Applications in Automotive Industry is a number one manufacturing method which used in the automotive industry. In this method we inject molten plastic into the mold and then it cools down, and then removing the hardest part. This method is fast and produce a large amount of product at low cost.
Now there are many parts of vehicles are made through plastic injection due to its weight and it is available at low cost. In this content we will tell you why we have to used it, is it useful, which type of material used in it and etc.
Benefits of Applications in Automotive Industry
1. Weight Reduction
In vehicles “we are using plastic parts because its light weight it’s reduce the average weight of vehicles”. Plastic is lighter than metal. Car manufacturers want to make vehicles low-emission and environment friendly. Plastic injection molding it help us to produce strong and lightweight parts.
2. Cost Efficiency
We all know that plastic is cheaper than metal and it reduce cost. We knowing that plastic injection molding is produce product in large amount at a time and it is important for automotive industry because once the plastic mold is made, we produce large number of products easily and at affordable price.
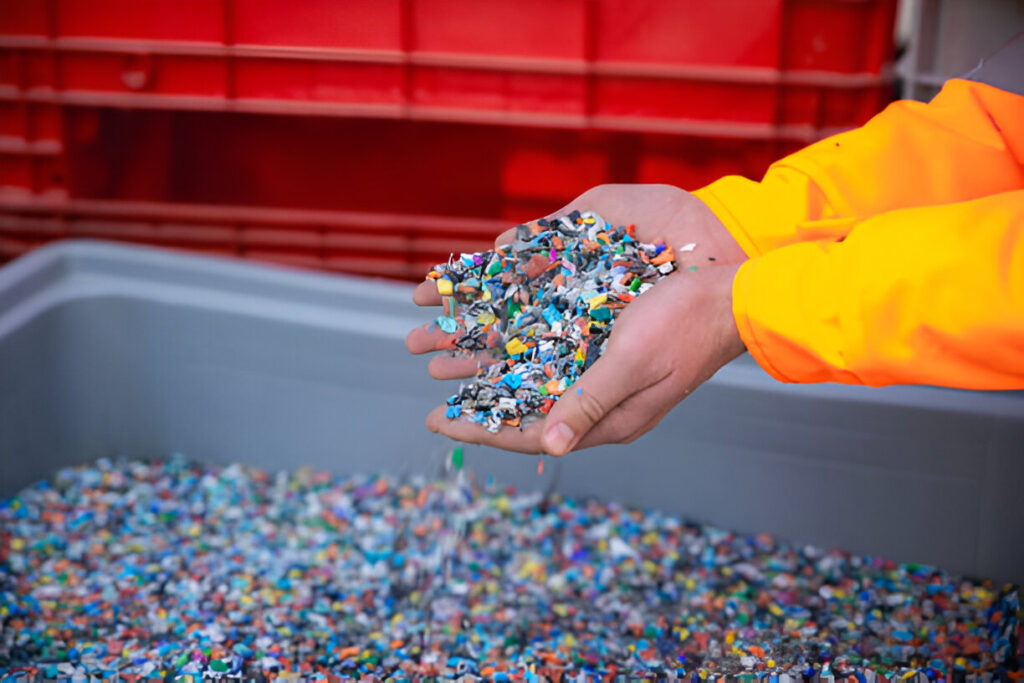
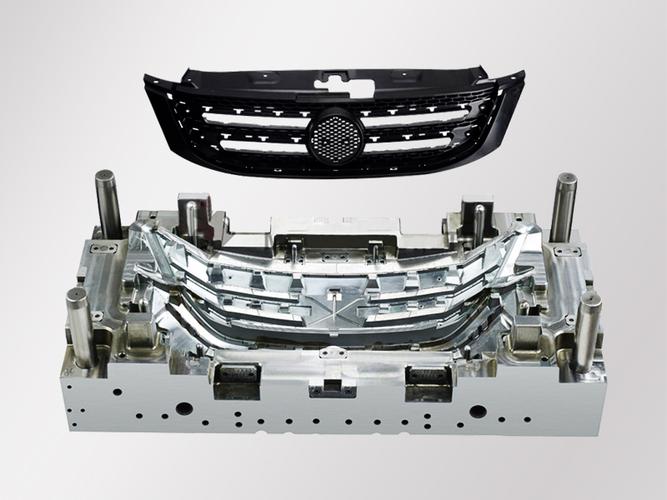
3. Flexible Design
In Plastic injection molding process we have to create complex shapes and design. The flexibility is valuable in automotives industry because it has to fit into tight spaces or have different design. It combines multiple of features combine together in single parts.
4. Eco-Friendly and Sustainable
Applications in Automotive Industry using sustainable practical. Recycle plastics are used in this process due to reducing environmental impact. Plastic material helps to improve fuel emission because they were lightweight.
Common Car Parts Made with Plastic Injection Molding
Plastic material is lightweight and eco-friendly, offering durability and cost-effectiveness. For instance, plastic helps reduce the weight of vehicles. Moreover, advancements in technology have made plastic suitable for designing automotive components. In addition, plastic serves multiple purposes and fits various automotive applications. There are some parts which made from plastics:
- Bumpers
- Chemical tanks
- Wire insulation
- Gas cans and etc.
Types of Plastic Materials Used in Car Injection Molding
Some different types of plastic used in automotive plastic injection molding, depend on some particular parts and its requirements. Here are some popular materials include:
1. Polypropylene (PP)
Polypropylene is the most well-liked plastic in the automotive due to its strength, flexibility, and etc. It is used for both interior and exterior parts.
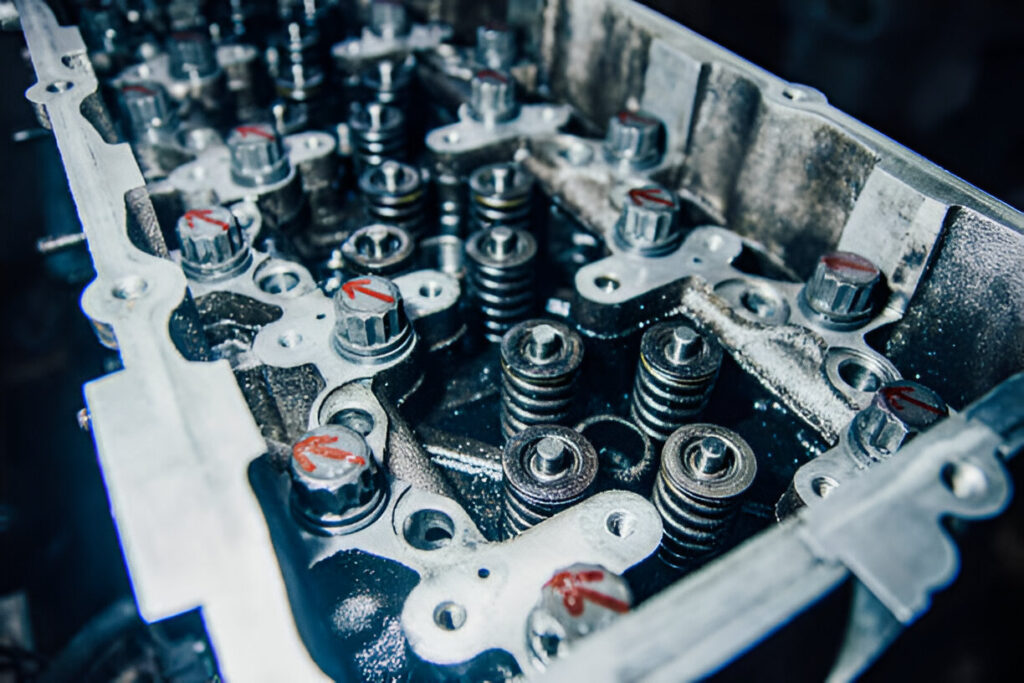
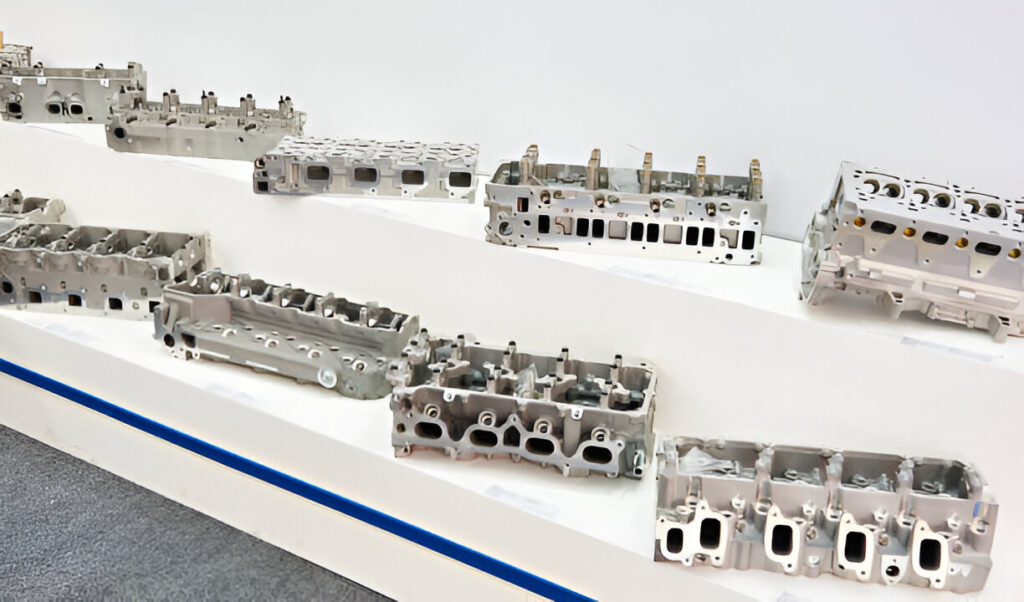
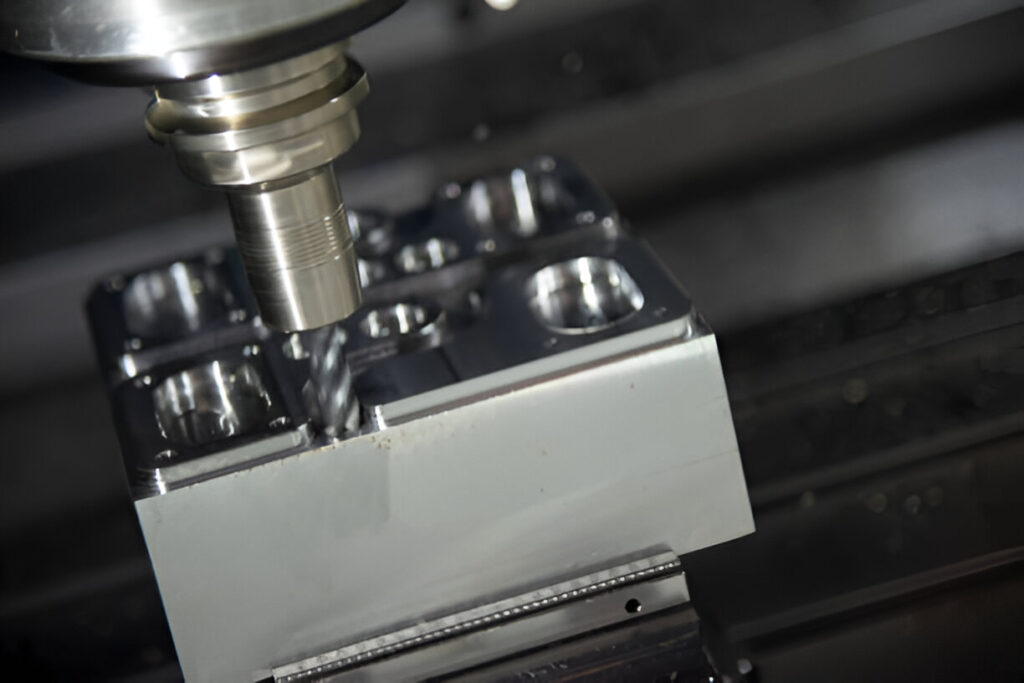
2. Acrylonitrile Butadiene Styrene (ABS)
ABS is used to make interior components like dashboards and trim because it is a strong and durable plastic. Moreover, it serves to create both functional and decorative parts inside the car.
3. Polycarbonate (PC)
Polycarbonate is known for its high impact resistance. It is transparent, lightweight polymer. It is used for car bumpers and headlight lenses.
4. Thermoplastic Elastomers (TPE)
TPE is a flexible, rubber-like structured plastic. It is commonly used for seals, gaskets, and weatherstripping. Additionally, TPE provides excellent durability and resistance to various environmental factors. Therefore, it is a preferred choice for many applications. It is best for both interior and exterior application.
5. High-Density Polyethylene (HDPE)
HDPE is a strong and durable plastic, commonly used in fuel system element like fuel tanks and vapor canisters. It is opposition to chemicals and can withstand the high pressure and temperatures variation’s present in a car’s fuel system.
6. Polyurethane (PU)
Polyurethane is flexible, comfortable, and durable; therefore, it is used in car seating and other interior parts. Additionally, its softness makes it ideal for soft touch-ups on surfaces inside vehicles and padding for seats.
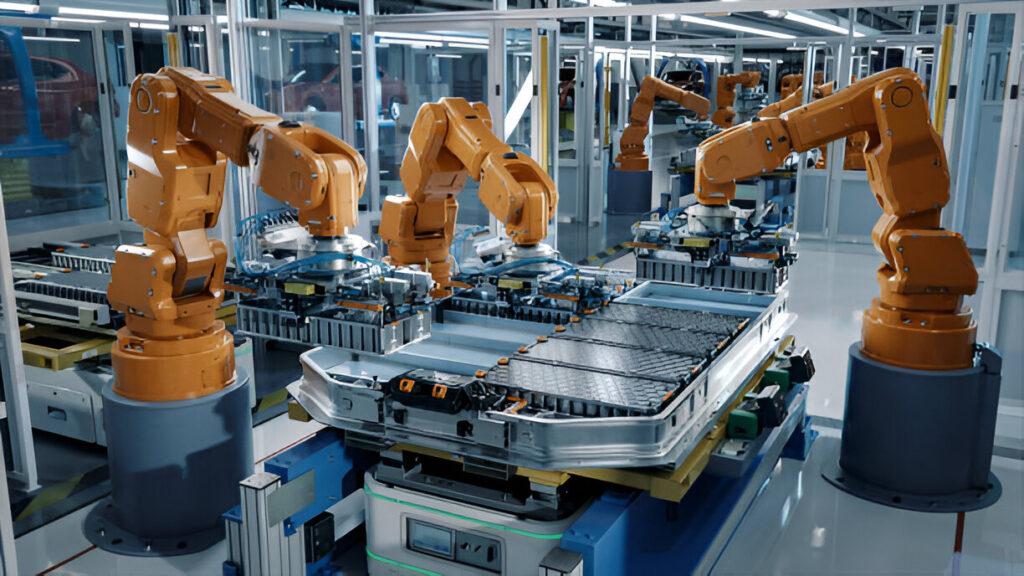
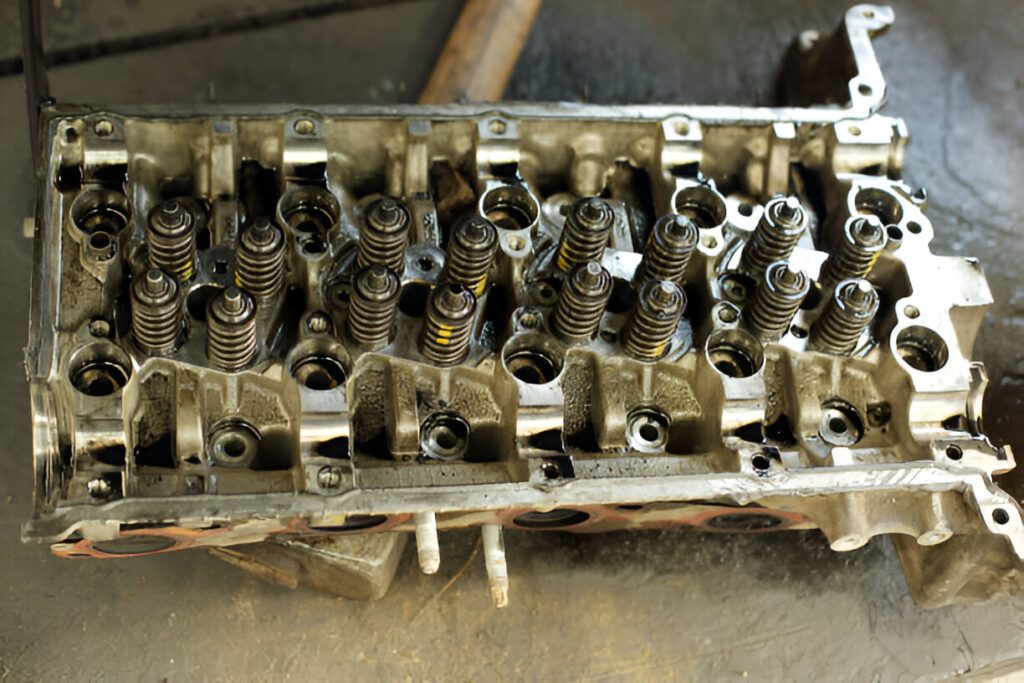
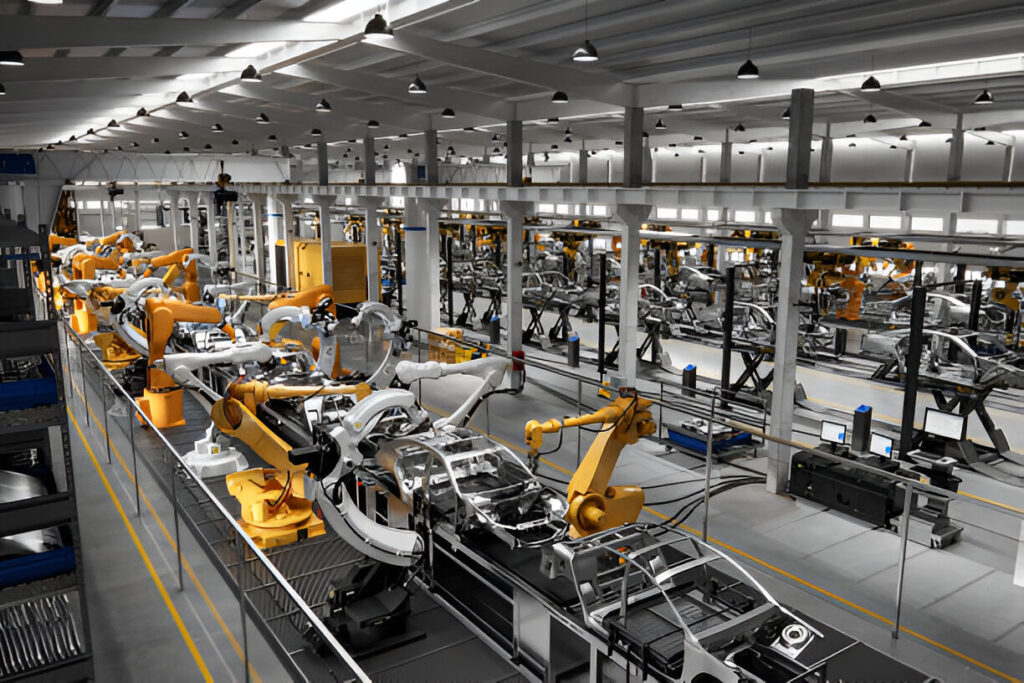
What are the Future Challenges in Plastic Injection Molding ?
Sink marks occur when the wall thickness at the sink is greater than the surrounding walls. After molding, the thicker plastic shrinks more, leaving a dent. These marks are not desirable on plastic parts that need a smooth appearance. Fortunately, sink marks can be predicted and avoided by designing the parts properly.
1. Quality Control and Consistency
- Challenge: Maintaining consistent product quality is crucial in life sciences due to stringent regulatory requirements. Variations in temperature, pressure, and material properties can affect the final product.
- Solution: Implementing rigorous quality control processes, such as Statistical Process Control (SPC), automated inspection systems, and regular calibration of machinery, can help maintain consistency. Firstly, these methods ensure precise monitoring of production. Moreover, automated systems reduce the potential for human error. Additionally, regular calibration further guarantees accurate measurements. Consequently, we minimize variations in product quality. Therefore, we improve overall efficiency. Ultimately, these practices contribute to higher standards and better outcomes.
2. Material Selection and Handling of Applications in Automotive Industry
- Challenge: Selecting and handling the right materials is vital, as different materials have unique properties and behaviors during the molding process. Contamination must be avoided.
- Solution: Working with material experts to choose appropriate materials and implementing cleanroom manufacturing environments can mitigate risks. Proper storage and handling procedures are crucial.
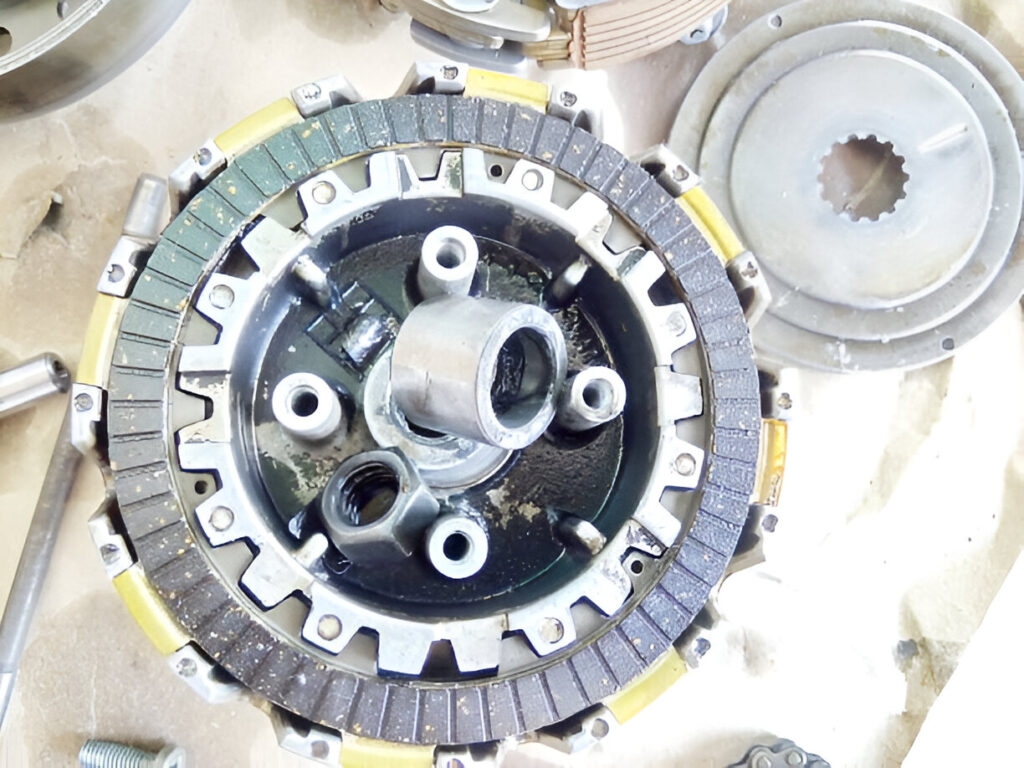
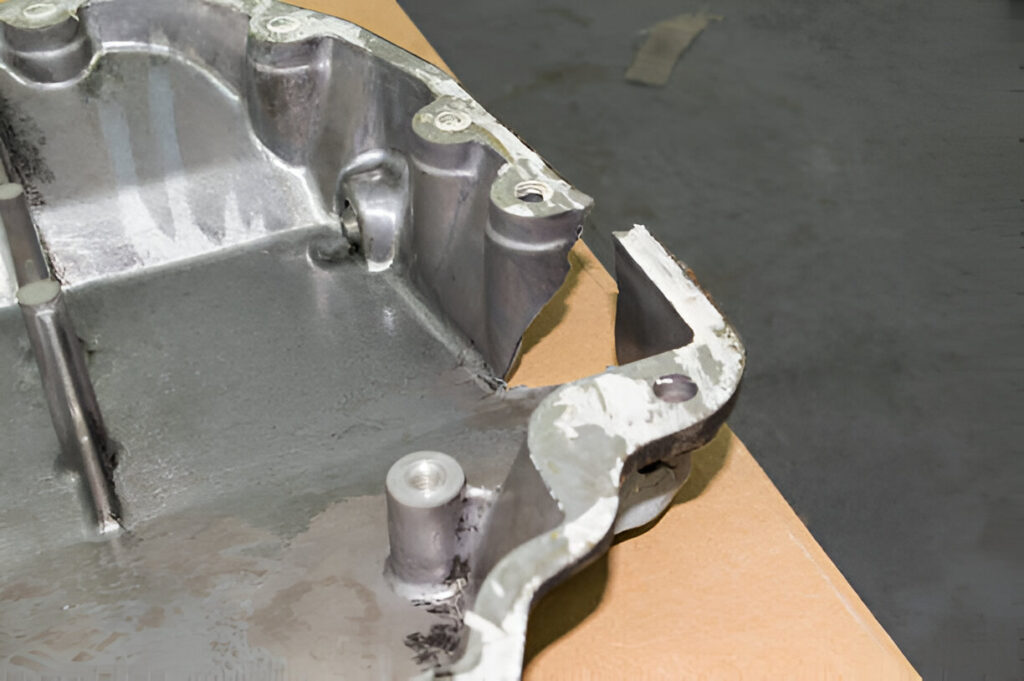
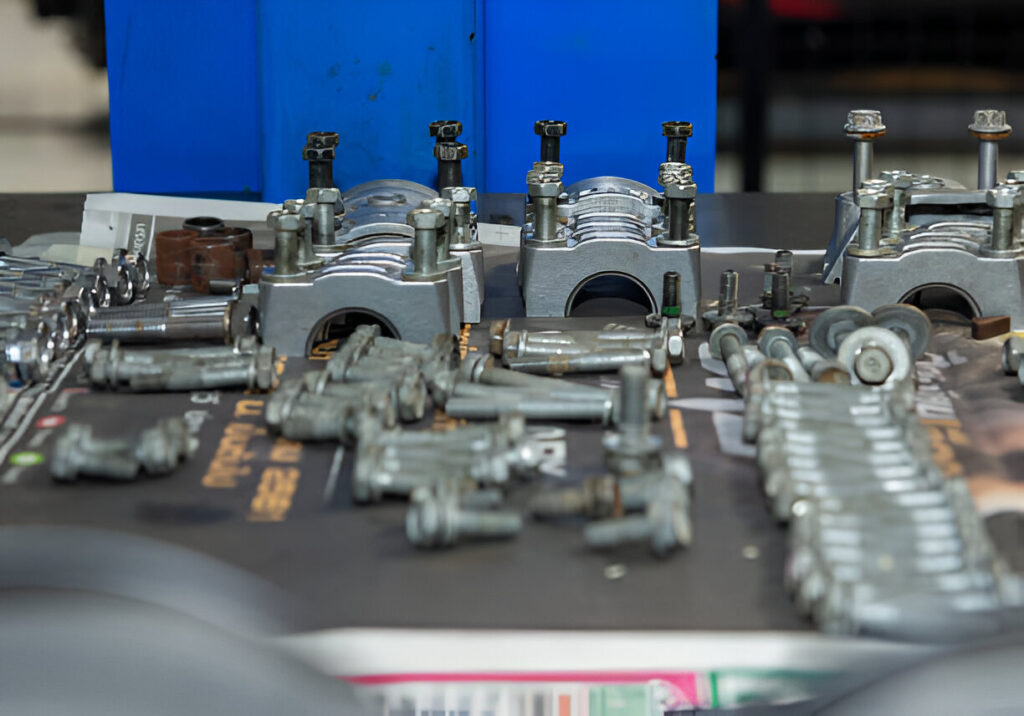
3. Supply Chain Management
- Challenge: Ensuring a reliable supply of raw materials and components is essential. Supply chain disruptions can impact production schedules.
- Solution: Developing strong relationships with suppliers, diversifying supply sources, and maintaining adequate inventory levels can reduce the risk of disruptions. Implementing supply chain risk management strategies is also beneficial.
4. Cost Management
Challenge: Controlling production costs while maintaining quality and compliance can be challenging, especially when scaling up.
Solution: Utilizing cost-effective materials, optimizing production processes, and adopting automation can help manage costs. Conducting regular cost-benefit analyses can identify areas for savings.
Conclusion
Applications in Automotive Industry is expanding its technologies and providing its services in a wide range of different industries. Their applications cover a wide range of automotive components, from interior parts to functional elements. If we look at the 90s, technology has become quite advanced in today’s life and the capacities are huge. Which includes capacity, size of the product, Durability, High tensile strength etc.
The future of plastic injection molding in construction is not just about continuing what we’ve been doing, but about revolutionizing how we build. With the integration of new materials, smarter technologies, and sustainable practices, plastic injection molding will play a crucial role in the construction industry’s future. Furthermore, it will drive innovation and enhance the efficiency of construction processes.
This industry’s successful growth depends on the government’s initiatives, the industry’s ability to adapt to the latest technologies, and the industry’s collaboration of national and international firms working together. As automation, new materials, sustainable practices, digitalization, and Industry 4.0 change the industry, manufacturers need to keep up.
Doing so will help them improve manufacturing quality, lower costs, and strengthen their competitive edge in this fast-changing market. Firstly, this approach enhances efficiency, thus boosting overall performance. Additionally, it allows for more effective resource management. Consequently, operational expenses are reduced. Moreover, by adopting these practices, the company can stay ahead of market trends. Ultimately, this leads to increased profitability and growth. Therefore, the business will be well-positioned for long-term success.
0 Comments
Trackbacks/Pingbacks