Multi-cavity injection molds are of utmost need in plastic injection molding. Essentially, it’s a process performed to produce a range of plastic products with similar features and attributes. In this production process, several identical parts are manufactured in just one cycle using the multi-cavity mold. These molds increase productivity; reduce cost and ultimately maximize profits per unit time for any given manufacturing facility.
However, optimizing multi-cavity molds is no child’s play as ideal approaches must be used with precision, talent and practice that can only be accomplished if you possess adequate knowledge about materials and mold designing processes.
This article will tell you about different approaches for optimizing Multi-Cavity Injection Molds which help achieve top end quality plastic injection molded products at economical prices along with unsurpassed production reliability.
1. Optimize Mold Design for Uniformity
One of the biggest challenges with multi-cavity molds is making sure every cavity is the same. If there are any differences in cavity designs, cooling or filling, parts are going to differ from one another. To improve multi-cavity molds:
- Insure symmetrical mold design for filling balanced.
- Use same gate dimension so as no any pressure difference.
- Balance runner system to get the evenly material distribution.
- Uniform flow rate use for Injection Molding Materials.
2. Use Good Quality Material for Molds
Material of a mold determines its life and performance in general, high quality material means more life and less wear & tear. Commonly used materials for molds are :
- Hardened steel : High wear and corrosion resistance.
- Pre-hardened steel : Moderate production volume.
- Aluminum: It is cost effective and is good for prototyping.
- Beryllium copper: Mainly used in critical areas to enhance the thermal conductivity.
Selecting right material on the basis of production volume, plastic injection molding service requirement and type of plastic used will help improve the mold life.
3. Implement Proper Cooling System
Cooling is most important in multi-cavity Injection molds. If cooling is not as per requirement, then there will be non-uniform shrinkage, warpage and high cycle time. For proper cooling:
- Try to design cooling channels closest to the cavity surface.
- Utilize baffles and bubblers in molds with complex geometries.
- Conformally cool to gain better heat removal.
- Optimize the water flow rates to keep the temperatures uniform.
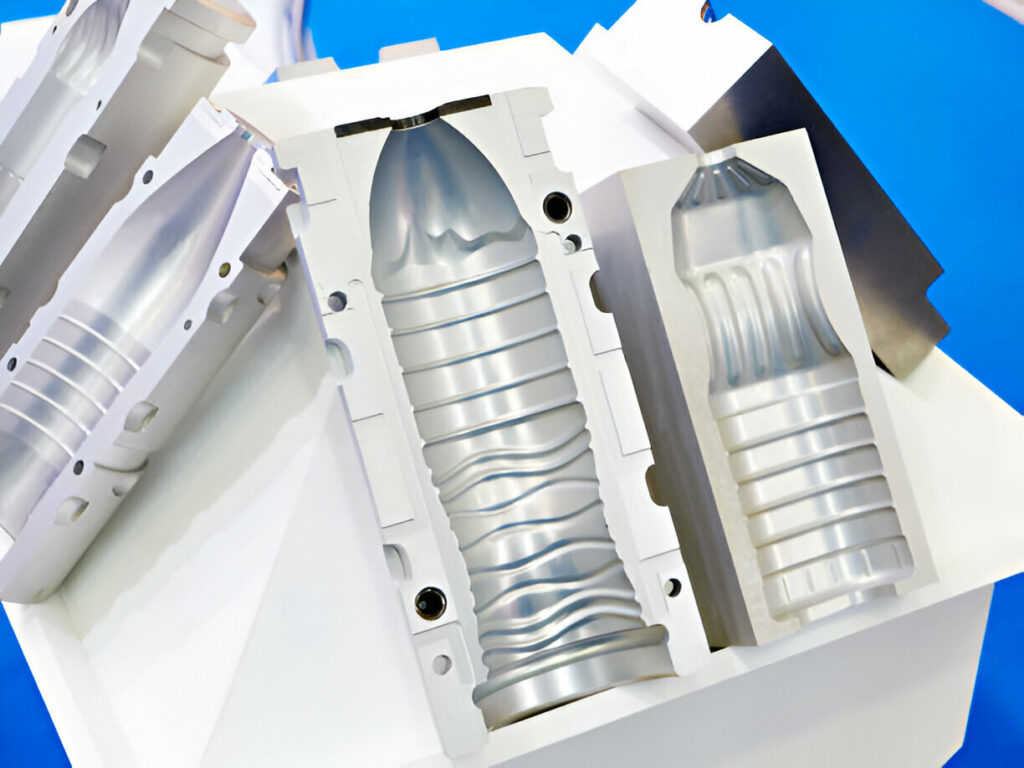
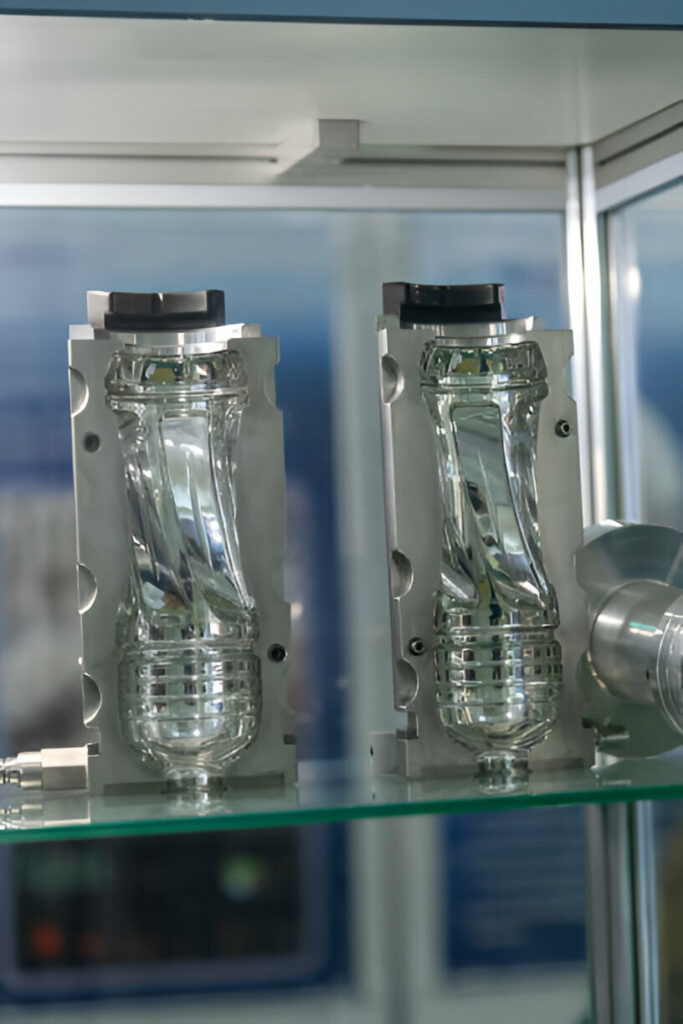
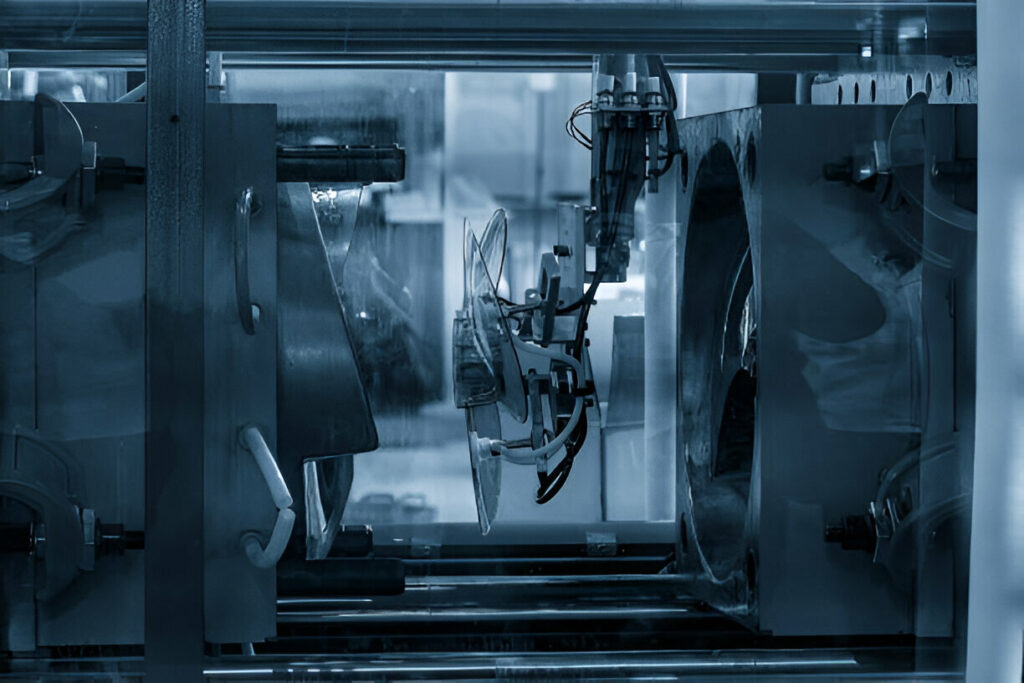
4. Improve Mold Flow Analysis
Material flow is king when it comes to creating a defect free part with plastic injection molding. Prior to building the production tool, you can run a mold flow analysis and find any issues up front. A few things you can consider are:
- Optimizing the gate location to avoid hesitation flow.
- Computer simulations air traps and weld lines detection.
- Increase or decrease the wall thickness to get a proper uniform distribution of material.
- Check the pressure and temperature sequence to make sure they are constant.
- Simulation tools can also help optimize vent designs and gas removal.
5. Improve Venting and Gas Removal
Trapped gases in multi-cavity molds can produce burns, voids, and incomplete fills. Vents should be designed at locations of critical flow.
- Using porous materials or vented pins to ease air evacuation, especially for the deep part sections.
- Correct setting of vent depth to avoid flash.
- Improved Venting leads to better injection molding products – less defects, improving part quality overall.
6. Select the Right Injection Molding Machine
Partnering with the right plastic injection molding company and machine is key to meet or exceed multi-cavity design goals. Factors to consider include:
- Clamping force- You should have enough force so that your mold will not separate.
- Injection pressure – You need to apply uniform pressure on all the cavities.
- Barrel Capacity: Match the shot size to minimize material degradation.
- Automation Integration: Implement robot systems to achieve faster cycles.
7. Consistent process control in manual hand.
Process stability is the first key to success towards high quality output. Critical process parameters to be considered for monitoring are:
- Temperature – stable melt and mold temperatures are needed.
- Injection speeds – for a balanced flow of material.
- Holding pressure: To maintain uniformity of packing in the cavities.
- Cooling time: Depends upon material and mold design.
Advance process control system, real time monitoring and AI based automation can increase the efficiency of process to repeat same.
8. Use high-performance injection molding materials
Material is very important, to keep the part quality always the same. The best Injection Molding Materials for multi-cavity molds are:
- ABS: Is tough and impact resistant.
- Polypropylene (PP): Is lightweight and has high flexural strength.
- Polycarbonate (PC): good clarity and is tough.
- Nylon: strong, tough and wear resistant.
- PBT: High strength and dimensional stability.
High quality, consistent viscosity with thermals material properties, better moldability and defect less.
9. Optimize Gate and Runner Design
Both gate design and runner design determine how the material gets into the mold. In order to get better performance:
- For better control over material flow and reduced material wastage, use a hot runner system.
- Optimum diameter of runners should be designed geometrically to have balanced material flow.
- Choose right kind of gates i.e. pin, edge or sub-gates.
- Maintain equal length of runners for same fill.
A well-optimized gating system not only improve the quality of part, but also decrease the scrap rate in plastic injection molding process.
10. Regular Mold Maintenance and Cleaning
Preventive maintenance is important to obtain the best performance from a mold and to maximize production output. These are some best practices:
- Clearing cavities and vents after each production.
- Lubricating parts so they are not caught up as much.
- Checking for any blockages in the cooling channels.
- Inspecting the part for any signs of corrosion or damages.
- Keep Warpage and Shrinkage to a Minimum
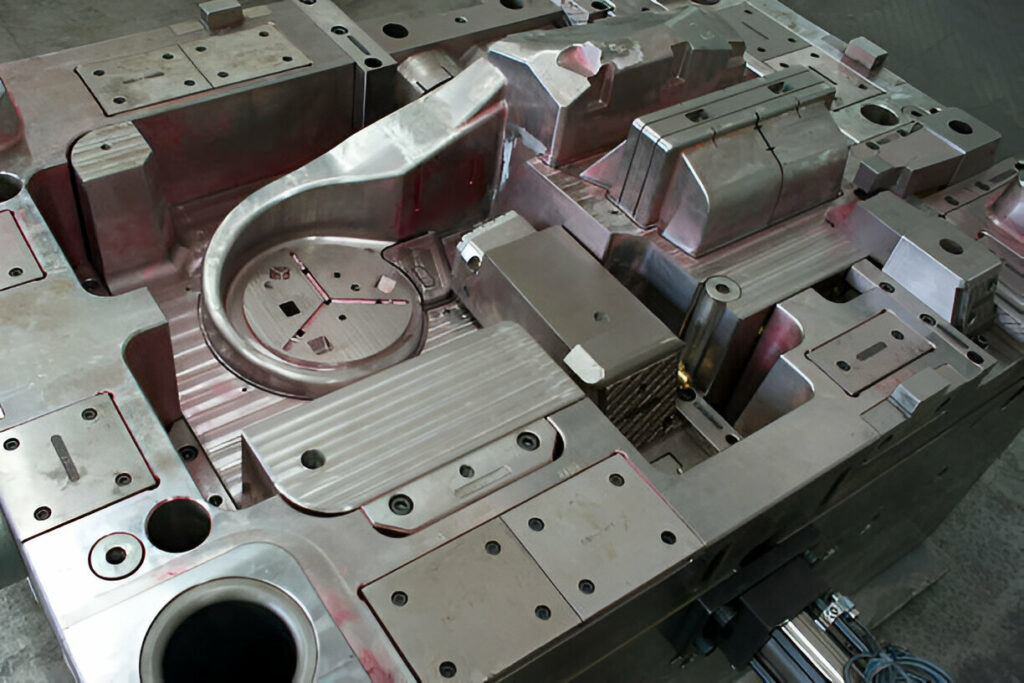
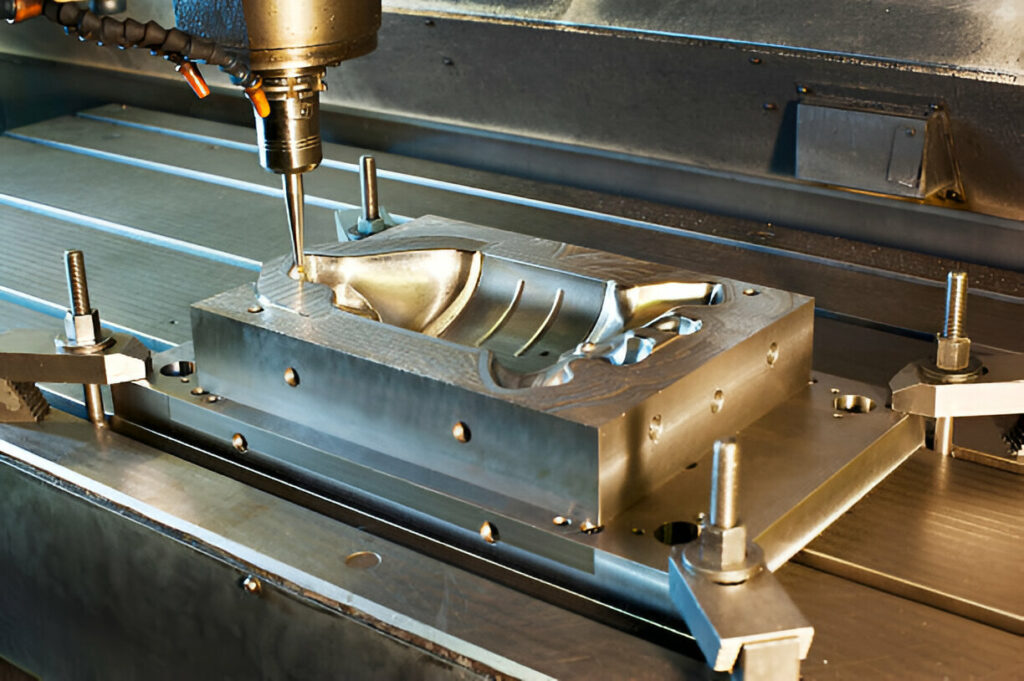
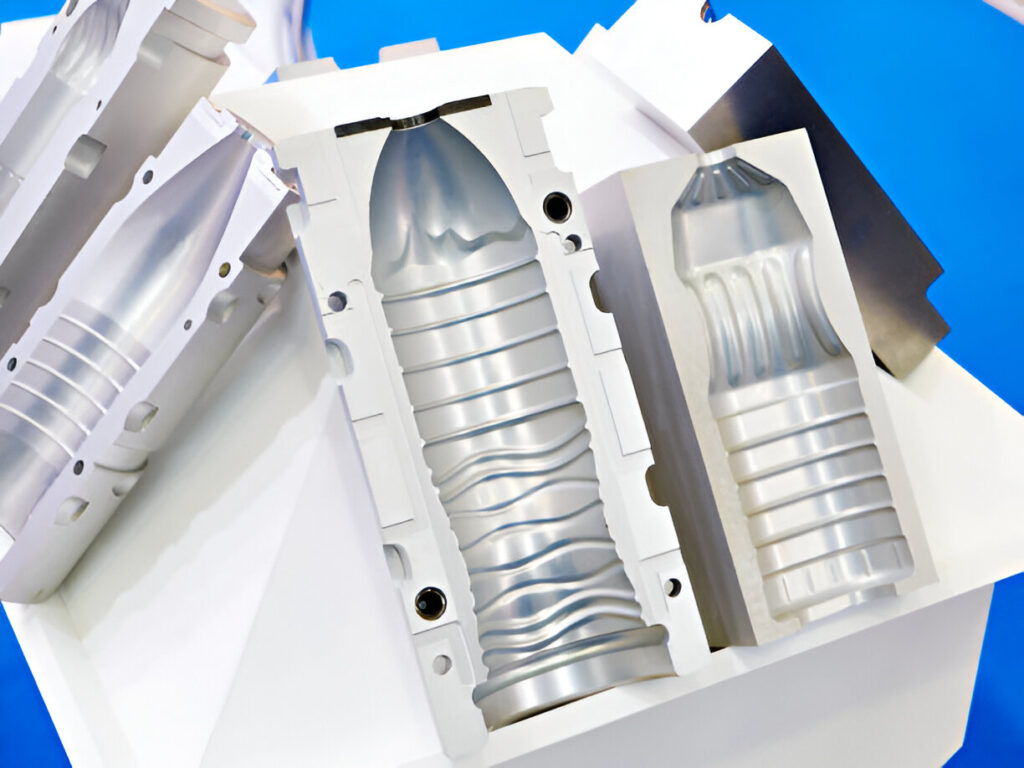
11. Keep Warpage and Shrinkage to a Minimum
Warpage and shrinkage defects are often highly-cavity dependent. To minimize the warpage and shrinkage defects, design the cavity by following:
- Uniform wall thickness to avoid stress concentration
- Optimize the cooling rate in order to have solidification without shrinkage.
Choose materials with low shrinkage rates, for example low carbon steels shrink by a thousandth of the area when cooled from 1200 degrees Celsius to room temperature. When the material cools adjustments occur so that it fits to the contour of the mold which can cause defects or deform a part you are trying to create.
12. Using Automation to Be Efficient
You can conveniently increase the multi-cavity molds with the aid of automation, and there are many benefits along with it:
- Robotic part handling for faster cycle times.
- AI monitoring for consistent process control.
- Lower labor costs and reduced human efforts.
- Improved quality inspection using vision systems.
Automating your plastic injection molding process will help you increase your productivity to become more competitive.
Conclusion
Improvement in multi-cavity injection molds can be done by making use of precision engineering, right material, better cooling and by controlling overall process. This will help to produce more production, less defects also economical high quality plastic injection molding products.
If you are service provider or product manufacturer these methods are really helpful in order to improve your business performance as well cost saving and standardization of products for a long run.
0 Comments