Plastic injection molding is one of the most popularly used manufacturing processes for the production of plastic parts. A wide variety of products are manufactured using plastic injection molding, which vary greatly in their size, complexity, and application. The plastic raw material is melted in the injection molding machine and then injected into the mold, where it cools and solidifies into the final part. Some of the common materials used in injection molding are Acrylonitrile Butadiene Styrene (ABS).
1. Acrylonitrile Butadiene Styrene (ABS)
Properties:
- It can bear the heavy crash.
- Good heat and chemical resistance
- Excellent mechanical strength and toughness
- Easily machinable and finish able
Advantages:
- Widely available and economical.
- Good dimensional stability & stiffness.
- Lightweight and durable.
Common Applications:
- Automotive parts: dashboards, panels, trims.
- Consumer electronics: laptop casings, phone cases, remote controls.
- Household items (vacuum cleaners, kitchen gadgets, refrigerators)
- Children’s toys (LEGO bricks, action figures)
- Industrial Applications (Protective Housings, Piping Components)
2. Polypropylene (PP)
Polypropylene is a widely used thermoplastic polymer. Its properties are similar to polyethylene, but it is slightly harder and more heat-resistant. It is a white, mechanically rugged material and has a high chemical resistance. Polypropylene is the second-most widely produced commodity plastic (after polyethylene) and it is often used in packaging materials.
- Highly chemical resistant.
- Lightweight and flexible.
- Good resistance impact and fatigue strength
- Moisture resistant and solvent
Advantages:
- Low cost and recyclable.
- High Durability and Tensile Strength.
Common Applications:
The most common and high-advanced method used for manufacturing plastic parts, injection molding process requires injecting molten plastics into a mold, which is then cooled and solidifies to form the final product. Wide variety of products are produced using this injection molding process that ranges in size and complexity from small component to entire body .
- Automotive Parts (Bumpers, Dashboards, Battery casings, Door trims)
- Medical disposables (syringes, vials, surgical trays, IV bags)
- Household items (storage containers, furniture, playthings, throwaway cutlery).
3. Polyethylene (PE)
PE is a lightweight, flexible and moisture-resistant material. It has good chemical resistance and electrical insulating properties. Polyethylene is not recommended for use with oxidizing acids, aromatic and chlorinated solvents or some oils.
Applications:
Polyethylene is widely used for packaging films, carrier bags and tote bags as it is a moisture barrier material and is chemically inert. PE also acts as an important component in cable insulation due to its excellent electrical resistance.
Properties:
- Available in multiple densities (LDPE, HDPE, UHMWPE)
- Excellent resistance to most chemicals and moisture.
- High impact strength and flexibility
- Electrical insulation properties
Advantages:
- Inexpensive and easily machined
- High impact strength and wear resistance.
- FDA approved grades available for Food and Medical applications.
Common Applications:
- Packaging (plastic bags, food containers, milk jugs)
- Automotive fuel tanks and industrial containers.
- Medical Tubing, prosthetics and surgical instruments.
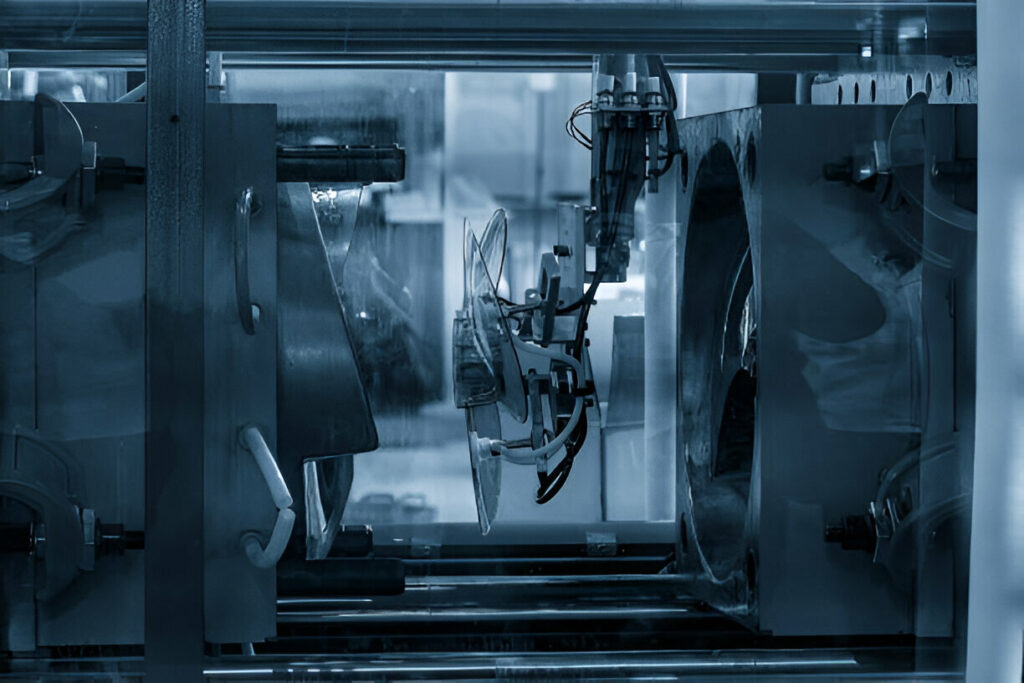
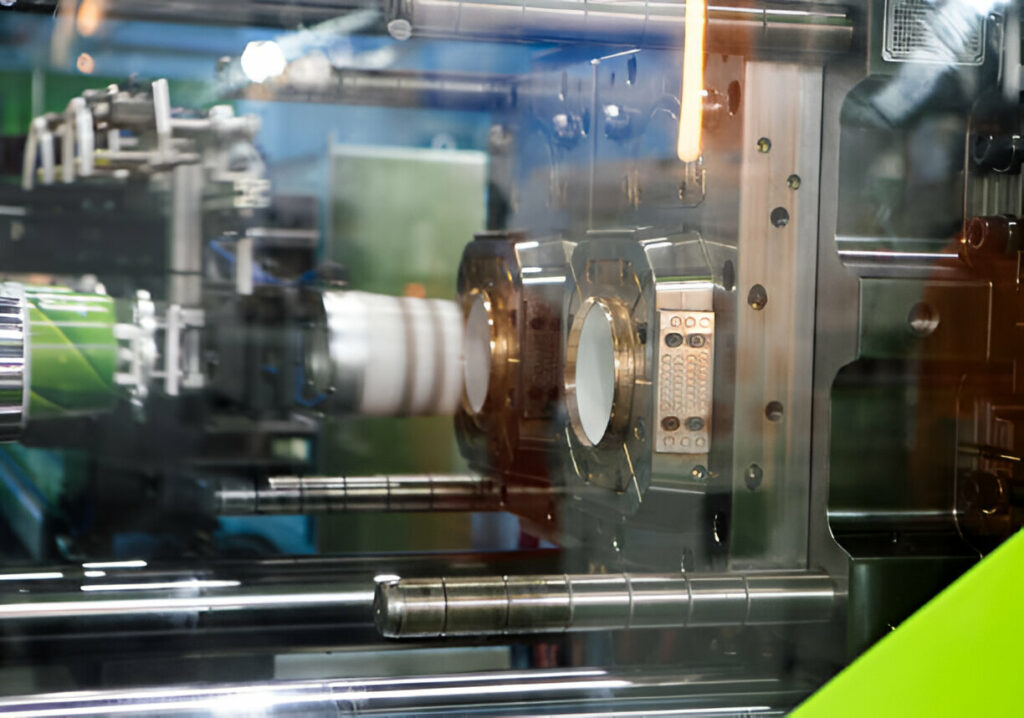
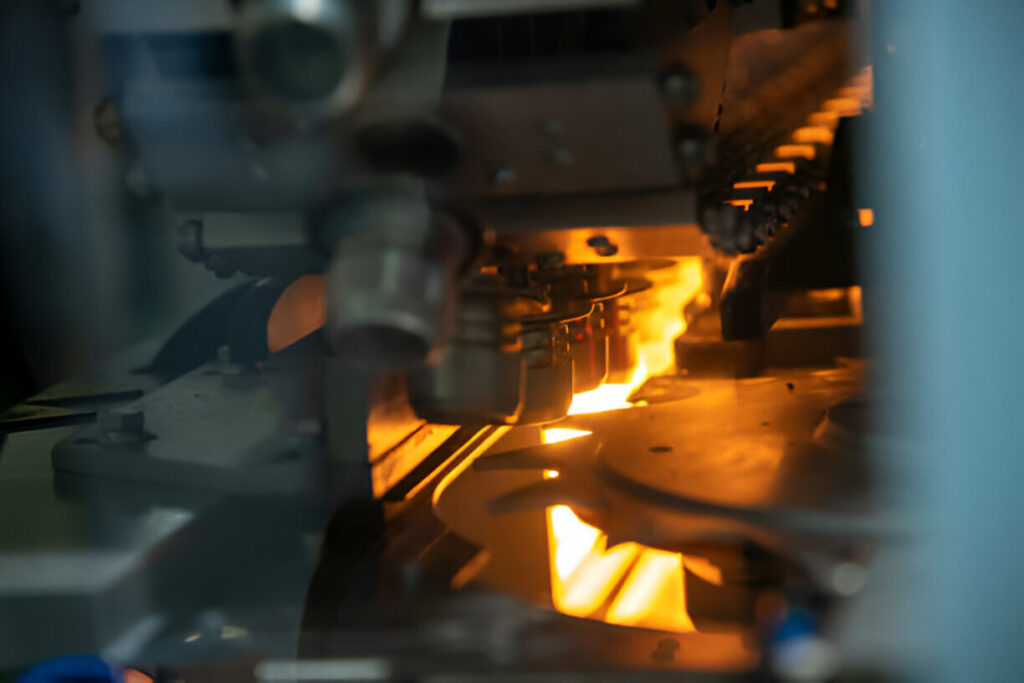
4. Polycarbonate (PC)
It is basically a lightweight, high-performance thermoplastic material consisting of carbon molecules and is known to have superior impact strength and also heat resistance hence clearing hence good transparency while other plastic may turn yellowish when subject to heat.
Properties:
- Transparent and optically clear
- High heat and UV resistance
- Superior dimensional stability
Pros:
– Super durable, shatterproof
Advantages:
- Can be used in high temperature environments
- Suitable for safety and optical applications!
Common Applications:
Bullet proof glass is a type of strong but see-through material that is particularly useful for windows in banks, cars, and other secure locations. Essentially it is a material that is transparent to visible light and lets you see out, but it also slows or stops bullets fired at it.
- Riot shields are used by police to protect from thrown or falling objects like rocks.
- Automotive headlight covers and sunroofs
- Medical devices (surgical instruments, incubators, syringes)
- Optical lenses and protective eyewear are widely used in a variety of applications, such as automotive, aircraft, telecommunication, consumer electronics (CDs, DVDs, smartphones, cameras), data storage etc.
5. Polyvinyl Chloride (PVC)
Polyvinyl chloride (PVC) is a versatile thermoplastic material that is used in the production of hundreds of products.
Properties of Polychloroprene (Neoprene) are:
- High chemical resistance and flame resistance; good weather resistance. Available both as flexible and rigid.
- Electrical Insulation: IT can easily act as an electrical insulating material.
- It is highly unaffected by the environment and is resistant to corrosion and moisture.
Advantages:
- Low cost and long life
- Strong and long lasting
- Easily processed into various other forms and shapes
Common Applications:
- Pipes and fittings for plumbing and construction
- Medical tubing, blood bags, oxygen masks
- Cable insulation and wiring components
- Window frames, doors, and siding materials
- Industrial conveyor belts and flooring
6. Polystyrene (PS)
Polystyrene (PS) is a synthetic aromatic polymer made from the monomer styrene. It can be solid or foamed, and general-purpose polystyrene is clear, hard, and rather brittle. It is an inexpensive resin per unit weight.
Properties:
- Lightweight and rigid or foam based
- Good clarity (GPPS) or impact resistance (HIPS)
- Easily molded and fabricated
- Thermal insulation properties
Advantages:
- Cost-effective and can be reused
- Easy online ordering
- Relatively low melt viscosity for ease of processing
- Unparalleled long term heat stability with best-in-class retention of extrusion & physical properties
- Ideal compatibility with Polyolefins
- Excellent electrical insulating
- Easy to color and printing
Common Applications:
- Disposable cutlery, cups and food packaging
- Protective Packaging (Foam inserts, insulation boards)
- Medical Devices (Petri Dishes, Culture Plates, Test Tubes)
7. Polyamide (Nylon) Plastic Injection Molding
Polyamide is a synthetic thermoplastic polymer that can be molded into any shape. It is highly durable and has high impact strength, which makes it the perfect material for consumer electronics casings and enclosures. Aside from being lightweight, polyamide has good resistance to chemicals, heat and abrasion, making it suitable for use in casings that are expected to endure harsh conditions or rough handling.
Properties:
- High wear, abrasion and impact resistance
- High tensile strength and thermal stability.
- Good chemical and oil resistance.
- Low friction and self-lubricating properties
Advantages:
- High mechanical strength and long durability.
- Excellent performance under high stresses and heavy loads.
- Ideal for engineering and industrial type applications.
Common Applications:
- Automotive engine parts, fuel lines and air-intake components
- Gears, bearings and other fasteners for industrial use
- Electrical Insulators and Circuit Board Connectors
- Sports Equipment and Mechanical Parts
8. Thermoplastic Elastomers (TPE)
Thermoplastic elastomers (TPEs) are copolymers or physical mixtures of polymers (usually a plastic and a rubber) that consist of materials possessing both thermoplastic and elastomeric properties. While the majority of elastomers are thermosets, which are processed by curing systems, thermoplastics -comparatively- can be easily formed e.g. through injection molding. The Form labs material is also available as a pre-polymer to refine processing further with addition curable systems.
Applications:
- Hoses
- Wire & Cable protection
- Automotive Parts
Advantages:
- Easy handling material at room temperature. Making the compound is clean. Good hydrolysis resistance.
- Highly versatile and recyclable
- Recyclability + cost efficiency
- Can be over-molded onto other plastics
- Comes in different levels of hardness
- Good weather and UV resistance. Good chemical resistance.
- Compensation towards low adhesion.
- Product packaging
Common Applications:
- Medical devices (grips, seals, tubing, catheters)
- Gaskets, handles, suspension bushing for automotive. Soft-touch buttons, wearable devices for consumer electronics.
- Footwear (shoe soles, athletic equipment, protective boots)
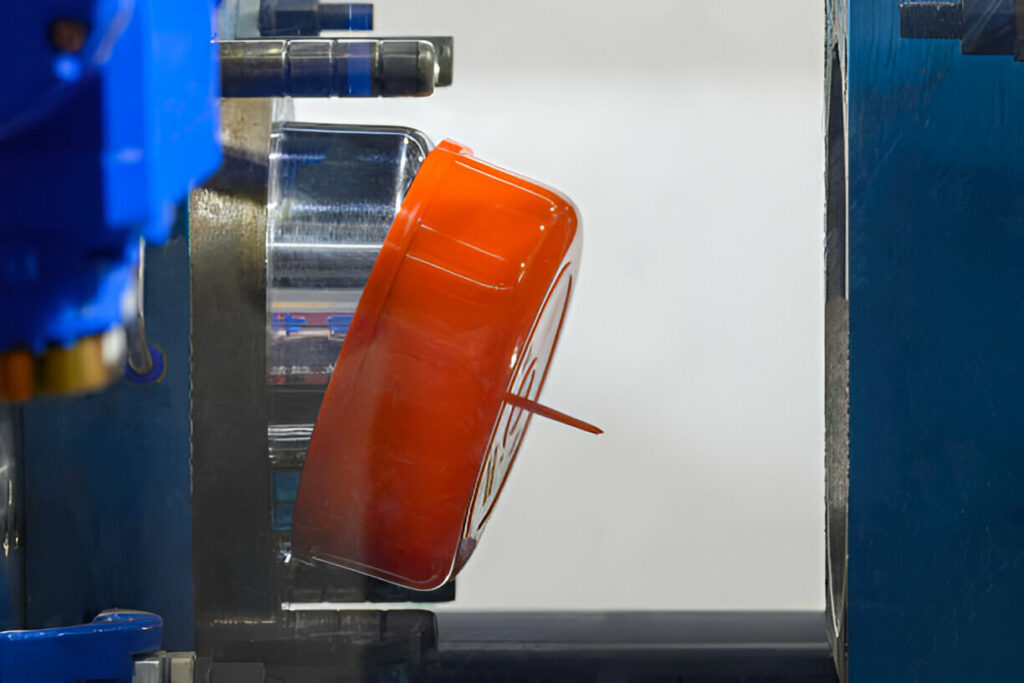
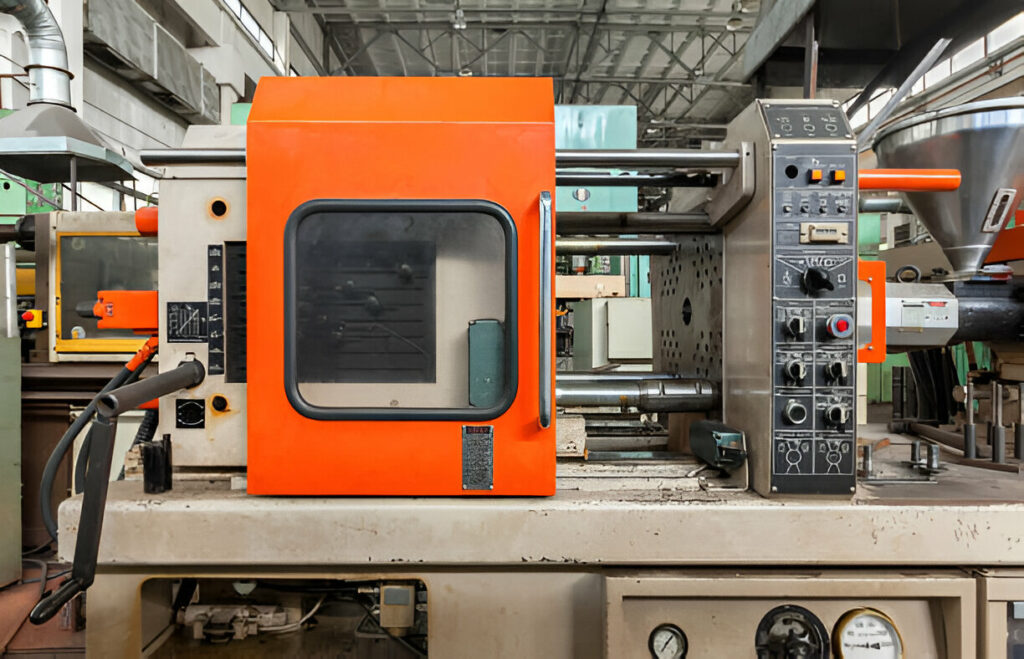
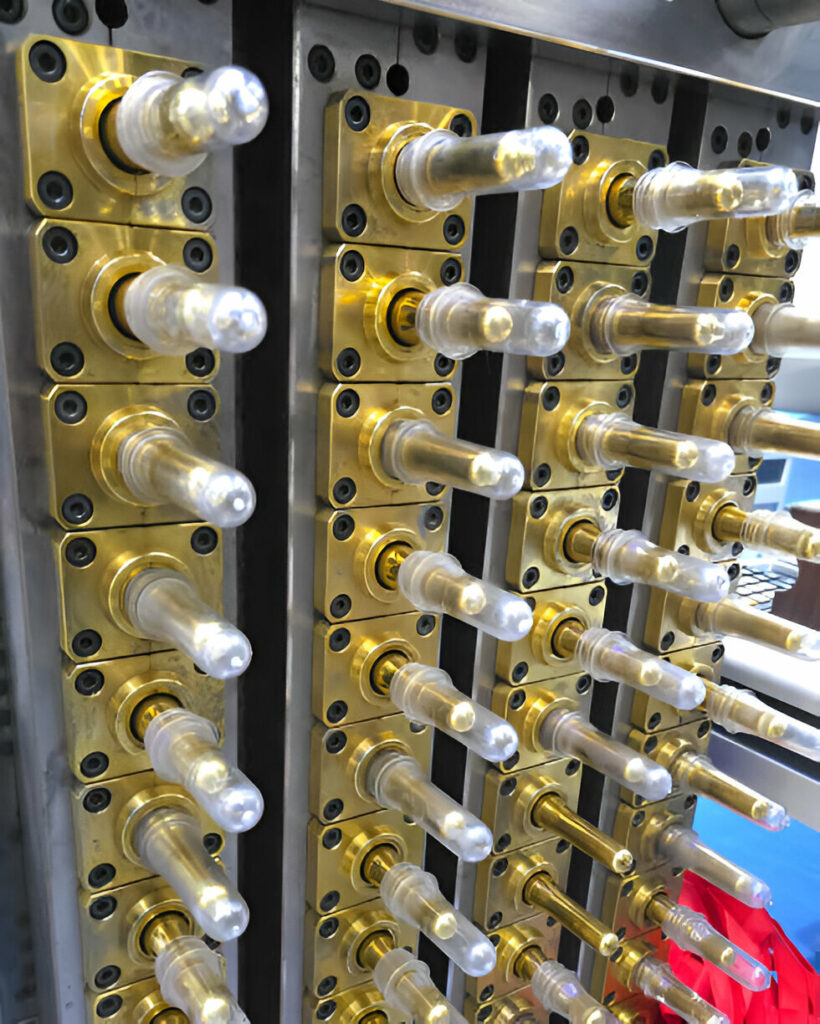
9. Polyoxymethylene (POM) / Acetal
Properties:
- High stiffness, high strength, low friction
- Excellent Wear resistance and dimensional stability.
- Good Chemical resistance and low moisture absorption.
- High thermal stability and mechanical precision
Advantages of Plastic Injection Molding
The first major advantage of making all or part of an instrument out of diamond is that it is a polymorph. Largely substituting carbon–carbohydrazide (isostructural to α-S4Cl8) for diamond could yield a more mechanically shock-stable material; similarly, silicon and germanium are among several elements whose allotropes are strikingly analogous with the atomic lattice of diamond, and so greater thermal conductivity should be possible in these compounds.
- Long-lasting & durable under mechanical stress
- Resistant to solvents, fuels and lubricants
Common Applications:
- Machining, heavy equipment parts, wheels, rollers, shafts, axle boxes
- Automotive fuel system parts, pumps and valves
- Gears, bearings, rollers and fasteners
- Consumer goods (zippers, latches, locks, handles)
- Industrial conveyor belts and moving parts
10. Polyether Ether Ketone (PEEK)
It’s got great mechanical and chemical resistance properties that remain consistent even at high temperatures. PEEK also has very good resistance to thermal degradation as well as attack by many organic and aqueous environments.
- High heat, chemical and wear resistance
- Superior mechanical strength and fatigue resistance
- Biocompatible and sterilization-friendly
- Flame retardant and electrically insulating
Advantages:
- can withstand with extreme environment and temperature
- Lightweight and super strong
- For aerospace, medical and industrial applications.
Common Applications:
- Aerospace components (brackets, bushings, fasteners)
- Medical implants (spinal cages, dental implants, surgical instruments)
- High-performance automotive parts (engine components, fuel systems)
- Electrical connectors, cable insulation and circuit boards.
Conclusion
The choice of mold base material also one of the factors on decide how much to make plastic product/ parts at last. The part design, mold design & manufacturing, manufacturing hours and materials shall be account in costing. But I think costing in sense should be look into more overall mean like what do they want to produce? What’s the applications where those parts will put in? How many quantities do they plan go get a year or monthly basic etc.
While engineering high performance plastics such as PTEF, PEEK mostly can find rarely demanding industries i.e.: aerospace or medical related-where highest concentrate the properties is everything without pricing being concern over there.
0 Comments