In today’s industrial world, the storage, transportation, and organization of material are more important than ever. And one such product that serves the requirements of multiple industries right from agriculture to manufacturing is a pallet bin. These bulk containers are responsible for in-house storage as well as end-to-end logistics. Over the years, with the development of manufacturing processes particularly plastic injection mold technology, the production of a pallet bin has become faster, economical and highly customizable.
In this article we will be discussing about everything you need to know about Pallet Bin– How does it work? Where all it can be applied? Design guidelines while creating injection molds for them and finally towards the end market trends related to businesses using these.
If you’re a plastic bin manufacturer or a warehouse manager or just have an inclination towards Industrial Storage Solution then this piece will definitely help you gather great insights.
What is a Pallet Bins?
A pallet bin or bulk bin or plastic pallet container is a portable, rigid and reusable industrial storage and transport container used to handle heavy or bulky raw materials and finished components. Pallet bins are designed with a view to ensure proper space utilization of return trucks that return without carrying any loads. A pallet bin typically has a load-holding base so forks can lift it from all four directions using forklift trucks (or electric stacker or hand-guided truck) and conveyance it in trains etc.
Pallet Bins as an industry segment grew out of modern supply chain needs of use of gloves by human workers while handling raw components possible only if supplied in large quantities at one go (so it’s not over after every few hours resulting in loss in production) automated lines needing uninterrupted supplies requiring storage requirements, better availability and competitiveness necessitating larger imports, needing lesser number of people for doing same work requiring handling more quantity each time etc.
Unlike regular storage containers, pallet bins are made to be used in an industrial environment. This means that they have heavy duty walls, bases and lids if necessary. They are also made to withstand the elements when used for outdoor storage or shipping. Some are even designed to nest inside one another when empty so that you can save space.
Key Features of Pallet Bins:
Integrated Pallet Base: Built in pallet base for safe and easy lifting, moving and stacking with material handling equipment. Many pallet bins have a high load capacity, often holding hundreds of kilograms or liters of product, making them ideal for heavy-duty use. Pallet bins are designed to be stacked vertically, whether they are full or empty in order to maximize warehouse space and minimize transport costs.
- Collapsibility (Optional): Some variant of plastic pallet bins come with collapsible walls that can be folded down when the bin will not be in use, thus saving on space occupied during return shipping.
- Durable Plastic Construction: Most of the pallet bins are made making use of plastic injection mold technology which makes the bins last-long, high-strength, precision &, highly wear-resistant.
- Customization Options: Bins can be customized to include your company logo, color coding, RFID tracking slots, or food-grade finish.
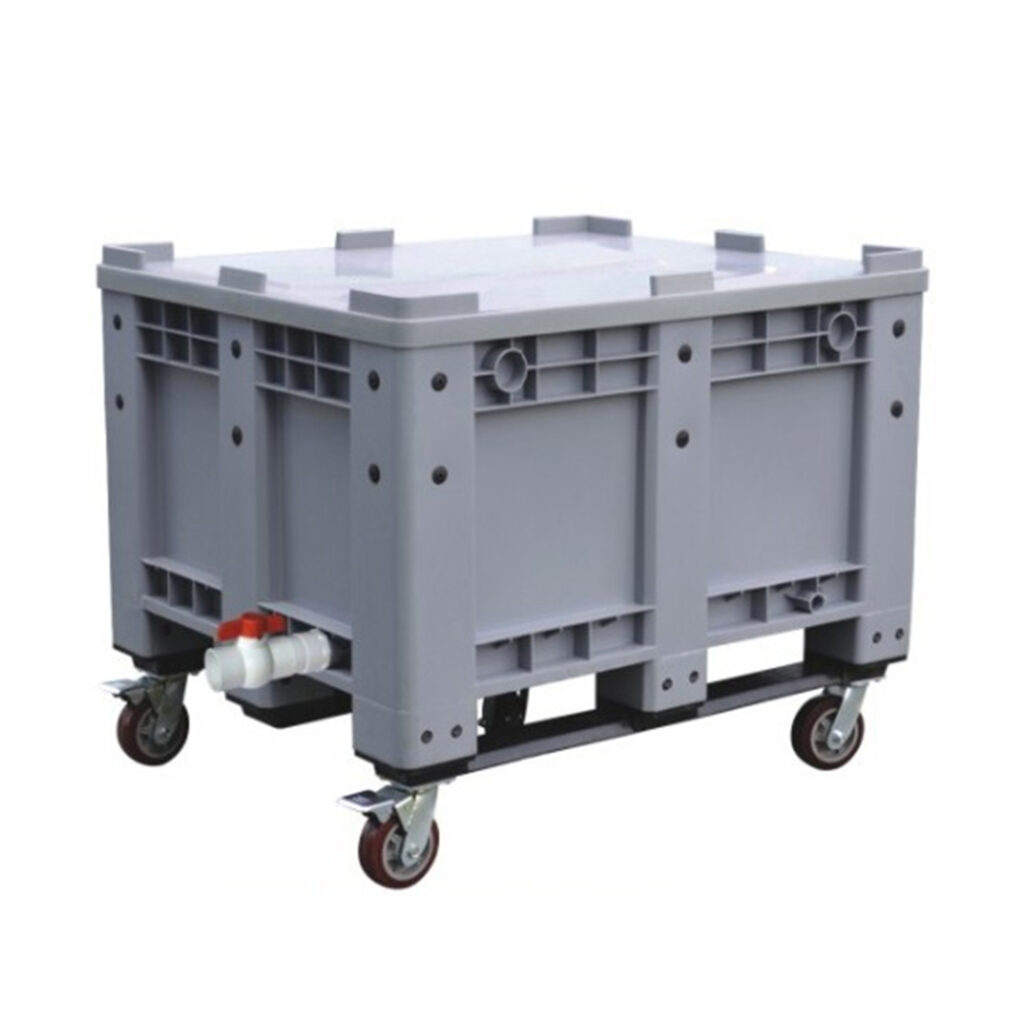
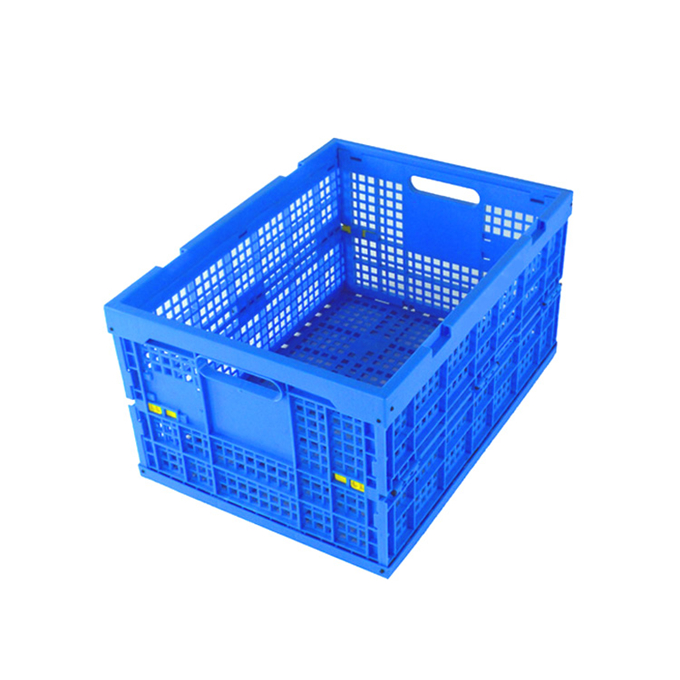
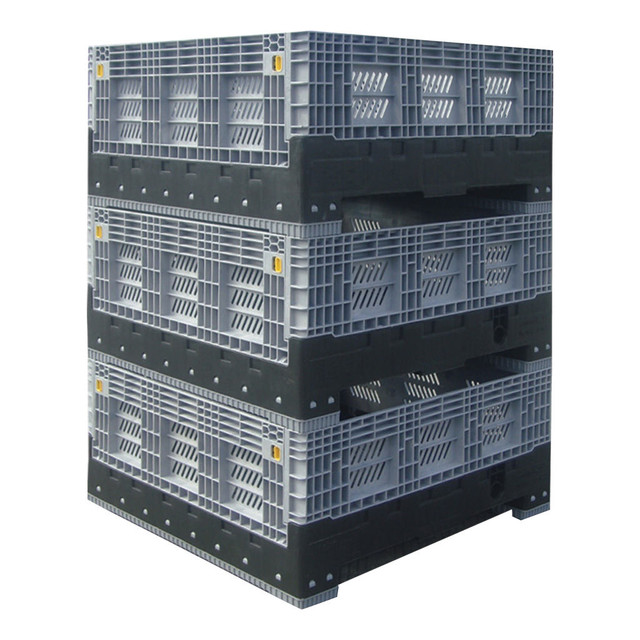
Applications of Pallet Bin Products
The pallet bin products are high performance designed to suit multiple industries. The plastic storage solutions are advantageous as they are strong, hygienic, stack-able and stress environment resistant among other forms of utilities. Below we will take a detailed look at where and how pallet bins are commonly used.
1. Agriculture & Horticulture
Vented and solid plastic pallet bins are a necessity in the agricultural industry to help with the handling, storage and transport of fresh produce.
Applications include:
- Harvesting and bulk transport of fruits like apples, oranges and mangoes
- Temporary storage of vegetables like potatoes, onions and carrots
- Grain storage and transfer between fields and mills.
- Sorting, washing, and cooling bins in post-harvest processing.
Why Pallet Bins?
The Pallet Bin’s ventilation holes promote controllable airflow, helping keep fresh produce fresh for longer. Plastic surfaces are easy to clean, reducing the risk of carrying and spreading pests compared with the porous structure and rough surface of wood.
2. Retail, Logistics, and Distribution
Retailers and warehouse operators use pallet bins extensively for bulk product handling, inventory management, and cross-docking operations.
Key uses:
- Storage and sorting of non-perishable stock in warehouses
- Safe movement of goods in distribution centers
- Transport of items between stores and storage hubs
Benefits of Pallet Bins:
- Uniform design makes it easy to stack and it is automatic friendly
- Barcode or RFID tag can be inserted for inventory tracking
- Stackable and collapsible, saves storage space.
3. Automotive and Engineering Components of Pallet Bins
In the automotive industry, workers use large and rugged plastic pallet bins to transport and store heavy components such as engine blocks, bearings, and body panels.
Use cases:
- Use cases include transporting engine parts between manufacturing units.
- Storing high-value components on assembly lines
- Safe handling of lubricated or oily machine part
Advantages:
- The reinforced bottom and corners can take a lot of weight
- Plastic bins resist oils, greases and solvents.
- Durable construction reduces damage to costly components
- Food and Beverage Industry
Manufacturing Process of Pallet Bins Using Plastic Injection Mold
Manufacturing pallet bins by plastic injection mold process. Plastic injection mold is the most common and widely used manufacturing process for the production of pallet bin. Manufacturers use this advanced manufacturing process to produce lightweight, durable, and high-quality pallet bins at a large volume with consistent dimensions and strength.
Here is a detailed, step-by-step explanation of how manufacturers actually produce pallet bins using the plastic injection molding technique:
Step 1: Product Designing and Development
Prior to actual production, engineers and designers make a specific 3D CAD (Computer-Aided Design) model of the pallet bin. The mold design has especially to contain:
- Bin dimensions: length, width, height and wall thickness.
- Structural reinforcement: So that it does not get warped/break when heavy objects are placed on top of it.
- Draft angles: We add draft angles wherever possible on the model to make it easier to eject out of the mold.
Challenges & Solutions in Mold Design
✅ Challenge: Molds can be costly to produce, especially for custom designs.
✅ Solution: Manufacturers often use modular mold systems that allow interchangeable parts to modify bin designs without building an entirely new mold.
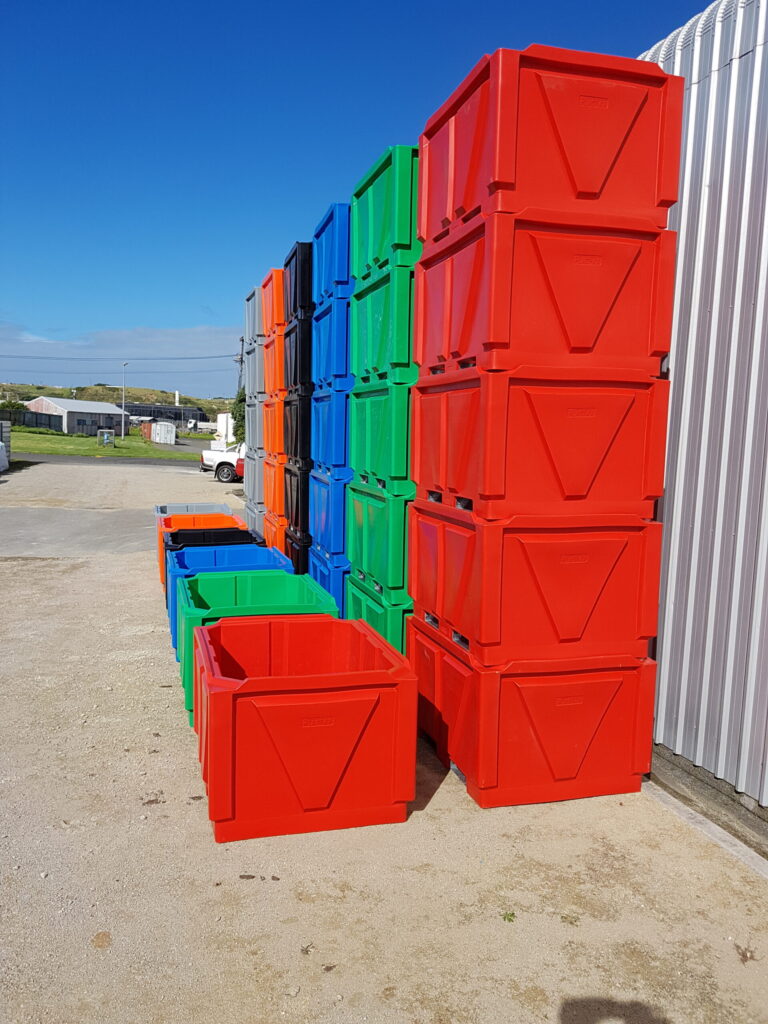
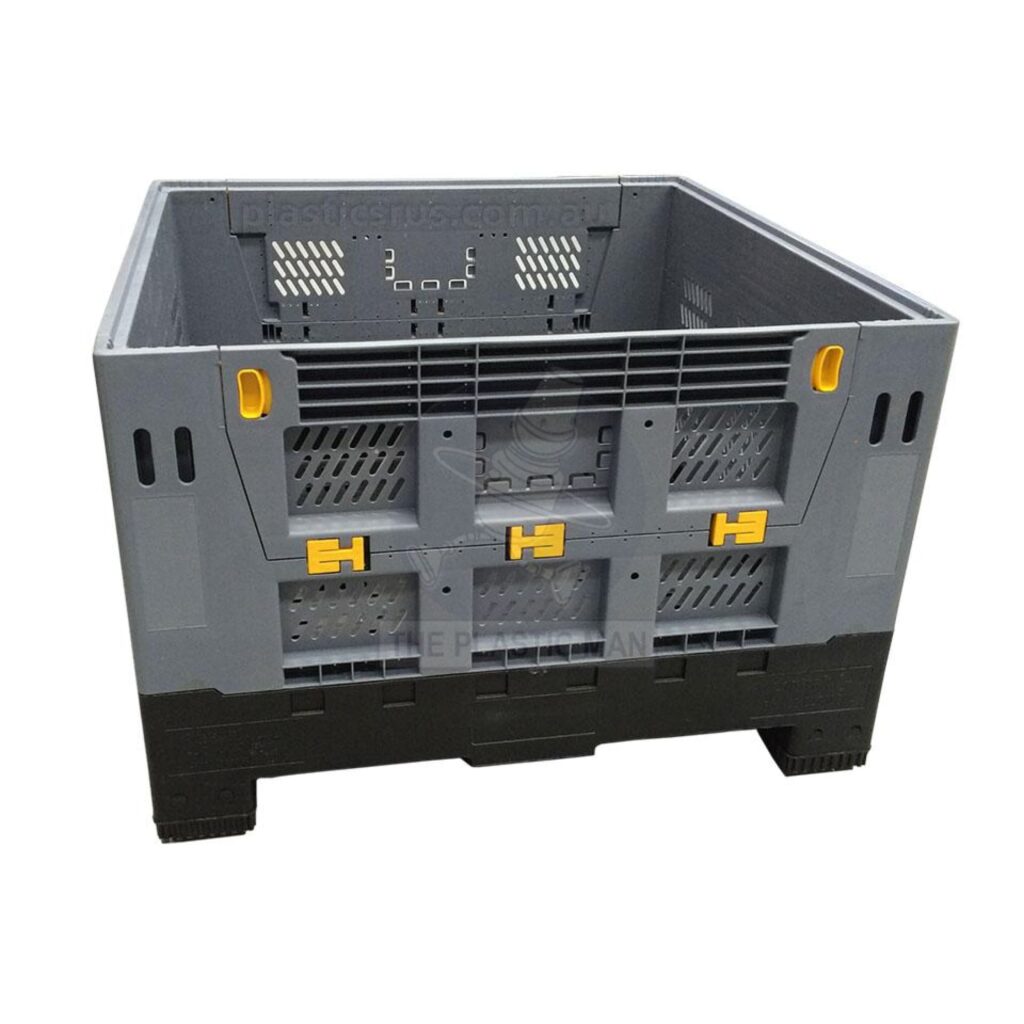
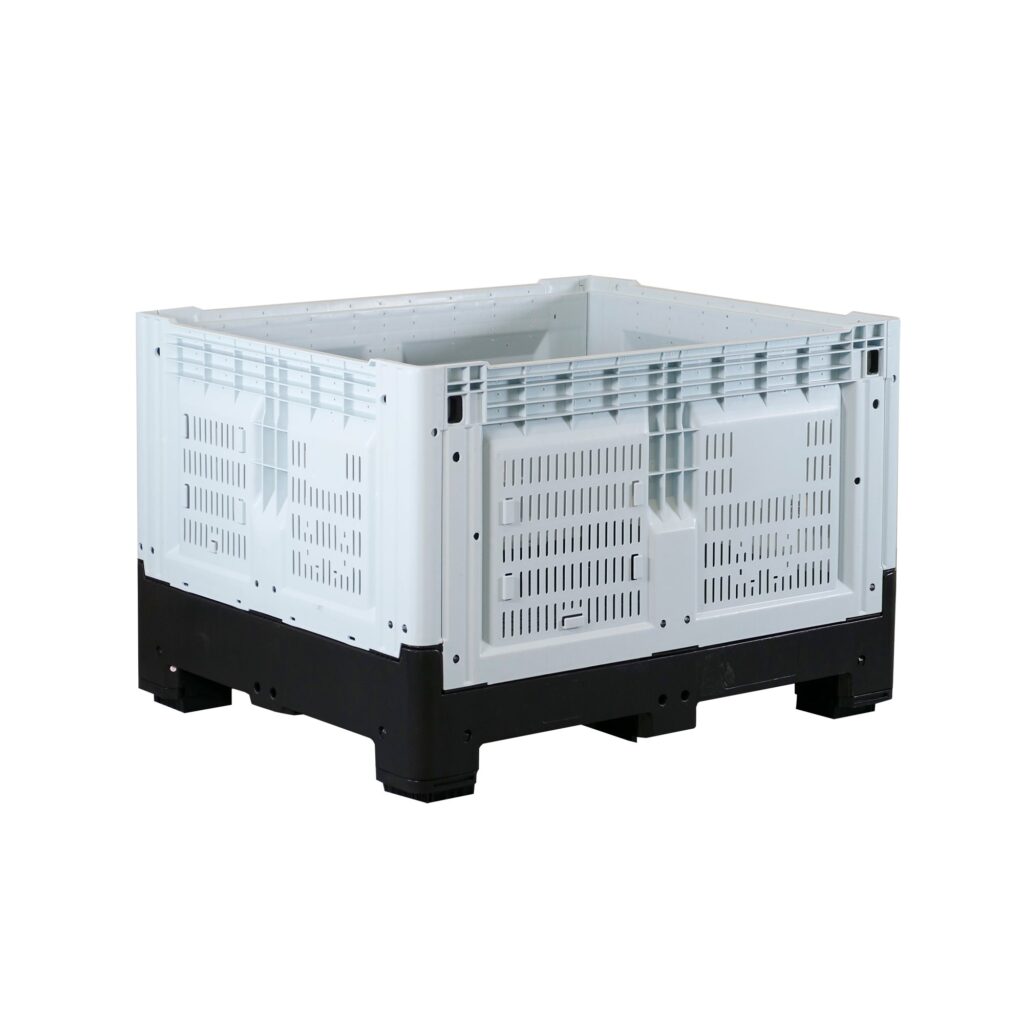
Step 2: Selecting the Right Plastic Material
The plastic resin that you choose will impact the durability, flexibility, and resistance of your final pallet bin. Some commonly used materials are:
- High-Density Polyethylene (HDPE): Impact resistant, UV stable and ideal for outdoor use.
- Polypropylene (PP): Lightweight, chemical resistant and commonly used in food & beverage industries.
- Recycled Plastics: More sustainable and cost-effective for industries focusing on eco-friendly solutions.
Additives & Enhancements: Manufacturers may mix in:
- UV stabilizers (for outdoor storage bins)
- Antimicrobial coatings (for food & medical use)
- Chemical areas (above or below deck)
Challenges & Solutions in Material Selection
✅ Challenge: Finding a balance between cost, durability, and sustainability.
✅ Solution: Many manufacturers now use blended recycled and virgin plastics for optimal performance and reduced environmental impact.
Step 3: Material Preparation & Melting
After the plastic resin is selected, it is provided to the injection molding machine. Material goes through following steps:
- Drying: To ensure that no moisture remains in the plastic granules.
- Color Mixing: If color pigments need to be added.
- Feeding into the Injection Barrel: The plastic granules are fed into the heated barrel through a hopper.
The high temperature (up to 200°C-300°C) of the barrel, melt the plastic and turn it in liquid. Then, with the help of a screw-type plunger, this liquid is injected into a desired mold cavity for getting the required shape.
Challenges & Solutions in Melting
✅ Challenge: Overheating can cause degradation and affect the mechanical properties of the polymer.
✅ Solution: Advanced temperature monitoring system and automatic material feeder controls heat.
Conclusion
The combination of pallet bins and plastic injection mold technology have revolutionized industries which required bulk storage, material transport or distribution as well as the simple management of inventory. In the past, people used heavier materials like wood and metal for this function, but these materials gradually deteriorated over time when exposed to different environmental conditions during shipping by land or sea.
From food processing to automotive industry, agriculture to pharmaceutical industry etc., plastic bins have repeatedly proven their worth in improving efficiency in material handling and in managing waste due to reduced product damages. Its ability to stack vertically and horizontally when empty, ease of sanitizing bins containing freshly harvested crops, availability of add-on features for use within larger systems or automated assembly lines, and customization options make it a preferred choice for businesses of all sizes—from small setups to multinational corporations—helping keep costs low.
The reason plastic injection molds are used in the manufacture of pallet bins is because no other method offers the same level of consistency, structural integrity and design freedom. Manufacturers can switch easily between different bin designs, produce large volumes, and add special features such as reinforced bases, vented walls, foldability and RFID tracking.
In essence, pallet bin is the result of a perfect union between engineering, material science, and functionality. Whether you’re after efficient storage, hygienic standards compliance, sustainability goals or materials handling productivity we have you covered with this production technology. The companies that purchase injection mold designed and manufactured pallet bins are ahead of the game in driving cost effective results for their operations through waste reduction and productivity increase.
0 Comments