Injection Molding Manufacturing is an important manufacturing process used in various industries. These include the automotive industry, medical equipment manufacturing, making consumer goods and packaging. It is important to find a good injection molder that you can partner with to realize success in your business. Here are some of the things that you have to factor out when finding an injection molder.
1. Assess Your Product Requirements
Before you choose a factory, you should have an outline of your product specifications, including:
- Material Type – are you looking for thermoplastics, thermosets, elastomers or biopolymers.
- Production Volume – Low, medium, or high volume.
- Precision & Tolerance – Required dimensional accuracy & quality standards.
- Design Complexity – This includes the mold design, number of cavities and part geometry. The more you know about this the easier it will be to hone in on potential manufacturers with the right capabilities.
2. Evaluate the Factory’s Experience & Expertise
The more experience a factory has, the better equipped they are to navigate challenges or unexpected issues that may arise during production. Additionally, an experienced factory is often more reliable and financially stable.
However, keep in mind that some newer factories may still have modern equipment and highly skilled staff members despite being younger than other factories.
In general, it’s best to look for a factory that has had at least 10 years of operation.
- Years in Business – Seek out manufacturers with a long history of success in injection molding.
- Industry Specialization – Work with a factory that has experience serving your industry (automotive, medical, electronics, etc.)
- Past Projects & Clientele – Check out their portfolio to get an idea of the quality and complexity of work previously undertaken by the vendor.
- Certifications – Ensure that they comply with industry standards for example ISO 9001, ISO 13485 (medical), IATF 16949 (automotive).
3. Check Manufacturing Capabilities & Technology
Advanced technology ensures high precision, efficiency, and cost savings. Assess factory’s capabilities in:
- Injection Molding Machines – Look at the range of machines in terms of tonnage, automation and accuracy.
- Material Handling & Processing – Can they handle a variety of resins, additives and colors.
- Mold Fabrication & Maintenance – Ensure they can design, build and maintain high-quality molds.
- Secondary Services – Can they provide additional secondary services such as over molding, insert molding, ultrasonic welding or assembly.
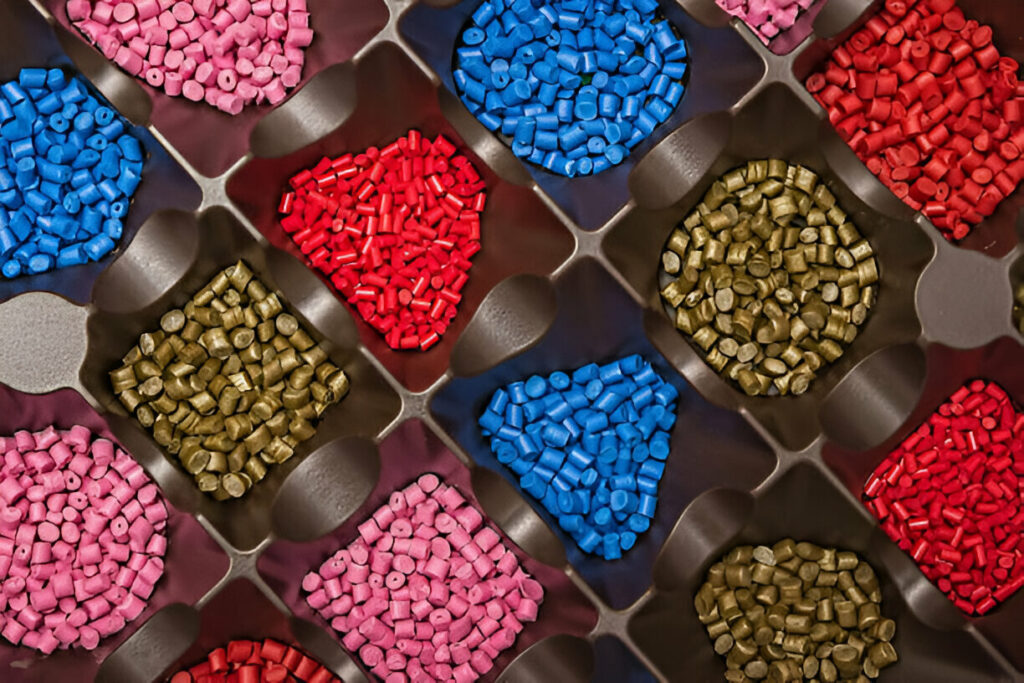
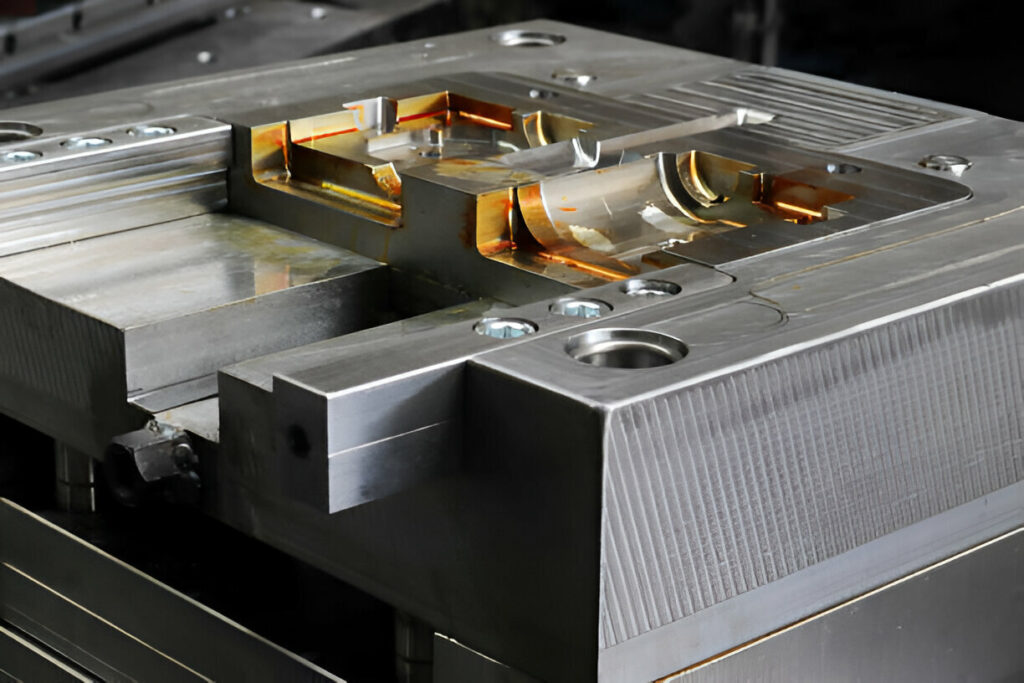

4. Quality Control & Certifications of Injection Molding Manufacturing
Quality control is important when it comes to manufacturing. Find out about the factory’s quality control:
- Inspection & Testing – Check if they have capabilities such as CMM (Coordinate Measuring Machine) inspections, X-ray testing, pressure testing etc.
- Defect Rate & Quality Reports – Request for defect rates and also sample quality control reports.
- Certifications – Ensure they meet international quality standards such as Six Sigma, GMP or UL certification.
5. Lead Times & Production Capacity- Evaluate
Production efficiency affects the timely delivery of products. Check how fast they can design and make molds.
- Lead Time for Tooling & Production – How quickly can they design and make molds.
- Scalability – They should be able to manage increased production volumes.
- Supply Chain Efficiency – Understanding their raw material supply chain stability. We wouldn’t want delays because mill shut down.
6. Review Costs & Pricing Structure of Injection Molding Manufacturing
Pricing is a major factor when choosing an injection molding manufacturer. Consider:
- Tooling Costs – Compare the costs to manufacture the mold and the amortization possibilities.
- Per Unit Cost – Compare the cost per part related to material, complexity and volume.
- Hidden Costs – Check for additional charges like setup fees, design modifications and shipping.
7. Check Compliance with Environmental & Safety Standards
Sustainability and safety are growing concerns in manufacturing. Be sure that the factory meets the following:
- Environmental Regulations – Ensure compliance with RoHS, REACH and ISO 14001.
- Waste Management & Recycling – Enquire if they have eco-friendly waste disposal and recycling practices.
- Workplace Safety – Ensure compliance to OSHA, ISO 45001 and local labor safety laws.
8. Communication & Customer Support Assessment
A trustworthy factory should include good communication and support features such as:
- Responsive Customer Service – Inquiries and technical support shall be responded to very quickly.
- Transparency in Operations – Purchase from manufacturer who agree to give real-time production update.
- After-Sales Support – Check for warranty period offered, maintenance support and defect resolution mechanism available.
9. Visit the Factory for On-Site Evaluation
If possible, visit the factory to assess:
- Facility Infrastructure – Check cleanliness, orderliness and conditions of the machines.
- Workforce Skill Level – Note the skill level of the workers and training programs that are in place.
- Real-Time Production Processes – Analyze how well operations and production workflows are working.
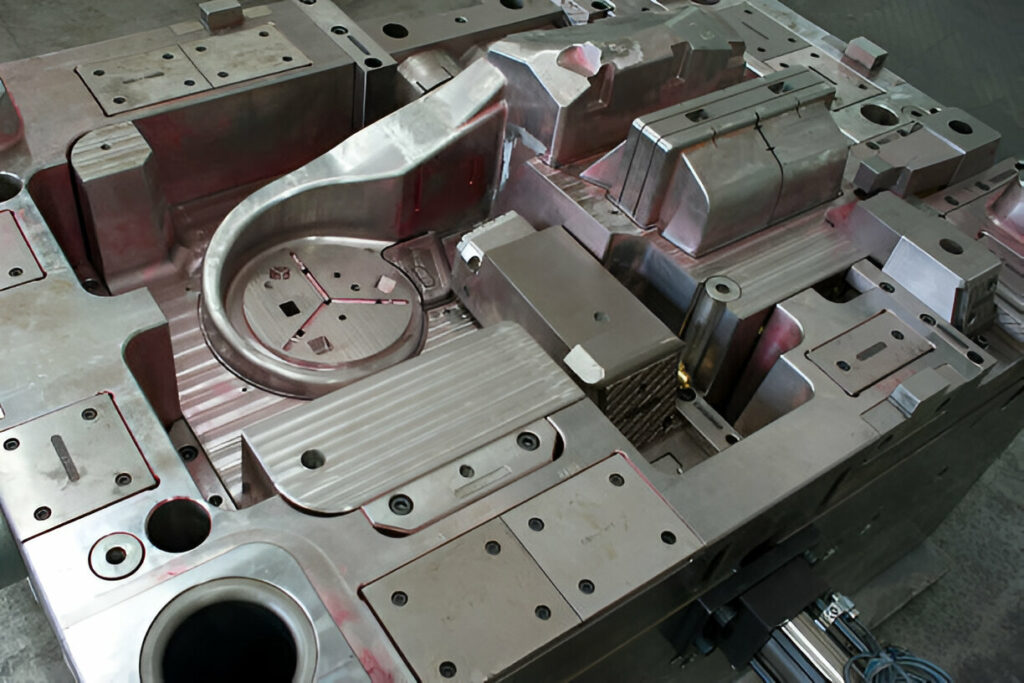
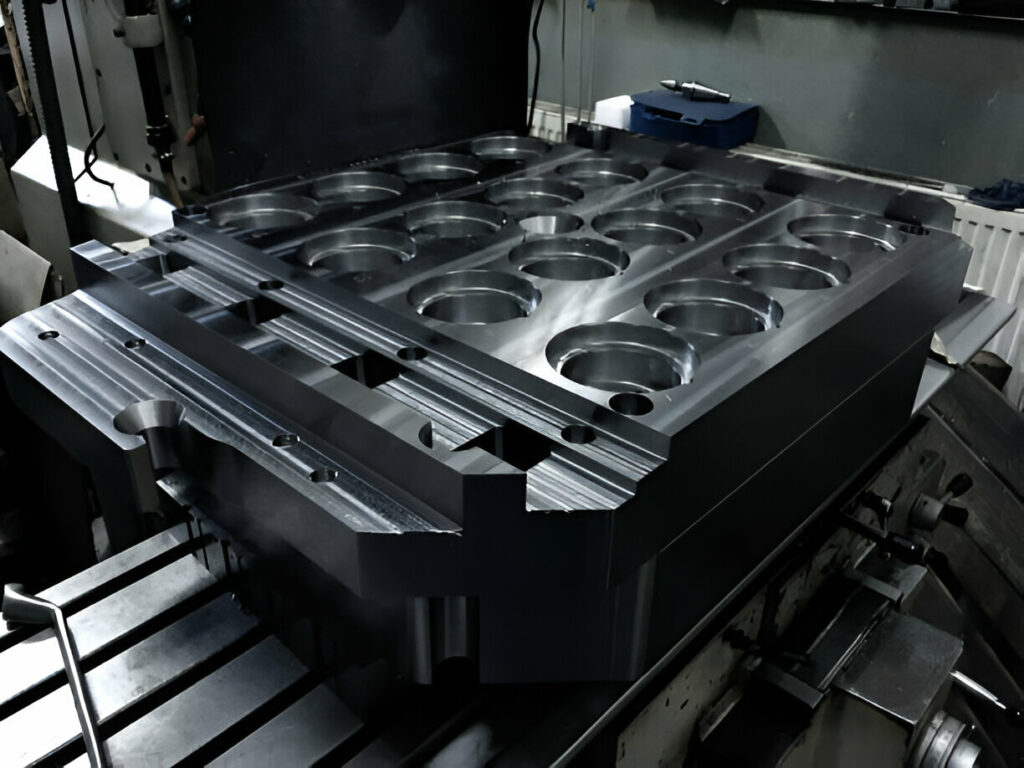
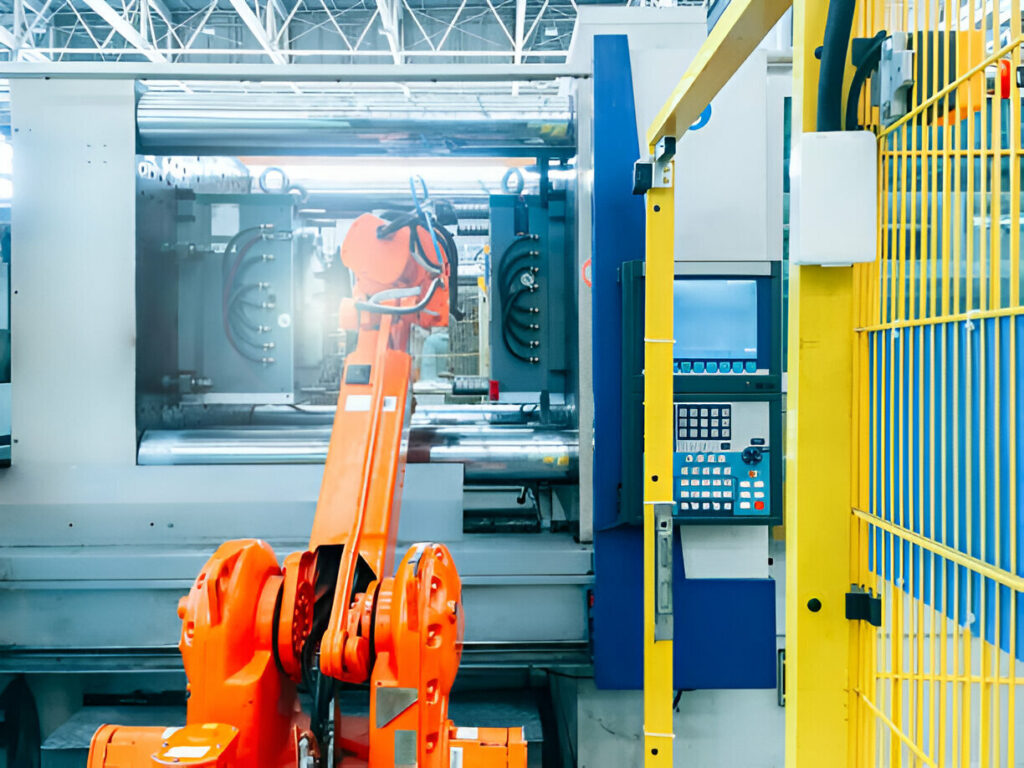
10. Read the Customer Reviews & References
Go through online reviews and ask for client references to get an understanding of:
- Reliability & Timeliness – Feedback relating to on time deliveries and quality of production.
- Customer Satisfaction – Overall feedback from past clients of the manufacturer.
- Conflict Resolution – How the manufacturer handles complaints and defects.
Conclusion
Choosing the right injection molding manufacturing factory is a crucial decision that will impact your business for years to come. To help you decide on the perfect partner, you will need to consider many points including experience, manufacturing capabilities, quality control, lead times, cost structure and compliance with environmental/safety regulations.
A good manufacturer should be able to provide high-quality products and help you increase efficiency, lower production costs and support long-term growth. It’s important to do extensive research online or even better yet take a trip out to visit them personally before making any decisions. Contact their customers if possible too as they would have already gained firsthand experience with these manufacturers. The right factory will ensure superior product quality, operational efficiency and market competitiveness.
0 Comments