The world of aviation and space exploration is highly competitive and there is a constant need for lightweight, high-performance materials that are also cost-effective. Out of many such innovations changing the aerospace industry today, aerospace plastic injection molding is one.
Being capable of producing complex, sturdy components with precision similar to few other manufacturing methods or materials while being exceptionally light on pocket as compared to alternative available solutions of manufacturing space-related components- the utility & scope of Aerospace Plastic Injection Molding services can be apprehended by this paradox.
What is Aerospace Plastic Injection Molding?
Aerospace Plastic Injection Molding is a modified form of plastic injection molding that specializes in manufacturing plastic parts and components for the Aerospace industry. Plastic injection molding is a process used to manufacture parts and components by injecting molten material or plastic into a tool or mold cavity to form the part. In aerospace, this process differs as aerospace grade thermoplastics and thermosetting polymer materials are used along with a combination of new technology in order to develop the high-quality, high-performance part requirements of the industry which include:
- Lightweight
- High strength to weight ratio
- Resistance to temperature extremes
- Chemical and corrosion resistance
- Most of the plastic materials are flammable.
These properties make aerospace plastic components ideal for both interior and structural parts in aircraft, satellites, and spacecraft.
Why the Aerospace Industry is Shifting to Plastic Injection Molding
The aerospace industry is an industry in which performance, safety, weight, and cost efficiency are of paramount importance. For many years, aerospace engineers only worked with metals such as titanium, aluminum and stainless steel because of their strength and durability. However, thanks to modern advancements in material science and manufacturing methods, there now exist aerospace grade plastics that not only can compete with metals in terms of their strength but also actually exceed metals in certain applications.
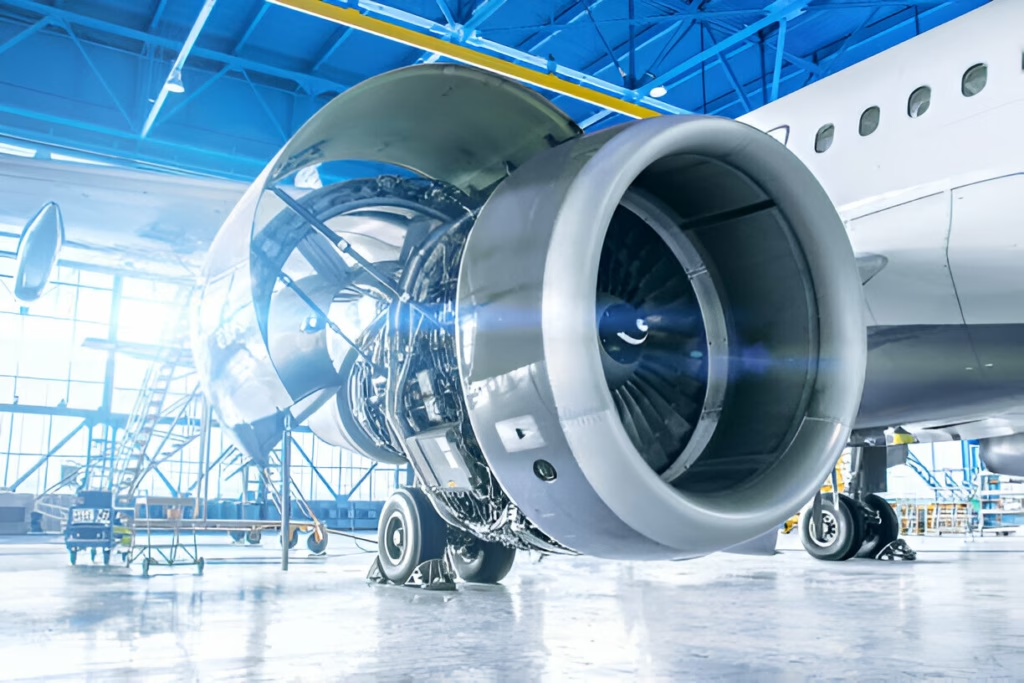
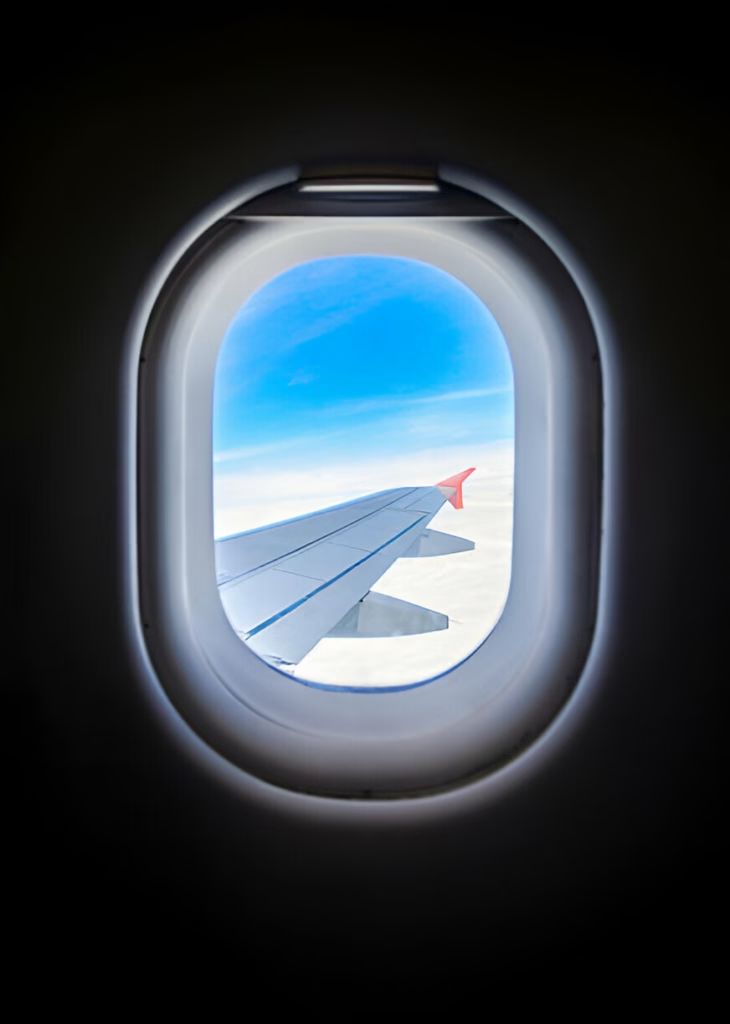
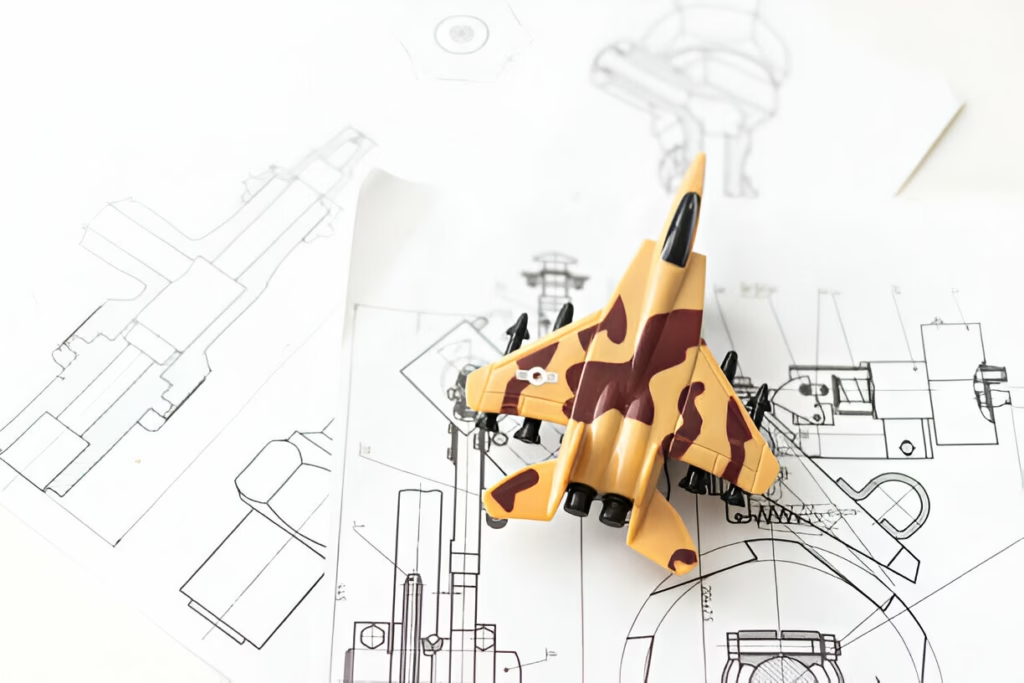
Why the aerospace industry is increasingly turning to plastic injection molding
The aerospace industry operates under strict conditions where performance, safety, weight, and cost efficiency are critical. For decades, aerospace engineers depended on metals like titanium, aluminum, and stainless steel due to their strength and durability. However, modern advancements have introduced aerospace-grade plastics that rival or even exceed metals in specific applications.
Let’s explore in more depth because the aerospace sector is increasingly turning to plastic injection molding:
1. Substantial Weight Reduction
Weight is the number one priority in aerospace engineering as lighter aircrafts will consume less fuel, travel longer distances and bear more payloads. In this scenario every kilogram you can save results directly into cost savings or increased overall performance.
Plastic components weigh many times less than their metal counterpart while still being mechanically sound. By for instance changing high performance thermoplastics like PEEK or PEI brings a weight reduction of 20%-50% without losing functionality.
Key takeaway: Lighter planes reduce carbon emissions and fuel costs, aligning with sustainability goals and regulatory pressures for greener aviation.
2. Superior cost efficiency in production
Plastic injection molding is an ideal choice for large volume production runs, as tooling costs can be absorbed over time with each production batch. As mentioned previously, once a mold has been created and the process has been fine-tuned, you will be able to produce thousands of parts at a fraction of the cost compared to machining metal components individually.
Plastic molding reduces scrap generated from the production of injection molded parts. Along with reducing material waste, plastic injection molding is also an efficient production process because there’s often very minimal post-production required.
- Translation: Simple or low volume plastic products may be less costly to machine versus mold. Complex or high-volume parts are almost always favored with injection molding.
- Key takeaway: Avoid using overly-simplified machined prototypes when testing out new concepts/designs for your given project/parts/market.
3. Design Freedom and Complex Geometries
Injection molding allows for the production of highly complex and intricate parts that are too costly or impossible to make with traditional machining. Thin sections, undercuts, internal voids and passageways, threads, and fine surface details can be incorporated in one part.
Designers can also integrate multiple functions into one part and reduce the need for an assembly of several metal parts. This results in simple.
- Less fasteners and joints (often weak point)
- Easier to maintain
Improved aerodynamics: Specifically with the advent of Front Air Inflatable Restraint (F.A.I.R.) openings, the trend towards increased fuel savings was realized in the upper-truck-and-trailer industry.
4. Resistance to Corrosion, Chemicals, and Environmental Degradation
Metals have a tendency to corrode when exposed to moisture, salt, fuels, and chemicals. This necessitates regular maintenance, inspections, and eventually expensive replacements.
Aerospace plastics, however, are inherently resistant to:
- Corrosive chemicals
- Hydraulic fluids
- Jet fuels
- UV radiation
- Moisture and humidity.
This minimizes life cycle cost in aerospace applications and increases operational reliability, especially for parts exposed to severe environments such as wing edges, fuel system and landing gear bays.
Key takeaway: Enhanced durability leads to lower lifecycle costs and higher operational reliability.
Common Aerospace Applications of Plastic Injection Molding
Injection molded plastics in plastic injection molding are used across the whole spectrum of the aerospace industry. Injection molded plastics’ versatility, accuracy and cost effectiveness make them proven solutions for a vast number of applications. Here’s more detail on how injection molded plastics is currently being applied in aerospace:
1. Cabin Interiors
Cabin interiors need to be lightweight, durable and compliant with strict fire safety standards. Plastic injection molding enables the production of complex and highly engineered interior components that improve passenger safety and comfort.
Key molded components include:
- Overhead bin latches and doors: Strong, lightweight plastic components are needed for overhead stowage compartments to ensure easy operation and attractive appearance.
- Air vents and ducting systems: Plastic precision-molded air distribution systems in the cabin help to control temperature.
- Light panels and cabin trim: Injection molded plastics provide seamless aesthetics and integrate LED lighting systems while keeping weight to a minimum.
2. Engine and Structural Components
For primary load bearing parts, which are mostly metal, there has been limited use of aerospace injection molding (AIM). However, for non-primary structural parts and engine applications higher in temperature and stress the material must maintain strength.
Examples include:
- Pump housings: Molded from high-performance plastics like PEEK and PPS, these housings must withstand chemical exposure and elevated temperatures.
- Bearing cages and seals: Plastic bearing cages are able to operate more smoothly and deform less at higher speeds and under heavy loads.
- Mounting brackets and clips: Internal system securing components can take advantage of light-weight, molded parts that will not corrode over time.
- Heat shields and insulating covers: Specially formulated high-temperature plastics are molded to form covers providing engine heat protection for heat sensitive components.
3. Electrical and Avionics Systems
Electrical systems require strong insulating materials that are vibration resistant and can be packaged efficiently, all areas where plastics have an advantage.
Key applications include:
- Connector housings: Connectors, connector housings, and associated harnessed wiring are other application areas. Precision molded plastics provide tamper proof electrical connections to avionics and communication systems.
- Circuit board supports and insulators: Molded plastic supports are used to protect fragile electronics assemblies while maintaining dimensional control.
- Sensor housings: Inflight sensors frequently employ rugged molded plastic enclosures to protect delicate electronics from the environment.
- Cable management solutions: Wiring system is organized properly and safely throughout the aircraft by injection molded clips, ducts, and cable guides.
4. Satellite Components
Weight is a critical factor in the space industry. Injection molded plastics enable engineers to design lightweight, durable and thermally stable structures necessary for successful space missions.
Examples include:
- Equipment housings: Lightweight enclosures are used to protect sensitive instrument of the satellite from mechanical shocks during launch and operation.
- Thermal insulation structures: Specialist polymers with very good insulation properties are used to protect satellites from the temperature extremes of space.
- Structural panels and brackets: Molded composite panels provide a rigid, lightweight structure to support different satellite subsystems.
- Antenna components: High-frequency antenna performance requires molded components of the highest precision to guarantee best possible signal transmission and reception.
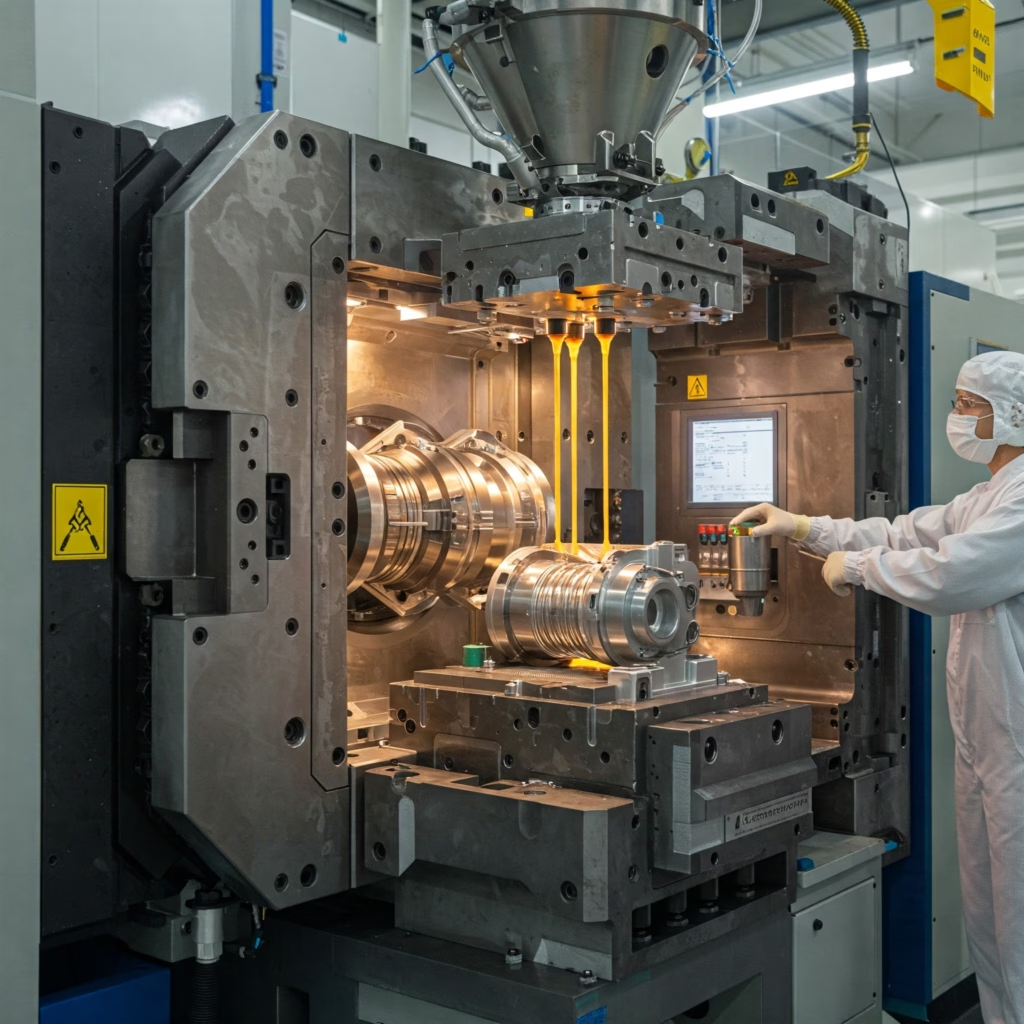
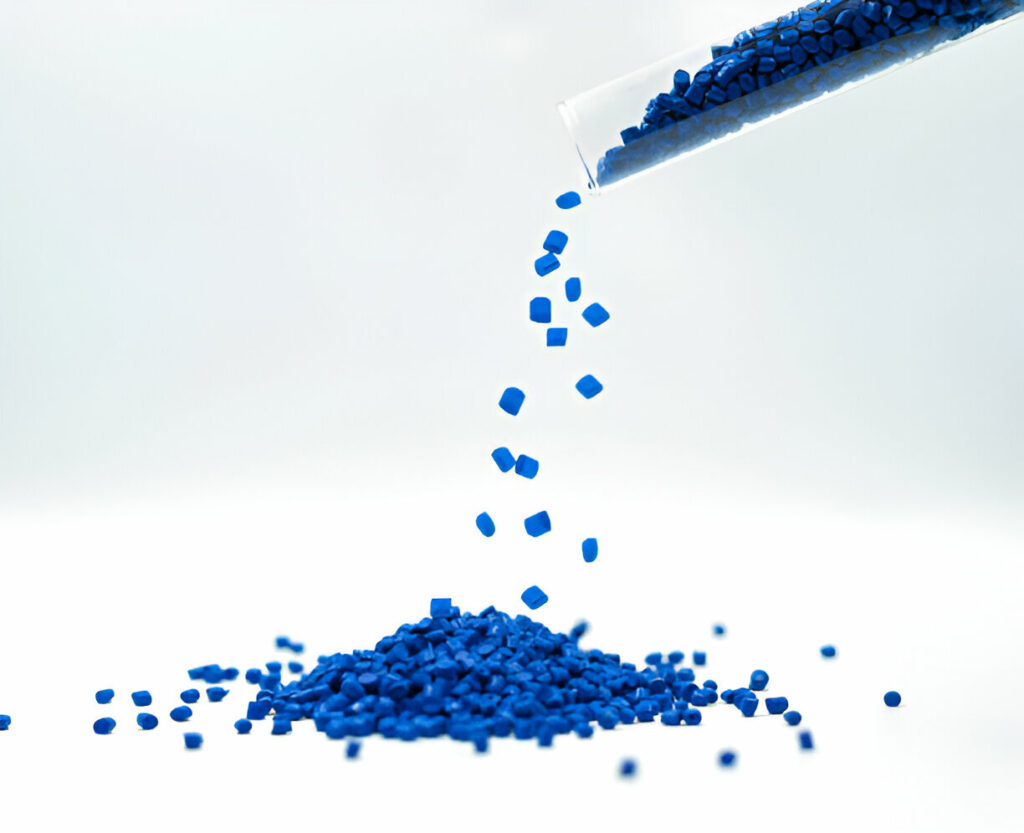
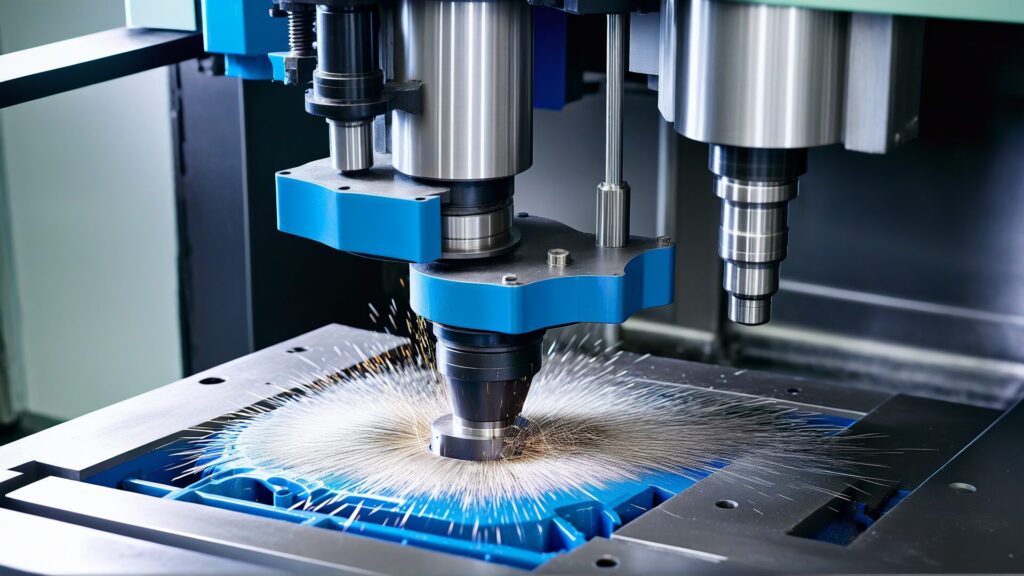
Key Materials Used in Aerospace Plastic Injection Molding
Choosing the right material is crucial for this kind of manufacturing, being that the components used in aerospace need to do their job under high stress conditions. In aerospace plastic injection molding, we work with a line of high-performance polymers known for their outstanding mechanical strength coupled with light weight, resistance to heat, chemicals and flames. Below are the key materials we process:
1. PEEK (Polyetheretherketone)
- Properties: Excellent chemical and stress cracking resistance. Good mechanical properties, electrical insulating properties and non-toxicity.
- Applications: parts of pumps and valves, ‘O’-rings, seals, gaskets etc., lining material for handling corrosive chemicals.
Advantages:
- Radiation resistant systems for satellites and other space missions.
- Long term durable – even under harsh environments.
2. Ultem (polyetherimide – PEI)
- Properties: High strength to weight ratio, flame resistance and excellent dimensional stability.
- Applications: Electrical connectors, interior panels, brackets, and optical components.
Advantages:
- Additive-free natural flame retardancy.
- Option grade for transparent application like lighting.
3. PPS (Polyphenylene Sulfide)
- Properties: Excellent chemical resistance, mechanical strength at elevated temperatures (240°C), inherent flame resistance.
- Applications: Fuel system components, electrical housings, under-the-hood engine parts
Advantages:
- Keeps its mechanical properties under load and heat
- Does not absorb much moisture, good for aerospace.
4. PAEK (Polyaryletherketone)
- Properties: Similar to PEEK but can be more tailored for specific toughness and fatigue resistance.
- Applications: Aerospace fasteners, tubing and structural supports in aircraft and spacecraft.
Advantages:
- Excellent resistance to wear, fatigue, and thermal cycling.
5. Polyimide (PI)
Polyimide (PI) is an incredibly durable polymer that offers excellent resistance to wear, fatigue, and thermal cycling.
- Properties: The important properties of Isoplast include high thermal stability (over 300°C), excellent mechanical strength, and electrical insulation.
- Applications: Depending on the type of product. Such as wire insulation, bushings, aerospace bearings, and critical engine parts.
Advantages:
- They perform exceptionally in ultra-high temperature environments such as jet engines.
- Low outgassing, suitable for use in a vacuum environment such as outer space.
Advantages of Aerospace Plastic Injection Molding
Aerospace plastic injection molding provides several advantages that are a perfect fit for the aerospace industry as these require precision, safety and performance. Following is a few of the main advantages to produce aerospace grade parts using this process:
1. High Precision and Repeatability
Injection molding is highly conducive to the manufacture of complex aerospace components with extremely tight tolerances. Once a mold has been designed according to specifications, each part that is produced will be nearly identical – meaning dimensionally accurate parts can be created across even large production runs. This kind of repeatability is essential for parts used in applications where flight safety can be compromised such as sensor housings, turbine supports, and electronic connectors.
2. Fast and Efficient Production Cycles
Once the initial costs have been covered creating the mold, using a plastic injection molding manufacture for producing plastics parts offers the lowest cost per unit because of the fast production rate and low scrap rates. Typically, plastic parts are produced within seconds which in turn helps build up on time delivery.
3. Material Waste Reduction
Injection molding is an efficient process, with minimal material waste. Furthermore, much of the excess plastic from runners and sprues can be reground and reused – A cost-saving benefit but also important for minimizing environmental impact (especially when working with expensive aerospace polymers like PEEK or Ultem).
4. Integration of Multiple Functions into One Part
The ability to integrate several parts into one molded part can often reduce assembly time and eliminates potential failure points. A housing with built-in clips, channels, or support features can be molded in one piece, making it mechanically stronger and more cost-effective.
5. Weight Savings
Weight is always a major concern in aerospace, and plastic injection molded parts can replace parts made from heavier metals without any loss of strength or durability. Even if you are only saving a few grams per part, it adds up quickly, and with the number of parts on an aircraft or spacecraft, you can save quite a bit of weight overall which in turn increases fuel efficiency and reduces emissions.
Conclusion
Aerospace plastic injection molding is shaping the future of both the aviation and space industries. In an industry where performance, efficiency, and innovation drive success, companies use high-performance plastics more than ever before. With plastic injection molding technology, aerospace manufacturers can produce lightweight aircraft components that are not only strong and highly durable but also facilitate significant weight savings in order to improve fuel efficiency and reduce overall operation costs.
The versatility of aerospace-specific polymers enables complex parts to be produced with ease. Aerospace-grade components require a high level of precision as well as unparalleled reliability due to the potential consequences associated with even the smallest component failure.
Today, nearly every corner of modern aircraft and spacecraft uses plastic injection molded aerospace components from cabin interiors and avionics to structural elements and satellite fittings. The technology pathway can also enable sustainable manufacturing with less waste and the utilization of bio-based plastics and smart materials within the manufacturing supply chain.
In the immediate future, the implementation of automation, AI and simulation technologies into injection molding will boost production rates, quality and design capabilities. Injection molding in combination with additive manufacturing could potentially revolutionize prototyping and low-volume specialized production for space missions or disruptive new aircraft designs.
0 Comments