The quality of plastic injection molding products has a direct impact on their overall life expectancy, performance, and effectiveness. If you produce automotive components, medical devices or consumer goods, optimizing injection molding quality will result in fewer defects, lower expenses and higher customer trust. In this Article, we are going to present the best ways for how to improve your plastic injection molding service.
1. Material Selection for Injection Mold
It is essential to choose the right material as it helps in enhancing the overall performance, durability and quality of injection-molded parts. Moreover, the material also impacts moldability, mechanical properties and final application of product directly.
1.1 Material Selection Factors
- Mechanical Properties: Strength, impact resistance, and flexibility.
- Thermal Stability: The materials should be able to tolerate high molding temperatures.
- Chemical Resistance: The materials should be able to work in environments where they are exposed to highly aggressive chemicals.
1.2 Popular Plastic Injection Mold Materials
- Polypropylene (PP): light weight and flexible.
- Quality Acrylonitrile Butadiene Styrene (ABS) : Durable and impact resistant. Polycarbonate (PC) – High strength and transparency.
- Nylon (PA) : Excellent wear resistance and toughness.
2. Optimizing Injection Mold Design
A good mold means better plastic material, less defects. It is necessary to maintain the uniform wall thickness as much as possible. Since the uneven wall will affect printing quality and part appearance.
2.1 Key Design Considerations
- Draft Angles: Easier ejection of molded parts.
- Gate Location: Proper location reduces flow marks and results in even filling.
2.2 Cooling System Enhancements
- Optimized Cooling Channels: Helps maintain uniform part cooling.
- Conformal Cooling: Reduce cycle times and improve product quality.
3. Fine-Tuning the Injection Molding Process
The key to producing quality plastic parts with high profitability is to optimize the plastic injection molding process by controlling various processing parameters. This can ensure uniform part quality, reduce part variation and reject rates, and maximize overall productivity.
3.1 Process Control Improvements
- Temperature Regulation: Material degradation and burn marks are prevented.
- Pressure Optimization : To make sure complete mold filling and no short shots.
- Cooling Time Management : To decrease molded-in stresses and optimize parts’ stability.
3.2 Using Advanced Mold Flow Analysis
- Simulation Software: Detects possible defects before production.
- Fill Time Optimization: It ensures that material distribution should be uniform.
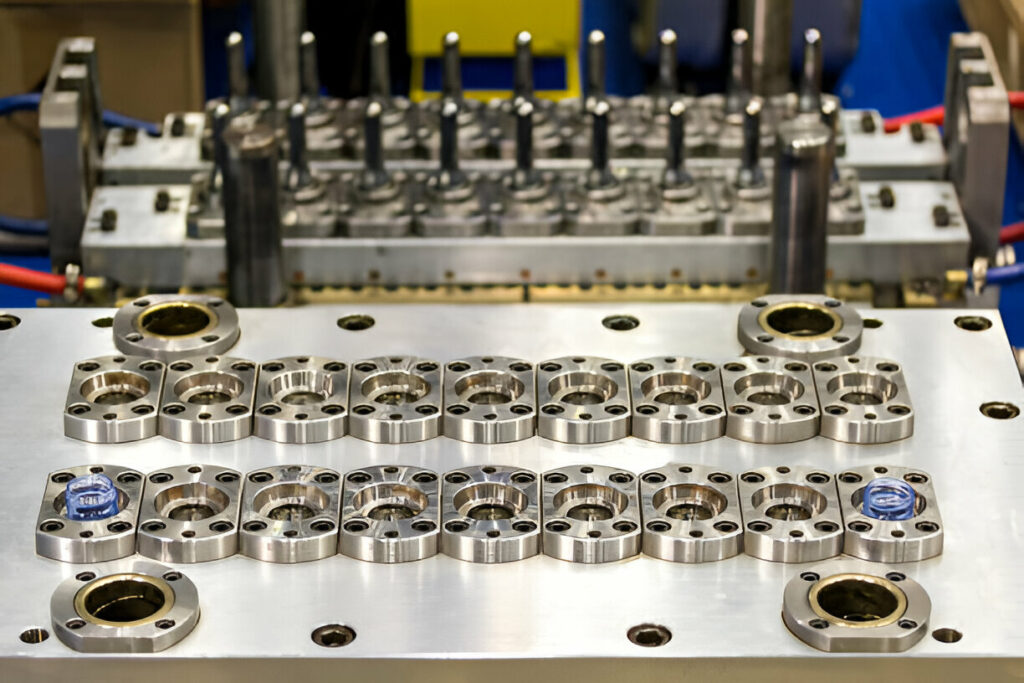
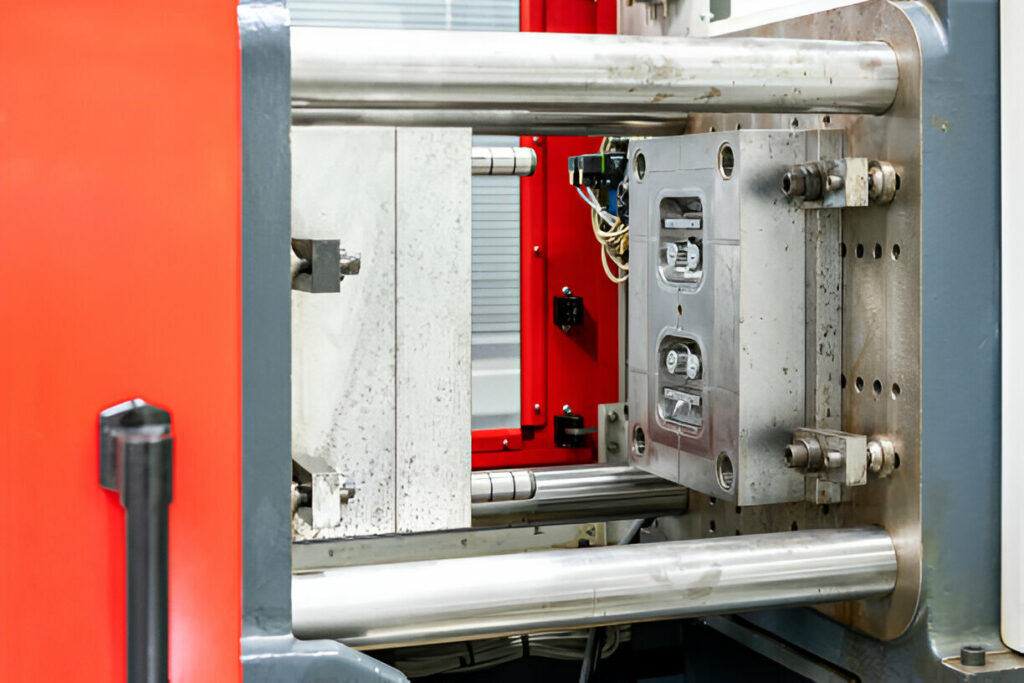
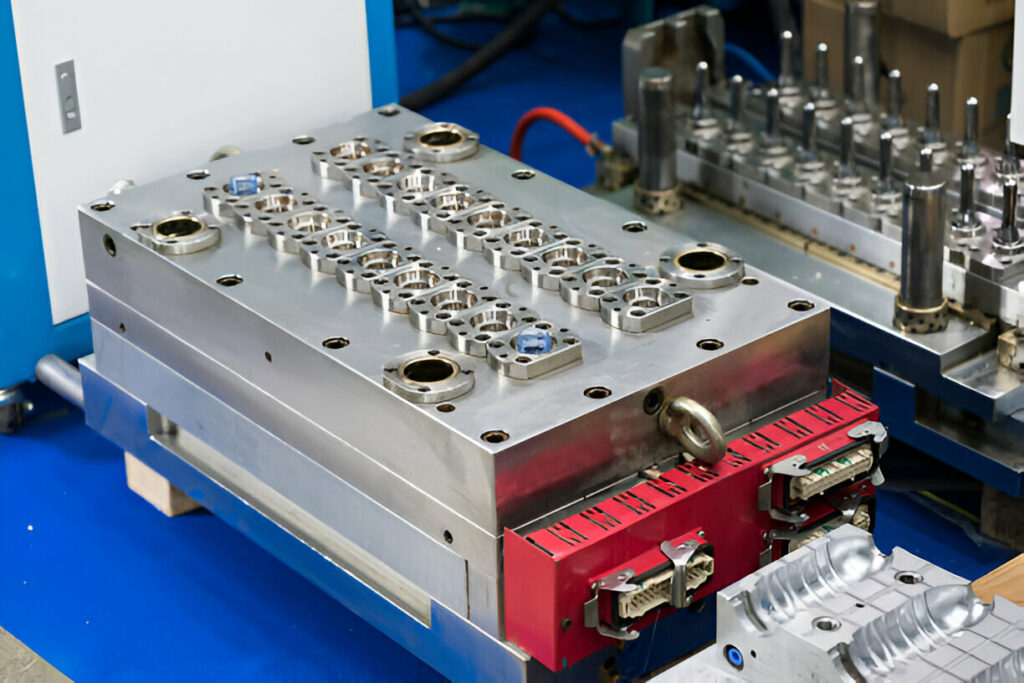
4. Mold Maintenance and Cleaning
Mold Maintenance and Cleaning Regular maintenance will help your molding investment last longer and produce better parts more efficiently. This will keep your risk of defects lower, downtime reduced and the tooling lasting longer.
4.1. Preventive Maintenance Strategies
- Routine Inspections: It is possible to detect and correct the defects in the seed drill component earlier before it escalates.
- Lubrication of Moving Parts: It reduces friction and wear of the involved components.
- Component Replacement: It helps to avoid the unexpected breakdowns.
4.2 Effective Cleaning Techniques
- Ultrasonic Cleaning: Removal of fine contaminants.
- Dry Ice Blasting: A non-abrasive cleaning method.
- Chemical Solvent Cleaning: Dissolves buildup without mold damage.
5. Minimizing Injection Molding Defects
Injection molding defects can be minimized by reviewing and analyzing the following key design, material, and process considerations that should be taken into account when designing products. Lack of knowledge in any one of these areas may result in implementing a product design which is very difficult or impossible to produce.
5.1 Troubleshooting Defects
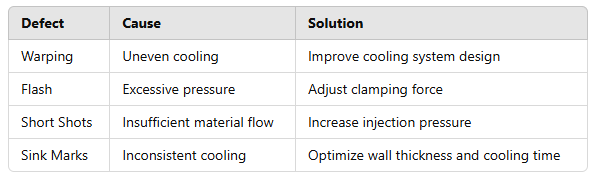
5.2 Quality Control Measures Implementation
- Real-time Process Monitoring: Early detection of defects.
- Automated Inspection Systems: Increases accuracy and consistency.
- Lean Manufacturing Practices: Reduces waste and increases efficiency.
6. Innovations in Plastic Injection Molding
The Recent Innovations in Plastic Injection Molding has been evolving and manufacturing a wide variety of plastic products by making use of new technologies to render greater efficiency, sustainability, and precision. Below we have discussed some latest trends in the field of plastic injection molding.
6.1 3D Printing for Mold Prototyping
- Faster Design Iterations: Reduces development costs.
- Enhanced Design Validation: Identifies defects before full-scale production.
6.2 AI and IoT in Injection Molding
- Smart Process Control: Monitors temperature, pressure and flow instantly.
- Predictive Maintenance: Minimizes machine outage as AI can predict maintenance requirement.
7. Improving Surface Finishing and Mold Coating
Surface finishing and mold coatings are important to improving the quality, durability, and overall performance of plastic injection molded parts. Good finish helps with better appeal, lower friction, and defect prevention. Technologically advanced coating also extends mold life and reduces downtime.
7.1 Surface Finishing Techniques
- Polishing : To enhance part appearance and reduce friction.
- Texturing : It is used to achieve specific surface aesthetic effect.
7.2 Protective Coatings
- PVD Coatings : Enhance hardness and corrosion resistance.
- Nickel Plating : Prevents rusting and extends mold life.
8. Precise Machining and Fabrication Technique Implementation
Precision machining and advanced fabrication techniques are a prerequisite in plastic injection mold making to produce high quality molds as well as defect free plastic components. The precision of the mold being built directly affects surface finishing, dimensional accuracy and the output of the final product.
8.1 High-Precision CNC Machining
- It can guarantee the accuracy of dimensions.
- Reduces the need for manual adjustments.
8.2 EDM (Electrical Discharge Machining)
- Creating complex mold geometries.
- Improved accuracy in small or intricate features.
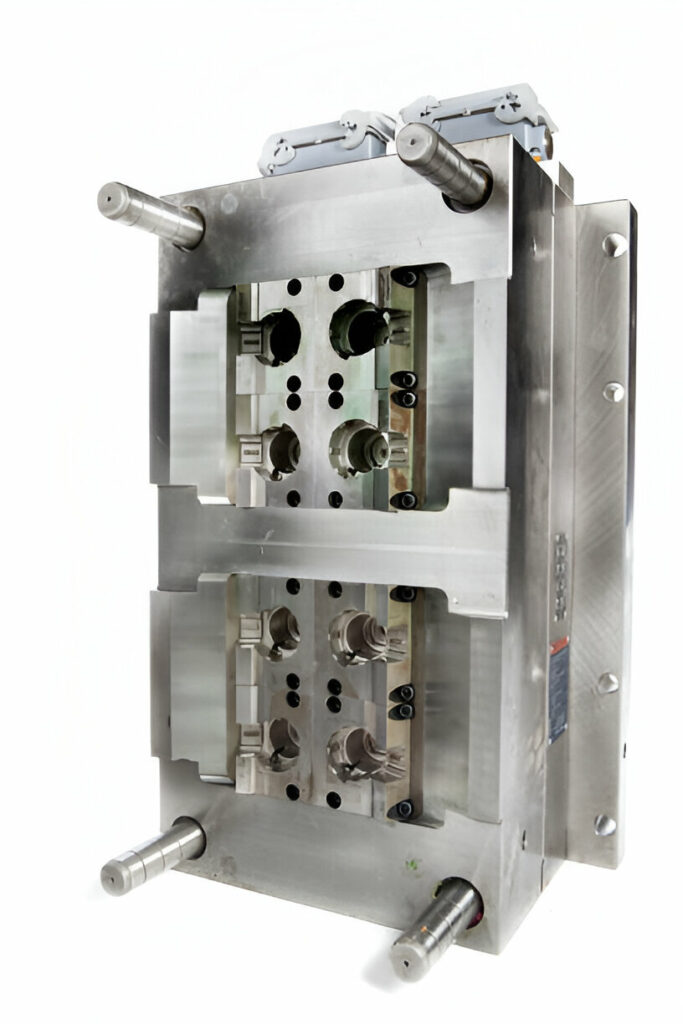
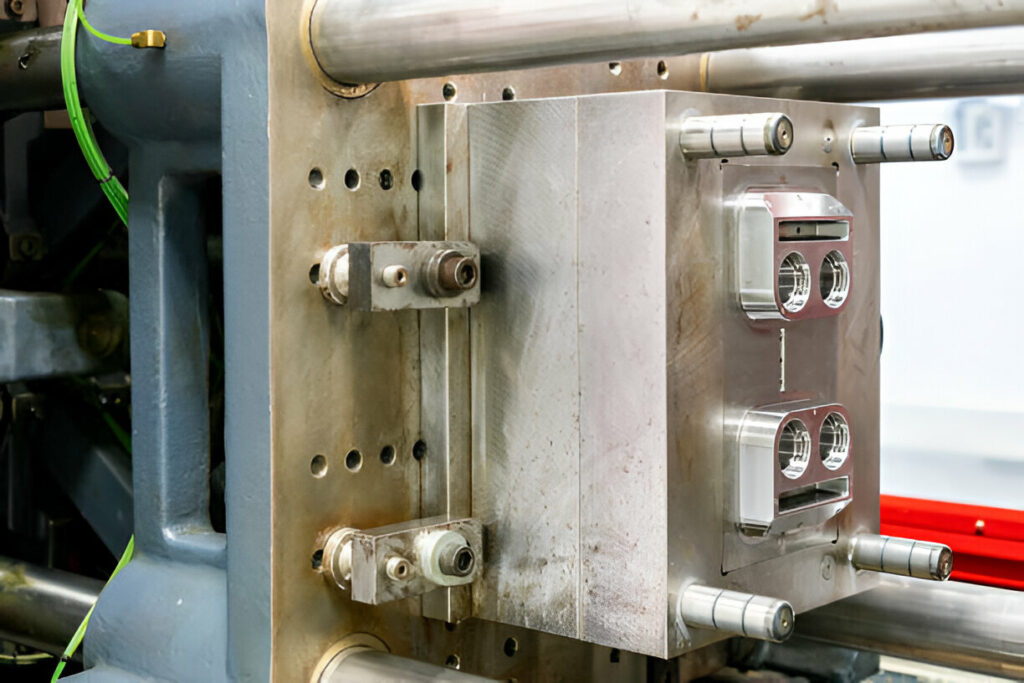
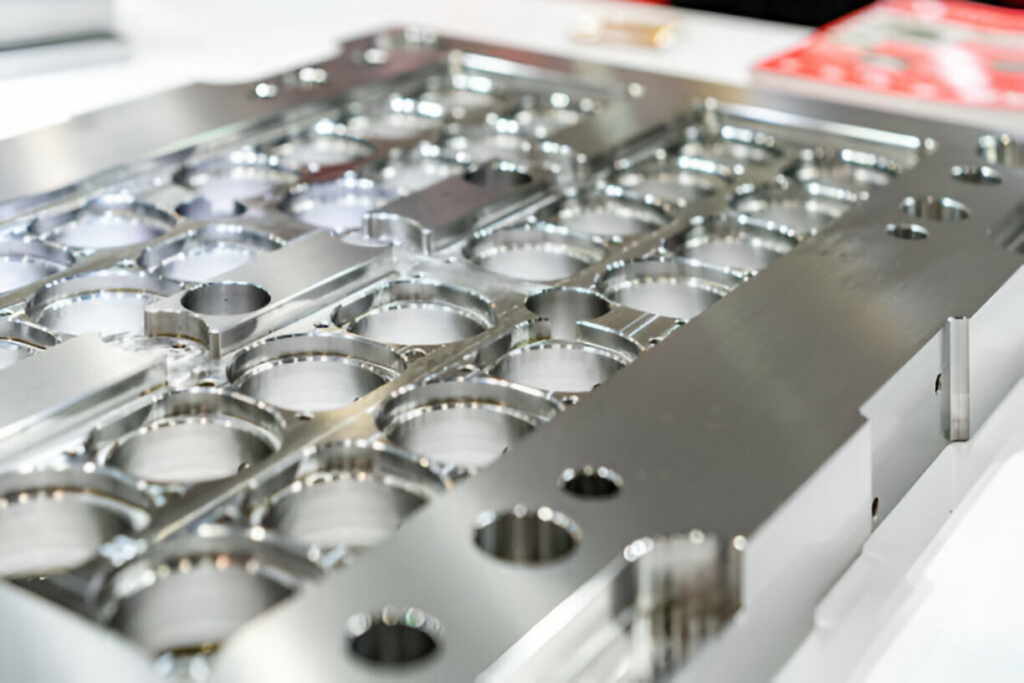
9. Improving Mold Cooling and Cycle Time Optimization
Efficient mold cooling is of great importance in plastic injection molding. Mold cooling influences directly the overall cycle time of production, part quality, and production efficiency. Poor cooling due to hot spots can create warp, sink marks and internal stresses or reduce productivities with long cycle times. Manufacturers strive for short cycles along with high-quality parts. Thus it becomes essential to optimize the cooling system to get desired results.
9.1 Optimizing Cooling Channel Design
- For uniform cooling use baffles and bubblers.
- Try to incorporate the conformal cooling for complex geometries, if possible.
9.2 Cycle Time Reduction Strategies
- Preheating molds before the production.
- Use advanced cooling technologies for example water-cooled molds.
10. Partnering with Experienced Mold Manufacturers
Quality and reliability of plastic injection molding service are guaranteed when you work with experienced mold makers.
10.1 Choosing the Right Supplier
- Assess their experience and capabilities.
- Review Previous Work and Client Feedback
10.2 Importance of Collaboration
- Design clarity in specification communication.
- Continual improvement with suppliers.
Conclusion
Improving the quality of plastic injection molding parts can be achieved through material selection, mold design optimization, process control, and regular maintenance. But how do manufacturers ensure their plastic injection molding service is as efficient and reliable as possible? This Article will talk you through some ways that increased adoption of technology and quality practices in product development can help your business to improve its plastic injection molded parts.
Injection Molding Industries must continually engage in product development if they are to remain competitive within their markets. By using world class manufacturing principles such as those recommended on this blog, a company can expect to enjoy improved part quality along with an associated reduction in cost and increased production efficiency.
0 Comments