Injection molding is involved with the producing high-level quality of Designing for Injection Molding: Tips to Optimize Your Parts with the speed and scalability. the advantage pf this process is directly connected with an engineer and designer for the purpose of manufacturing, function, cost efficiency etc. Highly efficient process for maximum production.
It is widely using overall industry to create a vast array of plastic parts from simply house item for complexity. the advantages of this process, a well-thought-out design is essential. A poorly designed part can lead to numerous issues such as warping, sink marks, voids, and excessive material waste, which ultimately increase production costs and lead to part failures.
The optimized design can be reliably reducing the cycle time and production cost. It is helpful for the engineers and designer for manufacturing and increase performance.
1. Knowledge of the injection molding process.
It is a process of manufacturing process where are molten plastics are injected into a mold to the cool and ejected a solid part. It process are valuable for producing huge volume of parts are within a few time taken.
There are some important guidelines of this process are like that:
- Holding: it is closed by holding unit with the stand injection pressure.
- Cooling: the molten plastic cool and solid in the cavity.
- Injection: plastic is injected into mold.
- Ejection: Mold open and parts are ejected.
2. Selection of material for injection molding.
In the selection time of material, we are fully careful and we are focused on some important factor such are strength, flexibility, heat resistance, and chemical resistance should guide the choice of material.
Consideration for material selection:
- Cost: we are mainly the concern about the cost because of higher-performance materials may increase the cost, so balance material properties with budget constraints.
- Automatic Possessions: Ensure the material chances the part’s powered necessities (stretchable forte, effect confrontation, etc.)
- Movement Features: The ability of melted plastic to current into composite details of the mold rest on the material’s viscosity.
- Contraction: Diverse plastics psychoanalyst at different rates as they cool. Secretarial for reduction in the design is crucial to achieving dimensional accuracy etc.
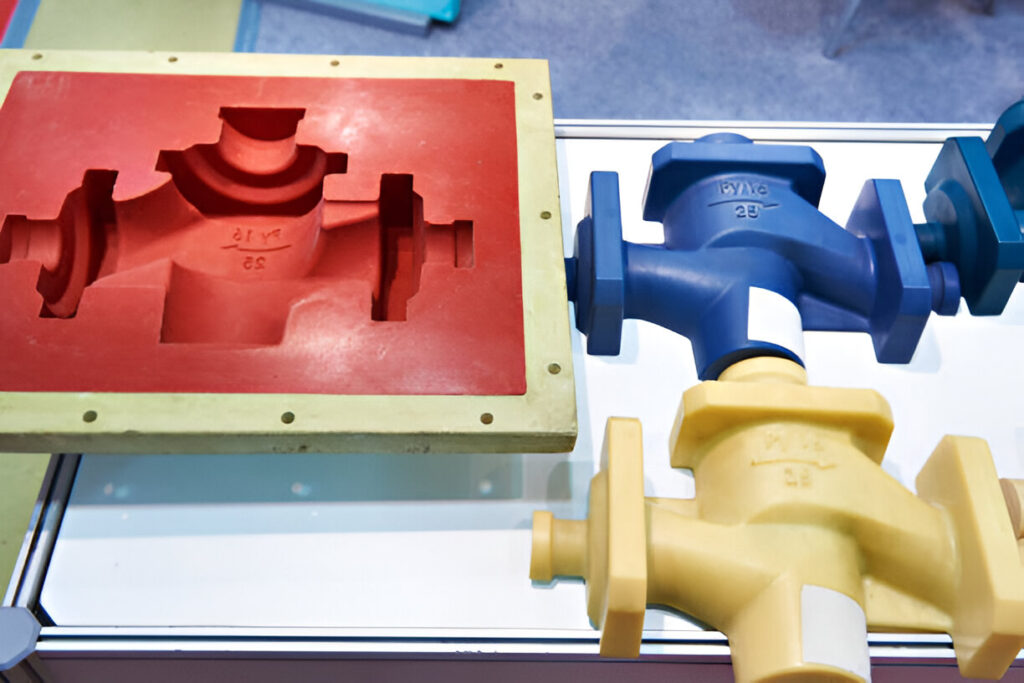
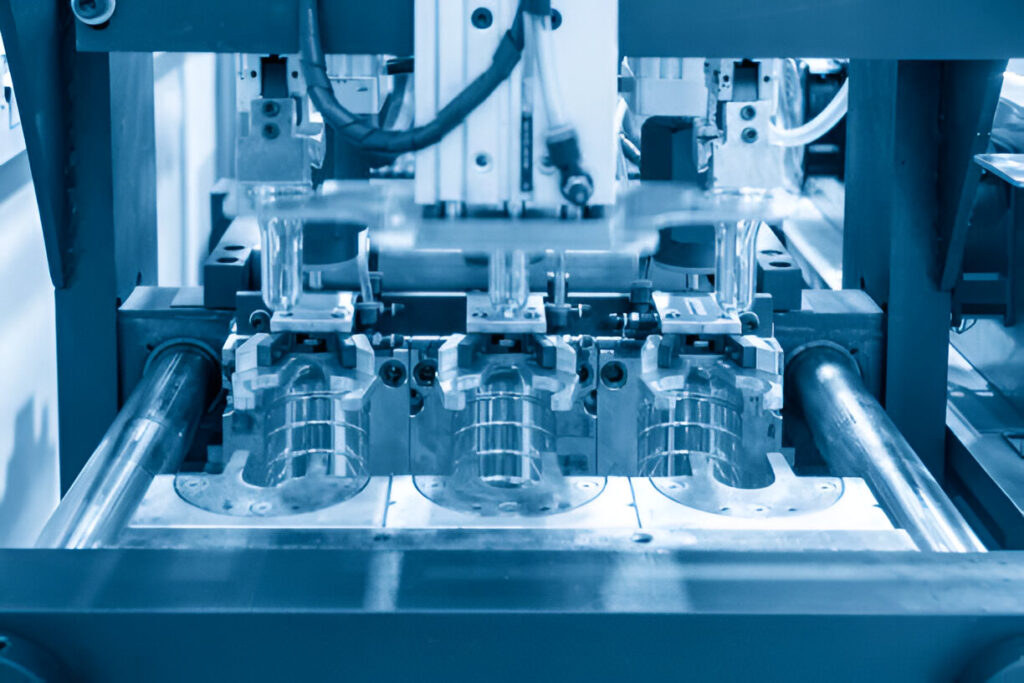
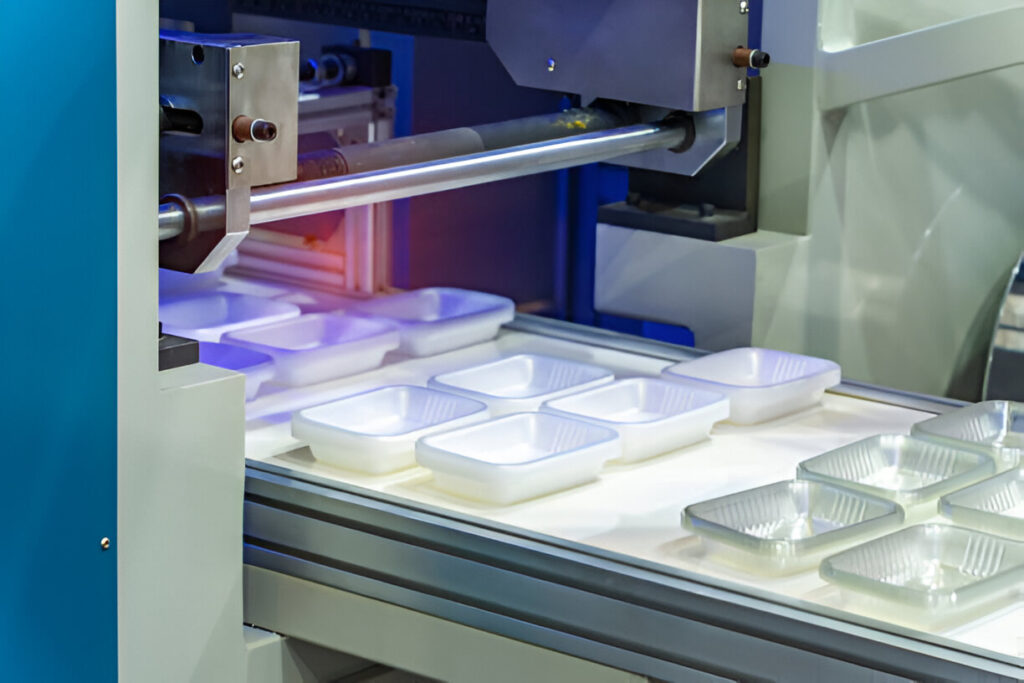
3. Uniform wall thickness
All major wall sections throughout a part as consistent as possible is key to plastic injection molding. Doing so keeps material flow in the cavity consistent and makes for even cooling. Most injection molding materials do not react well to flowing through large differences in thickness.
Inconsistent wall thickness can cause pressure spikes, material degradation, too high of differential pressure across the part, and poor process control. The plastic also cools at different rates when you have varying wall thickness.
Thick wall sections can cause sink issues because the material is shrinking as it cools. To avoid sinking, design ribs slightly smaller to reduce the wall section at the connection point.
4. Drafts angles to your design
Many material removal processes such as CNC machining can produce vertical walls. However, creating a part’s design for injection molding with vertical walls will cause the part to get stuck, particularly at the core, as the part contracts on cooling.
Applying too much force to eject the part greatly increases the risk of damaging the ejector pins and the mold. Design the walls of parts with a slight slant to avoid this problem. This slanting is called a draft.
Due to the high complexity in designing, designers usually add the draft during the final stages of the part design. Different surfaces require varying drafts. Textured surfaces require the most draft.
Some common surfaces found in injection molding and their minimum draft angles are as follows:
- For “near-vertical” requirements: 0.5°
- Most common situations: 1 ~ 2°
- All shutoff surfaces: 3°
- Faces with light textures: 1 ~ 3°
- Faces with medium textures: 5
5. Add ribs and gussets to certain parts
It is preferable to add Designing for Injection Molding: Tips to Optimize Your Parts rather than increase the thickness of parts to increase strength. However, if not properly designed, this can lead to shrinkage. Shrinkage happens when the cooling rate of certain parts is much faster than others, resulting in the permanent bending of some sections. Reduce warping by keeping the rib thickness between 50–60% of the thickness of the attached wall.
6. Add radii and fillet to part design
Applying radii to parts, when possible, eliminates sharp corners, which improves the flow of material and the part’s structural integrity. Sharp corners weaken the part because molten material flows through or into the corner. The only places where sharp corners are unavoidable are the parting surfaces or shut-off surfaces.
Radii and fillets help with part ejection because rounded corners are less likely to stick during ejection compared to sharp corners. Furthermore, sharp corners are also not structurally advisable as they lead to stress points that can fail. Radii help to smoothen out the stress on the corners.
Including sharp corners in your part design will exponentially increase production costs because creating sharp corners in the mold requires very expensive manufacturing techniques.
Add internal radii at least 0.5 times the thickness of the adjacent wall and external radii 1.5 times the size.
7. Avoid undercuts and provide slots where possible
Undercuts are usually created using side cores. However, side cores significantly increase tooling costs. Luckily there are some design tips to achieve the function of an undercut without using side cores. One way of doing this is by introducing a slot instead.
This is also referred to as a pass-through core. Another way is to adjust or move the parting line of the part. When doing this, also adjust the draft angle accordingly. Moving the parting lines is most suitable for undercuts that are on the outside of the part.
You can also use stripping undercuts, also referred to as bump offs. However, only use this feature when the part is flexible enough to deform and expand during ejection from the mold.
Give Enough Clearance:
Bump-offs must have a lead angle of 30° to 45° for effective ejection. All these alternatives to expensive side cores require significant redesigning of the part. When the redesign of a part is not possible due to the possibility that it may affect the functionality of the part, then you have to employ sliding side-actions and cores to deal with undercuts.
These features slide in as the mold closes and slide out as it opens. The side cores must move perpendicularly and have appropriate draft angles.
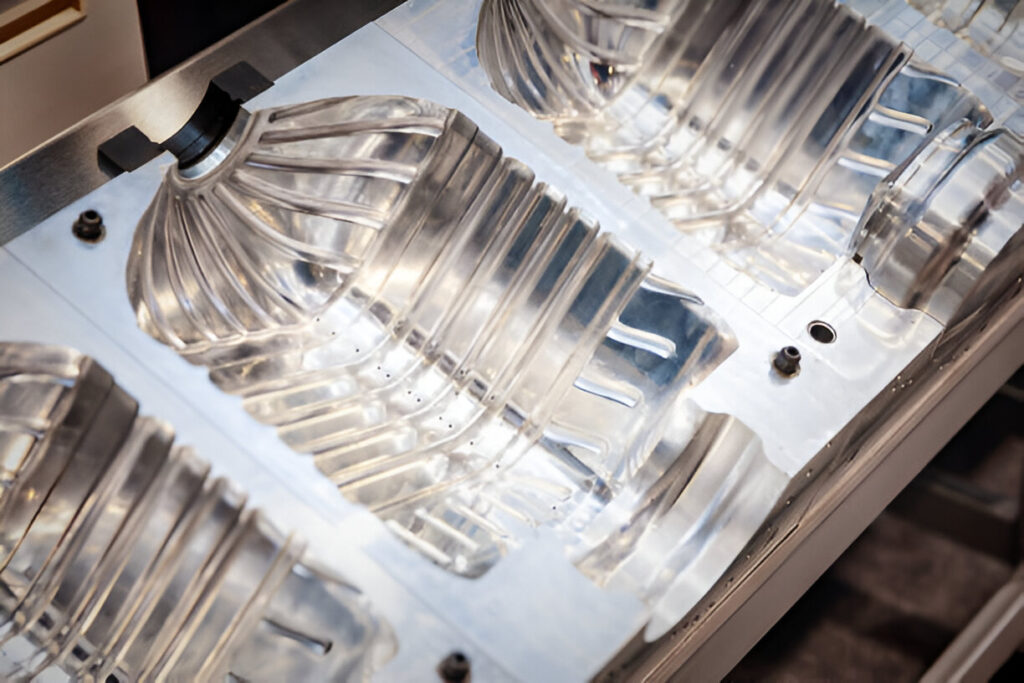
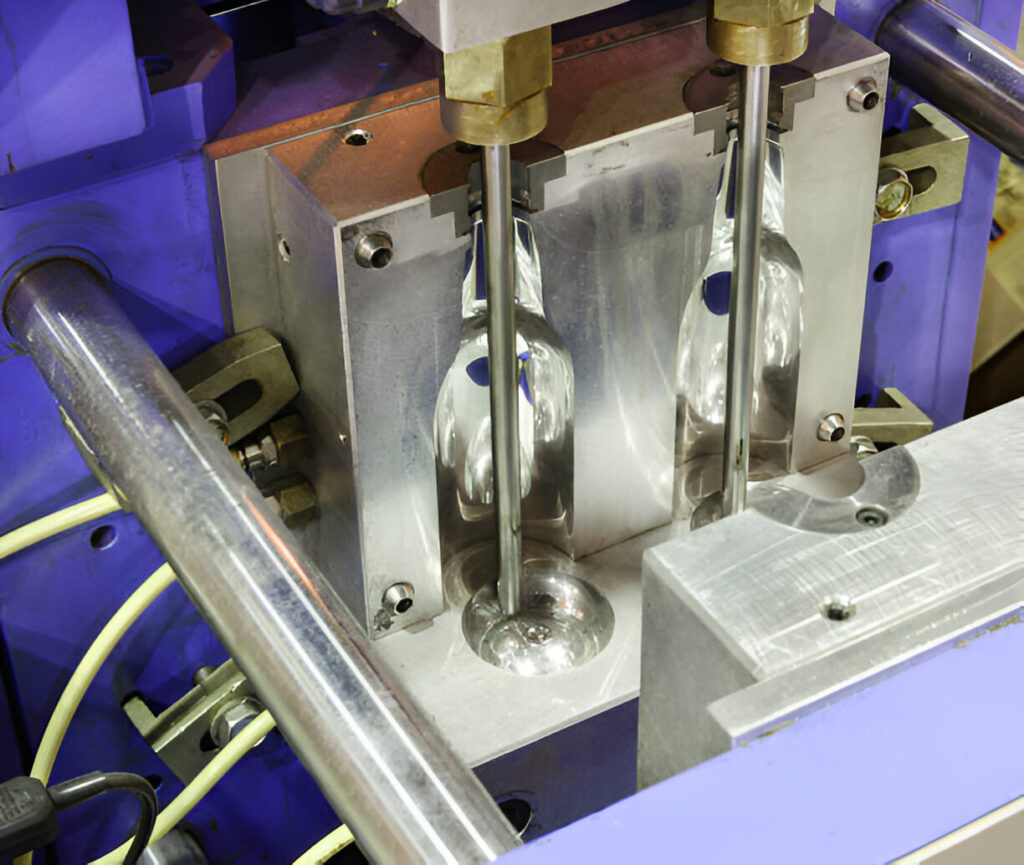
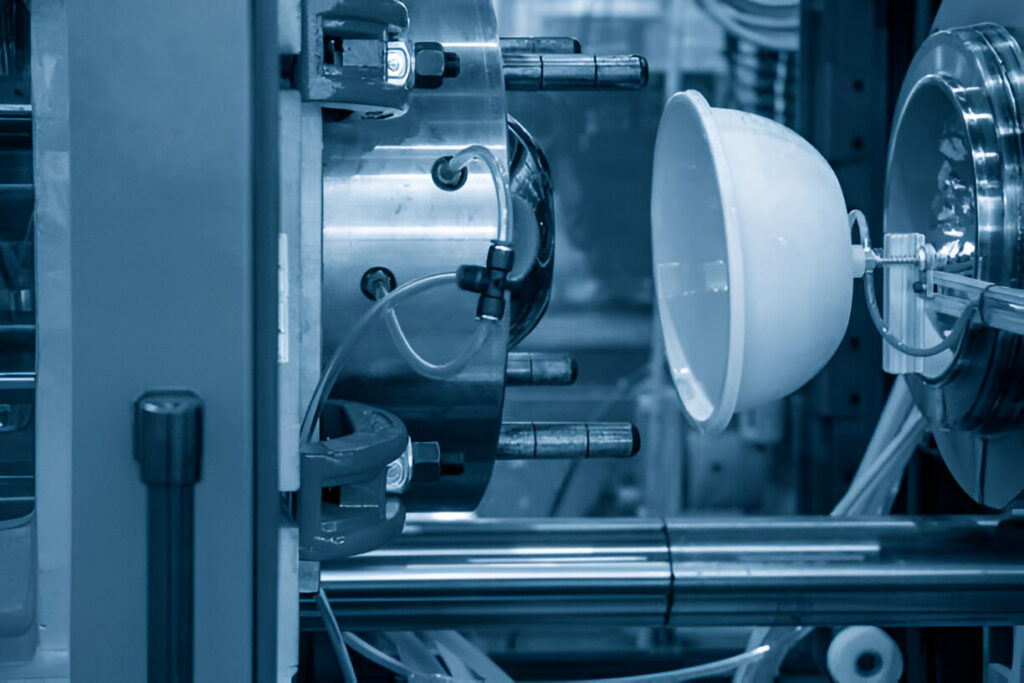
8. Attach bosses to side walls or ribs
Bosses are cylindrical standoffs molded into a plastic part to accept an insert, self-tapping screw, or pin for assembling or mounting parts.
The outer diameter (OD) of the boss should be 2.5 times the diameter of the screw diameter for self-tapping applications.
Bosses shouldn’t be freestanding. Always attach bosses to a side wall or to the floor with ribs or gussets. Their thickness should not exceed 60% of the overall part thickness to minimize visible sink marks on the outside of the part.
9. Gating: Highlight Visually Important Surfaces on Your Part Where There Must Not Be Any Marks
It is important for the manufacturer to understand Designing for Injection Molding: Tips to Optimize Your Parts from the outset what your requirements are in terms of its appearance.
One key point for the tool maker to consider is the gate location. Gates are entry sections through which the molten material enters the mold. The tool maker has to choose the type of the gates and position them strategically to minimize potential quality issues.
Gates also leave gate vestige or a visual indication that the part was gated—even if it is subtle.
That’s why we recommend letting your supplier know about any aesthetic and functional requirements and defining where not to gate. etc.
Conclusion
Designing for Injection Molding: Tips to Optimize Your Parts, above the knowledge we can say that, the design for injection molding is required some few balancing factor. Factors such as material selection, functionality, manufacturability, and cost play a crucial role. Key principles include maintaining uniform wall thickness, using appropriate draft angles, and optimizing the gate design.
When all the process are connected correctly then injection molding can offer an unparallel efficiency and precision. it the go-to process for high-volume industrial of plastic parts. Incorporating the tips discussed here into your design process will help you get the most out of injection molding while minimizing defects, reducing costs, and certifying a smooth production run.
0 Comments
Trackbacks/Pingbacks