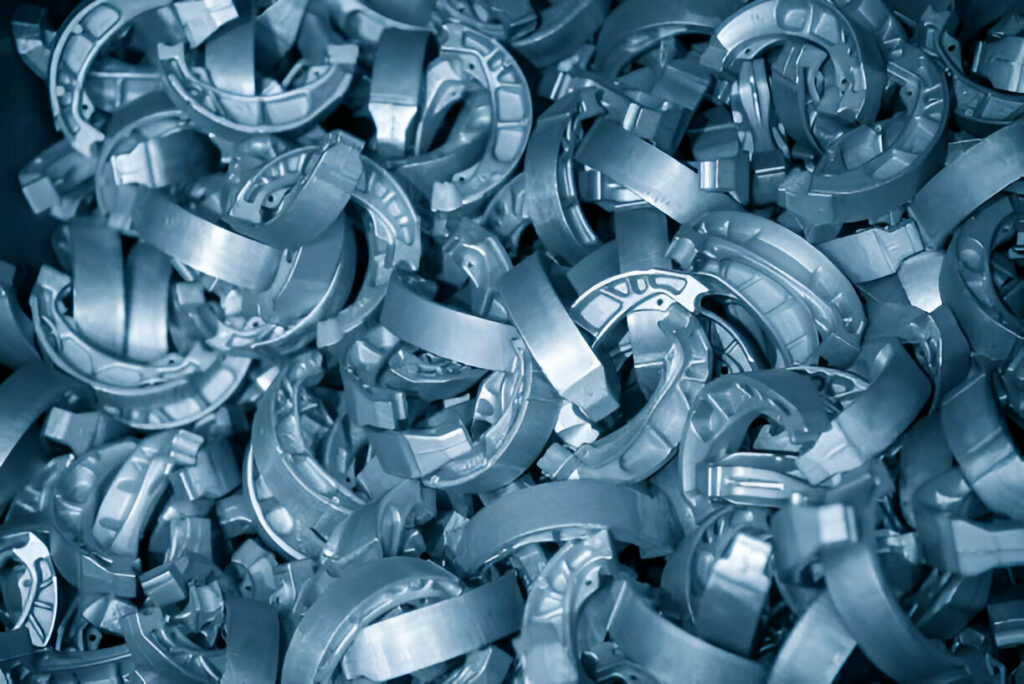
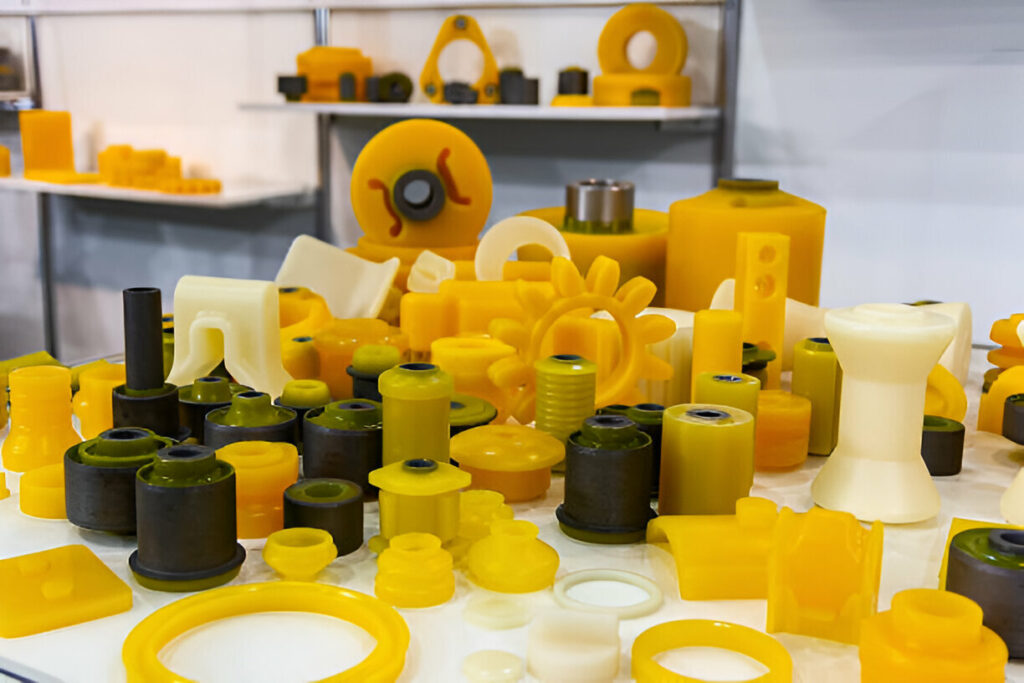
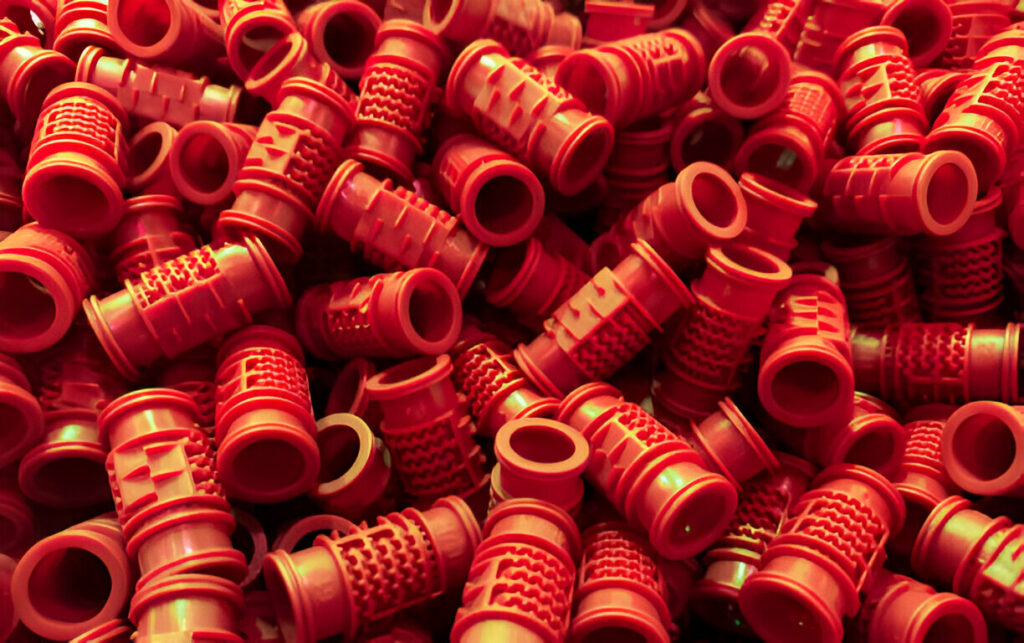
Case Studies: Successful Cycle Time Reduction
Case Study 1: Automotive Industry Optimization
A leading manufacturer of automotive parts optimized cooling channels, and used high thermal conductivity mold materials, reducing cycle time by 30%, and increasing production output.
Case Study 2: Consumer Goods Company
A consumer goods company implemented automation with robotic part removal and overlapping machine processes, reducing cycle time from 40 seconds to 25 seconds per part.
Case Study 3: Medical Device Manufacturing
A medical device company utilized scientific molding techniques and implemented real-time monitoring sensors, reducing cycle time by 20% while sustaining precision and quality.
Conclusion
The cycle time in injection molding can be improved by employing a few key strategies such as ensuring a balanced design of the mold, setting up and maintaining an efficient machine, using proper cooling measures, employing automation where possible and finally carrying out regular maintenance.
Implementing these changes leads to increased productivity and reduced costs while still meeting the desired quality standards. In fact, each second saved on the cycle timing means more efficiency and higher profits for the injection molding operations.
0 Comments