Components of an Injection molding is a specific manufacturer method used to produce plastic parts. It is made by molten plastic material in Mold. The Mold plays an important role in this process because it defines the final shape and structure of the product.
If you want to understand injection molding firstly you have to understand about the different components of the Mold. This article provides an overview about the injection Mold, their function, and their role in the production.
1. Mold Base
The Mold base is most important part of the injection molding. It is the most necessary support for other components, its ensure that Mold works smoothly and perfect. The Mold base has two main halves: first one is the stationary half (also known as the fixed half) and the second one is the moving half (also called the ejector half). These two halves are used to injected molten plastic and take a perfect shape.
2. Cavity and core
The parts of Mold that give plastic its shape are the cavity and core. The hollow space where the molten plastic is injected is called the cavity, while the internal features of a part are formed by a core. Both types form outside and inside surfaces of any final object.
Functions:
- Shaping the Part: The cavity together with the core provides a final shape and size for it.
- Material Flow: How molten plastic flows in a Mold is affected by to how cavity or core has been designed, this affects quality and consistency of finished components.
- Ejection: The part’s removal from the Mold after solidification may be facilitated by use of cores as they assist in ejection process sometimes.
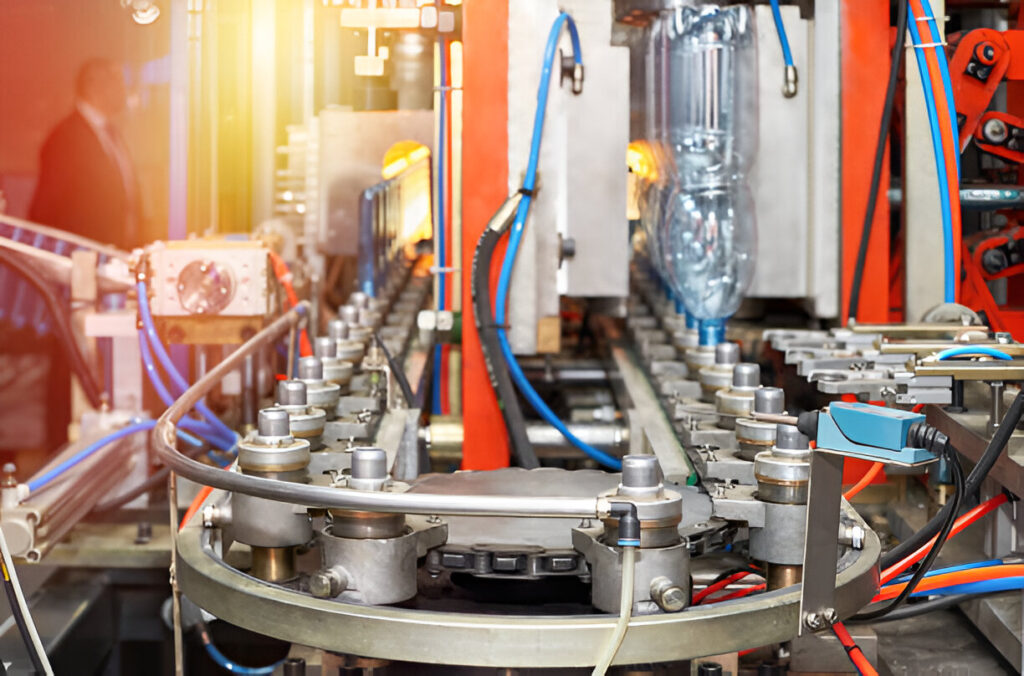
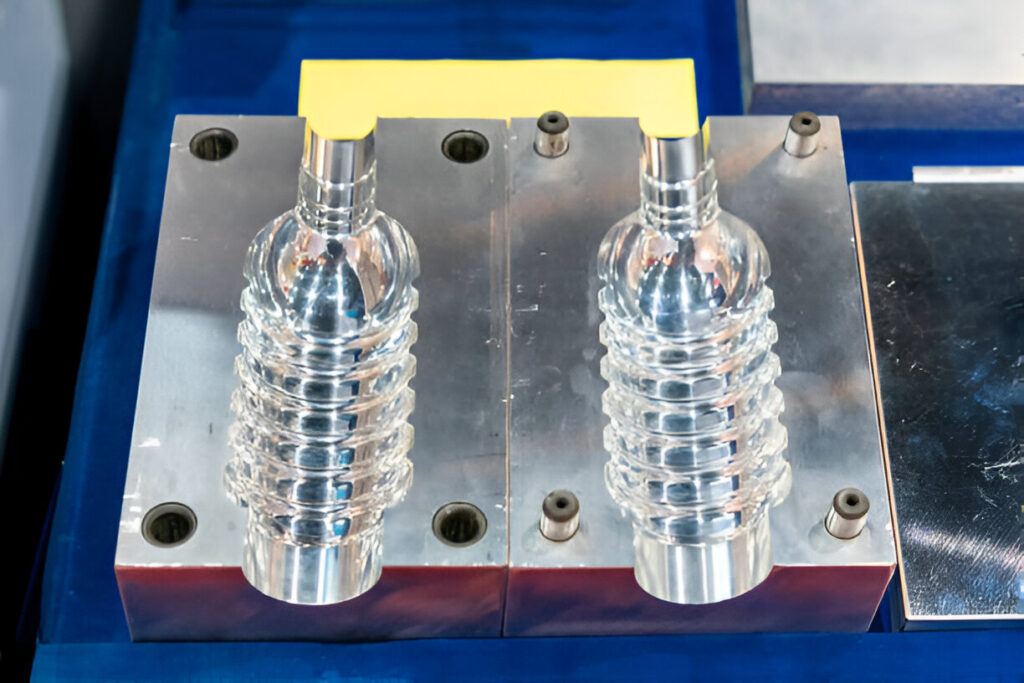
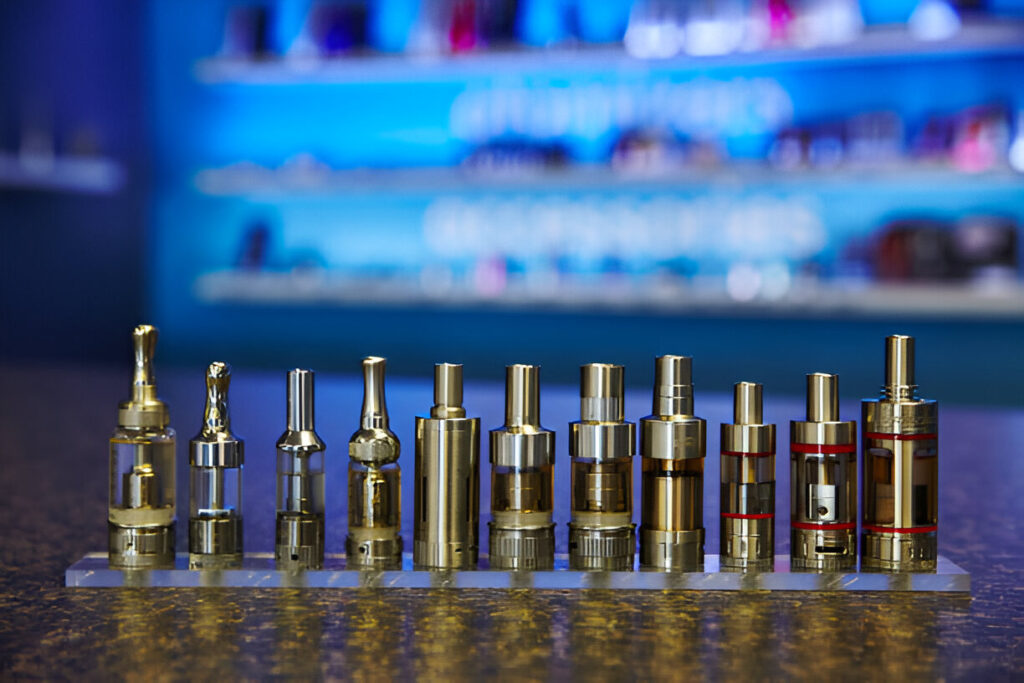
3. Understanding the Components of an Injection Mold: Runner System
In injection molding, the runner is a pathway that guides the molten plastic from the machine’s nozzle into the mold’s cavities. This runner system consists of several parts, including the sprue, runners, and gates, which work in unison to ensure the plastic flows smoothly into the cavities.
Here are Few Points on Components of an Injection Mold
- Cold Runners: Cold runner systems consist of simple, unheated channels that transport the molten plastic to the cavities. After the plastic has solidified, the runners must be manually removed from the part, leading to some material waste.
- Hot Runners: Hot runner systems use heated channels to keep the plastic in a molten state as it flows to the cavities. This eliminates the need for runner removal and reduces material waste.
4. Ejection System
In injection molding, the ejection system consists of ejector pins, which are located on the ejector plate. These pins are used to push the part out of the mold cavity once it has been formed and has been cooled. After the solidification of a molded part, the ejection is done by the ejection system. Mostly made up of ejector pins, ejector plates or sometimes air valves and other devices that help in removal from Mold.
5. Cooling System
The purpose of plastic injection Mold cooling is to offer heat management throughout the injection molding process. When the hot plastic melt enters the Mold chamber, it cools and solidifies due to heat dissipation via the cooling system.
To remove waste heat from an injection molding system, cooling should ideally use either air or liquid. As a result, the system may produce injection Mold items that are flawlessly shaped. For it to execute this purpose there are several components required in this injection molding cooling system.
6. Ventilation System
The ventilation system is very important in plastic injection molding because the final product must be of high quality. Ventilation system reduce time cycle due to its too much pressure. It helps to reduce machine Mold life and making them life longer. It is important to check regularly maintenance and ventilation system it necessary to keep the process is running smoothly.
7. Clamping System
The clamping system is used to keep the mold shut when the melted plastic is pushed into the closed mold. The main types of clamping system include toggle clamping system and direct hydraulic clamping system. The toggle clamping system is the traditional system for standard IMMs.
8. Mold Inserts
Insert molding is an injection molding process that involves adding inserts, particularly metal, into an injection-molded part. Placing the insert within the Mold cavity occurs before molten plastic injection. Consequently, on cooling, the insert becomes a permanent plastic part.
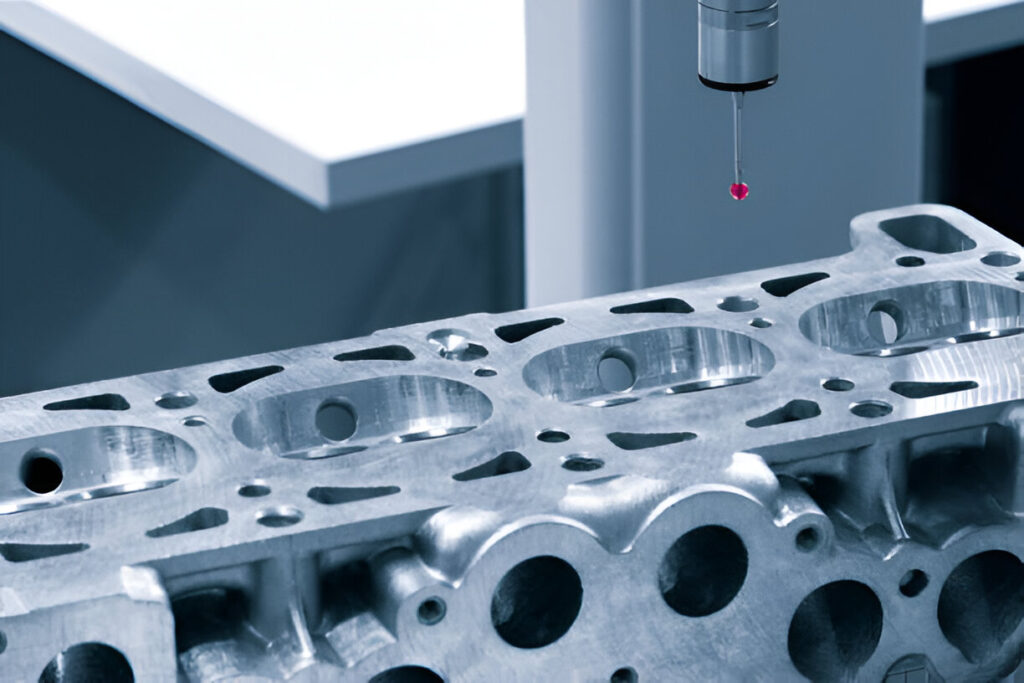
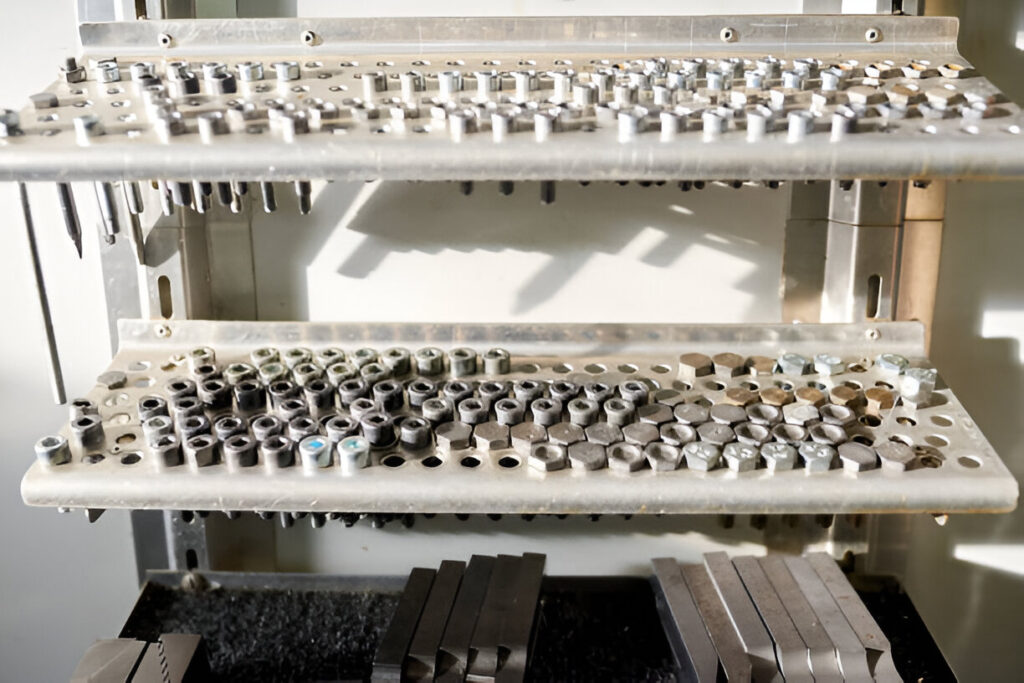
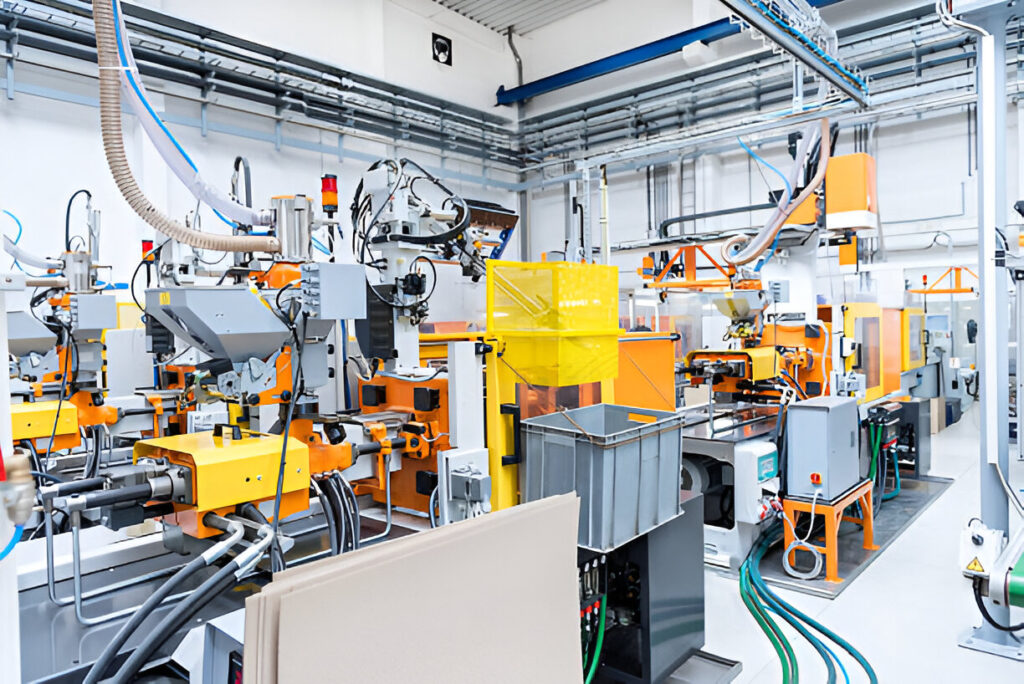
9. Guide Pins and Bushings
Guide pin is also known as the alignment and locating pin. It is a cylindrical component and use for aligned and positioning the Mold halves in molding machine.
They are typically installed on one Mold half, commonly the moving half or “B-side,” and fit into corresponding guide bushings on the Mold’s stationary half or “A-side.” The guide pin ensures accurate alignment during the mold closing and opening cycles.
10. Core and Cavity Inserts
Cavity and core are used in the injection molding process, where the concave part of the Mold is the cavity and the convex part is the core. The cavity and core are used in pairs. Firstly, the cavity is often referred to as the female mold, whereas the core is known as the male mold.
Moreover, these two mold components function together during the molding process. In fact, they are the most important parts of a mold. Consequently, without them, the mold would not perform correctly. Lastly, understanding their role is essential in the field of injection molding.
11. Hot Runner System
Comparison diagram of cold runner injection Mold and hot runner injection mild illustrating the cold runner, hot runner, cavity, runner, and finished part.
A hot runner system, specifically used in the injection molding process, is an internally heated system that is added to a plastic injection mold in order to mold single parts or multiple parts simultaneously. Additionally, hot runners eliminate the cold sprue or cold runner mold, allowing the molten plastic to be injected directly into the part cavity while the plastic injection molding process is ongoing.
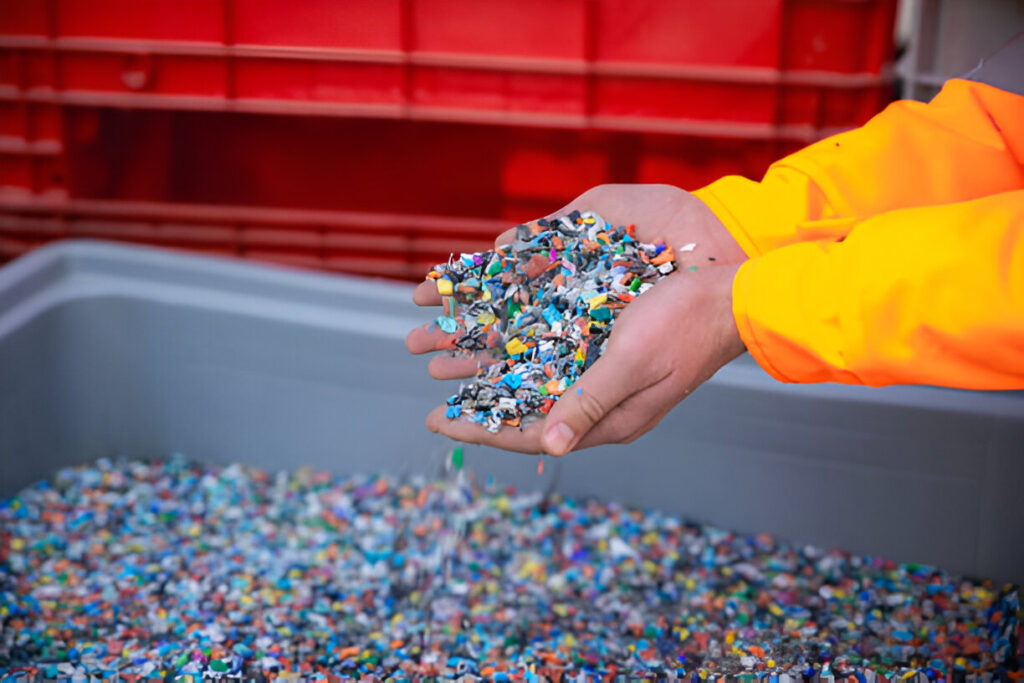
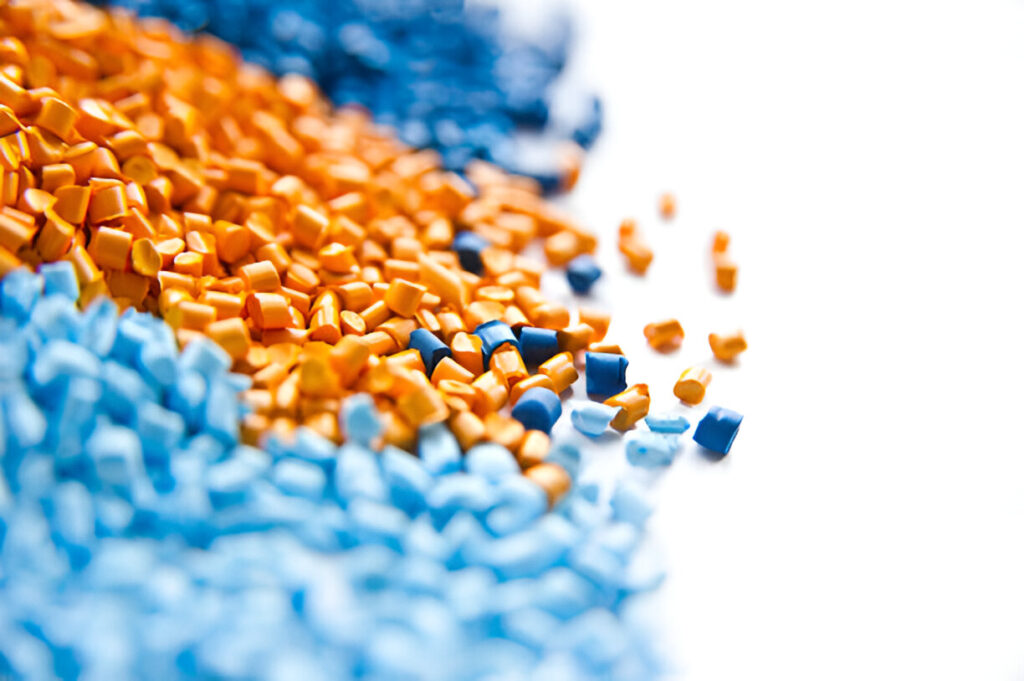
Conclusion
Components of an Injection Mold, we all know that injection molding is popular manufacturer way to make plastic parts. Mold is very important for manufacturing and it play a very critical role. The component of mold is mold base, cavity and core, runner system, ejection system, cooling system, ventilation system, clamping system, mold insert, guide pins and bushing, core and cavity insert, hot runner system. These components have their own property and all these component play important role.
0 Comments
Trackbacks/Pingbacks