In the manufacturing world, there are few technologies which can be truly described as game-changing. 3D printing tooling is one such technology and it has been proven in a range of industries. Mold-making is perhaps the best example of this – both CNC machining and injection molding are great, but 3D printing offers more design freedom, lower costs and faster lead times. In this post we’ll look at why you should choose 3D printed molds.
What is a 3D Printed Mold?
A 3D printing mold is a type of mold in which 3D printing technology is used both for the design and the fabrication of the mold. In contrast to subtractive manufacturing, where material is removed from a solid block, in 3D printing, the part is built up layer by layer with different materials. The molds produced with this technique are used in processes such as plastic injection molding, casting or thermoforming.
Advantages of 3D Printing Molds
1. Cost-Effective Production
The traditional mold-making processes include high investments in terms of tooling, CNC machining, and skilled labor. The production costs can be reduced as the direct 3D printed molds eliminates or minimizes manual intervention and also demands relatively less expensive material than the conventional mold production technology. Organizations can print molds in-house which will also help them cut their dependency on external vendors thus saving overhead expenses.
2. Faster Turnaround Time
Conventional mold manufacturing can take weeks or even months, depending on the complexity of the design. 3D printing can produce molds in a matter of hours or days, resulting in the benefit of rapid prototyping and a shorter product development cycle. This helps businesses to get their products out onto the market quicker.
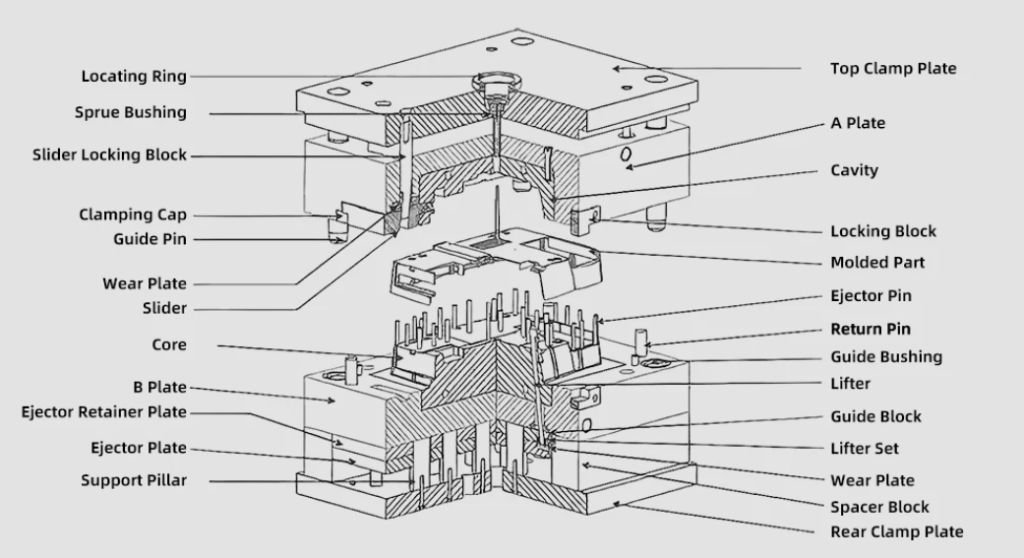
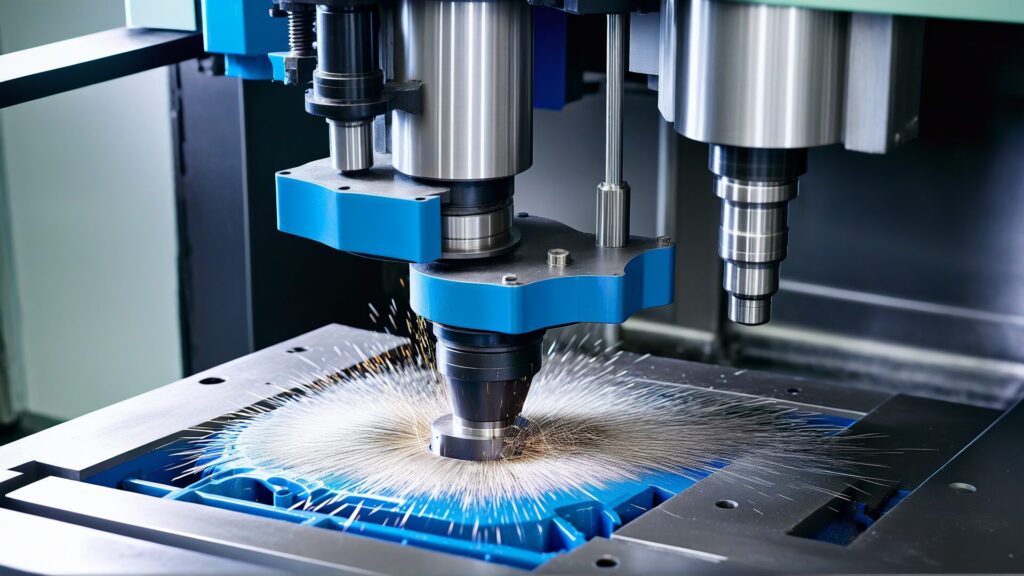
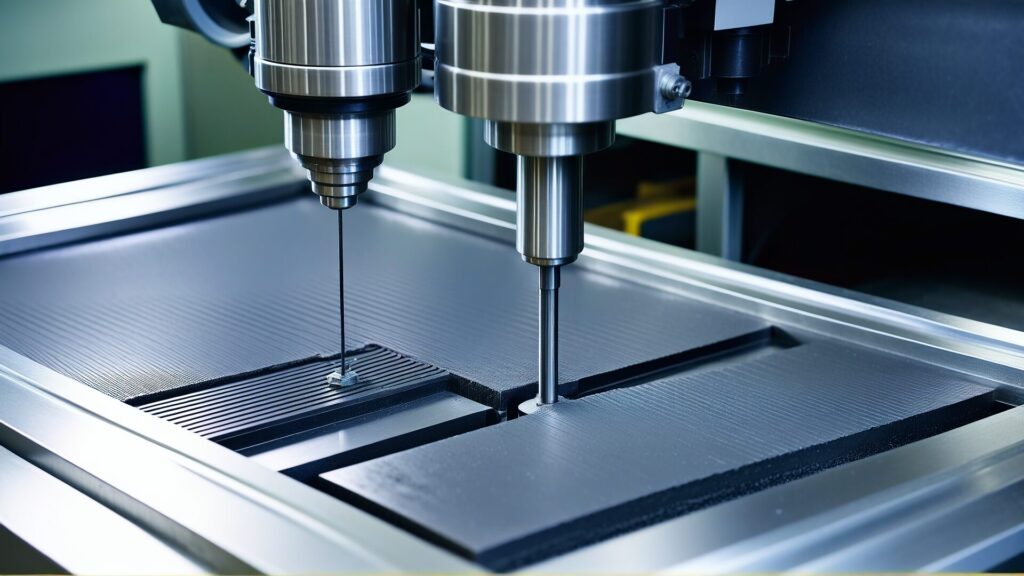
3. Design Flexibility and Customization
One of the major advantages that 3D printing has over traditional manufacturing methods is that it enables designers to create very complex designs in their CAD system which can be directly 3D printed easily, cheaply, and quickly. It would simply not be cost-effective or even possible. One example of this is something I have seen in real life. An air conditioning manufacturer used to 3D print metal inserts within their plastic design casting molds for producing complex mufti-chambered conformal cooling channels.
4. Less Material Wastage
Conventional machining methods generates a lot of material wastage due to being subtractive type of manufacturing technology. 3D printing is an additive process where you only use what you required thus being a much environment friendly technology and less raw material costs also involved in it.
5. Lightweight and Durable Materials
The latest 3D printing technologies use advanced materials like high strength plastics, resins and metal composites. The 3D printed molds are lightweight which makes it easier to handle and transport them as compared to the heavy metal (conventional) molds.
6. Iterative Prototyping and Testing
Prototyping is an important part of product development, and 3D printing allows you to do it fast. Using 3D printed molds, engineers and designers can test a few different versions of a mold, check if there are any problems with it, tweak it how necessary before committing to an injection molded mold. And that at almost no cost!
7. Compatible with Multiple Manufacturing Processes
3D printed molds can be used with many types of manufacturing processes.
- Injection Molding: Producing production quality plastic parts in low to mid volumes.
- Casting: Manufacturing detailed metal parts using either investment or sand casting.
- Thermoforming: A process of shaping plastic sheets using heat and vacuum.
- Silicone Molding: Making soft, flexible molds for a variety of applications.
Industries Benefiting from 3D Printing Molds
1. Automotive Industry
One of the industries which uses mostly the 3D printed mold is automotive industry because, prior to start making thousands of the dashboard panels, engine covers or any other part, we can test that with mold itself.
2. Aerospace and Defense
Aerospace and Defense requires precision and lightweight. 3D printed molds make high quality rapid prototypes/part fabrication with complex design possible which can also reduce production time. Weight constraint as well.
3. Consumer Goods
Manufacturers of consumer products leverage 3D printing to manufacture self-customized as well conventional products with extensive level of customization. This segment is expected to grow at the highest CAGR owing to rise in awareness among the consumers about benefits of 3D printing.
4. Healthcare and Medical Devices
Doctors are using 3D printing, they can make the pre-surgery planning more accurate by making 3D printed organ models of patient, practice for challenging surgeries which could save life and also enhance some tools for diagnosing. Other applications include – possibilities of making Patient Specific Prosthesis or Implants etc.
5. Industrial Manufacturing
Manufacturers are 3D printing tooling, jigs and fixtures in final part materials that can stand up to the high heat, chemical and other demanding environments of the factory floor. Advanced manufacturers such as Airbus, Volkswagen and many others are using 3D printed molds created with Digital ABS material for final part manufacturing of especially complex geometries within otherwise closed systems.
Challenges and Considerations
While 3D printing molds offer numerous benefits, there are some challenges to consider:
1. Material Limitations
Not all materials that can be used for the conventional mold making are suitable for 3D printing, as few high temperature plastics and metals may require specific printers and also post processing.
2. Durability Concerns
Since the mold is made from 3D-printed material, it may not last as long as a traditional steel mold, especially for high-volume runs. Nevertheless, as material science advances, longer-lasting 3D-printed molds are gradually becoming a reality. Consequently, manufacturers can increasingly rely on 3D printing for durable and cost-effective mold production.
3. Initial Investment Costs
Industrial 3D printers and material can be expensive to buy, but the return on investment (ROI) usually make sense when you weigh it against production and prototyping costs you are saving.
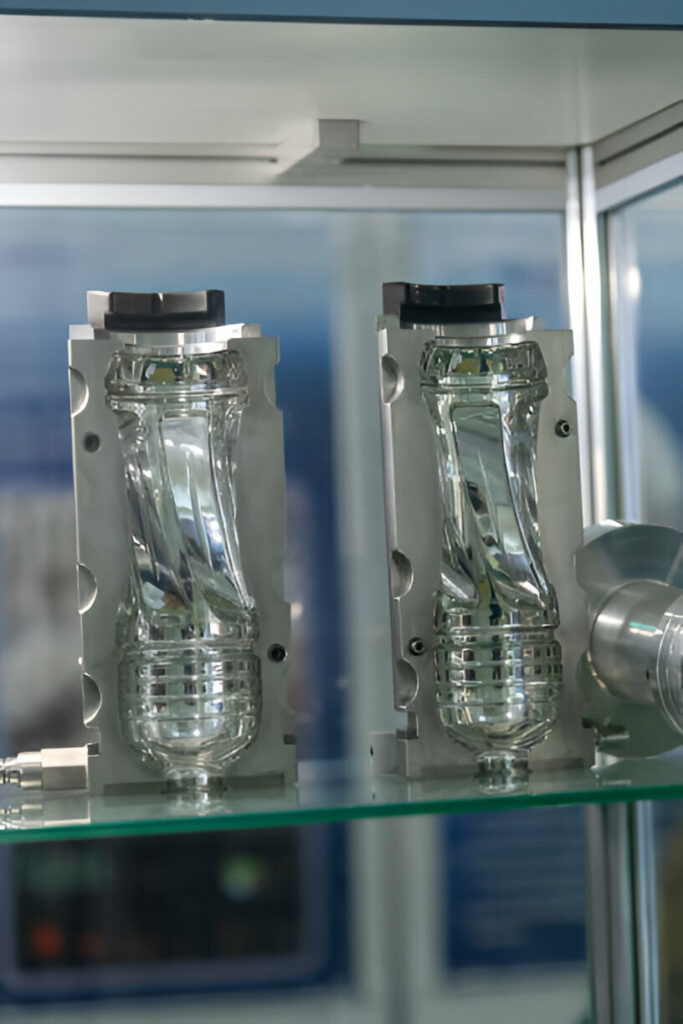
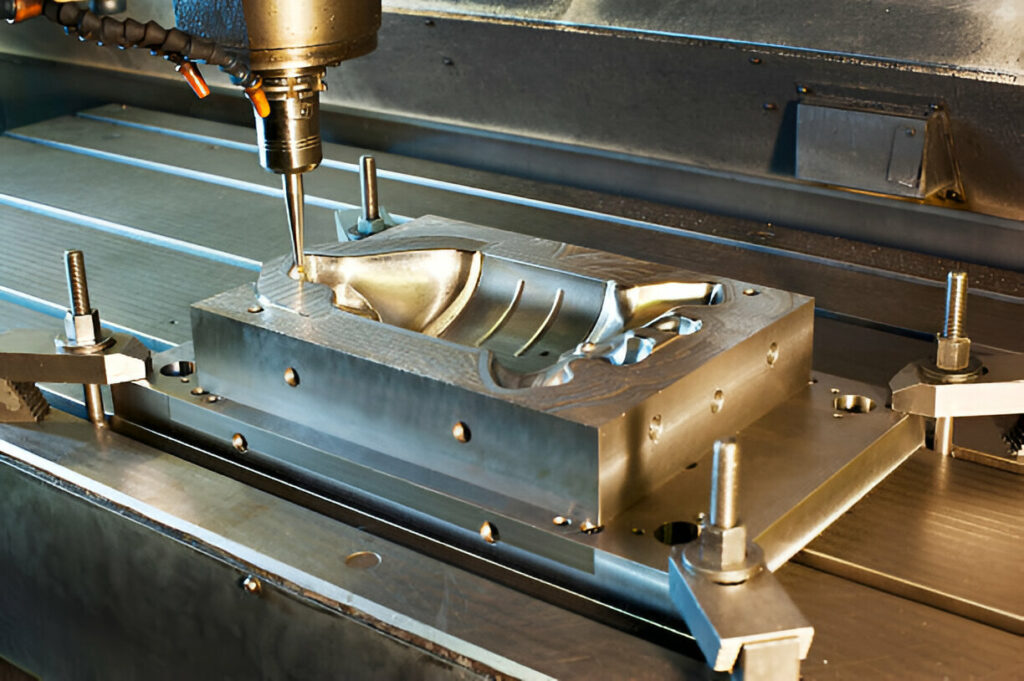
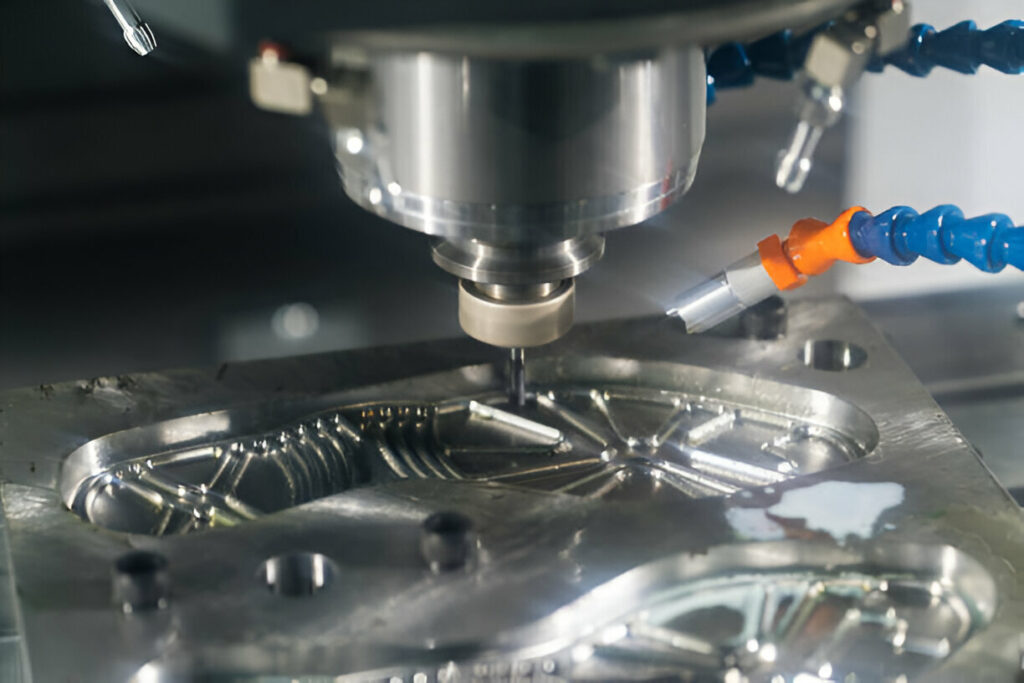
The Future of 3D Printing in Mold-Making
The adoption of 3D printing in mold-making is expected to grow as technology advances. Key future trends include:
1. Improved Material Selection
With continuous research, scientists will develop new materials with high heat resistance and durability. These advancements will enable manufacturers to use 3D-printed molds in large-scale production.
2. Hybrid Manufacturing Approaches
Hybrid manufacturing processes integrating 3D printing and conventional machine tools create more robust molds with enhanced geometric precision.
3. AI and Automation Integration
AI and automation will be applied to integrate mold design and production for the material loss due to human reasons being minimum.
Conclusion
3D printing molds have transformed traditional mold-making by offering low-cost, fast, and flexible solutions across industries. While CNC machining and injection molding remain relevant, 3D printing enables quick iterations, material savings, and intricate designs. Its ability to produce complex, lightweight yet strong molds benefits automotive, aerospace, medical, and consumer sectors.
However, challenges like limited printable materials, durability concerns, and high equipment costs persist. Hybrid manufacturing and AI-driven automation are rapidly addressing these issues, making large-scale production more viable.
With advancements in heat-resistant materials, smarter design tools, and automation, manufacturers can achieve greater efficiency and cost savings. As businesses seek faster market entry, 3D-printed molds will gain popularity, driving innovation.
0 Comments