In the high-stakes arena of product development, time is everything. There’s no longer the luxury of waiting months to turn an idea into a physical part. That’s where rapid prototyping comes in. Whether you’re developing parts for aerospace applications, automotive components or medical devices even simple consumer goods rapid prototyping allows you to test, refine and perfect your designs faster than any other method of manufacturing.
Rapid prototyping encompasses a variety of manufacturing techniques designed to produce physical samples and models quickly, usually within only a few hours of the designer’s initial conceptualization. Typically, 3D computer aided design (CAD) data are used for this purpose. Such parts may be prototypes or may be the end use production components themselves. Rapid prototyping is also called solid free-form manufacturing,3D CAD manufacturing, and layered manufacturing.
1. History and Evolution of Rapid Prototyping
The concept of rapid prototyping emerged in the 1980s with the introduction of stereolithography (SLA), the first 3D printing technology. Since then, rapid prototyping has evolved significantly:
But what exactly is rapid prototyping? How does it fit into modern production strategies like injection molding and plastic injection molding? We’ll answer all those questions in this article by covering the basics on what you need to know about rapid prototyping including its methods, advantages and applications as well how it plays with large-scale production via injection molding specifically.
1990s: Expansion of Techniques and Materials
In the 1990s there was an explosion of growth in part because of the number of new prototyping technologies that became popular. Some new prototyping processes and technologies that were developed and widely used are shown below.
- Selective Laser Sintering (SLS): Invented by Carl Deckard, it used a laser to fuse powdered materials (like nylon), allowing for stronger and more functional parts to be 3D printed.
- Fused Deposition Modeling (FDM): Patented by Scott Crump, this technique works by melting and extruding thermoplastic filaments layer by layer. It’s one of the most commonly used forms of 3D printing due to its low cost and versatility.
Entry Into Mainstream Use: Early 2000s
In early 2000s, it transitioned from being an industrial hype to a technology that became accessible to everyone as open-source software, low-cost 3D printers and easy to use CAD tools made it possible for even small start-ups, schools or individuals to experiment with rapid prototyping.
At the same time, researchers were also investigating the use of rapid tooling-where prototype molds are used for short-run injection molding-for developing “bridge” solutions that would enable manufacturers to produce small numbers of final-material parts necessary for pilot-testing and investment-casting trials.
2010s: Democratization and Software Revolution
- The 2010s ushered in a new era of democratization and digital integration:
- Desktop 3D printers flooded the market. MakerBot, Prusa and other brands led the way.
- Cloud based CAD platforms like on shape, Fusion 360 made real time collaboration and simulation a reality.
Today: Rapid Prototyping as a Standard Practice
Rapid prototyping isn’t just something that’s good to know it’s a necessity for product development. Every modern product, from those made by large multinational corporations to boutique design shops, goes through some form of rapid prototyping before it hits the shelves.
More advanced processes such as Multi Jet Fusion (MJF), Direct Metal Laser Sintering (DMLS) and Continuous Liquid Interface Production (CLIP) have appeared offering prototype parts made with production grade strength, accuracy and surface finishes. In addition to above plastic injection moulding has come on board with rapid prototyping via low volume / fast turnaround tooling allowing test of injection molded parts within days.
2. How Does Rapid Prototyping Work?
Rapid prototyping is a well-defined and very iterative process used to physically produce, within hours or days, scale models or functional prototypes of design concepts. It uses computers and computer-controlled machine-tools that work from digital data to fabricate featured physical objects by building them up, a layer at a time. The earliest rapid prototypes were produced using mostly stereolithography apparatus (SLA) machines. Today most are manufactured under direct control by the computer using computer numerically controlled machines (CNC).
Here’s a deeper look into each step of the rapid prototyping workflow:
1. Idea Generation and Concept Sketching
Every product begins with a concept. In this phase, designers brainstorm product ideas, features, shape, and who the target customers will be. It can be done by hand sketches or digital drawings. The purpose is to visualize and finalize the overall design direction before moving into any digital modeling.
2. 3D CAD Modeling
The first step is turning your concept sketches into a digital 3D model. You’ll use computer-aided design (CAD) software like SolidWorks, Fusion 360, or AutoCAD to create this. In our case, CAD models are the digital blueprints of rapid prototypes from which we work. Every dimension, surface, and feature of the part you want to produce is defined in these CAD files not discussed as they can be easily edited, duplicated or adjusted based on what you learn from prototyping.
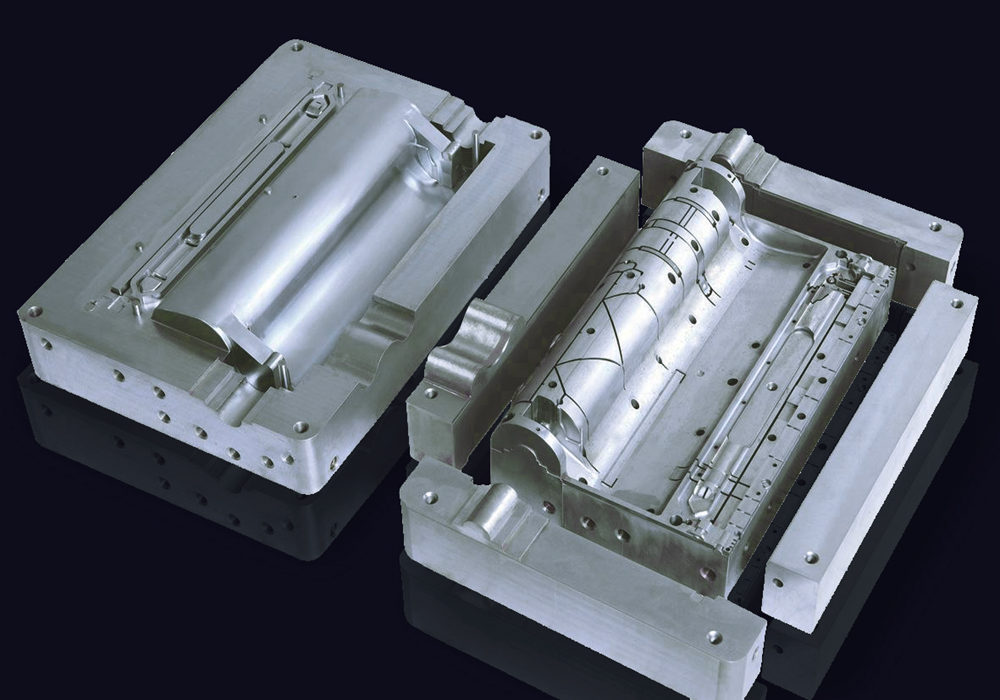
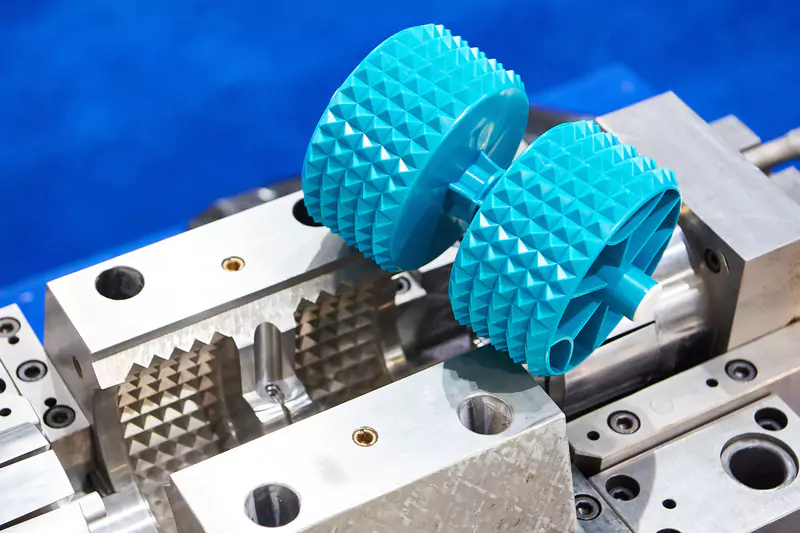
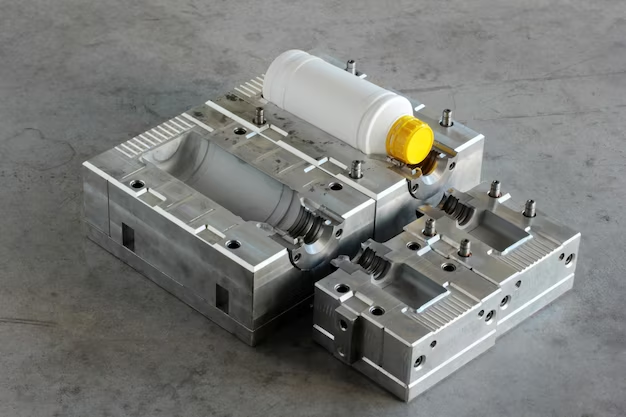
3. Simulation and Analysis (Optional but Recommended)
Some teams prefer to do a virtual design test before physical production using simulation tool for structural, thermal or even mold flow analysis if injection molding is considered in further fabrication. This pre-validation step will save time and cost as we can detect the problem early before fabrication.
4. File Preparation for Prototyping
After the CAD model is fully developed, it needs to be exported into a machine language readable format, most commonly STL (Stereolithography) or OBJ files. These files slice the 3D model in layers, so additive manufacturing systems can recognize the geometry of the final part; if a subtractive method like CNC machining is used, the geometry is translated into G-code that will feed the cutting tools.
3. Common Types of Rapid Prototypes
Different stages of product development require different kinds of prototypes. Understanding the common types of rapid prototypes helps businesses choose the right approach to test form, fit, function, and usability. Here’s an in-depth look at each type:
1. Concept Prototypes
Purpose: Visualizing early ideas and design intent
Description:
Concept prototypes are low-fidelity models that are built to test design concepts in the early stages of product development. They are used to test design direction, help visualize ideas, and communicate with team members or stakeholders. Concept prototypes also help understand overall size, scale, and proportions of a new product design.
Materials:
- Foam
- Cardboard
- Paper
- Basic 3D-printed plastic (e.g., PLA)
Use Case:
An industrial design team might construct a full-scale foam model of a new handheld device to evaluate grip, placement of user interfaces, and overall aesthetics.
Pros:
- Fast and inexpensive
- Useful for brainstorming and design reviews
- Great for when you need feedback from non-tech stakeholders
2. Form and Fit Prototypes
Purpose: To evaluate physical dimensions, assembly, and tolerances
Description:
Form and fit prototypes are closer in look and function to the final product. They are used to test how different parts of a product fit together, if they do go where they are supposed to go and if the product meets defined dimensional and spatial requirements. These prototypes will verify that the shape of a part or an assembly is according to the design functional specification.
Materials:
- ABS, PLA, Nylon (3D printed)
- Resin (SLA)
- Polyurethane (Vacuum casting)
Use Case:
An engineer uses a prototype to check whether the front and back panel of a plastic casing for a new electronic gadget snap together and if the circuit board fits inside.
Benefits:
- Catches early dimensional errors
- Allows for basic mechanical testing
- necessary to iterate on product geometries before you tool
4. Technologies Used in Rapid Prototyping
Rapid prototyping employs a variety of modern technologies that facilitate the quick creation of physical models from virtual designs. Depending on the purpose of the prototype, required material behavior and expected production run, every technology has its own advantages. We will now closely observe the rapid prototyping technologies in use based on certain specificness.
1. 3D Printing (Additive Manufacturing)
3D printing is at the heart of what we call rapid prototyping. Object are formed layer by layer from a 3D digital CAD model. It’s incredibly versatile with the ability to create almost any geometrical feature or shape you can dream up, as well as being able to mould multiple different parts together in a single build. Some of the more popular ways of 3D printing include:
a. Fused Deposition Modeling (FDM)
- One of the most popular and affordable 3D printing methods.
- Works by melting and extruding thermoplastic filament.
- Great for functional parts, rugged prototypes, and more.
- Build sizes range from smaller than a basketball to almost four feet long.
- We print using industrial grade thermoplastics which makes the parts suitable for rigorous testing.
b. Stereolithography (SLA)
- Uses a UV laser to cure liquid resin layer by layer.
- Producing high-detail, smooth surface concept models.
- For the purpose of finely detailed design and visualization appraisals.
- Good for dental models, jewelry and medical devices.
c. Selective Laser Sintering (SLS)
- Uses a laser to fuse powdered materials such as nylon or polyamide.
- Best for functional rapid prototypes of superior quality.
It doesn’t require support structures, which makes it great for internal features of complex parts.
2. CNC Machining
Additive manufacturing and CNC machining are both computer-controlled technologies for creating prototype parts from solid models or CAD (Computer Aided Design) drawings.
Manufacturing is a process whereby digital 3D design data is used to build up a component by depositing successive layers of material. Additive manufacturing takes virtual blueprints from computer aided design (CAD) software, and transforms them into thin, virtual, horizontal cross-sections, until the model is complete. CNC machining, on the other hand, involves subtracting material from solid blocks of plastic or metal. This removal process starts with a block of material and ends with a finished part.
While additive manufacturing builds parts layer by layer, CNC machining is known as a subtractive method that cuts away layers from a solid block of material. Because it actually “removes” any excess materials during prototyping/machining phase of product development, sometimes they say. It’s like “making an elephant out of stone”.
Key Benefits:
- High accuracy and tight tolerances
- Supports wide metal (aluminum, steel, titanium) and plastic ( ABS, POM, nylon) variety
- Ideal for functional testing and engineering prototypes
- CNC-machined prototypes are especially valuable when it comes to dimensional stability, structural performance, or validating a design before making the financial commitment to plastic injection molding for production.
3. Vacuum Casting (Urethane Casting)
Vacuum casting is a rapid prototyping process for the production of small series of functional and high-quality plastic parts. It uses a master model, usually produced by 3D printing or machining, to make a silicone mold. This mold is subsequently filled with polyurethane resin under vacuum, so there are no air bubbles.
Advantages:
- Parts produced are very close to injection molded parts
- Great for functional testing, product demos and limited production runs
- Simulates elastomeric materials and rigid plastics
- Lower cost and faster than tooling for plastic injection molding
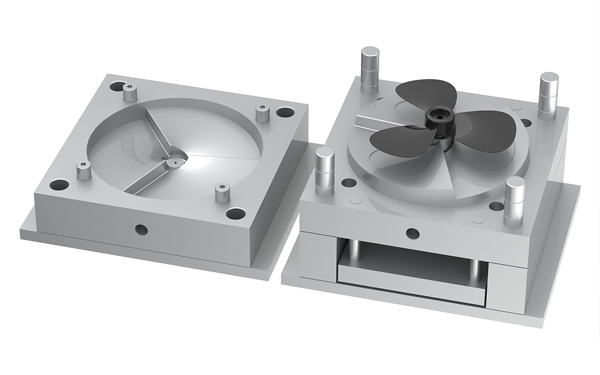
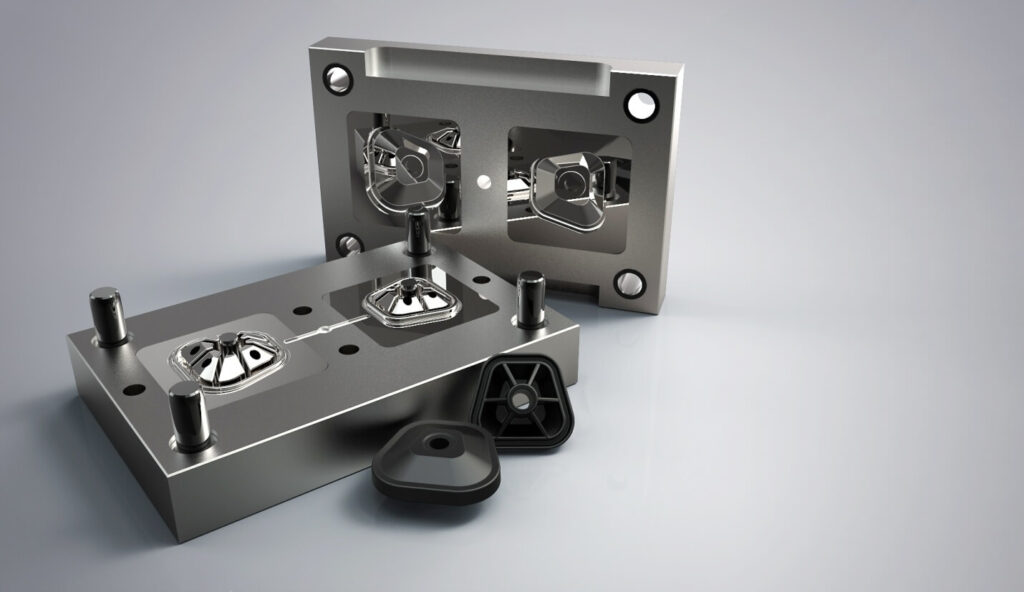
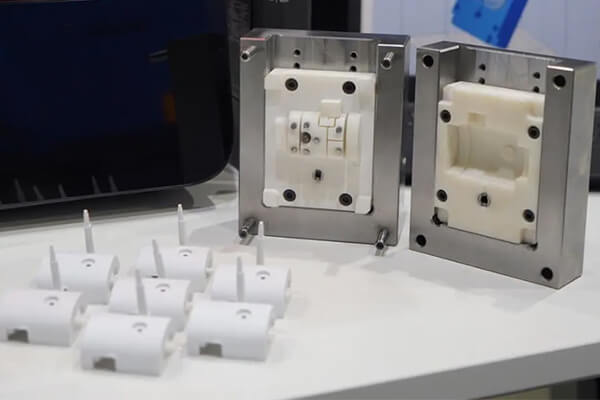
5. Applications of Rapid Prototyping Across Industries
Rapid prototyping is a game-changing technology that has impacted how products are designed, tested, and produced. It helps businesses in different industry verticals innovate fast, cut down product development costs, and be responsive to customer needs. Here’s a detailed overview on the applications of rapid prototypes developed mainly with 3D printing, CNC machining and plastic injection moulding in different sectors.
1. Automotive Industry
The automotive sector has been an early adopter of rapid prototyping technologies and today a rapid prototype is used in every aspect of automobile design and testing, from concept cars to production parts, rapid prototype.
Applications:
- Design Validation: Concept cars and internal parts can be prototyped and tested for fit, aesthetics, ergonomics.
- Functional Testing: Engine mounts, air ducts, intake manifolds and brake housings can all be tested with real-life functional prototypes.
- Customization: Low volume specialty parts and customer specific accessories can be produced in very short lead times.
- Bridge Production: Temporary injection molding tools create thousands of plastic parts for testing before full-scale production begins.
- Benefit: Reduces the time from concept to prototype from months to days, speeding up development cycles and innovation.
2. Consumer Electronics
Speed is of the essence in the consumer electronics market, where companies must launch new products ahead of competitors and before technologies become obsolete. Rapid prototyping (RP) is helping many consumer electronics manufacturers meet product development challenges.
Applications:
- Prototyping Product Housings: Plastic cases for smartphones, wearables, and remotes are typically prototyped with FDM or SLA before injecting the plastics for mass production.
- User Interface Testing: Buttons, screens, ports, and input/output configurations are tested using working rapid prototypes.
- Ergonomics and Design: Developers do test on various form factors and grips especially with handheld or wearables.
- Thermal and Structural Testing: High-performance plastic rapid prototypes were used to test thermal and structural capabilities.
- Benefit: Enables faster iteration cycles, better usability testing, less risk of expensive recalls.
3. Healthcare and Medical Devices
Healthcare industry demands high accuracy, patient-specific solutions, and compliance to stringent safety norms. Rapid Prototyping helps healthcare professionals and medical device manufacturer. Hankie with fast development and testing of solutions having their intended real-life performance.
Applications:
- Custom Prosthetics and Orthotics: Where patient specific anatomical data is used for the production of personalized limbs, braces or implants.
- Surgical Planning Models: CT or MRI scans are converted into 3D models to allow surgeons to plan complex surgeries.
- Device Enclosures: Defibrillators, monitors, diagnostic equipment and ventilators typically go through multiple revisions of housings that are prototyped and then finally mass manufactured using plastic injection molding.
- Biocompatible Rapid Prototypes: FDA approved materials are now available to prototype implants and test them safe.
- Benefit: Improved patient outcomes, faster development, lower time to regulatory approval.
4. Aerospace and Defense
In an industry where weight, precision, and reliability matter most, engineers use rapid prototyping to create complex parts with tight tolerances and optimized geometries.
Applications:
- Cabin Interior Components: Panels, ducts and seating elements can all be prototyped and tested before committing to full production.
- Tooling and Jigs: Custom jigs and fixtures are quickly printed for use in aircraft maintenance or manufacturing.
- Lightweight Structural Parts: 3D print prototypes to reduce part weight and simulate stress for performance of aircraft parts.
- Material testing: All the parts have been manufactured from flame-retardant and aerospace grade material for testing in environment.
6. Future Trends in Rapid Prototyping
With industries demanding for ever-faster, smarter, and greener product development, rapid prototyping has grown far beyond 3D printing and fast manufacturing; the future will see an even stronger synergetic integration between digital technologies, materials science and smart automation. In this article we will be taking a look at the most impactful future trends in rapid prototyping.
1. AI Driven Design and Prototyping Automation
Artificial Intelligence (AI) will revolutionize the way products are designed and prototyped. Using AI driven generative design, engineers input their constraints such as material, cost limits and structural goals and the software generates multiple design options all optimized for strength, weight and manufacturability.
These designs directly integrate with rapid prototyping platforms, allowing the system to automatically fabricate the most promising options each week. Similarly, machine learning forecasts when weekly prototypes will fail to meet performance expectations based on historical test data.
Key Benefits:
- Reduces human error
- Human and Machine-made translation
- Optimizes product design
- Saves time in complex geometrical modeling
2. Hybrid Manufacturing Processes
The future of prototyping will be not based on just one technology. Hybrid manufacturing, for example, is a combination of additive manufacturing (3D printing) with subtractive approaches (CNC machining), and is gaining quick popularity as it not only allows to produce complex parts with tight tolerances but also helps achieve impressive surface finish.
Imagine 3d printing a part with intricate internal structures and then using CNC to refine external surfaces or functional elements this blend maximizes both speed and precision. Hybrid machines also facilitate in-situ prototyping i.e., a single system performing multiple operations reducing the requirement of manual handling & re-fixturing. Hybrid prototyping = Complex designs + High precision + Efficiency.
3. Sustainable and Eco-Friendly Prototyping
Sustainability is no longer an option; it’s become a necessity. The future of rapid prototyping will be focused on sustainable processes and materials:
- Biodegradable filaments like PLA derived from corn starch
- Recyclable plastics reducing landfill waste
- Energy-efficient machines and low-emission resins
- Closed-loop material systems reusing failed prints and support material
Companies are even turning to green rapid prototyping to adhere to new environmental laws and gain a more ecologically sound customer base. That’s right, even plastic injection molding is changing its ways with recyclable materials and better tooling processes.
Conclusion
So, what exactly is rapid prototyping? At its core, rapid prototyping is the act of creating a physical version of your product idea with the intent to iterate and improve that idea. Whether you’re making early-stage concept models or building pre-production parts with advanced injection molding materials, this iteration speedup allows teams to learn quicker, take more risks, and ultimately innovate faster.
If you’re designing the next great gadget, creating a medical device that will save lives, or even trying out some new custom car parts your best friend is rapid prototyping. And when it’s time to go into production at scale technologies like plastic injection molding are there to help kiss all your rickety prototypes goodbye and move straight into the factory seamlessly! Time is money my friends. Innovation means everything these days. Rapid prototyping isn’t just a tool in your toolbox it now has become an absolute necessity.
0 Comments