Plastic injection molding transformed the automotive industry by allowing automobile manufacturers to have high volume production in a short period of time using plastic. Injection molded plastics are used in a third of cars today. The use of plastic avoids metal replacement, reduces cost per part, weight, improves fuel efficiency and virtually limitless design flexibility has created endless applications to use plastic parts in cars making aftermarket upgrades a breeze or new applications integrated into manufacturing the next vehicle model. Many major countries around the world are focusing on reducing carbon emissions along with fuel consumption and therefore heavily investing on developing fuel-efficient vehicles.
The article would throw light upon the importance of plastic injection molding process in automotive applications. Additionally, we would also get to know about some of the benefits & possible materials that are likely to replace plastics in this industry, technological advancements made over years and current challenges faced by plastic injection molding automobile applications manufacturer. At last, I will take you thought future trends related with metal replacement with use of aluminum or composite-materials.
What is Automotive Plastic Injection Molding?
Automotive plastic injection molding is a manufacturing process that uses thermoplastic polymers to produce parts. The machine injects molten plastic at high pressure into a mold shaped as the inverse of the desired part. The molten plastic cools and solidifies inside the mold to form the part.
Key Features of Automotive Injection Molding
Precision and consistency: Injection molding can produce highly complex parts with excellent precision, repeatability and with a high surface finish. It ensures same part is produced over and over again with zero to minimal variance.
The benefit of cost-effectiveness: The large-scale production will make the per unit product cost down, which is most suitable for the mass production.
Design flexibility: It allows designers to create components that are simply too difficult to be produced by other methods.
Durability and strength: Automotive plastic parts are highly resistant to heat, impact and wear, ensuring longer life.
Reduced material waste: Uses recyclable materials and generates minimum scrap.
Versatility in material selection: You can use different types of plastics, including those that provide the product with flexibility, rigidity, and heat resistance.
Improved efficiency: Advanced automation and AI-driven molding processes enhance production speed and quality.
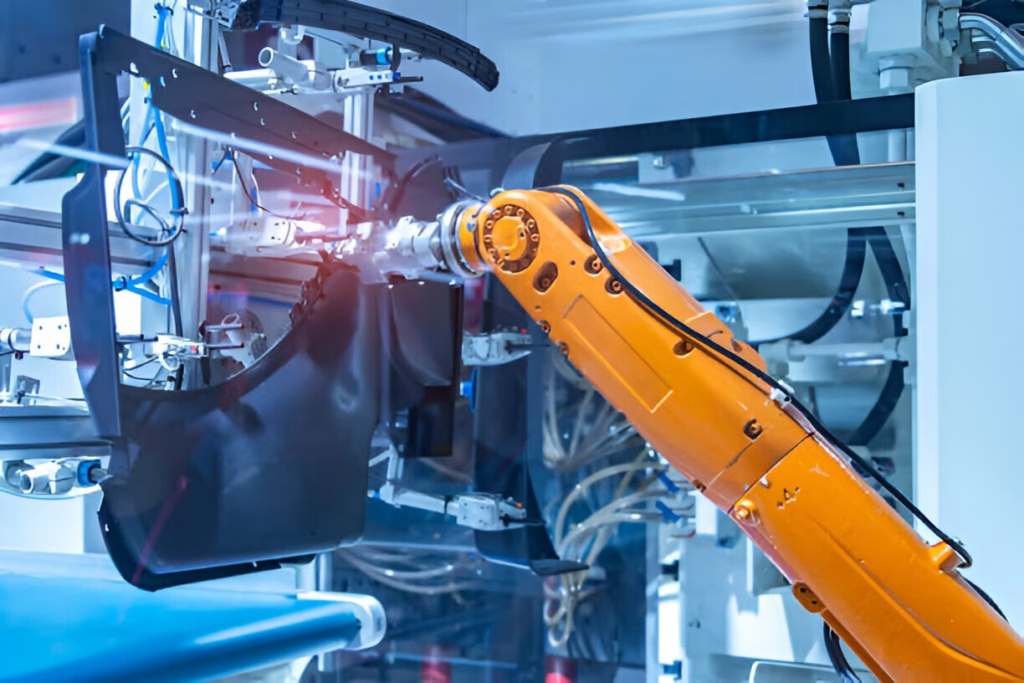

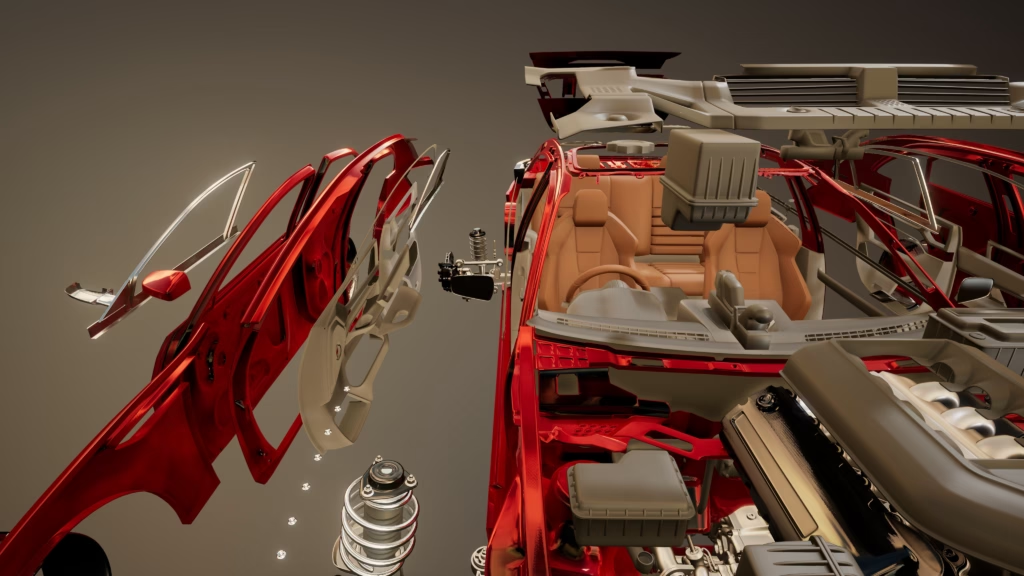
Benefits of Plastic Injection Molding in the Automotive Industry
Many plastics injection molding automotive parts manufacturers opt to make use of car parts made from plastic injection molding. This is due to the fact that the use of these components comes with a wide range of benefits for both manufacturers and consumers.
1. Lightweight Components for Fuel Efficiency
Plastic components are often 50 percent lighter than comparable metal parts, leading to increased fuel efficiency and reduced emissions. When a vehicle uses energy for purposes other than propulsion, it burns more fuel. Therefore, lightweight vehicles of all types offer greater sustainability regardless of whether they run on internal combustion engines or electricity.
2. Cost-Effective Mass Production
Once the mold is built, automotive injection molding enables high-volume production of auto parts at a very low cost per unit. This is due to two factors: first, the relative low cost of building an injection mold as compared to other tools used in other forming processes; secondly, the automated production process dramatically reduces labor costs because injection molding is a highly repeatable and accurate process that doesn’t require much post-processing.
3. Complex Designs and High Precision
Injection molding allows for the production of highly complex and intricate designs which would be too difficult to achieve using traditional manufacturing methods. This flexibility is crucial in the production of aerodynamic, ergonomic and appealing automotive parts.
4. Durability and Impact Resistance
The present-day plastics used in automotive plastic injection molding are exceptionally durable and hence they have high resistance against wear, impact and also with the environmental factors like heat, moisture & chemicals.
5. Eco-Friendly and Recyclable Materials
A lot of the plastic materials used in automotive manufacturing are actually recyclable, which is great news for the environment and supports sustainable production.
6. Faster Production Times
Through automation and advanced molding technologies, plastic parts can be produced faster than with traditional metalworking methods, increasing overall productivity.
Common Automotive Parts Manufactured Using Injection Molding
Manufacturers commonly use injection molding to produce interior and exterior parts of automobiles. This process creates a wide variety of components, including vehicle instrument panels, automotive wiring connectors, floor consoles, medical equipment housings, and other automotive trim parts.
Under-the-hood component applications include coolant flanges, electrical junction boxes, air/fuel delivery parts, cylinder head covers and oil filter housing among many others. Plastic Injection molding produces many different products for the automobile industry using multiple sizes, strengths, colors and complexities in design. The process gives designers more freedom in designing complex devices by fabricating large structures with compound curves enabled as well.
Interior Components
- Dashboard panels: Light and stylish designs for modern vehicles
- Door handles and trims: Long lasting and convenient parts for comfort and safety.
- Center consoles: Storage with usages created for ease of access.
Exterior Components
- Bumpers and fenders: impact-resistant components that reduce injury risk.
- Grilles: Shield the radiator while increasing fuel savings.
- Light housings: Sleek protective covering for head lights and tail lights.
- Mirror casings: Durable plastic enclosures that house the side mirrors.
Under-the-Hood Components
- Engine covers: Protects the engine from dirt and moisture.
- Battery cases: Protection of batteries and for increased vehicle performance.
- Air intake manifolds: Directing air to the engine for combustion.
Structural & Safety Parts
- Seatbelt components: High strength plastics help keep passengers safe.
- Airbag casings: Has airbags safely for accident.
- Sensor housings: Protect electronic sensors from damage.
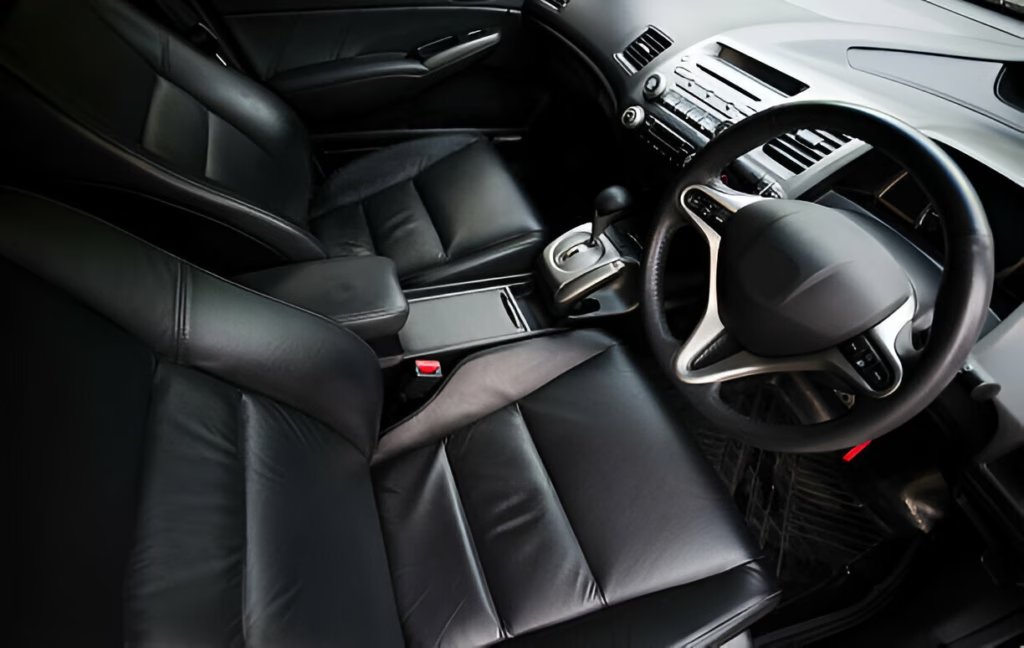
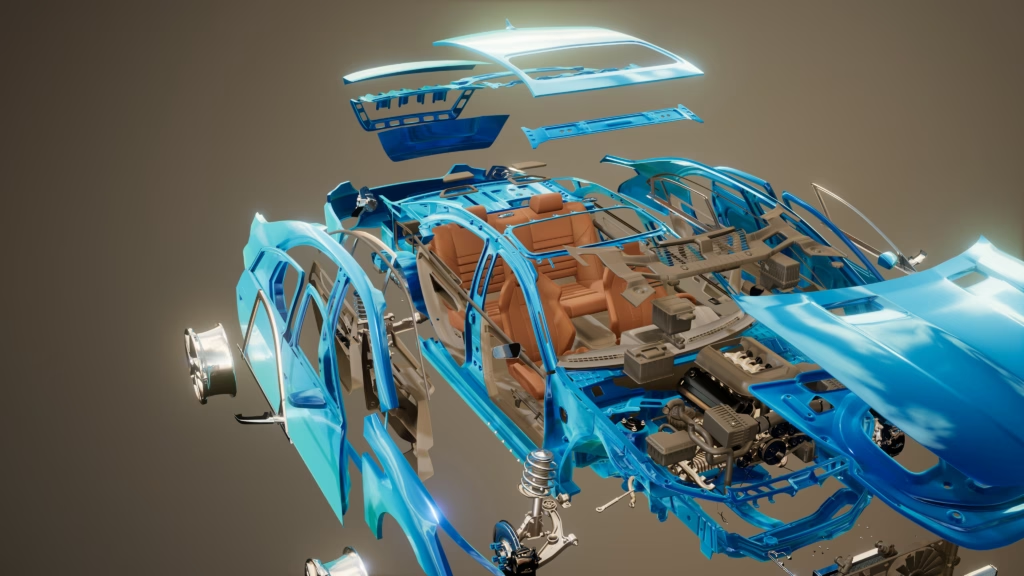

Types of Plastics Used in Automotive Injection Molding
There are multiple types of plastic materials, or resins, that are used in automotive plastic injection molding. Each material has its own set of unique characteristics, but all plastic materials fall into two broad categories: thermoplastics and thermosetting plastics.
Learn More For Life Cycle of a mold
Polypropylene (PP): It is a lightweight plastic which is also chemical resistant. It is used to make automotive parts like bumpers, battery cases and interior trim.
Acrylonitrile Butadiene Styrene (ABS): This type of plastic is impact-resistant. ABS plastics are used for making dashboards, trims panels and mirror housing in automobiles.
Polycarbonate (PC): It’s strong and transparent. Good for light housings, instrument panels.
Polyamide (Nylon): High strength, heat resistant. Used for engine components, gears.
Polyethylene (PE): Durable and flexible, often seen in fuel tanks and wire coatings.
Polyvinyl Chloride (PVC): weathering resistant, featured in door panels and sealing systems.
Thermoplastic Polyurethane (TPU): TPU is an injection molding plastic material that processes easily. It offers elasticity, abrasion resistance, and flexibility, making it a common choice for seals and gaskets.
Polyphenylene Sulfide (PPS): PPS has a very high thermal stability and chemical resistance. It is used for fuel system components.
HDPE (High-Density Polyethylene): Manufacturers use it to produce plastic fuel tanks and other components that come into contact with fuel or under-the-hood chemicals.
Acrylic (PMMA): Transparent and UV-resistant, ideal for automotive lighting and displays.
Conclusion
Plastic injection molding has transformed the automotive industry, enabling manufacturers to develop lightweight, durable and cost-effective parts. The use of advanced materials, accurate molding technologies and sustainability initiatives are accelerating the future development of the automotive plastic injection molding market. With new advancements continuing to deploy in the landscape, new plastic solutions will become more sustainable, high-performance and cost-effective.
0 Comments