Plastic injection molding is one of the most versatile and widely used manufacturing processes in the world. From automotive text to household items or mass production. The main purpose of all productions that involve plastic is to have high precision, to be cost effective and to produce plastic components in very large quantities. In this article, you will be told how plastic injection molding works and how this process is carried out. We will try our best to explain it to you step by step in detail.
It is very important for beginners to know the phases of plastic injection molding work. What are the steps that are taken and in what ways is this process executed and how is the establishment made till the market?
1. What is Plastic Injection Molding?
Plastic injection molding is a manufacturing technique that involves injecting molten plastic into a cavity and creating a specific design. The process is highly efficient in producing complex geometric shapes that are repeated and formed rapidly. Therefore, the material becomes extremely important and these materials are thermoplastic and thermosetting plastics.
2. Key Components of the Injection Molding Process
First it is important to know the steps involved in injection molding. I would like to tell you everything that is involved in it such as:
- Injection Molding Machine : This machine compromises of three sections which include injection unit, closing unit and mold.
- Mold : Steel and aluminum form a custom-designed tool that defines the shapes resulting in the final product.
- Raw Material : Plastic pellets and granules are typically thermoplastics such as ABS, polyethylene, and polypropylene.
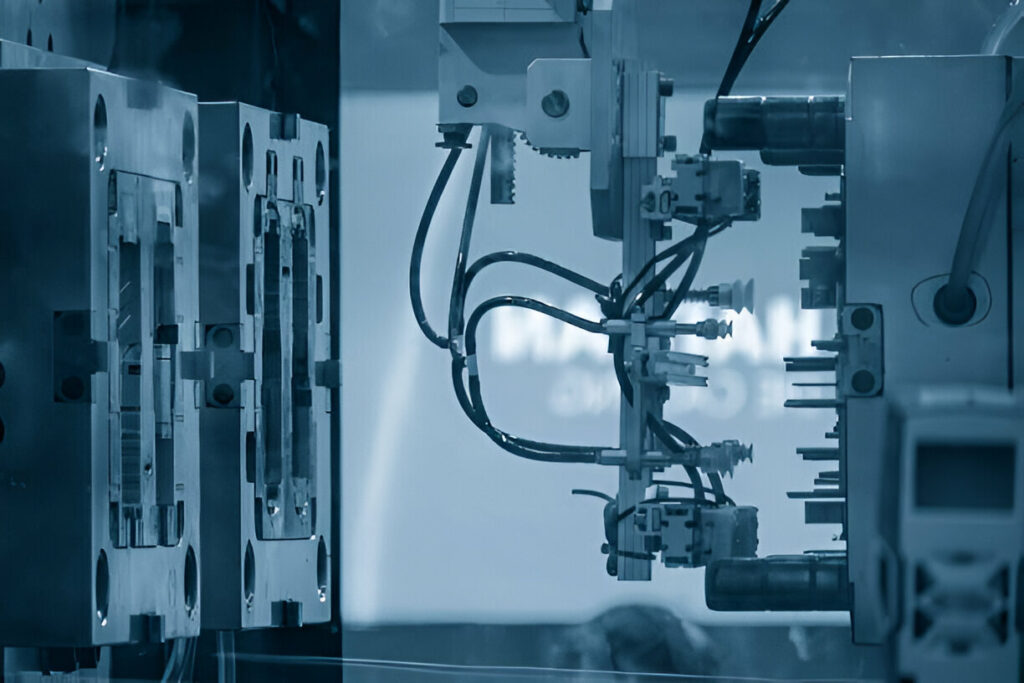
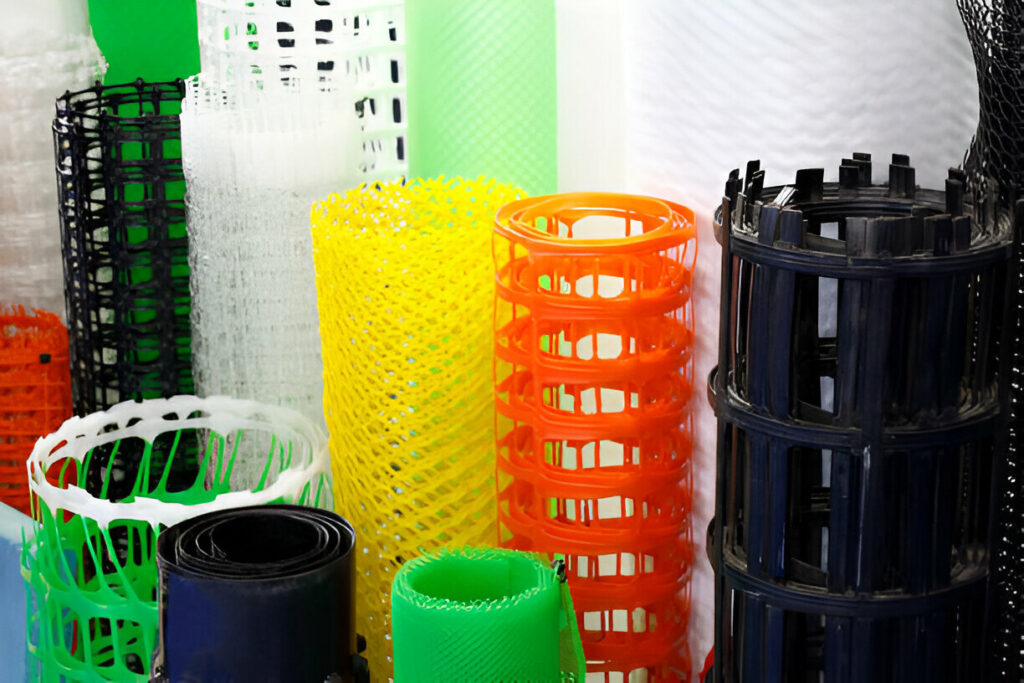
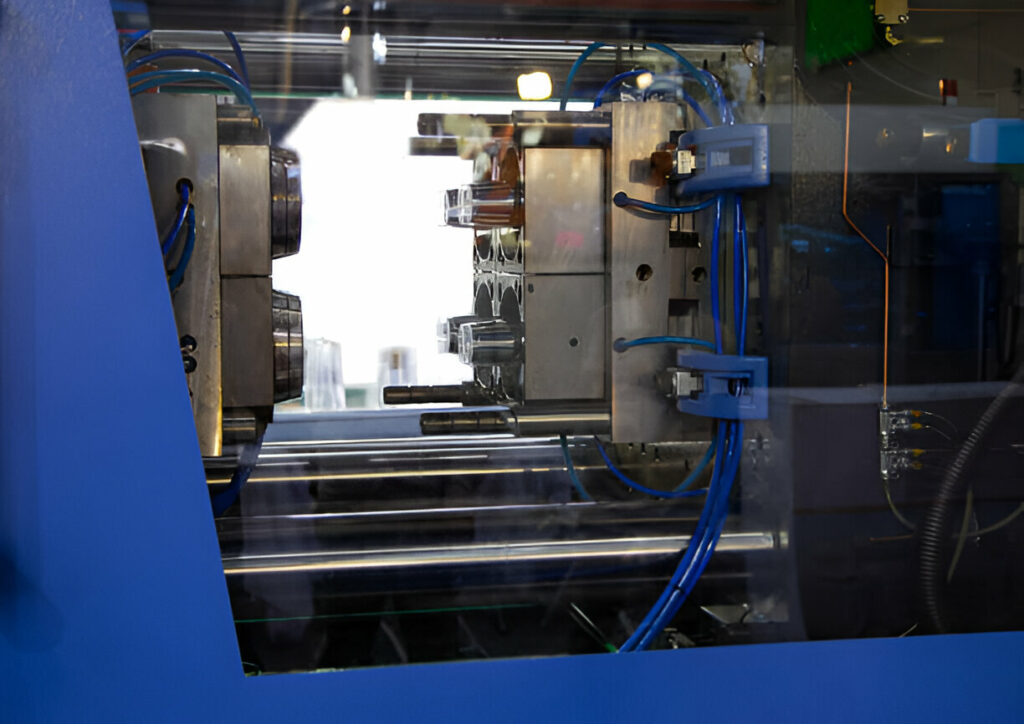
3. The Step-by-Step Process of Plastic Injection Molding
Step 1: Material Preparation
This process begins with selecting and preparing the raw material, which includes plastic pellets and granules. This material is then fed into hoppers, undergoes a thorough treatment and removes moisture from the material to prevent it from affecting the molding process.
Step 2: Melting the Plastic
The machine transfers the raw material from the top to the injection unit, where the barrels with a reciprocating screw mix and melt the plastic by heating it to its melting point.
- Heating Zones : Several heated zones divide this barrel, and each zone must maintain a specific temperature to ensure all substances melt uniformly.
- Reciprocating Screw : The screw not only melts the plastic but also bends it reversibly, allowing pressure to inject through it into the material.
Step 3: Mold Clamping
The mold concept requires you have to keep one cavity side and another core cavity side. These have multiple clamps that are tightly clamped together so that they can be clamped to the clamping unit that is inside the plastic injection molding machine. Proper clamping ensures that the mold will remain closed under high injection pressures.
- Clamping Force: The air force applied to the cloning unit depends on its size and the complexity of the mold.
4. Advantages of Plastic Injection Molding
- High Efficiency: This process is very sustainable for mass production and that is why we use it. It executes the production in very few seconds.
- Design Flexibility: Designers can create detailed shapes, no matter how complex, and easily achieve or reduce them very effectively in plastic injection molding.
- Material Variety: Here we used in the wide range of plastics. These include some additional properties that enhance the durability and strength of the plastic.
- Cost-Effectiveness: Although the initial mold creation is an expensive task, when we look at it in large quantities, it proves to be very effective and can reduce your mass production cost significantly.
5. Challenges and Limitations
- High Initial Investment: This would have been highly prohibitive of cost designing and manufacturing molds.
- Material Waste: Though minimized, some waste occurs during the trimming and purging processes.
- Defects: Warping, sink marks, or short shots can occur if you do not optimize the process.
6. Applications of Plastic Injection Molding
Plastic Injection Molding products are being used in wide range of applications like some of the industries which we would like to explain to you are given below.
- Automotive: Dashboards, bumpers, and interior trims.
- Medical: Syringes, surgical instruments, and diagnostic devices.
- Consumer Goods: Toys, containers, and electronic housings.
- Aerospace: Lightweight components for aircraft.
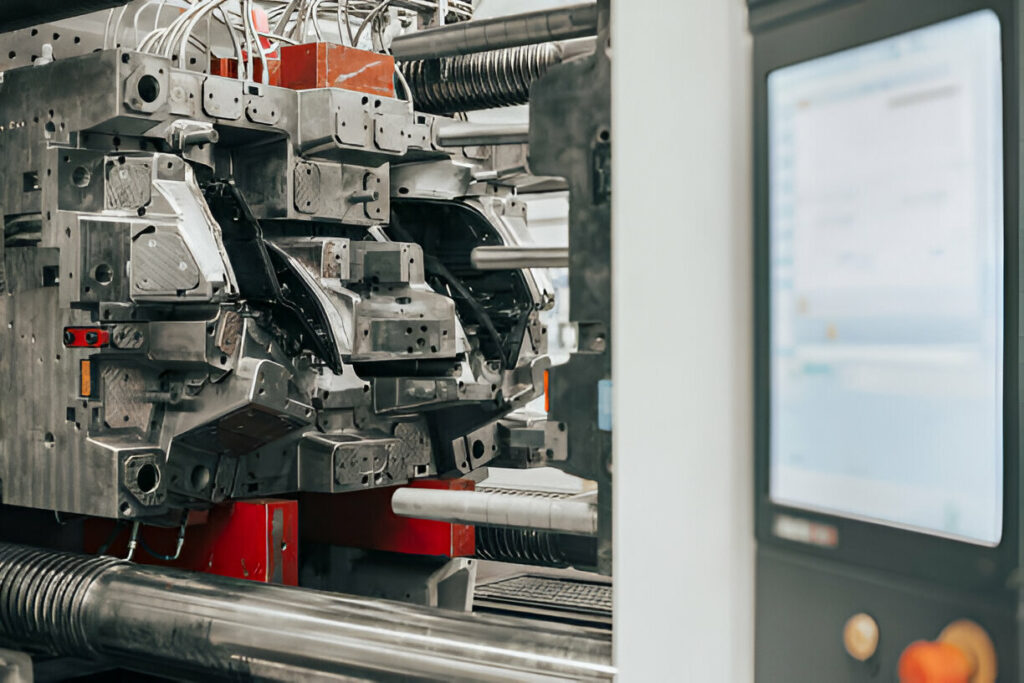
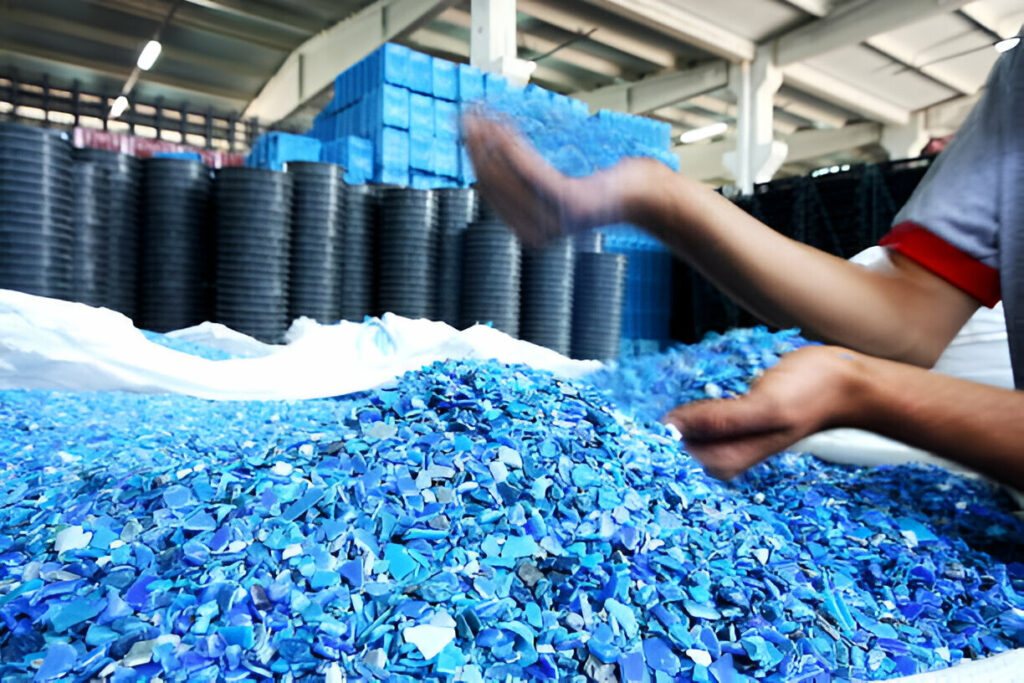
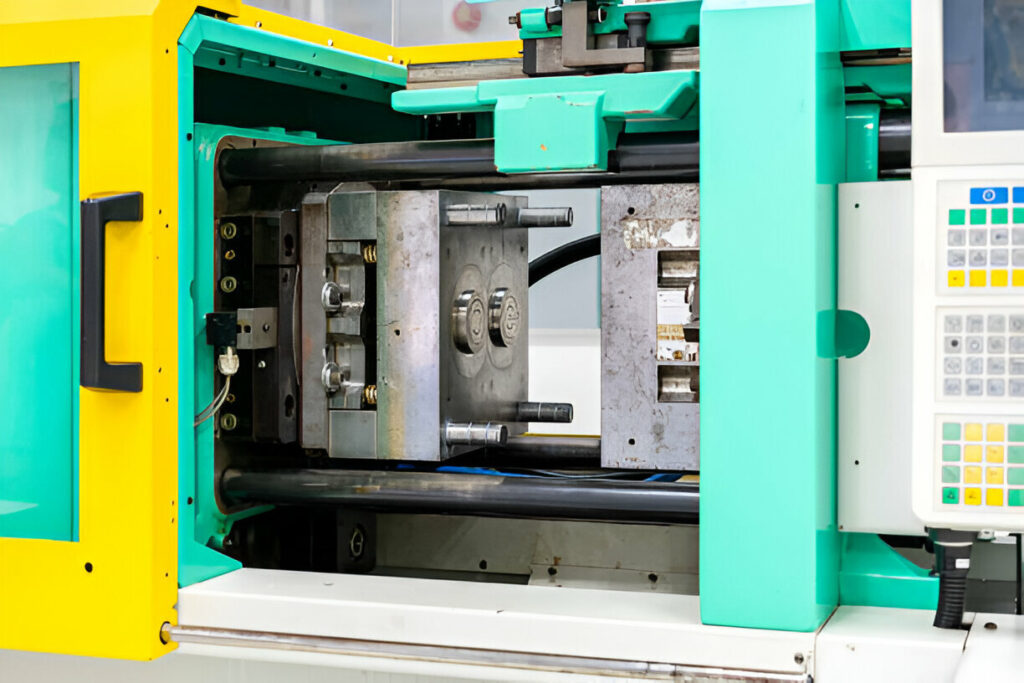
7. Tips for Optimizing the plastic Injection Molding Process
- Material Selection: You have to select the right plastic that you will used in the application. And make sure that it have tendency to sustainability for long period of time.
- Mold Design: Check that the mold is well-designed and don’t have any kind of defects.
- Process Parameters: Optimize temperature, pressure, and cooling time for consistent results.
Conclusion
Plastic injection molding is a highly efficient and versatile manufacturing process because it is making parts in a very effective way with revisions. There are many steps to understand this. But there are many advantages, challenges and applications in this process, which gives very good performance to the business. According to today’s technology and we all know that every industry needs plastic, so for this we have to move with future prospective and make the equipment highly qualified.
That is why we are innovating, so that work can be done on the looks of future plastic injection molding and their decision making like strength and sustainability. So that cost effectiveness can be reduced and most businesses can afford it.
I hope you must have gained a lot of knowledge from this article. But if you want to know in brief, then you will have to read all our other blocks and articles so that we can give you a lot of explanation there. Visit once related to each topic.
0 Comments
Trackbacks/Pingbacks