Manufacturing techniques have evolved significantly over the past few decades with new technologies that offer flexibility, cost savings and efficiency. Along with all the advantages and disadvantages, Injection Molding vs 3D Printing have played a very effective role and have also become popular in a wide range, their methods are very good in production. Both methods serve various purposes and operate on creating objects using difficult principles. They also have different advantages and limitations.
After understanding all these things, the difference between 3d printing vs injection molding helps the business to go ahead and helps the engineer to decide which one will be better for the project. They have different factors like production volume, complexity, Cost, Material requirement and lead times.
3D printing offers of 1-2 week, making it ideal for rapid prototyping and for designs with frequent changes. This process is also able to produce relatively small plastic parts and components as well as being ideal for complex or intricate designs. It is, however, best suited to print parts for low production runs of 100 parts or fewer, as it can be costly in terms of time and money for larger runs.
1. 3d Printing
3D printing is an additive manufacturing process that involves building parts layer by layer using digital 3D models. It utilizes many materials such as plastics, metals, ceramics and biological substances to create complex structures. This technology has revolutionized what photo type and customization and even production do in a certain industry. Let us explain things in brief:
How It Works:
- Mold is made up of metals like steel or aluminum, and designed is made as per the requirements then the final product will be produced.
- As I have said in above that molten plastic is injected in the mold at the high pressure.
- Then, plastic fills the mold cavity and get the right shape.
- Let the plastic cools and solidifies, then we will open the mold and get the final product.
Advantages
Each are explained below:
- 3D printing has a low entry cost. A desktop 3D printer and supply of materials is cheaper than injection moulding equipment. The proliferation of open-source software and hardware can also provide ongoing support at little or no cost
- Easy to make design changes. Since it is an additive process, 3D printing allows you to make design changes even during production, saving time and money on a run of components that may have a flaw. Being able to pause mid process and make design changes means that you do not need to start the entire production run from the start. 3D printing is also good for quick prototypes as there is little set-up required ahead of production
- Good for intricate designs. Because it produces parts layer-by-layer, 3D printing is perfect for producing complex or intricate designs with detailed infrastructures.
Disadvantages
- Despite the set-up being relatively fast, 3D printing is a slow production method. The CAD-based, detail-oriented process limits how many parts can be produced at once, with most printers only capable of building one or two items at a time.
- 3D printing is unable to produce larger items as the process is limited by the size of the printing area. The design becomes increasingly unstable if parts hang off the edge of the printing area, so while large scale 3D printing is possible, it is not the best use of this process.
- Rough finish. The finish of 3D printed parts is rough due to the layers being additively built, no matter how fine the detail is. As a result, post-build smoothing is required should you need a smooth finish.
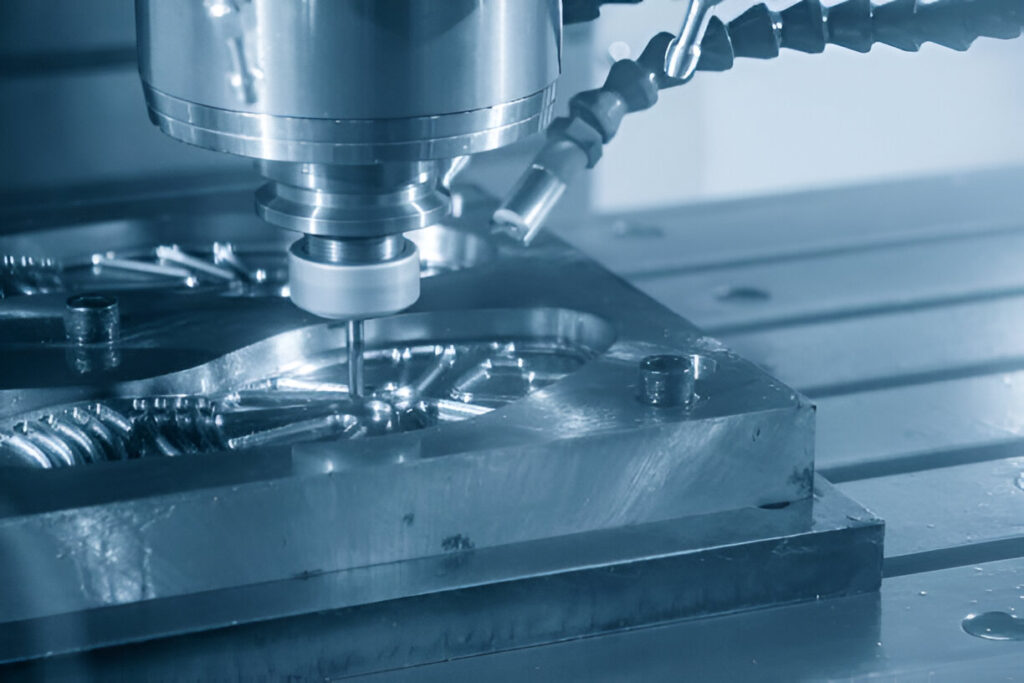
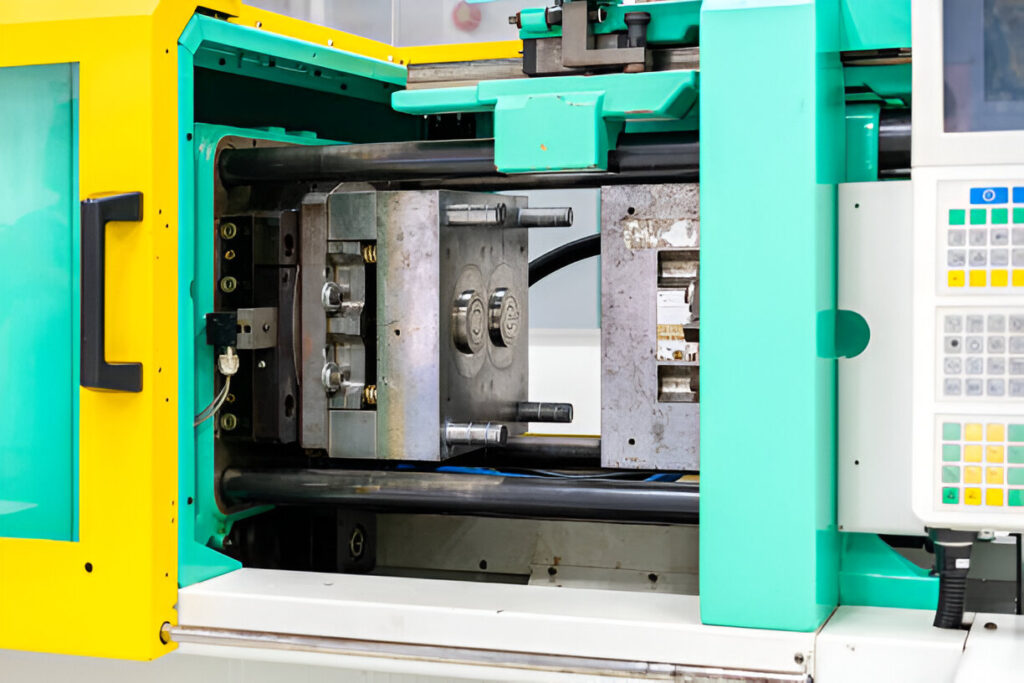
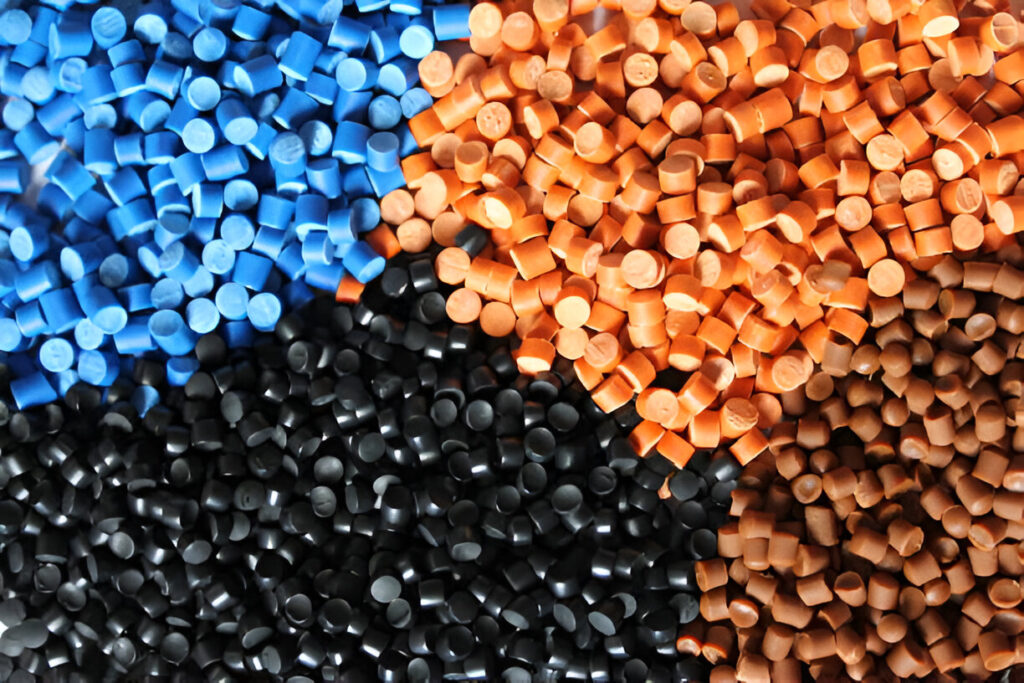
2. Overview of Injection Molding
Injection moulding has long turnaround times to prepare for the creation of parts (5-7 weeks even for simple parts), which means it is not well suited to frequent design changes. However, despite the long turnaround times this process is ideal for producing parts in high volumes (1,000+ parts per run). The mold tool is also fine for producing large or small components of any complexity.
Advantages
- Able to mass produce a high volume of parts. Injection moulding can use a high number of molds at once, meaning that it is more cost-effective for producing a large number of objects.
- Enhanced strength of objects. Injection molded parts are created using a single layer of poured material, eliminating any fissures or other areas of weakness. This process also works for dense materials, such as concrete, that would need to be diluted or modified for 3d printing.
- Minimal wastage. Because injection moulding involves pouring material into a mold, it uses exactly the amount of material required for the design. This means this manufacturing method is ideal for mass producing objects cost-effectively.
Disadvantages
- Limited design capabilities. The use of a mold means there are design limitations placed upon this production method. Right angles in the design can make it difficult to remove an object from the mod without it breaking. Injection moulding is also not well suited to creating precise and delicate designs that can stand on their own.
- Difficult to correct mistakes or change designs. Because of the long set-up times associated with injection moulding it is difficult and expensive to rectify any mistakes in the design. The mold needs to be completely remade to change designs or fix problems, while any objects produced would need to be scrapped.
- Expensive entry costs. Injection moulding machines are expensive, often costing upwards of six figures. Designed for industry, these systems are not really for hobby use as there is the cost of making molds, materials and design prototyping to take account of in addition to the original machine cost.
Injection Molding vs 3D Printing: Key Differences
Production Process
- 3D Printing: Inside this, some objects are made which are layer by layer and they include plastic, metals and resin materials.
- Injection Molding: It involves creating a mold as molten materials are injected inside it which is sustainable for mass production.
Cost
- 3D Printing: There is no higher cost of any kind in it but lower initial cost is invested and no tooling of any kind is required. Cost effective for small batches and one off design.
- Injection Molding: Higher initial cost investment resulting in lower per-unit cost charged on tooling for high-volume production.
Speed
- 3D Printing: Faster for prototypes and small batches and it creates multiple units which takes a lot of time.
- Injection Molding: It works very fast for mass production once the mold is created.
Material Options
- 3D Printing: There is a wide variety of materials available but limited in mechanical properties when we compare injection molded parts.
- Injection Molding: It supports a border range of materials that offer superior mechanical and thermal properties.
Complexity
- 3D Printing: Can easily handle complex geometries and custom designs without any additional cost.
- Injection Molding: Complex design requires intricate molds require increasing in cost and production times.
Applications of Injection Molding vs 3D Printing
3D Printing Applications
Prototyping
- It is ideal to create a quick and cost effective prototype which is designed and all its functionalities are working through testing.
- There are some big industries in which they are used such as automotive, aerospace and consumer electronics.
Medical and Dental
- Custom prosthetics, implants, dental crowns, and surgical guides.
- Enables precise customization and rapid productions.
Aerospace
- Produces lightweight materials and complex components used in aircraft and spacecraft.
- It will reduces material waste compared to traditional methods.
Consumer Goods
- When it comes to consumer goods, it includes custom jewelry, eyewear and personalized accessories.
- Facilitates the production of small batches that are unique designs.
Injection Molding Applications
Mass Production of Consumer Goods
- Mass production takes place inside it such as bottles, caps, toys and kitchen sets.
- As long as you are completely injured, we will send your uniform in large quantity.
Automotive Industry
- We will be manufacturing dashboards, bumpers and other types of components with high durability and precision.
Electronics
- We will produce casings, connectors and other components used in devices such as smartphones and computers.
Medical Devices
- As we know that in medical equipment, we make maximum products such as syringes, surgical instruments and some medical equipment parts.
- It is our endeavor that all the medical equipment banks are sending from our side to you, it should be with complete hygiene and there should not be any standard deviation in quality.
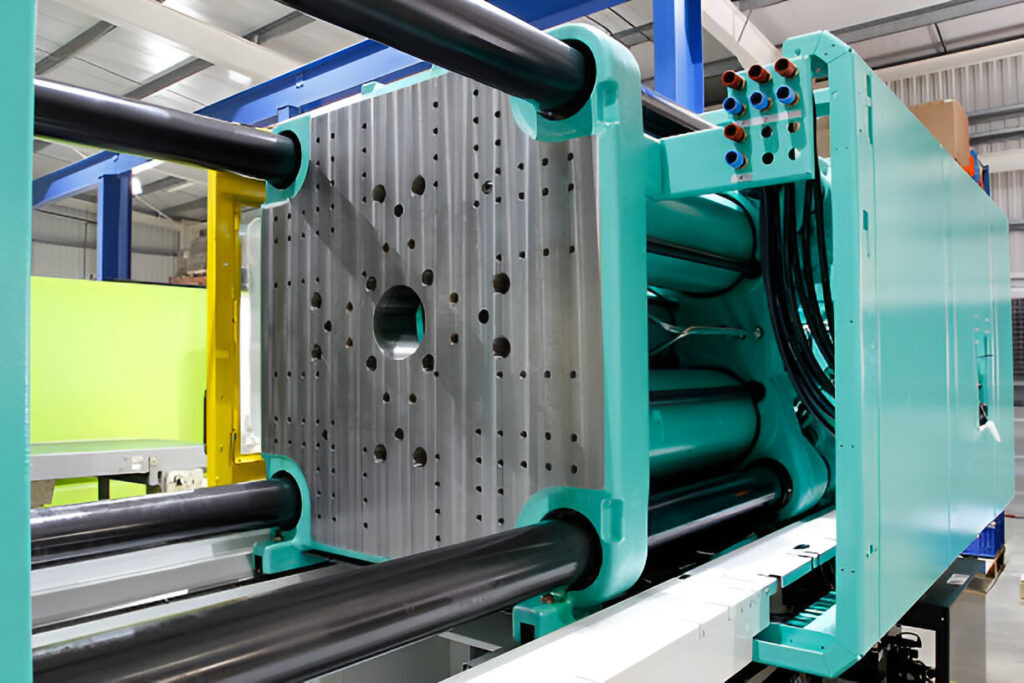
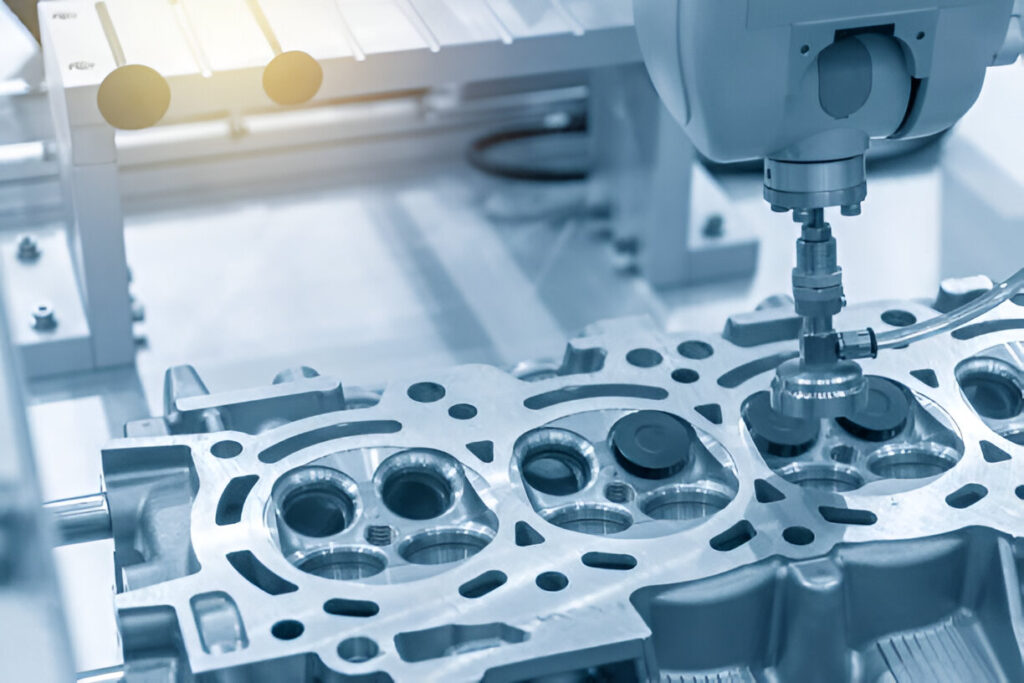
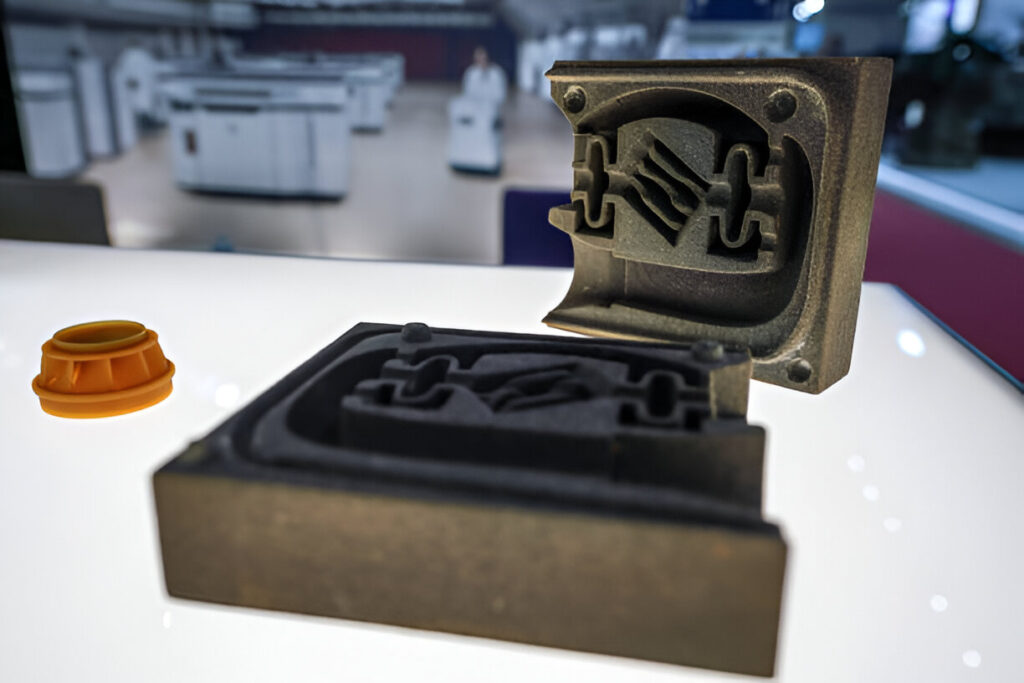
Conclusion
Both 3d printing vs injection molding offer district advantages depend on their application, production volume, and budget. While 3D printing excels design flexibility rapid prototyping and low volume production Injection Molding is a clear choice for high volume manufacturing.
If we need to choose between the two, factors like complexity, production volume, and material requirements should guide the decision. In many cases, a combined approach works best—using 3D printing for initial prototypes and injection molding for final mass production.
Both technologies are rapidly advancing, leading to more efficient manufacturing processes. Innovation is driving down costs while improving durability, accessibility, and overall efficiency.
0 Comments
Trackbacks/Pingbacks