Thermoplastic Polyurethane Injection is a versatile polymer that is widely used in the injection molding industry. Its unique combination of properties—flexibility, durability, and resistance to chemicals—makes it a thermoplastic material suitable for a wide variety of applications. This article helps you explore how the injection molding industry uses thermoplastic polyurethane, highlights its advantages and applications, and explains the role that plastic injection molding machines play along with the potential they offer.
What is TPU?
It is a class of thermoplastic elastomers that bridge the gap between rubber and plastic and thus form a solid. This gives the hard shot segment the ability to work in conjunction with elasticity and toughness. This adaptability makes TPU suitable for both rigid and flexible applications.
This material comes in various forms and is highly tailored to meet specific requirements for instantaneous processing. You can modify it to enhance its hardness, transparency, and resistance. It protects against light and chemicals. Offers flexibility and plays a role in many regions. It is used in significant transactions and is used in injection molding industries.
The Injection Molding Process with TPU
Injection molding involves injecting molten materials into molded cavities to create shapes that fit specific forms. The process requires careful consideration to produce a product with unique properties.
1. Material Preparation
Before proceeding with TPU, it is important to know that TPU is a hygroscopic material, which means that most of the materials in the environment lead to defects such as bubbles or poor surfaces which can be desiccant dryer to remove moisture is a crucial step.
2. Processing Parameters
TPU requires precise control, which the processing parameters provide. Some key points are described below:
- Temperature: The melting temperature of TPU varies between 180°C and 250°C, depending on the grade.
- Injection Pressure: High pressure is essential to ensure the material flows into intricate mold details.
- Cooling Time: TPU’s cooling rate affects the final part’s quality. Uniform cooling ensures dimensional stability.
3. Mold Design of Thermoplastic Polyurethane Injection
The TPU injection molding design accommodates shrinkage and elasticity, ensuring no issues arise. Features such as venting channels and draft angels are work critical to avoid defects such as warping and incomplete filling.
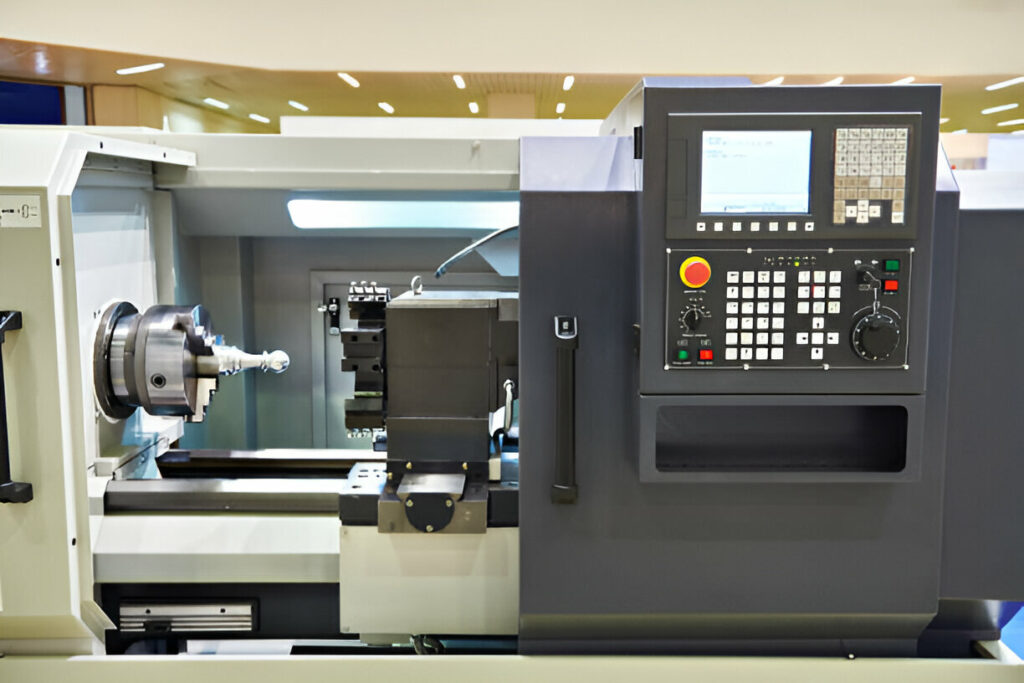
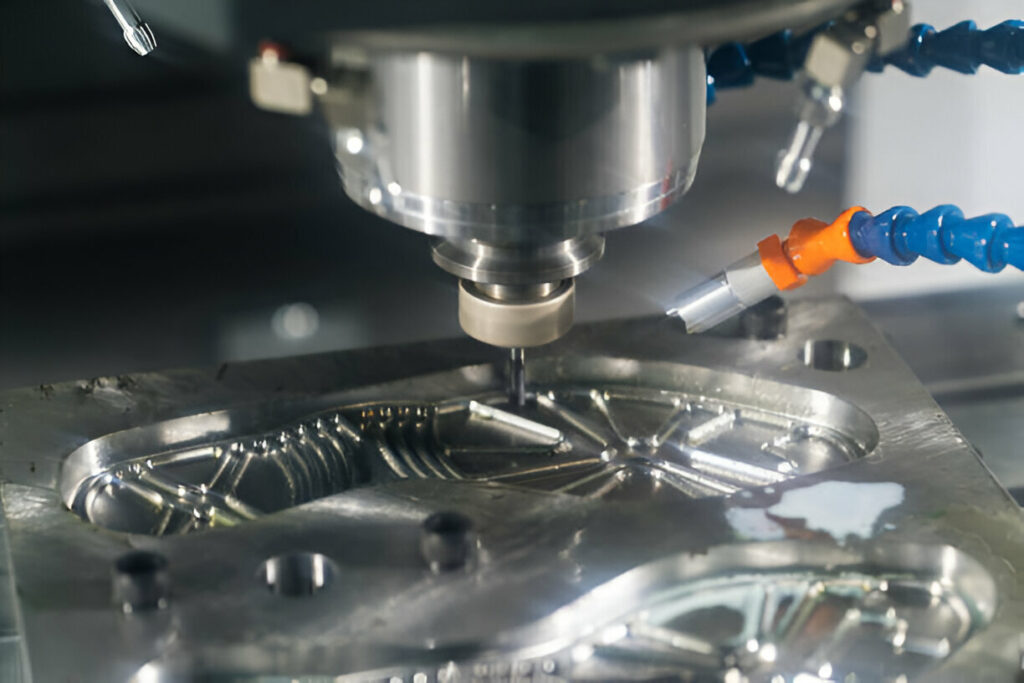
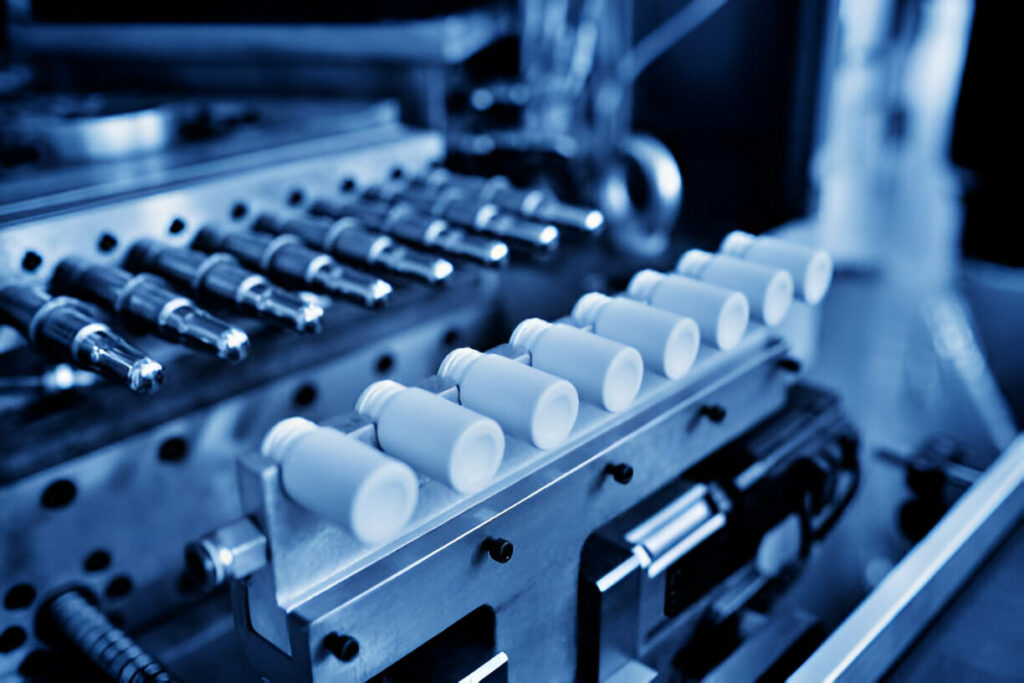
Advantages of TPU in Injection Molding
Using TPU in injection molding offers numerous benefits:
- Flexibility and Elasticity TPU’s elastomeric nature makes it ideal for products requiring flexibility, such as gaskets, seals, and wearable devices.
- Durability TPU exhibits excellent wear and tear resistance, making it suitable for parts exposed to mechanical stress.
- Chemical Resistance TPU is resistant to oils, greases, and many chemicals, ensuring longevity in harsh environments.
- Transparent grades of TPU serve in applications like protective films and medical devices, where visibility is essential.
- Versatility TPU allows co-molding with other materials, which expands its application range.
Applications of TPU in the Injection Molding Industry
TPU adaptability has led to its use in diverse industries:
1. Automotive Industry
In automotive applications, TPU is used for:
- Cable Insulation: TPU’s abrasion resistance ensures durability in wire and cable coatings.
- Seals and Gaskets: Its flexibility and resistance to oils make it ideal for sealing components.
- Interior Components: TPU provides a soft-touch finish for dashboards and handles.
2. Consumer Electronics
TPU is popular in electronic device manufacturing due to its:
- Shock Absorption: Used in protective cases and covers.
- Flexibility: Ideal for wearables like smartwatches and fitness bands.
3. Medical Industry Thermoplastic Polyurethane Injection
The biocompatibility of TPU makes it a preferred choice for:
- Catheters and Tubing: Its flexibility ensures patient comfort.
- Medical Device Housings: TPU’s durability and sterilizability are advantageous.
4. Footwear
TPU is extensively used in shoe manufacturing for:
- Outsoles: Its abrasion resistance enhances durability.
- Midsole Components: TPU’s cushioning properties improve comfort.
5. Industrial Applications
TPU finds use in:
- Hoses and Tubing: For transporting chemicals and gases.
- Conveyor Belts: Its toughness ensures reliability in demanding environments.
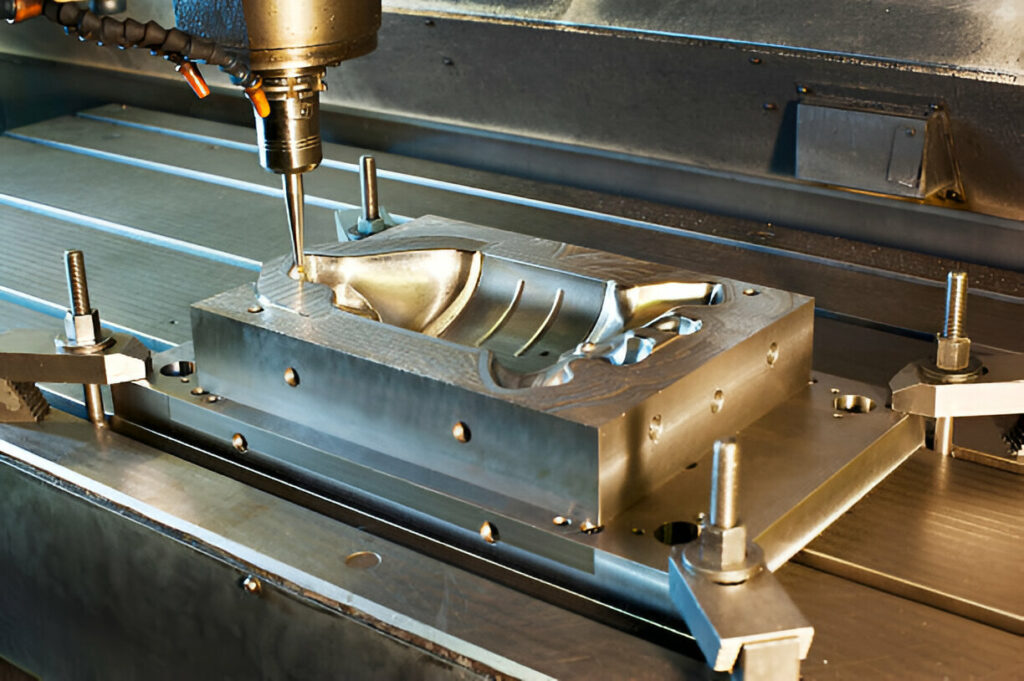
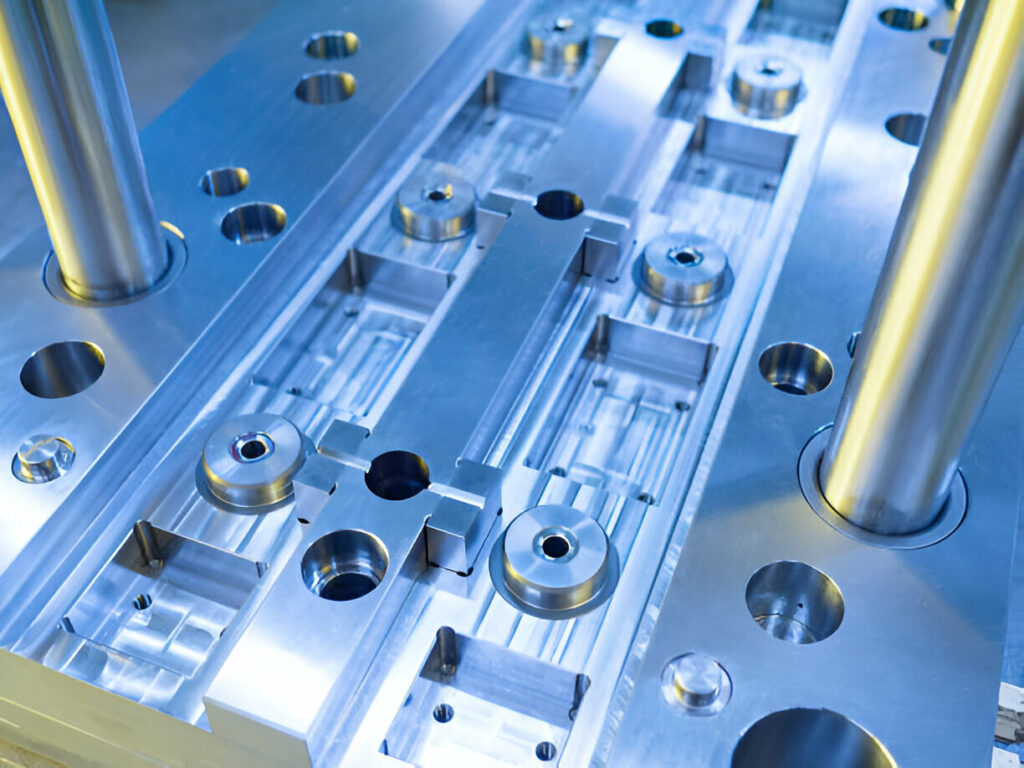
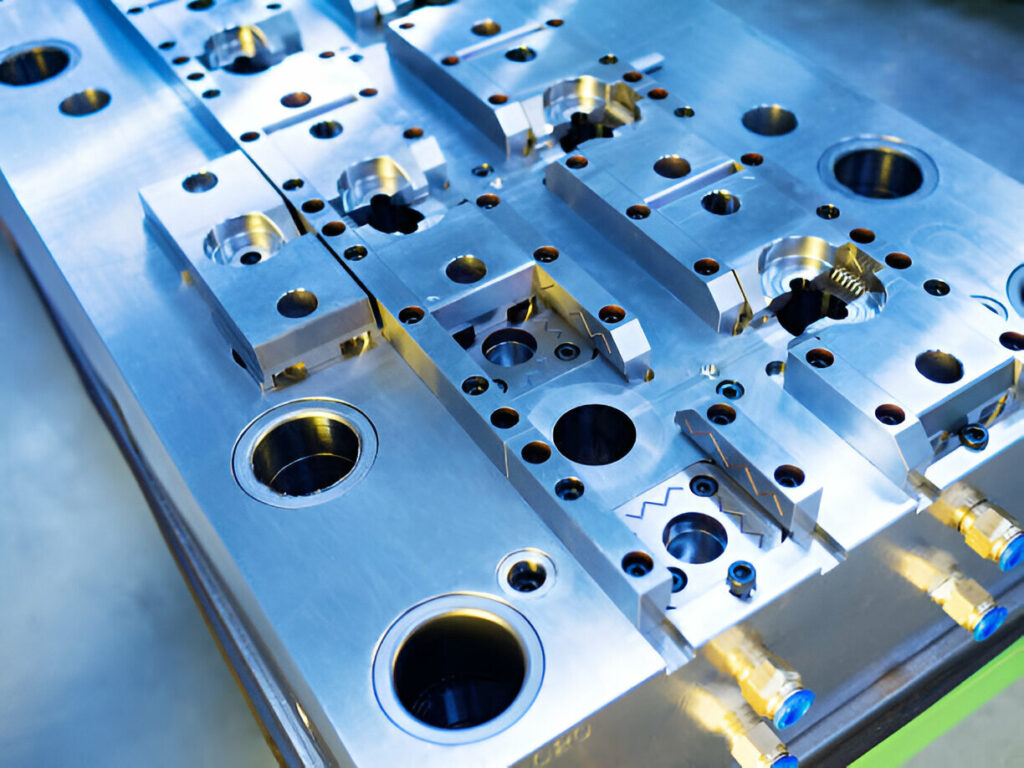
Challenges of Using TPU in Thermoplastic Polyurethane Injection
While TPU offers numerous advantages that will prevent certain challenges as described below:
- Moisture Sensitivity Proper drying is essential to avoid processing issues.
- Processing Complexity TPU’s narrow processing window requires precise control of temperature and pressure.
- Cost TPU is generally more expensive than other plastics, making it less suitable for cost-sensitive applications.
- Shrinkage and Warping Improper mold design or cooling can lead to defects, requiring expertise in handling TPU.
Conclusion
Thermoplastic Polyurethane (TPU) Injection Molding has become a cornerstone for the injection molding industry because of its unique properties and versatility. Many creations, from automotive to medical devices, use this material. As innovation grows, products increasingly require its durability. Plastic Injection Molding Services is playing an advanced role in plastic injection molding machines. Its vital role is being unlocked. The full potential of TPU is being offered. Customized solutions come under very high-quality manufacturing.
As the industry continues to evolve, it continues to grow. TPU involvement in injection molding is important because its advancement is expected to be very high. It enhances efforts on materials, processes, and sustainability. By leveraging TPU, its capability increases. Businesses are able to achieve much higher productions using this technology. Your performance is also better. Molten molds meet many of the demands of today’s modern applications.
With advanced technology, sustainability efforts are increasing. TPU is setting its place in industrial applications. It can give shapes to future manufacturing products and TPU exceptional properties are that it will take the business forward in a competitive market and will create a new identity. With innovations that will be based on consumer needs or collaborate. It will innovate in material science and injection molding services.
0 Comments